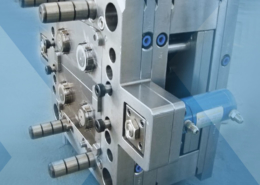
Exploring the Dynamics of Co-Injection Molding: Redefining Plastic Manufacturing
Author:gly Date: 2024-06-08
Introduction:
Co-injection molding stands as a revolutionary technique in the realm of plastic manufacturing, offering unparalleled versatility, efficiency, and cost-effectiveness. This advanced process involves injecting multiple materials into a single mold cavity simultaneously, resulting in complex, multi-layered components with superior mechanical properties and aesthetic appeal. In this article, we embark on a journey to unravel the intricacies of co-injection molding, exploring its applications, benefits, and transformative impact on the plastics industry.
1. The Evolution of Co-Injection Molding
Co-injection molding has evolved significantly since its inception, driven by advancements in material science, mold design, and process optimization. Initially used primarily for packaging applications to enhance barrier properties and reduce material usage, co-injection molding has expanded its footprint across diverse industries, including automotive, electronics, and consumer goods. The ability to incorporate functional additives, colorants, and recycled materials within a single molded part has propelled co-injection molding to the forefront of plastic manufacturing technologies.
Moreover, the integration of automation and robotics has streamlined production workflows, enabling manufacturers to achieve higher throughput and lower production costs. By leveraging these technological advancements, co-injection molding continues to push the boundaries of innovation, offering solutions to complex engineering challenges and driving sustainable growth in the plastics industry.
2. Superior Mechanical Properties and Performance
One of the key advantages of co-injection molding lies in its ability to produce parts with superior mechanical properties and performance compared to traditional molding techniques. By encapsulating a core material within a skin layer of a different material, manufacturers can tailor the properties of the finished part to meet specific application requirements. For instance, combining a rigid core material with a flexible skin material can enhance impact resistance, tensile strength, and fatigue durability, making co-injection molded parts ideal for demanding applications in automotive, aerospace, and industrial sectors.
Furthermore, the multi-layered structure of co-injection molded parts offers inherent advantages in terms of surface finish, dimensional stability, and resistance to environmental factors such as UV radiation, chemicals, and moisture. This versatility and performance make co-injection molding a preferred choice for applications where stringent performance standards and aesthetic considerations are paramount.
3. Sustainable Manufacturing Practices
In an era characterized by growing environmental awareness and sustainability concerns, co-injection molding has emerged as a frontrunner in promoting eco-friendly manufacturing practices. By enabling the use of recycled materials and bio-based polymers in combination with virgin resins, co-injection molding reduces the environmental footprint associated with plastic production while minimizing waste generation and resource consumption.
Moreover, the ability to create lightweight, thin-walled parts with optimized material distribution contributes to overall material savings and energy efficiency. By embracing a holistic approach to sustainable manufacturing, co-injection molding empowers manufacturers to align with regulatory requirements, meet consumer demands for eco-friendly products, and drive positive social and environmental impact.
4. Future Directions and Emerging Trends
Looking ahead, the future of co-injection molding holds immense promise, with ongoing research and development efforts focused on pushing the boundaries of material science, process technology, and product innovation. Advances in additive manufacturing, nanocomposites, and biodegradable polymers are poised to expand the horizons of co-injection molding, unlocking new possibilities in areas such as healthcare, electronics, and renewable energy.
Furthermore, the integration of digital technologies such as artificial intelligence, machine learning, and predictive analytics promises to revolutionize the way co-injection molding processes are optimized, monitored, and controlled. By harnessing the power of data-driven insights and automation, manufacturers can unlock new levels of efficiency, quality, and customization, positioning co-injection molding as a cornerstone of the Fourth Industrial Revolution.
Conclusion:
In conclusion, co-injection molding represents a paradigm shift in the field of plastic manufacturing, offering unparalleled versatility, performance, and sustainability. By leveraging advanced materials, innovative design concepts, and cutting-edge process technologies, co-injection molding enables manufacturers to create complex, multi-functional parts that meet the evolving needs of diverse industries. As we look towards the future, the potential for further advancements in co-injection molding technology remains boundless, promising a world where plastics continue to drive innovation and transform the way we live, work, and play.
GETTING A QUOTE WITH LK-MOULD IS FREE AND SIMPLE.
FIND MORE OF OUR SERVICES:
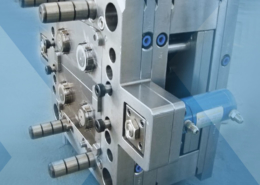
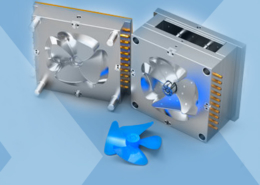
Plastic Molding

Rapid Prototyping
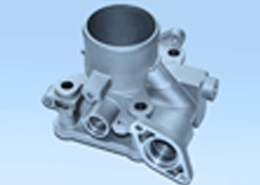
Pressure Die Casting
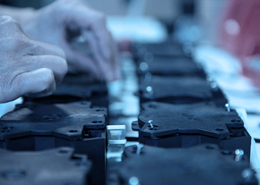
Parts Assembly
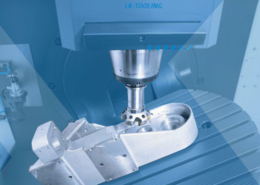