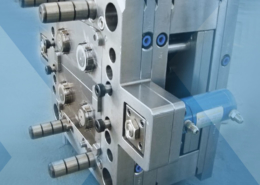
Mechanical recycling of acrylonitrile-butadiene-styrene copolymer and high
Author:gly Date: 2024-09-30
With Elmet‘s Smartshot E and Smartmix Top 7000 Pro systems, two of the company’s technological flagships are used in the production cell.
The technological high-end counterpart in material provision is the Elmet Smartmix Top 7000 Pro dosing system, which delivers precise and reliable dosing of material to the Elmet injection mold. A Sumitomo linear handling device removes the parts from the mold and transfers them to the weighing cell made by Mettler Toledo where every part is weighed. The result is stored in a database and displayed graphically to demonstrate the process accuracy of the system. After weighing, the silicone parts are marked by laser to ensure highest possible traceability. After lasering, the parts are placed on a conveyor belt.
In November 2020, Celanese introduced a sustainable polyacetal product offering known as POM ECO-B, a mass-balance, bio-based option that allows customers to realize a reduction in carbon dioxide emissions in their end-use products and advance toward renewable content goals. While POM ECO-B is commercially available now, not all customers or industries are ready to adopt bio-mass balance that comes with its carbon dioxide footprint reduction benefit.
Rick Lingle is Senior Technical Editor, Packaging Digest and PlasticsToday. He’s been a packaging media journalist since 1985 specializing in food, beverage and plastic markets. He has a chemistry degree from Clarke College and has worked in food industry R&D for Standard Brands/Nabisco and the R.T. French Co. Reach him at [email protected] or 630-481-1426.
PlasticsToday learned from Michael Schaffer, Elmet’s business unit manager tooling & turnkey, that the company built a 4-cavity mold specifically for the K Show. It will be used to make Smartcap lids in the Sumitomo booth as a souvenir for visitors, he adds.
Together with three project partners, Austrian company Elmet developed two innovative injection-molding production cell that manufacture four different covers for beverage and food cans, which have been dubbed as Smartcaps.
The joint announcement with MCAM builds upon Celanese’s sustainable product offerings by initiating development of a recycled content option of the Celanese Hostaform/Celcon POM product that will be marketed as POM ECO-R. MCAM will conduct recycled feedstock collection, separation, and processing, while Celanese will provide the formulation, product technology, and production capability. Celanese expects to offer its POM ECO-R solution with up to 30% recycled content.
“MCAM has invested significantly in enabling closed-loop opportunities for post-industrial and post-consumer POM waste streams. In partnership with raw material supplier Celanese and its extensive capacities, we can now offer a wide range of new opportunities to our customers to achieve their own sustainability goals, support CO2 reduction, and work toward a climate-neutral economy,” said Markus Wehinger, Business Manager, MCAM Recycling Solutions.
Lids for food & beverage cans are manufactured by the Elmet injection molding system with an all-electric Smartshot E valve-gate cold-runner system.
The heart of the innovation is the interaction between the high-tech contributions from the four partner companies. The combination of high-precision dosing (Elmet Smartmix), the all-electric injection-molding machine (Sumitomo IntElect), and the electric valve-gate cold runner (Elmet Smartshot E) enables a new level of accuracy in the reproduction of part weights.
The new system boasts a material utilization level of up to 99.6%. Drums are changed automatically to increase ease of use and keep the amount of training to a minimum. Use of special seals made of FDA-compliant materials allows the Smartmix Top 7000 Pro to be used for medical applications.
Compared to its predecessor, the Smartmix TOP 5000 P, the Smart TOP 7000 Pro features a completely new pump system, which now only contains approximately one third of the liquid silicone in the system, making it much easier to clean. This is particularly important for use in the medical and pharmaceutical fields where the pump unit is dismantled and cleaned each time the material changes to prevent mixing of different types of liquid silicone.
With help from Sumitomo Demag, Shin-Etsu, and Mettler Toledo, Elmet will debut two innovative production cells to make silicone can covers at K 2022.
The special four-cavity injection mold from Elmet injects four different can lids made of liquid silicone (LSR) from partner company Shin-Etsu. The silicone lids produced serve as coverings for customary beverage cans such as those for soft drinks, energy drinks, and various alcoholic beverages. A separate cavity also produces covers for customary food cans made of sheet steel.
Celanese and MCAM plan to work together to assess options to convert waste streams into marketable, end-product formulations so that Celanese can offer its customers sustainable options for scrap or end-of-life waste with assurances of closed-loop material reuse.
Celanese Corp. and Mitsubishi Chemical Advanced Materials (MCAM), a global manufacturer of high-performance thermoplastic materials in the form of semi-finished products and finished parts, have announced a joint collaboration to further develop mechanical recycling solutions for both post-industrial and post-consumer sources of polyacetal (POM) copolymer. The aim is to meet requests from customers seeking recycled content options and carbon dioxide reductions while maintaining product consistency, quality, and performance.
The dosing system design was focused on reducing the unit’s footprint to 1,150 mm/55.3 inches by 790 mm/31 inches. This makes the system the smallest liquid-silicone dosing system for 200-Liter container units on the market.
“Celanese is a leading, global producer of acetal copolymer, and our industrial-scale manufacturing capabilities for POM are ideally suited for helping customers in a range of industries — such as medical, automotive and consumer goods — to meet their strategic environmental goals,” said Tom Kelly, Celanese Senior Vice President, Engineered Materials. “Offering both bio-based POM content, which can be uniquely produced from waste products via bio-methane or from CO2 emissions, and recycled POM through a collaboration with MCAM, elevates the broad usability of POM as an ideal engineered material that can help our customers achieve their sustainability goals.”
GETTING A QUOTE WITH LK-MOULD IS FREE AND SIMPLE.
FIND MORE OF OUR SERVICES:
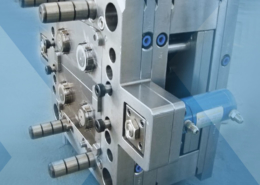
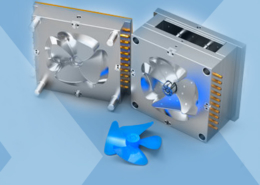
Plastic Molding

Rapid Prototyping
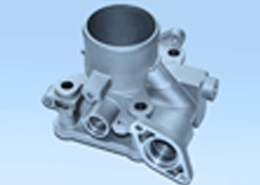
Pressure Die Casting
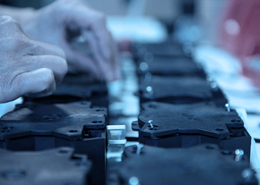
Parts Assembly
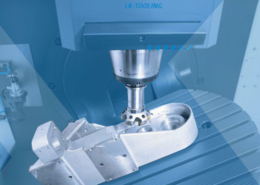