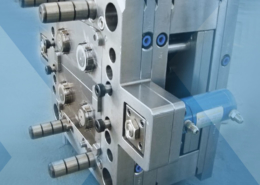
Exploring the World of Custom Molded Plastics
Author:gly Date: 2024-06-08
Custom molded plastics represent a fascinating intersection of technology, innovation, and manufacturing. In today's global landscape, these versatile materials play a pivotal role across various industries, from automotive to healthcare and beyond. Understanding their significance requires a comprehensive exploration of their properties, applications, manufacturing processes, and environmental impact.
The Versatility of Custom Molded Plastics
Custom molded plastics encompass a vast array of materials tailored to specific applications. From thermoplastics to thermosets, these materials offer unique properties such as strength, flexibility, and heat resistance. Their adaptability makes them indispensable in industries ranging from aerospace to consumer goods, where precision and reliability are paramount.
Applications in Automotive Engineering
In the automotive sector, custom molded plastics have revolutionized design and manufacturing processes. Components such as bumpers, interior trim, and engine parts benefit from the lightweight yet durable nature of these materials, enhancing fuel efficiency and vehicle performance.
Advancements in Medical Devices
The medical industry relies heavily on custom molded plastics for the production of surgical instruments, implantable devices, and diagnostic equipment. Biocompatible materials ensure patient safety, while precision molding techniques enable the creation of intricate components crucial for medical advancements.
Impact on Consumer Electronics
In the realm of consumer electronics, custom molded plastics contribute to the sleek designs and functionality of smartphones, laptops, and wearable devices. Their ability to withstand impact and harsh environmental conditions ensures product durability while maintaining aesthetic appeal.
Manufacturing Processes
The manufacturing of custom molded plastics involves a meticulous process that begins with design and ends with quality assurance. Injection molding, compression molding, and blow molding are among the primary techniques employed, each offering distinct advantages in terms of efficiency and scalability.
Precision Injection Molding
Injection molding remains the most widely used method for producing custom molded plastics. Molten material is injected into a mold cavity under high pressure, allowing for the rapid and cost-effective production of complex shapes with minimal waste.
Compression Molding Techniques
Compression molding is favored for applications requiring high strength and dimensional stability. The process involves placing a pre-measured amount of material into a heated mold cavity, followed by compression to shape the part. This method is ideal for producing components with intricate details and tight tolerances.
Sustainable Practices in Blow Molding
Blow molding, particularly in the context of PET bottles and containers, has seen significant advancements in sustainability. From utilizing recycled materials to optimizing energy efficiency in production, manufacturers are committed to reducing the environmental impact of custom molded plastics.
Environmental Considerations
While custom molded plastics offer numerous benefits, their environmental footprint remains a concern. From raw material extraction to end-of-life disposal, each stage of the product lifecycle requires careful consideration to mitigate environmental impact.
Embracing Recyclability
Efforts to increase recyclability and promote the circular economy are underway across the plastics industry. Innovations in material science and recycling technologies aim to reduce dependency on virgin plastics and minimize waste accumulation in landfills and oceans.
Addressing Single-Use Plastics
The proliferation of single-use plastics poses a significant challenge to environmental sustainability. Manufacturers and policymakers are exploring alternative materials and implementing regulations to curb plastic pollution and promote responsible consumption habits.
Lifecycle Assessments and Eco-Design
Lifecycle assessments play a crucial role in evaluating the environmental performance of custom molded plastics. By considering factors such as energy consumption, greenhouse gas emissions, and resource depletion, stakeholders can make informed decisions regarding product design, manufacturing processes, and end-of-life management.
Conclusion
In conclusion, custom molded plastics represent a cornerstone of modern manufacturing, driving innovation across industries while presenting both opportunities and challenges. By understanding their diverse applications, manufacturing processes, and environmental considerations, stakeholders can navigate this dynamic landscape with a focus on sustainability and responsible stewardship. As we continue to advance technologically and environmentally, collaboration and innovation will be key to shaping the future of custom molded plastics.
GETTING A QUOTE WITH LK-MOULD IS FREE AND SIMPLE.
FIND MORE OF OUR SERVICES:
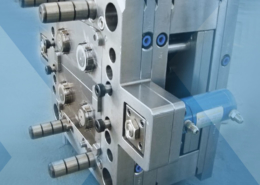
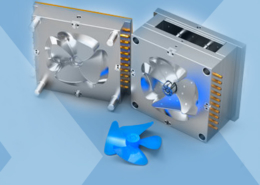
Plastic Molding

Rapid Prototyping
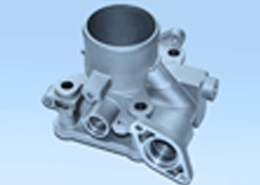
Pressure Die Casting
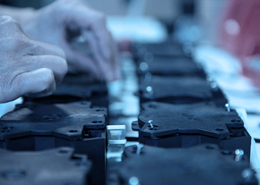
Parts Assembly
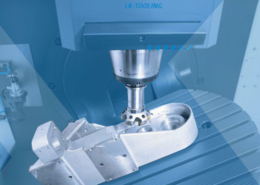