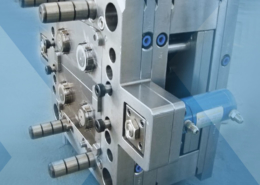
Meet the Moulder: WSM Plastics - plastic molding 1 2
Author:gly Date: 2024-09-30
Companies like Worrell, Stratasys, Advanced, and ATS are striving — often in collaboration — to improve and expand the 3D IM prototyping process. For example, Worrell is exploring the use of 3D-printed molds for use in blow molding, another area currently burdened by expensive tooling. Eventually, Darst expects to see 3D-printed molds move beyond prototyping and into short-run manufacturing.
One way to improve both surface finish and tolerance of 3D IM parts is by inserting aluminum inserts or pins into the mold before injection and then picking them out once the parts are molded. For example, Worrell worked on a valve design with small, thin fluid channels that ran through the main body housing and narrowed along the way. By using an insert in the 3D IM mold, the designers managed to achieve the tight tolerance and smooth surface required of the part.
There has long been a debate about open versus closed systems in 3D printing, with several big-name companies preferring to maintain control over their material supply and others offering an open ecosystem to certify a variety of materials.
Compared with straight 3D-printed prototyping, 3D IM’s big advantage is the aforementioned ability to fabricate parts in parent materials, which helps streamline device validation and verification. Often, 3D-printed materials lack the tensile strength or other important properties of final production materials, making them unsuitable for true functional testing. Since 3D IM allows the use of many parent materials, prototypes fashioned this way are ready-made to be tested and submitted to the FDA. This adds to 3D IM’s lead in the speed department.
“At that point, you might as well build a production tool and then modify it, so you aren’t throwing away a hundred thousand dollars’ worth of work if mold changes become necessary.”
For example, Worrell used 3D IM in the industrial design and engineering of OBMedical Company’s LaborView, a maternal fetal sensor system that measures labor contractions along with the heart rates of both mother and baby. Generating 3D IM parts in the parent material enabled OBMedical to progress quickly through electrical safety testing and submit final reports for its FDA submission, putting it way ahead of schedule. “Using the 3D IM process allowed us to move into safety and mechanical testing for our LaborView pilot devices in order to file for FDA clearance much more quickly and less expensively than originally anticipated,” Weaver Gaines, president and CEO of OBMedical, said.
An Introduction To 3D IM The 3D IM process has a lot in common with traditional metal mold IM. To significantly oversimplify matters, 3D IM uses a 3D printer to create the A and B sides of a given mold out of plastic. The two parts of the mold are clamped together in standard IM equipment, and molten material is injected into the mold. Once the part is cooled, it is removed from the mold. Sounds pretty straightforward, right?
“This isn’t very sexy stuff. It’s not generative design or customization or consolidations of 15 parts into a single part—all that stuff’s fantastic and well and good, but ultimately you need a manufacturing foundation to build all that great stuff into an economic model of consistency, reliability, and traceability,” he told me. “Without that, generative design isn’t going to go anywhere.”
“We look for platforms where we can characterize, understand and control all the parameters that are going to affect the quality of the part,” he said of Jabil’s stance. “That’s what we’re committing to for our customers, and that’s what we have to stand behind.”
In prototyping, pricing models allow for the assumed occasional misprint; when it comes to 3D printing for production, any mistakes affect the bottom line.
What Lies Ahead For 3D IM While there is certainly room for improvement, 3D injection molding is already being used successfully to produce functional medical device prototypes — and interest in the process is growing. “There is a very strong interest in 3D IM with everybody that we talk to, whether it’s a small startup company or a larger OEM,” Darst reported. “There is a great deal of attention being paid to this.”
Early applications for 3D printing provided a much-needed foundation for the technology, but they weren’t exactly critical or fit for end-use parts and production. As technologies have advanced, however, so has the industry’s understanding of the real potential for additive manufacturing: actual manufacturing. Product solutions leader Jabil has dedicated significant resources toward advancing a more digital future, including in manufacturing technologies; the company established the Jabil Additive Manufacturing Network earlier this year in response to growing demand for real-world applications in 3D printing. Driving that future forward requires a major focus on qualification and confidence.
Another area where 3D IM is imperfect (literally) is in surface finish. Since it is a layered process, 3D printing leaves small steps on the surface — it is not completely smooth or polished. And 3D IM can only deliver tolerances down to 2- to 4-thousandths of an inch, so extremely high-tolerance fits can also be an issue. However, Worrell and others have developed strategies to address these challenges.
“That’s all the tool; the next aspect of it is that you need to put it into a manufacturing facility that has the right quality systems and manufacturing disciplines and processes. These are usually characterized by some ISO certifications, whether for general manufacturing or for medical devices or automotive. All those systems are manufacturing processes and quality methodologies and systems to ensure that the plant is going to operate at a certian level of rigor and repeatability and consistency. Qualifying the tools is one thing; go to a manufacturing plant that can bring in a set of disciplines and procedures to stand behind the output and ultimately the file part for the customer,” he said.
Results: The Advantages Of 3D IM Over Conventional IM And 3D Printing 3D IM prototyping has two major benefits compared with traditional IM processes — namely cost and speed. “What makes 3D printed molds really appealing is you can mold out of Digital ABS material without having to make a large capital investment in aluminum or P20 steel tooling,” Darst told me. “And then you avoid the associated lead times that go with building metal molds.”
Returning to a discussion of their work with HP, Dulchinos noted that they gravitated to that open approach as well as to a powder bed technology, which he described as offering “a lot more control and openness than a lot of SLA.”
Earlier this year, Worrell decided to implement 3D IM in its model shop, investing in an Objet500 Connex from Stratasys and an 85-ton injection molding press from Toshiba. For larger parts, Worrell works with Advanced Molding Technologies, a neighboring injection molding company with a 250-ton press. The two companies have partnered in the development of the 3D IM process for medical device applications.
“I think this industry has grown up on prototyping and trinkets; neither of those has required very much rigor in terms of manufacturing processes or discipline, or any kind of real qualifications. They’re not critical. In our world, everything is mission-critical,” Dulchinos told me. “We think about 3D printing, the reality is 3D printing moves into applications where we are making true-to-life parts and are required to deliver at a cost model and level of quality—we’re not going to let that off the hook from instituting those.”
Over the past year, a hybrid prototyping process has begun to emerge, offering medical device developers the best of both worlds — the speed and economy of 3D printing combined with the material and accuracy advantages of IM. The approach uses 3D-printed molds to generate fully functional, injection-molded prototypes. I recently had the opportunity to discuss the technique with Dan Darst, executive VP and partner at Minneapolis-based product design and development firm Worrell. Darst and his company have been one of the early adopters of the 3D IM process and one of the evangelists spreading the word about the benefits of 3D IM within the medical device industry.
As a result, device makers usually turn (back) to traditional manufacturing methods like injection molding (IM) to create their functional prototypes. IM is capable of producing highly accurate plastic parts in parent materials, though the process is not without its own drawbacks. The steel or aluminum molds into which the materials are injected are comparatively expensive, costing thousands or tens of thousands of dollars. (Steel molds can get into the hundreds of thousands.) Manufacturing of these molds takes anywhere from two to six weeks, and that’s before production of prototype parts can even begin. As you might imagine, design changes or mold corrections can be extremely costly, both in time and money.
As education and upskilling come more into focus with the growth of the 3D printing industry, such tongue-in-cheek references are also realistic, as introductory-level classes are incredibly helpful for understanding the realities of additive manufacturing.
Worrell and Advanced are now using 3D IM to produce molds and prototypes for medical device makers using a broad range of materials — including some with surprisingly high melting temperatures. For instance, Worrell has been able to run a polycarbonate that melts between 540 degrees and 590 degrees F.
Addressing 3D IM’s Shortcomings No, 3D IM is not the perfect prototyping process, and it is not appropriate for all situations. While the number of materials that can be molded using 3D IM is impressive and growing, the plastic molds still can’t touch metal molds when it comes to materials that require extremely high heat or pressure to process.
In the meantime, proponents of 3D IM will continue to share its benefits and success stories with the medical device industry. “We are hopeful that this process is changing the way device makers look at innovation,” Darst said, “and we think it will fundamentally change the way medical devices are designed and developed.”
MedTG, a medical device startup developing specialized catheter devices and associated technologies, recently partnered with Worrell on the design and engineering of a dual-flow needleless blood collection system that decreases the need for multiple injections. By using 3D IM to generate the prototypes, they were able to reduce costs by 70 percent and cut times by 95 percent compared with traditional tooling.
“You have to take a very methodical engineering and manufacturing approach to it if you want to be confident that build after build will be repeatable, and able to deliver the same dimensional stability and part quality,” Dulchinos said. “That’s what happens in the rest of the manufacturing world, and we’re trying to bring that discipline to 3D printing.”
In addition to polycarbonates, the firm has also successfully run acrylonitrile butadiene styrene (ABS), nylons, Delrin (acetal resin), thermoplastic elastomers (TPEs), polyethylenes, polypropylenes, and other commodity-type materials and resins through 3D IM molds.
“For companies like Jabil, what’s more important is the openness of the platform,” he explained. “In a lot of these applications, people come in and look at closed 3D printing solutions and say, ‘There’s no way we can certify that.’ At the end of the day, we need the ability to control our own destiny and have the ability to have the unique understanding of the building block we’re working on. The degree to which 3D printing companies want to build a full system, with their software, with control of the materials and printing parameters, there’s no control over the variables.”
In addition, the longevity of 3D IM tools is nowhere near that of molds made of steel or even aluminum. Best case scenario, your 3D IM mold holds up for 50 to 100 shots using a resin like polycarbonate, ABS, nylon, polypropylene, ethylene, or propylene, according to Darst. And some molds can only run a handful of shots. Mold durability is dependent not only on material selection but also on the complexity of geometry and the size of the part. Worrell tells clients to expect runs of 10 to 25 parts out of a 3D IM mold.
Not exactly, Darst told me. “Although 3D molding requires an injection molded press, it doesn’t necessarily follow all of the rules and techniques of traditional IM,” he says. “The molding conditions and settings are very different than they would be with metal tools. The process steps outside a lot of what you know about molding.”
“3D IM molds are very versatile. You can do insert molding, undercuts, threaded inserts, overmolding, and living hinges,” Darst stated. “You can do a lot of things you would traditionally do in an aluminum tool.”
“Imagine sending a part file to a product development firm and having a cavity and core for a mold completed in 16 hours,” Steve Jenkins, business development manager at Advanced, explained. “And in a matter of 24 more hours, you have molded parts in medical-specified resins in hand.”
“Manufacturing certifications are really important if you want to take these into different applications in industry,” Dulchinos said. “Qualify the solution, qualify the application and deliver it in a certified manufacturing operation to make it satisfy the requirements of these industries.”
Exploring other technologies led back to a discussion about traditional technologies like CNC and injection molding. Decades of operations experience has led to these methods being extremely well understood as they relate to the manufacturing operating process. It struck him as interesting, he said, that the ability to control these processes in a customized way has long been available, but newer solutions want to provide a print button rather than customized operations.
When you visit any web site, it may store or retrieve information on your browser, mostly in the form of cookies. Control your personal Cookie Services here.
1,346 polymer and metal AM companies and 143 end-users. Consumer products AM generated $2.6 billion in 2023. Segment expected to grow to $28 billion by 2033 at 26.8% CAGR. This new market study fro...
Customers expect production-quality results for production parts, and that’s where additive manufacturing needs to focus on delivery.
The biggest difference is the heat profiles of the molds themselves. Molds made out of aluminum or steel can withstand extremely high temperatures and thus can handle materials with extremely high melting points. Many of the thermoplastics and other materials being used in today’s medical devices have melting temperatures of 500 degrees F or higher. 3D IM molds, however, are made out of a two-part plastic material called Digital ABS — originally developed by the Israeli 3D printer manufacturer Objet, now part of Stratasys — which will break down at constant high temperatures.
In the context of Jabil’s operations, they see that mature technologies like injection molding and machining are consistent. Users can trust, Dulchinos noted, the output that comes from taking an established material and a certain molding machine and process parameters; “you can trust in delivering a certain capability.”
Jabil has been working with a variety of 3D printing companies, including with HP as an early partner for Multi Jet Fusion. One of the key points that makes this a strong technology choice for Jabil is that HP offers an open platform approach to its 3D printing solution.
“When we first heard about 3D-printed injection mold tooling with Stratasys Digital ABS material, we were apprehensive, especially due to claims made by competitors in the past,” said Matt Havekost of Advanced Technology Systems (ATS), the Stratasys reseller that helped Worrell select the right 3D printer for its business. “I will never forget the look on the face of the experienced injection molding press operator when the first part came off the 3D printed mold. That is something that sticks with me to this day as I talk with people about this exciting new application.”
He pointed out an even more extreme example of the potential costs savings. “Stratasys is doing an enclosure for vein pumps in 3D IM that requires very complex tools. It is probably too expensive to do in aluminum tooling, because the prototype tool would be half of the cost of a production tool,” Darst said.
In addition to quality and repeatability, traceability is a critical concern. Should a recall be necessary at any point, a full traceability ensures that operators have access to the full pedigree of what happened, where, to which part or material in a given batch.
Looking at subscription models, or “Tesla-like models where you drop over the web to your platform,” Dulchinos noted that “there’s no way to do that in a manufacturing environment without having to re-qualify and re-certify that process.” Discipline is needed to operate at manufacturing quality and efficiency and unless 3D printing companies want to take on qualification and certification themselves, openness is the key for global solutions companies like Jabil to provide viable production-quality 3D printing.
“Metal tooling can take four to six weeks to get, and then you hope that your design is done, the molding conditions are right, and you can produce good parts. If not, you will need to make revisions. When all is said and done, you are at four to eight weeks before you get a good working part,” Darst said. “This 3D printing technology allows us to produce the mold in a day, and then we can be in the press the very next day. We can have parts within two to three days.”
As for the speed element, Darst says that some of the smaller 3D printed molds can be run in 5 hours, and his firm hasn’t encountered a mold yet that takes more than 24 hours to produce. That’s several weeks faster than for metal molds, and it doesn’t even take into account the possibility of mold rework.
3D printing has fundamentally changed the way medical devices are prototyped and tested. The technique turns out sample parts much more quickly and cheaply than conventional manufacturing methods, enabling designers to significantly shorten iteration cycles and speed time to market for their products. As the cost of equipment has fallen, the technology has improved, and the range of applicable materials has expanded, 3D printers have become a fixture in design departments — even the smallest of medical device companies is investing in these rapid prototyping tools.
To circumnavigate this issue, 3D IM puts its unique spin on the standard IM process. The time between injection cycles is lengthened by up to a minute, to allow the surface of the mold to cool down to its optimal operating temperature before more molten material is injected into it. Using this modified IM process, 3D printed molds can produce as many as 25 to 100 parts before degrading — a far cry from the durability of a metal mold but more than sufficient for rapid prototyping purposes.
But today’s 3D printing technology can carry a product only so far into the development process, primarily due to material constraints. Following a design freeze, it is preferable to build functional prototypes using parent materials — the specified materials intended to be used in the final product — to enable accurate verification and validation testing (as required by the FDA). In many cases, parent materials are incompatible with the current generation of 3D printing technology. Plus, 3D printing can’t always deliver the fidelity or surface finish necessary to satisfy regulatory or internal testing requirements.
While this framework is dramatic, Dulchinos is the first to admit that it’s not inherently the most exciting consideration in 3D printing.
“This material, on these 3D printers, with these process parameters, will deliver a certain set of capabilities out of that set of conditions,” he explained. “On an application-by-application basis, we take that and qualify to the application. Certain applications, like aerospace or healthcare, go through and really certify methodically to ensure that we trust and monitor what comes off the printers on an ongoing basis.”
How much can 3D IM save you compared to metal molds? In most cases, Worrell has found that 3D IM molds cost 60 to 75 percent less than aluminum molds. Darst put it in practical terms: “If it is a $12,000 mold, you might be able to make it for $3,000 or $4,000, pending part geometry design, secondary options, functional requirements, and mold complexity.”
On the other hand, the fact that 3D IM molds are so cheap and quick to produce more than offsets their longevity limitations. “If your mold starts to break down or delaminate after 25 parts, the next day you could have another mold and run another 25,” Darst said. If you don’t want to wait a day to get a replacement mold, you can always print two of them at the same time.
This highlights another plus of using 3D IM for prototyping — its design for manufacturing (DFM) capabilities. For instance, it can help identify potential problems with your design or tooling prior to building expensive production tools. “You can inexpensively work out the fits and the features that you need for assembly through 3D IM and mitigate some of the tooling-associated risk with creating a part,” he explained. “So when you do make the huge investment in tooling, you are pretty confident that your changes will be minimal and you aren’t throwing out an entire tool.”
Ensuring consistency build after build is a major focus for Jabil, which has instituted an MPM solution: Machine, Process, Materials.
Jabil is looking toward the future of manufacturing—a future that includes 3D printing, but not as industry has previously known it. This technology evolved around applications in rapid prototyping and grew into trinkets, but it has the potential to be so much more, John Dulchinos, Jabil’s Vice President of Digital Manufacturing, told me when we spoke recently.
“When you’re working with customers’ gross margins, you have to take into account the economic model; they can’t afford to make it twice or three times. They have to get it right the first time. Machines have to operate at a high degree of operating efficiency. This requires a more methodical discipline and approach to qualifying discipline,” Dulchinos continued. “With the MPM process, there’s a certification framework that allows you to go from consumer product to aerospace or healthcare, which obviously have different requirements, so we created a dynamic framework that allows you to right size it for where you’re using it.”
“There’s a lot of focus on the fun stuff—generative design, personalization, freedom of design, all these great things that additive brings—but at the end of the day, to deliver as a manufacturing solution, you need to put it into a fully qualified MPM process and deliver in a certified facility,” he said. “To have that discipline so you can deliver quality and cost point, to get production parts that help with customers’ gross margins, there’s an emphasis on delivering optimal solutions at scale. It needs to be looked at from an IT standpoint from design through build through qualifying through the supply chain, all in a fully traceable manner, and you need to monitor the whole process.”
GETTING A QUOTE WITH LK-MOULD IS FREE AND SIMPLE.
FIND MORE OF OUR SERVICES:
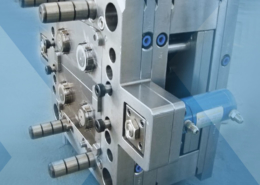
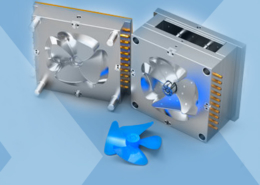
Plastic Molding

Rapid Prototyping
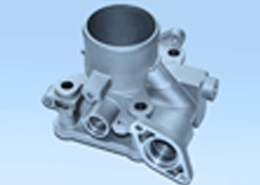
Pressure Die Casting
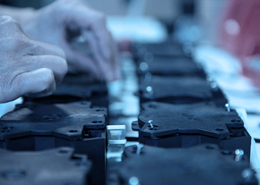
Parts Assembly
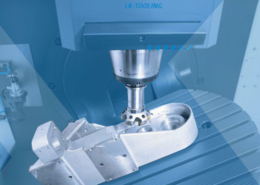