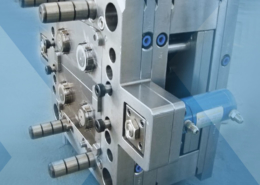
Maserati Shows Off Its New 2021 Quattroporte For North America: - 3k injection m
Author:gly Date: 2024-09-30
At the same time, Makerbot wants to score some of the market share in China’s economy to make up for their less than spot-on predictions about their sales numbers. What do they do? This past November, they partner up with Alipay and, now, Chinese customers have access to Makerbot products to love, use, cherish forever and reverse engineer without consequence. But does China even need to do this?
Sometimes, details of Chinese and American partnerships in the 3D printing industry are hard to come by, but it will be interesting to see how 3D printing companies around the world create new partnerships in 2015.
Take HLH Prototypes, for example, which is one of China’s top 3D printing manufacturing and rapid custom injection molding companies in China. By adding 3D printing to traditional manufacturing techniques, such as injection molding, they are able to quickly make a prototype and then produce significant volumes via rapid injection molding to produce plastic and metal components.
According to Susie Su, a prototyping consultant for HLH, “In their state-of-the art facility, HLH Prototypes is one of the leading 3D printing manufacturers in China. HLH Prototypes offers custom injection molding in China from their UKAS ISO certified facilities.” Like many other industrial designers, they have a team of design engineers who produce drawings for a wide range of programs for a variety of applications. Also, like many industrial design services, clients are given 3D prototypes and models for them to test and evaluate,until a final prototype is designed and produced.
“Their engineers are able to work on plastic injection molds to fit any program requirement regardless of product size and complexity. HLH Prototypes is able to shave weeks off lead times to ensure clients get high quality products on time and every time.”
Most mold manufacturers do not use material flow analysis software as a part of the mold design process as a general rule. Yet, because the mold is such a critical part of the success or failure of the entire molding process, all available tools should be used. That’s the opinion of Rick Carobus, president of EPS Flotek, a mold and material flow simulation service company and reseller of MoldEx 3D analysis software.“This has always been seen as a luxury item by many moldmakers,” Carobus told PlasticsToday at NPE2012. “While they understand that it will save money in the long run, they know it’s not necessary to build or run a mold. Some OEMs will spend money to do an engineering change on the back end, however they won’t spend money to make it right on the front end.”
Generally the process starts with the part designer and from there, in succession, goes to the tool designer, the tool builder, the molder, and finally the parts get to the OEM, Carobus explained. “When the part is delivered and is failing in the field someone wants a simulation analysis. We don’t want to get involved at that point. We want to work with the part designer or the tool designer at the front end of the project because as you move up the ladder, the mold gets more expensive to fix. But, we seem to get involved at the back end about equally with the front end involvement.” OEMs requiring process flow in initial bidThat said, Carobus acknowledges that business has picked up considerably as some markets, such as the automotive industry, require process flow analysis and design validation prior to the mold build. “More advanced industries like the automotive will automatically include mold and material flow analysis in their design,” he noted. “Big companies tend to have this capability in-house, but some will depend on the mold maker to perform an analysis on the part design prior to cutting steel.”Often material suppliers will run a quick analysis to support the use of their material. “Does it really help the OEM or solve any problems?,” asked Carobus. “They might miss things. It’s not just running an analysis but knowing what you’re looking for—looking for real molding conditions and doing it right is what counts. Many companies own the software but don’t optimize the part design or tool design. They spend money then complain they didn’t get the information they needed. But are they using the tool correctly? Even with the stuff that’s easy to use can give you bad results.” Some OEMs depend upon the tool builder to run the analysis. Industrial Molds Group purchased the MoldEx 3D software from ESP Flotek several years ago, however due to a change in personnel, they lost some of the talent that knew how to use it. A few months ago, they re-evaluated the software and decided that it was a good tool, and that they weren’t using it the way it was meant to be used to provide benefits to both their customers and the company. They called in EPS Flotek and had the latest versions of MoldEx 3D installed and provided training to the engineering department. “Now we use MoldEx 3D to check the mold fill on every job before we cut steel,” said Kerry Smith, Industrial Molds’ Engineering Manager. “Filling the mold properly is the first consideration in the mold design and causes the most angst for our customers or their molders. The simulation allows us to look at the gate, the hot runner system and the venting. We look at hot spots and determine how to implement better cooling. It also has the ability to do warp analysis.”“The analysis tool should be used interactively – not behind the scenes in the closet,” commented Carobus. “The part designer, the tool designer, the moldbuilder, the molder and the customer should all work collaboratively. We want to build a tool as efficiently as possible, so we can tell you what happens if you reduce your cycle time by 2 seconds. The customer wants a tool that produces the best quality part, and it helps the moldmaker get them just that.” Old habits die hardOften it’s the life-long moldmaker who resists this type of software because they’ve been building molds for 40 years and think the software doesn’t know more than they do. “It’s not about the software knowing more but that the plastic process has so many variables that one little change in a rib, a gate location, a material can make a huge difference in the part quality, the cycle time savings and in profitability for their customer,” Carobus commented.Smith pointed out that some of the reluctance of smaller shops is the cost involved in purchasing a seat of mold-filling simulation software, which he acknowledges is not cheap. “They say ‘I can’t buy it because the customer won’t pay for it,’” he said. “But what does that mean? What is the cost of not running a mold-filling analysis? The customer will pay for it. He’ll pay for it with a bad tool that runs slower cycles or bad parts. The tool shop will pay for it by reworking a tool—often on their own dime—that doesn’t run right.”For smaller mold manufacturers that don’t have the resources for in-house simulation software or an analyst on staff, there are companies such as EPS Flotek that can perform a full range of engineering services for them using MoldEx 3D simulation software. EPS Flotek offers that service for them on a per-project basis for about $2500 to $3500.Moldex3D can predict the condition of the plastic parts during the molding process to help moldmakers understand how best to design the mold for optimum processability. The advantage to the mold designer and the moldbuilder is that simulation is a value added service. “The moldmaker can tell his customer, ‘We’re making sure you get the best tool and best part up front. We’ll fix anything that’s wrong after the mold is built but we don’t want to have to do that.’”Industrial Molds has realized the mutual benefits gained by both parties, noted Smith. “Performing the mold-fill simulation analysis saves us from doing an extra round of venting or reworking vents and runners,” he said. “On the customer side, they can see proof positive why their original idea for the design of the part, and the type of mold they thought they wanted, might not be the most optimum production mold for the part. Performing the mold fill analysis with the tool maker is the best path.”“In one instance, the customer wanted to use a three-plate mold. The part was captured by slides on all four sides so the runner system was very large. Early on in the design stage we did a quick runner system design to run a mold analysis. The analysis showed us there would be a tremendous amount of scrap, and the cycle time would be extended because of the distances the runners had to flow. We changed the basic mold configuration based on that problem, showed the customer why we needed to change the design, and got approval to change the mold design.”“We got the answer just a few days into the mold design rather than after we’d cut steel,” said Smith. “It was so meaningful for the customer to actually see the problems that would result from the three-plate mold design. It’s one thing to say to a customer ‘I think this is going to be a problem,’ but when you can show them the actual simulation that reveals the problem, that’s the real evidence—not speculation. And we did that in just a few days’ time rather than well into the design cycle.”“By not using mold analysis software, companies are losing out on unrealized profit and unrealized cost savings in design a mold that doesn’t perform optimally. Address the issues up front and everything becomes more efficient,” said Carobus. “It’s like an insurance policy. You don’t notice just how much you’ve saved until something goes wrong.”
Makerbot has created some features that exceed those available in Chinese 3D printers. But the former CEO of Tiertime, GuoGe said that their goal was to become the largest 3D printer manufacturer in the world, and wanted to send 80% of their products to developed economies such as the United States and Europe.
Besides owning 20% of US debt held by foreign nations, they produce a massive amount of goods using traditional manufacturing methods. China is sometimes mistaken as being off the ball or behind the mark when it comes to 3D printing. They are not. China’s 3D printing is estimated to grow to $1.6 billion (USD) by 2016, up from $163 in 2012. The Chinese government has invested around $33 million,which funded an established network of 10 3D printing innovation centers. They aren’t new to the industry and have been involved in R & D since 1992. Many of China’s universities and vocational schools such as Tsinghua University and South China University of Technology offer courses in additive manufacturing.
Andrew Wheeler is a 3D printing and technology journalist. He studied Creative Writing at NYU and received his Bachelor's Degree in Information Technology. He is currently working on a multi-media science fiction project. His favorite journalist of all time is George Orwell.
Besides dealing with the US government to the tune of 20% of US National Debt held by foreign countries, their partnerships in the technology sector trickle down to the growing 3D printing industry. 3D printers are cheaper to manufacture in China, which isn’t really surprising, but is surprisingly not focused on too often.
Until she retired in September 2021, Clare Goldsberry reported on the plastics industry for more than 30 years. In addition to the 10,000+ articles she has written, by her own estimation, she is the author of several books, including The Business of Injection Molding: How to succeed as a custom molder and Purchasing Injection Molds: A buyers guide. Goldsberry is a member of the Plastics Pioneers Association. She reflected on her long career in "Time to Say Good-Bye."
Most mold manufacturers do not use material flow analysis software as a part of the mold design process as a general rule. Yet, because the mold is such a critical part of the success or failure of the entire molding process, all available tools should be used. That’s the opinion of Rick Carobus, president of EPS Flotek, a mold and material flow simulation service company and reseller of MoldEx 3D analysis software.
My point is that China does not, in any way, need to reverse engineer fantastic American products. They are capable of innovating and dominating the 3D printing industry based on their years of experience as the world’s producer of pretty much everything via traditional manufacturing, which is not a hindrance to creating great 3D printers and materials. Their main obstacle is, in my opinion, creating great customer support and really great software for 3D printers. These advantages lay with the US, Europe, and Australia.
They will be attending many events in 2015 to feature the advancement in their services. In March 2015 they will attend the TCT Show + Personalized.
The Up! 3D printer technology was licensed to the US company Microboards Inc., from Tiertime, China’s largest 3D printer manufacturer. They turned it into the Afinia 3D printers, which proceeded to compete well against Makerbot, who have been losing more of their dominant market share since 2009 and a falling short on sales predictions.
GETTING A QUOTE WITH LK-MOULD IS FREE AND SIMPLE.
FIND MORE OF OUR SERVICES:
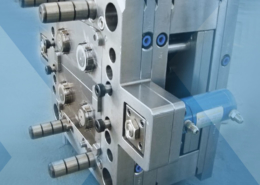
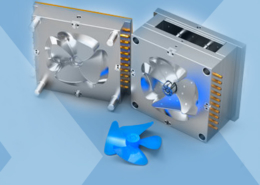
Plastic Molding

Rapid Prototyping
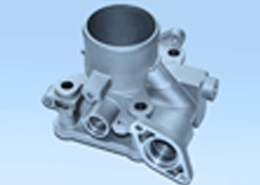
Pressure Die Casting
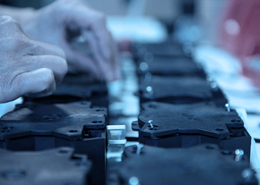
Parts Assembly
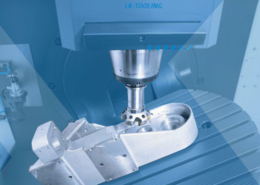