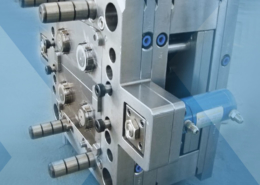
Materials: Cycle Time: Science vs. Rules of Thumb—Part 5 - scientific injection
Author:gly Date: 2024-09-30
Arterex describes itself as a multi-capability medical device contract manufacturing platform resulting from the combination of NextPhase, Formula Plastics, Kabo, Luc & Bel, and ModenPlast. The company produces Class I, II, and III disposable and electromechanical devices at eight facilities across the United States, Mexico, Italy, and Egypt.
Medical device developer and contract manufacturer Arterex has announced the acquisition of Micromold Inc. Riverside, CA–based Micromold has been supplying custom precision micro-molded plastic parts to medical device OEMs since 1984. The company is equipped with 20 Boy injection molding machines ranging from 10 to 33 tons in vertical and horizontal configurations.
Micromold will transfer its 24/7 operations to a 3,000-square-foot Class 8 cleanroom in Arterex’s Formula Plastics division in Tecate, Mexico. Micromold will continue to serve the medical, diagnostics, optical, dental, and laboratory markets, working under the ISO 13485:2016 quality system, said Arterex in the news release. The facility is registered with FDA.
Fusible-core injection molding technology has been employed to mold a fuel housing for an aircraft using PEEK (polyetheretherketone) resin supplied by Victrex (West Conshohocken, PA). The solution reportedly delivers a 30% cost saving and up to 50% weight reduction versus existing metal designs.Processor Egmond Plastic was able to consolidate the number of parts using a carbon fiber reinforced grade of Victrex PEEK polymer. A separate bearing, for example, was eliminated since it is now integrated into the overall design of the housing.Fuel housing molded for CF-PEEK compound using fusible core process.Fuel housings for aerospace applications have very complex inner geometries which are not moldable using conventional injection molding technology. Egmond Plastic's fusible-core technology enables moldings of complex hollow housings, manifolds, and pipes. Richard Brandwijk, Managing Director at Egmond Plastic, explains: "Our technology, in combination with carbon fiber reinforced Victrex PEEK polymer, delivers numerous benefits. These include cost reduction, enhanced manufacturing speed, and weight reduction leading to improved fuel efficiency and reduced CO2 emissions. Along with part consolidation, this exceptional technology and material combination enables the design of very complex parts, beyond the capabilities of standard injection molding and metal processes."Utilizing a near net-shape manufacturing process for the fusible core allows for an 80% time saving versus machined parts. Further, secondary treatments for corrosion protection, such as anodizing, can be eliminated. Lead times can be reduced by 50%. These factors combine to deliver part cost savings of more than 30% versus metal equivalents."The global aerospace industry stands to gain enormously by persistently replacing metals in key applications, in which Egmond has demonstrated tremendous leadership," said Uwe Marburger, Aerospace Business Development Manager at Victrex. "Clearly, our PEEK knowledge and material solutions help enable the use of a technology that addresses some of the toughest challenges in complex aerospace part design and productions."Previously, the end-user had generally specified aluminum for the production of fuel containing parts, but a carbon fiber reinforced PEEK polymer demonstrated superior fatigue performance when compared to aluminum. It does this while meeting all the engineering requirements for this application, including stiffness, effective flame, smoke and toxicity (FST) performance, and resistance to aggressive chemicals, including notably, for this aerospace application, resistance to jet fuel and Skydrol hydraulic fluid. Parts can range in size all the way up to 30 cm x 30 cm x 40 cm (11.8 in x 11.8 in x 15.8 in), and typically the process is used for production runs of up to 2,000 parts.Egmond's unique fusible-core technology has already established a proven track record using Victrex PEEK in a fuel pump for the Eurofighter Typhoon, a jet fighter in use in several European countries. This pump has been in successful operational use for more than 20 years.
The Informa Markets Engineering network of B2B media sites includes Design News, Battery Technology, Medical Device & Diagnostic Industry (MD+DI), Packaging Digest, PlasticsToday, and Powder & Bulk Solids.
Fusible-core injection molding technology has been employed to mold a fuel housing for an aircraft using PEEK (polyetheretherketone) resin supplied by Victrex (West Conshohocken, PA). The solution reportedly delivers a 30% cost saving and up to 50% weight reduction versus existing metal designs.Processor Egmond Plastic was able to consolidate the number of parts using a carbon fiber reinforced grade of Victrex PEEK polymer. A separate bearing, for example, was eliminated since it is now integrated into the overall design of the housing.
"Micromold brings with it over 40 years of expertise from mold design to end customer fulfillment services that allows us to expand our services and capabilities to our growing customer base,” said Arterex President for North America, Bill Gerard. “The company is an ideal addition to our offering of high-quality precision injection molded medical components, assemblies, and product design and development services.”
Micromold will continue injection molding plastic parts for medical device OEMs from Arterex’s FDA-registered facility in Mexico.
GETTING A QUOTE WITH LK-MOULD IS FREE AND SIMPLE.
FIND MORE OF OUR SERVICES:
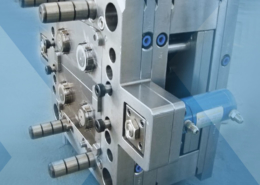
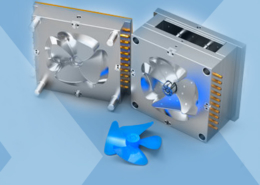
Plastic Molding

Rapid Prototyping
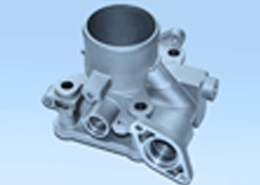
Pressure Die Casting
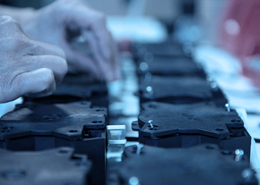
Parts Assembly
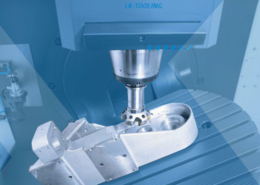