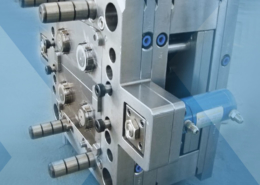
Materials: Novel Nylon 66 and Modified PPE Foams for Automotive - ppe injection
Author:gly Date: 2024-09-30
Pomerleau, J. & Sanschagrin, B. Injection molding shrinkage of PP: experimental progress. Polym. Eng. Sci. 46(9), 1275–1283 (2006).
All data generated or analyzed during this study are included in this published article and its supplementary information files.
According to the injection molding results shown in Table 9, the influence degree of the process parameters on the grey correlation data is: holding time > mold temperature > cooling time > holding pressure > melt temperature.
According to the injection molding results shown in Table 4, the influence order of various process parameters on warpage is: holding time > melt temperature > holding pressure > cooling time > mold temperature.
Thank you for visiting nature.com. You are using a browser version with limited support for CSS. To obtain the best experience, we recommend you use a more up to date browser (or turn off compatibility mode in Internet Explorer). In the meantime, to ensure continued support, we are displaying the site without styles and JavaScript.
According to Table 10, the average SNR and range of each process parameter are calculated, and the results are shown in Table 11.
After comprehensively considering the quality requirements of hydrogen storage cylinder lining and actual production experience, five factors were selected, including melting temperature, mold temperature, holding pressure, holding time and cooling time, recorded as A, B, C, D and E, respectively. Based on the number of factors selected in the orthogonal test, four levels of each factor were selected uniformly by combining the recommended parameters and the actual injection molding experience. Table 2 shows the process parameters in the simulation. According to the principle of the orthogonal test, the orthogonal test table L16(45) was established. And the process parameters of 16 combinations in the table were analyzed by Moldflow software.
Xie, P. et al. Effect of gate size on the melt filling behavior and residual stress of injection molded parts. Mater. Des. 53, 366–372 (2014).
Different from the orthogonal experiments, Taguchi algorithm introduces the concept of SNR on the basis of orthogonal experiments. In Taguchi algorithm, the index of measuring test results is no longer a certain analysis data. Instead, the analysis is converted into an SNR28.
Hassan, H., Regnier, N. & Defaye, G. A 3D study on the effect of gate location on the cooling of polymer by injection molding. Int. J. Heat Fluid Flow 30, 1218–1229 (2009).
Cylinder liner mold assembly drawing. 1. Floor 2. Push rod fixing plate 3. Push rod 4. Push rod 5. Dynamic die fixing plate 6. Dynamic die 7. Fixed template 8. Guide sleeve 9. Positioning ring 10. Gate sleeve 11. Screw 12. Fixed template floor 13. Type cavity inserts 14. Dynamic template 15. Push rod 16. Recoil pin 17. Spring 18. Floor rod.
k1, k2, k3 and k4 donate the average of the sum of each factor index at four levels, and the difference is R. Through the analysis of the warping process range, a better combination of process parameters A4B2C3D3E3 can be obtained. When the melt temperature reaches 270 °C, the mold temperature reaches 80 °C, the holding pressure is 55 MPa, the holding time is 20 s, and the cooling time is 18 s. The optimum combination was not in the test times, the optimized molding process parameters were entered into Moldflow software for analysis and verification. The final result is shown in Fig. 4, with a warping of 0.5185 mm.
At this time, a set of re-optimized process parameters can be obtained. The optimized combination parameters are expressed as A4B2C2D3E2. When the melt temperature reaches 270 °C, the die temperature reaches 80 °C, the packing pressure is 55 MPa, the packing time is 20 s, and the cooling time is 13 s. The simulation results of the process parameters in Moldflow software are shown in Figs. 8, 9, 10 and 11. The warpage is 0.5041 mm, the volume shrinkage is 12.4%, the residual stress in the first direction is 97.88 MPa, and the residual stress in the second direction is 114.1 MPa.
Through orthogonal experiments, the effects of molding parameters on volume shrinkage, warpage, first residual stress and second residual stress of cylinder liner were studied, and the optimal combination of molding parameters corresponding to four groups of evaluation indexes was obtained. The experimental results of four evaluation indexes under the combination of 16 groups of different process parameters are shown in Table 3.
The SNR and ANOVA were carried out. In order to minimize the comprehensive evaluation index value of the bottle liner, the SNR was analyzed. The optimum technological parameters were obtained as follows: A2B4C4E4E4. Under this technological parameter, the optimum warpage was 0.4892 mm, the volume shrinkage was 12.31%, the first direction residual stress was 98.13 MPa, and the second direction residual stress was 108.1 MPa. ANOVA was used to determine the significance of each factor in experimental research. After analysis, it was found that the melt temperature has the greatest influence on the comprehensive index, accounting for about 62.15%, followed by a pressure holding time and cooling time.
Plastic Innovation of Austria is hoping to resurrect the 1980s idea of injection-molded cycle frames. Such frames used to snap, made by companies which flopped in more ways than one.
Xu, G. & Yang, Z. Multiobjective optimization of process parameters for plastic injection molding via soft computing and grey correlation analysis. Int. J. Adv. Manuf. Technol. 78(1–4), 525–536 (2015).
Shen, Y.-K. et al. Analysis for optimal gate design of thin-walled injection molding. Int. Commun. Heat Mass Transf. 35, 728–734 (2008).
Zhao, P. et al. A Nondestructive online method for monitoring the injection molding process by collecting and analyzing machine running data. Int. J. Adv. Manuf. Technol. 72, 765–777 (2014).
The cylinder liner mainly acts as a barrier to hydrogen. This simulation uses ammonium polyphosphate (PA6). The main performance indicators are shown in Table 1.
Anovitz, L., Smith, B. Lifecycle Verification of Tank Liner Polymers; Oak Ridge National Lab. (ORNL): Oak Ridge, TN, USA, (2014). [CrossRef] storage vessel
Hydrogen is an important renewable and sustainable energy source with the advantages of zero pollution, a high energy conversion rate and an abundance of resources. The wide application of hydrogen energy requires solving the problems of hydrogen production, storage and transportation. Hydrogen storage technology is the key to hydrogen utilization1. Among them, a hydrogen storage cylinder is the most commonly used way of hydrogen storage, consisting of a lining and a composite winding layer. At present, the cylinders can be divided into type III aluminum liner and type IV polymer liner2. High density polyethylene (HDPE), polyamide (PA6), or PET(Polyethylene terephthalate) are the primary materials utilized to create type IV cylinder linings3. In general, injection molding is one of the methods of lining molding. The plastic molding technology, namely, the combination of metal head and resin lining molding, is used to produce lining through injection molding4.
Kima, H. S., Sonb, J. S. & Imc, Y. T. Gate location design in injection molding of an automobile junction box with integral hinges. J. Mater. Process. Technol. 140, 110–115 (2003).
Sateesh, N., Reddy, S. D., Kumar, G. P. & Subbiah, R. Optimization of injection moulding process in manufacturing the top cap of water meter. Mater. Today Proc. 18, 4556–4565 (2019).
Liu, X. Design of complex side core-pulling injection mold for automotive headlight housing. Eng. Plast. Appl. 49(11), 99–103+108 (2021).
Md Yusof, M. & Abu Mansor, M. S. Alternative method to determine parting direction automatically for generating core and cavity of two-plate mold using B-rep of visibility map. Int. J. Adv. Manuf. Technol. 96, 3109–3126 (2018).
The benefits of an injection-molded cycle frame are obvious – manufacturing is swift (just pop them out of mold every minute or so), and they won’t rust. Complex shapes can also be achieved.
Chen, S.-C. et al. Effect of cavity surface coating on mold temperature variation and the quality of injection molded parts. Int. Commun. Heat Mass Transf. 36(10), 1030–1035 (2000).
For simultaneous analysis of four evaluation indicators, residual stress in the first direction and residual stress in the second direction, the range analysis of grey correlation analysis was carried out. The best combination of process parameters was discovered when the process parameters were set to A4B2C2D3E2 (when the melt temperature reaches 270 °C, the die temperature reaches 80 °C, the packing pressure is 55 MPa, the packing time is 20 s, and the cooling time is 13 s) The optimal warpage, volume shrinkage, residual stresses in the first direction and residual stresses in the second direction were 0.5041 mm, 12.4%, 97.88 MPa and 114.1 MPa, respectively.
The above analysis showed that mean and range processing is an effective method to analyze and optimize single factors. However, these methods cannot be used simultaneously to optimize multiple objectives. In order to optimize the multi-objective data and carry out a comprehensive analysis to achieve the goal of this study, we introduced grey correlation analysis27.
Lasn, K. & Echtermeyer, A. Safety approach for composite pressure vessels for roadtransport of hydrogen. Part 1 Acceptable probability of failure and hydrogend mass. Int. J. Hydrogen Energy 39(26), 1413e241 (2014).
The reasonable setting of the feeding system affects the quality of the parts. Selecting the proper gate number and location may not only increase forming efficiency but also guarantee the quality of the components. Considering the shape of the lining structure and to ensure a smooth surface shape, after a comprehensive analysis, the end of the barrel section away from the metal head was chosen as the pouring position. Considering the parting surface and pouring position, the submerged gate pouring was selected. When the mold was opened, the gate can be automatically separated from the plastic part under the tension of the template. Figure 2 shows a mold with a two-cavity hydrogen storage cylinder lining structure and gate system, taking into account the injection molding machine's current structure and lining structure.
Through the analysis of the first direction residual stress process range, better process parameters combinations A4B2C1D3E4 can be obtained. When the melt temperature reaches 270 °C, the mold temperature reaches 80 °C, the holding pressure is 50 MPa, the holding time is 20 s, and the cooling time is 23 s. The optimum combination is not in the test times, the optimized molding process parameters are input into Moldflow software for analysis and verification. The final result is shown in Fig. 6. The residual stress in the first direction is 98.43 MPa.
Ozcelik, B., Kuram, E. & Topal, M. M. Investigation the effects of obstaclegeometries and injection molding parameters on weld line strength usingexperimental and finite element methods in plastic injection molding. Int. Commun. Heat Mass Transf. 39, 275–281 (2012).
Researchers have used a variety of optimization techniques in injection molding over the last few decades to lower various defect rates. Researchers used the experimental design (DOE) approach to perform a pilot thorough investigation of the injection molding process since warpage and shrinkage are two major injection molding defects. For warpage and shrinkage prediction, the neural network method is used to significantly reduce the defect rate21,22. The neural network has become a powerful and practical method for modeling highly complex nonlinear systems. In order to determine the optimum level of design parameters, a genetic algorithm is applied to the optimization of injection molding parameters of plastic parts23,24. Taguchi, another method for improving the quality of injection molded parts, is a robust parameter design technology, and shrinkage optimization plays a major role in determining the final size of injection molded parts. This method also determines the optimal level of each process parameter to reduce shrinkage and warpage in thin-walled products25,26. ANOVA (analysis of variance) and SNR (signal-to-noise ratio) are used for data analysis to determine the importance of factors, provide the initial optimal combination of process parameters, and obtain the contribution percentage of quantitative factors27,28. Grey correlation analysis is usually used in data processing of Taguchi orthogonal test to transform a multi-objective problem into a single-objective problem, which is beneficial for analyzing comprehensive data from tests29,30.
However, many of the frames and plastic components snapped in use, most of the parts were proprietary and therefore difficult replace, and the Itera was said to be uncomfortable to ride. Nevertheless, it’s estimated that in the four years the Itera was made 30,000 units were sold around the world.
The minimum characteristic warping value is set to Y1, and SNR is set to η1. The minimum volume shrinkage eigenvalue is set to Y2, the corresponding SNR value is η2, the minimum first residual stress is set to Y3, SNR is set to η3, the minimum second residual stress is set to Y4, and SNR is set to η4. The total SNR is as follows:
This research is supported by the National Natural Science Foundation of China (Grant number 52075361), the Major Science and Technology Project of Shanxi Province (Grant number 20201102003) and the Key Research and Development Projects in Shanxi province (Grant number 201903D421030).
Ozcelik, B. Optimization of injection parameters for mechanical properties of specimens with weld line of polypropylene using Taguchi method. Int. Commun. Heat Mass Transf 38(8), 1067–1072 (2011).
Graphics in the video above show that Plastic Innovation has been working wih Peugeot to produce CAD drawings of its proposed frames, which could be made from recycled plastics.
The purpose of ANOVA is to investigate which factors significantly affect performance characteristics. The ratio of deviation square sum and total deviation square sum for each factor in variance analysis reflects the influence of process parameters on test indexes. In this paper, \(\overline{{I_{{\text{j}}} }}\) is the average SNR of a certain experimental factor at a certain level, and the average signal-to-noise ratio of all levels of all experimental factors are taken.
\({\text{x}}_{{\text{i}}}^{*} (k)\) represents the gray relational values, max \({\text{x}}_{{\text{i}}}^{*} (k)\) and min \({\text{x}}_{{\text{i}}}^{*} (k)\) respectively represent the largest and the smallest values in the \({\text{x}}_{{\text{i}}}^{*} (k)\) sequence.
Analysis of warpage results: The warpage test data in Table 3 were analyzed by the range analysis method, and the analysis results are shown in Table 4.
\(\xi_{{\text{i}}} (k)\) represents the gray relational coefficients, \(\Delta_{{0{\text{i}}}} (k)\) represents the sequence differences between corresponding positions in sequence \(x_{0} (k)\) and subsequence \(x_{{\text{i}}} (k)\), \(\xi\) represents the identification coefficient (generally, 0.5).
According to the injection molding results shown in Table 6, the influence order of the process parameters on the residual stress in the first direction is: melt temperature > cooling time > mold temperature > holding pressure > holding time.
The SNR of small characteristics is a monotonically decreasing function, and the larger the value, the better the SNR. Therefore, in the average analysis of hydrogen storage cylinder liners, the minimum value of the total SNR should be obtained at the maximum SNR. It can be seen from the table that the optimal process parameters corresponding to the total SNR range analysis are A2B4C4E4E4, that is, the corresponding process parameters are: melt temperature is 250 °C, mold temperature is 100 °C, holding pressure is 65 MPa, holding time is 25 s, cooling time is 23 s. The simulation results of the process parameters are shown in Figs. 12, 13, 14 and 15. The warpage is 0.4892 mm, the volume shrinkage is 12.31%, the residual stress in the first direction is 98.13 MPa, and the residual stress in the second direction is 108.1 MPa.
Song, Z. et al. Optimization and prediction of volume shrinkage and warpage of injection-molded thin-walled parts based on neural network. Int. J. Adv. Manuf. Technol. 109, 755–769 (2020).
Dicheng, F. Design of injection mold for automotive cable connector based on CAD/CAE. Plast. Technol. 48(06), 102–108 (2020).
where \(\overline{{I_{{\text{j}}} }}\) —the average value of a certain experimental factor at a certain level ; \(\overline{Y}\)—Mean value of all test factors at all levels.
Analysis of residual stresses in the second direction: Range analysis of residual stresses in the second direction in Table 3. The analysis results are shown in Table 7.
The analysis in Table 12 shows that melt temperature is the most important factor affecting the four analyzed parameters. Compared with the other four factors, the influence of melt temperature on the four factors is 62.15%, accounting for the leading role, while the influence of holding pressure on the four factors is 4.15% (Supplementary file). The effect of mold temperature, holding time and cooling time on the four factors are 6.40%, 12.82% and 12.48%, respectively. The order of four factors is melt temperature > holding time > cooling time > mold temperature > holding pressure.
In this paper, the hydrogen storage cylinder liner structure needs to be molded by injection molding on the base of the metal head. Therefore, the core, cavity and ejection mechanisms of the hydrogen storage container liner injection model were designed, and the mold parts were established by 3D software. The mold design required not only the above mentioned parts but also the mold frame, gating system, cooling system, ejection mechanisms and exhaust system be supported. The three-plate mold frame and double cavity mold were used, and the latent gate was used in the gating system. Cooling channels were provided in the cavities and cores. The injection parts were ejected by a hydraulic ejector bar. A large amount of gas generated in the molding process will be carried away through the gap between the inserts. The final two-dimensional engineering diagram is shown in Fig. 3.
To minimize the comprehensive evaluation index value of cylinder liner plastic parts, this paper uses the SNR function of the small characteristic to calculate its SNR. The larger the SNR is, the smaller the target value is, and the better the quality performance is. SNR is calculated according to the following formula:
"The business model of Plastic Innovation GmbH combines two major innovations," claims the company. "The implementation of the bicycle industry’s new method of manufacturing frames using injection molding together with the innovative business model of rethinking bicycle design."
The components that make up an injection mold are referred to as the molding parts, and typically include the core, cavity, different molding rods, and molding inserts. Forming parts can be divided into installation parts and working parts. To produce plastic components, working parts come into close contact with the plastic parts33. In order to lower the cost of the die, it is advantageous to process and manufacture the structural design of die components in a way that is both convenient and easy to acquire qualified parts34.
Analysis of volume shrinkage results are shown in Table 3 and the analysis results are shown in Table 5, where the influence order of the process parameters on the volume shrinkage rate is: holding time > melt temperature > mold temperature > holding pressure > cooling time.
Xianbing, C., Yifei, C. & Yuanji, S. Design and CAE optimization analysis of injection mold for set-top box pouring into the same mold and different cavity. Eng. Plast. Appl. 49(08), 87–92 (2021).
Li, J., Zhao, C., Jia, F. et al. Optimization of injection molding process parameters for the lining of IV hydrogen storage cylinder. Sci Rep 13, 665 (2023). https://doi.org/10.1038/s41598-023-27848-1
Analysis of residual stresses in the first direction is indicated in Table 3 and the analysis results are shown in Table 6.
J.L and C.J.Z designed this study. J.L. did most of the laboratory analysis and wrote the first draft of the paper. S.H.M contributed to data interpretation and manuscript revision. F.L.J and S.Y.L participated in the experimental analysis and sample collection. J.G.L put forward constructive suggestions.
Injection molding (IM) is a popular polymer processing technology for the manufacture of plastic products with complex shapes, high precision and low cost, resulting in products with high quality and good dimensional tolerances5,6. Mode design and process parameters can improve the quality of injection molded parts. One of the main tasks of mold design is gate design7. The gate is the first orifice where the material is injected into the cavity. It has been demonstrated that an appropriate gate size and runner aid in the quick injection of molten plastic into the cavity, enhance the product's mechanical characteristics and aesthetics, and lessen warping and residual stresses in injection-molded components8,9. Another factor in the design of the mold is the number of gates. Setting two gates on both sides of the product as opposed to only one on one side will enhance the turbulence of molten plastic. Another significant element influencing the quality of injection-molded products is the gate position in the mold design. Injection molded components can solidify faster and with fewer flaws if the gate is placed properly10,11,12,13.
Mean and range analyses were performed. The warpage, volume shrinkage, residual stress in the first direction and residual stress in the second direction of the cylinder were selected as the experimental evaluation indexes, and different molding process parameters such as melt temperature, mold temperature, packing pressure, packing time and cooling time were used as the experimental level factors. The results showed that the minimum warpage process combination was A4B2C2D3E3; the minimum volume shrinkage process combination was A1B2C3D3E4; the process combination with minimum residual stress in the first direction was A4B2C1D3E4; the process combination with minimum residual stress in the second direction was A3B2C2D3E2;
By submitting a comment you agree to abide by our Terms and Community Guidelines. If you find something abusive or that does not comply with our terms or guidelines please flag it as inappropriate.
Hou, B. et al. A hybrid hint-based and fuzzy comprehensive evaluation method for optimal parting curve generation in injection mold design. Int. J. Adv. Manuf. Technol. 112, 2133–2148 (2021).
Parting surface of cylinder liner. 1. Positioning ring 2. Fixed template floor 3. Fixed template 4. Dynamic die 5 PS surface 6. guide post.
Through the analysis of Table 5, a better process parameter group A1B2C3D3E4 can be obtained. When the melt temperature reaches 240 °C, the mold temperature reaches 80 °C, the holding pressure is 60 MPa, the holding time is 20 s, and the cooling time is 8 s. The optimum combination is not in the test times, the optimized molding process parameters are input into Moldflow software for analysis and verification. The final result is shown in Fig. 5. The volume shrinkage rate was 12.66%.
According to the structure and process requirements of hydrogen storage cylinder liners, the cylinder liner forming mold was designed. The mold had two cavities, and the core was extracted using a hydraulic auxiliary method.
The influence of process parameters on the evaluation index was further optimized by grey correlation analysis and Taguchi algorithm based on SNR.
According to the injection molding results shown in Table 7, the influence order of the process parameters on the residual stress in the second direction is:holding time > mold temperature > melt temperature > holding pressure > cooling time.
The PS is the part that can be contacted when the moving mold and the fixed mold are closed, and the parting surface is where the plastic part is removed from the mold. The design of PS directly affects the product quality, mold structure and the difficulty of operation, and is one of the key factors for the success of mold design. When determining the parting surface, the location of the plastic part in the mold, the design of the cavity gating system, the structural manufacturability of the plastic part, the mold fabrication, venting and the operation process must be considered in conjunction with the design features of the hydrogen storage cylinder liner. After considering the above characteristics, the lining parting surface diagram was obtained, as shown in Fig. 131,32.
Lizhen, I. et al. Optimization of molding process parameters of automobile gear lever based on orthogonal test. China Plast. 33(7), 50–56 (2019).
The comparison of ANOVA and ANOVA shows that the degree of influence of each factor is consistent, but ANOVA can more intuitively see the influence of each factor on the index.
Therefore, we chose the grey relation modeling equation to determine the grey relation coefficient. As shown in Eq. (1), the SNR of each single quality feature was normalized by grey correlation generation. The normalized value is between 0 and 1. Subsequently, the deviation sequence (2) was used to calculate the difference between the values of the reference sequence and pretreatment . After data preprocessing, grey correlation analysis (3) was used to process normalized data to calculate grey correlation coefficient, which represents the relationship between actual and ideal normalized analysis results. After calculating the grey correlation coefficient of all 16 iterations, the grey correlation degree (4) was calculated by averaging the grey correlation coefficient values corresponding to each evaluation index.
The grey correlation degree of a comprehensive evaluation of hydrogen storage cylinders is derived from formula (1) to formula (4). At this time, the four factors multi-objective evaluation index problem can be transformed into a single objective evaluation index problem. The results are shown in Table 8. The grey correlation data were processed by the range and mean analysis, and the results are shown in Table 9.
In order to visualize the influence of various factors on warpage deformation, a range analysis was introduced. The range is the difference between the maximum and minimum values of the average value of each parameter test result at different levels35. The larger the range value, the greater the impact of the coefficient on the index and the higher the impact on evaluation indicators.
The percentage contribution of each factor to the SST sum of squares can be used to assess the importance of process parameter variations on the performance characteristics. In addition, the F value shown in Table 12 can also be used to determine which factors have significant effects on performance characteristics. Typically, changes in deterministic factors have a significant effect on performance characteristics when the F-values are large.
The most famous plastic bicycle (if we discount carbon composite bicycle frames, that is) was the Itera bicycle of Sweden. This was born from a massive 1978 grant from the Swedish National Board for Technical Development. By 1980 a rideable bicycle – of sorts – was demonstrated by the Itera Development Center AB, and in the following year the first mass-produced Itera bikes were shown to prospective retailers and to the press.
Almeida, F. D., Sousa, V. F. C., Silva, F. J. G., Campilho, R. D. S. G. & Ferreira, L. P. Development of a novel design strategy for moving mechanisms used in multi-material plastic injection molds. Appl. Sci. 11(24), 11805 (2021).
In fact, injection moulding has a long history in bicycle manufacturing. One of the first was made from injection-molded Lexan in 1973. The Original Plastic Bike Inc had been founded in 1971, and took out magazine adverts, but it sold very few, if any, of its proposed products.
Hentati, F. et al. Optimization of the injection molding process for the PC/ABS parts by integrating Taguchi approach and CAE simulation. Int. J. Adv. Manuf. Technol. 104, 4353–4363 (2019).
Another factor determining the quality of injection parts is process parameters; such as injection temperature, mold temperature and injection time, which they directly affect the production cost and quality. Unreasonable process parameters will lead to different defects in the final product, such as warping, shrinkage and residual stress, thereby reducing the mechanical properties of injection molded parts17,18,19,20. When manufacturing the cylinder liner, the process parameters will affect the quality properties, such as weld marks, under-injection and so on, increasing the waste rate.
By analyzing the residual stress process range in the second direction, a better combination of process parameters A3B2C2D3E2 can be obtained. When the melt temperature reaches 260 °C, the die temperature reaches 80 °C, the holding pressure is 50 MPa, the holding time is 20 s, and the cooling time is 13 s. The optimum combination is not in the test times, the optimized molding process parameters are input into Moldflow software for analysis and verification. The final result is shown in Fig. 7. The residual stress in the second direction is 136.8 MPa.
Li, K., Yan, S., Pan, W. & Zhao, G. Warpage optimization of fiber-reinforced composite injection molding by combining back propagation neural network and genetic algorithm. Int. J. Adv. Manuf. Technol. 90, 963–970. https://doi.org/10.1007/s00170-016-9409-3 (2017).
The company’s website is yet to be populated. However, from the awards information it appears that the company is seeking to mainly license its technology rather than make its own products. "The awareness of the new design options must first be created at the OEMs," says a company blurb.
The hydrogen storage cylinder lining was taken as the research object. The injection model of the cylinder liner was developed employing 3D software, a two-cavity injection molding system was built, and Moldflow was utilized for analysis to determine the best combination of injection molding process parameters. The effects of injection process parameters (melt temperature, mold temperature, holding pressure, holding time and cooling time) on the evaluation index were analyzed by orthogonal experiment L16(45). The prediction data of IV hydrogen storage cylinder lining under different parameters were obtained by the range analysis method. The multi-objective optimization problem of injection molding process was transformed into a single-objective optimization problem by using the grey correlation analysis method. The optimal parameters such as melt temperature 270 °C, mold temperature 80 °C, packing pressure 55 MPa, packing time 20 s and cooling time 13 s were obtained. Taguchi method was adopted to obtain SNR (signal-to-noise ratio), while range and variance methods were used for analysis. The results showed that warpage was 0.4892 mm, the volume shrinkage was 12.31%, the residual stress in the first direction was 98.13 MPa, and the residual stress in the second direction was 108.1 MPa. The comprehensive index was simultaneously most impacted by the melt temperature.
Li, C.-L. Design of flip-chip injection mold for chassis top cover based on CAE technology. Plastics 49(04), 50–54 (2020).
Hirscher, M. et al. Materials for hydrogen-based energy storage e past, recent progress and future outlook. J. Alloys Compd. 827, 153548 (2020).
In this paper, the injection mold for IV-type hydrogen storage cylinder lining is designed. The injection molding process parameters were studied. The optimum combination of process parameters was selected after range analyses of each assessment index. To determine the level of each parameter's effect on the overall assessment index, two additional analytic techniques are used: grey correlation degree and Taguchi and SNR. On this basis, the injection molding process parameters are simulated and verified.
Kramschuster, A. et al. Effect of processing conditions on shrinkage and warpage and morphology of injection moulded parts using microcellular injection moulding. Plast. Rubber Compos. 35(5), 198–209 (2006).
Li, K., Yan, S.-L., Pan, W.-F. & Zhao, G. Optimization of fiber-orientation distribution in fiber-reinforced composite injection molding by Taguchi, back propagation neural network, and genetic algorithm–particle swarm optimization. Adv. Mech. Eng. https://doi.org/10.1177/1687814017719221 (2017).
An important parameter considered in the design and manufacture of plastic parts is the parting surface (PS), which depends on the complexity of the parts and directly affects the design of the mold. One of the most time-consuming activities in mold design is to determine the parting surface14, which is mostly due to the fact that a variety of component geometry and pouring process-related elements must be taken into account when determining the parting surface. A reasonable parting surface helps simplify the mold structure and reduce costs15,16.
So, if Plastic Innovation GmbH has truly figured out a way to mass-produce rideable, long-lasting, non-floppy injection-molded cycle frames it would be on to a winner. As reported by Cycling Industry News, the company has already won an award: its “bicycle of the future” concept bagged an Austrian Greenstart gong.
Orthogonal experimental optimization technology, an experimental method to study multiple factors and levels, employs different orthogonal arrays to minimize the number of experiments, thereby reducing the time and cost25. The purpose of the experimental study must be established before designing orthogonal experiments. The experimental measurement indicators are developed in accordance with the objectives of the experimental study to determine the influencing factors of the experiment.
Toe, C. Shrinkage behavior and optimization of injection molded parts studied by the Taguchi method. Polym. Eng. Sci. 41(5), 703–711 (2001).
Wu, H., Wang, Y., & Fang, M., Study on Injection molding process simulation and process parameter optimization of automobile instrument light guiding support. Adv. Mater. Sci. Eng. https://doi.org/10.1155/2021/9938094 (2021).
Open Access This article is licensed under a Creative Commons Attribution 4.0 International License, which permits use, sharing, adaptation, distribution and reproduction in any medium or format, as long as you give appropriate credit to the original author(s) and the source, provide a link to the Creative Commons licence, and indicate if changes were made. The images or other third party material in this article are included in the article's Creative Commons licence, unless indicated otherwise in a credit line to the material. If material is not included in the article's Creative Commons licence and your intended use is not permitted by statutory regulation or exceeds the permitted use, you will need to obtain permission directly from the copyright holder. To view a copy of this licence, visit http://creativecommons.org/licenses/by/4.0/.
Wang, G., Wang, G., & Yang, G. Study on automotive back door panel injection molding process simulation and process parameter optimization. Adv. Mater. Sci. Eng. https://doi.org/10.1155/2021/9996423 (2021).
Xu, Y. et al. Optimization of injection molding process parameters to improve the mechanical performance of polymer product against impact. Int. J. Adv. Manuf. Technol. 76(9–12), 2199–2208 (2017).
"Our services accompany the customer from the design to the manufacturing process in the sense of integral planning with the aim of placing the product on the market in the best possible way."
GETTING A QUOTE WITH LK-MOULD IS FREE AND SIMPLE.
FIND MORE OF OUR SERVICES:
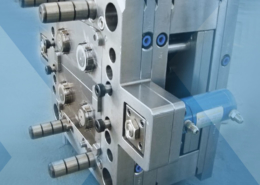
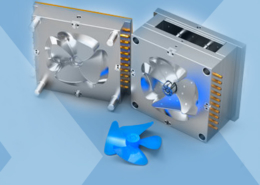
Plastic Molding

Rapid Prototyping
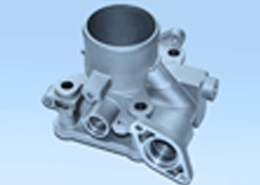
Pressure Die Casting
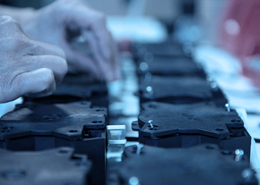
Parts Assembly
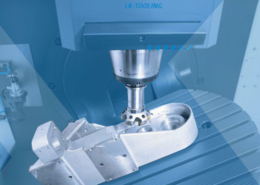