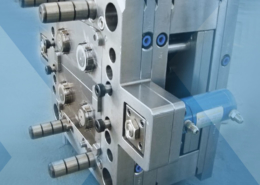
Materials: Novel Nylon 66 and Modified PPE Foams for Automotive - ppe injection
Author:gly Date: 2024-09-30
The TOP 700 can achieve delivery rates of over five litres/minute at a maximum pump pressure of 210 bar, so enabling short cycle times both when filling larger parts and with large numbers of small cavities. Additives and colours can be dispensed from 1, 4 and 20 litre containers. In order to achieve the dosing precision that is particularly vital for very small parts, the volumetric meter for colours has a resolution of below 0.1 μl/l. Depending on requirements, dosing can be carried out simultaneously or in a freely selectable mixing ratio.
Graziano Pestarino, Global Account Manager for thermoplastics solutions at Chem-Trend, added: “We know a lot is at stake for processors if the right purge compound and process are not used in colour changeovers amounting to significant time and cost. By combining our years of expertise in the field and our latest advancements in purging technology with that of Husky … plastics manufacturers stand to reap immense benefits of productivity and control previously unachievable.”
Chem-Trend and Husky aim to significantly enhance operational margins by increasing equipment and labour uptime. The collaboration reported an 85 per cent reduction in scrap and an 80 per cent increase in mould cleaning efficiency following early trials.
The team devised a new guided procedure made easily accessible to operators within the Husky Altanium Mold Controller operator interface. The instructions outline a simple, yet highly effective approach to setting up and performing the colour-change process explicitly for moulds with hot runner systems.
Husky Injection Molding Systems, Ltd. has announced its collaboration with Chem-Trend on a system solution that creates repeatability during the critical colour-change process to offer a faster, more accurate, and optimised approach for operators.
The joint approach is based on the process for using Chem-Trend’s Ultra Purge brand of purge compounds, which is designed specifically to reduce colour-change time and carbon formation in hot runner systems.
TOP 700 provides the same high precision dosing of silicones and additives as Elmet’s flagship TOP 7000 Pro dosing system with its 200 or 20 litre drum size which was launched back in 2021.
Due to the optimised design of the follower plates, just 40 ml of residues are left behind when the 20 litre drums have to be changed, resulting in material utilisation of up to 99.8%. With a design service life of 20 years or more for all its mechanical components, a modular structure and particular ease of servicing which keeps maintenance costs low, the TOP 700 is synonymous with cost-efficiency. Its low energy consumption of less than 50 Wh and minimal compressed air consumption also help to keep costs down.
Mike Ellis, Global Business Manager for Husky Hot Runners and Controllers, said: “Fast and effective colour-change processes are essential for our customers, and we are continuing to see an upward trend in colour-change applications. Our collaboration with Chem-Trend and the integration with our Altanium Mold Controllers addresses this critical market requirement and enables our customers to achieve more efficient and effective colour-change performance.”
Thorsten Häuser, development manager, explains: “We developed our TOP 700 dosing pump to meet customer demand for a space- and material-saving solution from ELMET. We’ve achieved this with a footprint of less than 0.5 m² (799 mm × 600 mm) and our new pump design. As a result, this new dosing system is particularly suitable not only for customers processing high-value, shear-sensitive or abrasive materials but also for R&D, prototyping and small-batch applications. The TOP 700 rounds out our product range while setting new standards in compact dosing technology.”
To avoid operating errors, the drums can be changed fully automatically from the drum rim from three sides within two minutes. Intuitive operation of the system, the use of simple clamp connections, a guided drum change procedure and an integrated cooling system mean even relatively low-skilled personnel can operate it without any problem. Fully automatic venting as standard completes the system’s many and varied safety and convenience features.
Designed to be FDA- and EMA-compliant, the new TOP 700 dosing system is used for applications requiring the highest levels of cleanliness such as medical technology, personal care, foodstuffs and optics. Virtually abrasion-free pumping also prevents metal particle contamination of the LSR which would impair its functionality. There are also no limits to the consistency of the processed LSR under real-world conditions because Elmet’s new system can dose any commercially available product with the same precision thanks to its ability to handle viscosities of between 0.001 Pas and 2000 Pas (shear rate 10/s) or 16,000 Pas (1/s). Its optionally OPC UA- and Euromap 82.3-compliant control system can be seamlessly integrated into the injection moulding machine’s own control system.
GETTING A QUOTE WITH LK-MOULD IS FREE AND SIMPLE.
FIND MORE OF OUR SERVICES:
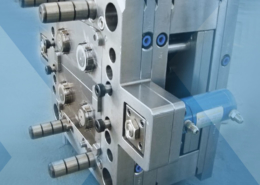
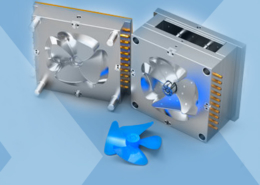
Plastic Molding

Rapid Prototyping
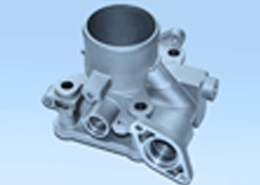
Pressure Die Casting
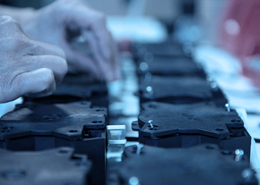
Parts Assembly
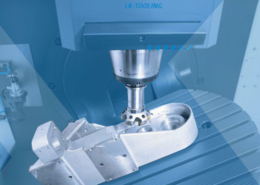