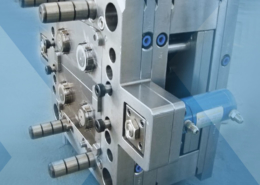
Medical Micro Molding at Scale Featured at IME South - molding services
Author:gly Date: 2024-09-30
Packaging manufacturer PulPac and global consultancy PA Consulting claim they have come up with the technology that can finally make it possible for dry-molded fiber (DMF) to be made into beverage containers. The companies say that the bottles would be a sustainable alternative to wide-spread packaging solutions such as cardboard and single-use plastics.
A system of this type in a real-world application might be a bit of a stretch, but it is quite stunning to witness the metamorphosis of a plastic vial into a bottle opener in such an all-encompassing manner.
“We have not finalized a set of markets to launch in but expect Europe to be very high on the list of priorities,” concluded Perrotta. The intention of our next phase of work is to demonstrate the scalability options to meet demand.”
So how does DMF compare to cardboard production on emissions, for example? “This solution is quite different to cardstock,” Perrotta said. “We can produce a myriad of sizes and shapes not possible in either cardstock or wet-molded processes today.
“Emissions work is currently being evaluated but since our process is a dry-molded process, there is a significant reduction in water use and energy compared to alternative forming methods.”
According to the product brief, the PA/PulPac Bottle Collective – as the prototype is called - can store water, dairy, non-carbonated soft drinks, adult beverages, and even hair- and skin-care products. The bottle can also be customized with bespoke shapes, sizes and decorations to reflect brand identity, with a growing number of businesses already taking an interest in the product, we were told.
“We expect our packaging to be a valid alternative for dairy beverages,” Perrotta told us. “We have not yet trialed shelf life for a full range of beverages yet; as we further engage specific brands and their unique needs, material transfer, color and taste profile and fragrance needs will all be addressed, too.
“When a liner is used in our bottle, it is not adhered or glued to the fiber layer. Meaning, it is easily separated by almost any mechanical process. We are working with various waste management facilities in various markets around the world to understand what this looks like in practice – not just theory.”
“Creating a DMF bottle already represents an enormous challenge,” opened Tony Perrotta, PulPac partnership lead at PA Consulting. “Creating a scalable and commercially viable process to replicate this has been even more so. Our aim is to provide a scalable process that meets existing need for cost, scale, speed, sustainability profile, and brand needs. It’s a tall order indeed but we have already demonstrated the foundational aspects of this work.”
Copyright - Unless otherwise stated all contents of this web site are © 2024 - William Reed Ltd - All Rights Reserved - Full details for the use of materials on this site can be found in the Terms & Conditions
They are then processed with a ZE 28 BluePower twin-screw extruder and, following the mixing and blending of adhesive and liquid color additives, the compound is sent to an all-electric PX 81-180 press, where the bottle opener is molded. The PX 81-180 is equipped with APCplus, which compensates for process fluctuations that may result from recyclates with different viscosities.
Blood-collection vials made from medical-grade polypropylene are injection molded on the show floor, transported via a series of what look like pneumatic tubes to a shredder, upcycled via a twin-screw extruder, processed with various additives, and injection molded anew to produce the bottle opener pictured here. The process is apparently seamless.
Since it’s still early days for the Bottle Collective, Perrotta couldn’t share specifics around how the packaging affects shelf life, or taste and flavor properties of milk – although the companies claim the bottle can hold water for six months.
DMF packaging is already being produced at scale, including in the shape of bottles for dry goods, but a DMF container for storing liquids hadn’t been successfully developed before.
“We are designing for standard kerbside collection and expect the dustcart pressure to easily and quickly separate the liner from the outer layer," Perrotta continued. “In addition, since a liner is being employed, the pulp is of a higher grade than alternatives,” he claimed. “The liner houses the product and any chemistry of the product keeping the pulp high grade.”
And it’s not just cellulose that can be used – the team is also exploring how so-called non-tree-based fibers could work. “In addition to virgin fiber, we can incorporate recycled content and, in some cases, non-tree-based fibers for added properties,” he told us.
The vials are first molded using ExxonMobil PP 9074 MED on an all-electric PX 251-1400 injection molder. Thirty-two vials are produced per shot. For the purposes of this demonstration, the vials are transported to a grinder via the tubes and transformed into pellets in a matter of minutes.
PulPac and PA Consulting say they will announce some of their first branded partners in the project ‘shortly’, but the team is yet to decide on the markets to launch the bottles in come 2025.
While PulPac and PA Consulting believe they have proof of concept, the challenge now lies in scaling this up to create a solution fit for the FMCG industry. The plan is to release the bottles at scale by 2025.
KraussMaffei has set up a rather remarkable example of closed-loop circularity at booth 600 in the west hall at NPE2024.
This allows components to be produced with consistently high quality and little waste, another important contribution to greater sustainability, said KraussMaffei.
Asked how a DMF milk bottle could look like - including what type of lining would be used and how easy that would be to recycle - Perrotta explained: “Our approach allows for the use of multiple types of liners, hence we could replicate existing use or find another alternative.
Watch the circular economy in action at booth W600 at NPE, running through May 10 at the Orange County Convention Center in Orlando, FL.
DMF is made when cellulose pulp is dry-molded into solid packaging. PulPac says the process brings significant environmental benefits since it requires less water and energy during production. Plus, DMF can take various shapes and forms that aren’t possible to achieve through so-called wet-molding. The process can also utilize recycled, residue as well as virgin cellulose, making use of readily available, renewable and affordable material.
Editor in chief of PlasticsToday since 2015, Norbert Sparrow has more than 30 years of editorial experience in business-to-business media. He studied journalism at the Centre Universitaire d'Etudes du Journalisme in Strasbourg, France, where he earned a master's degree.
GETTING A QUOTE WITH LK-MOULD IS FREE AND SIMPLE.
FIND MORE OF OUR SERVICES:
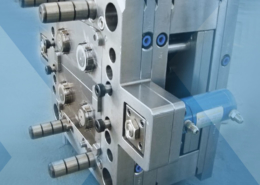
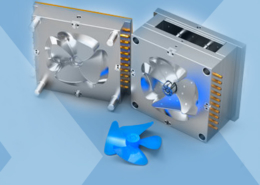
Plastic Molding

Rapid Prototyping
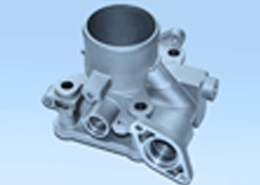
Pressure Die Casting
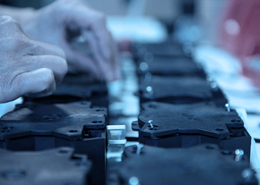
Parts Assembly
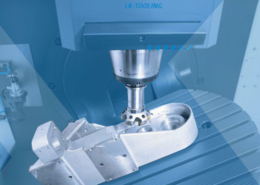