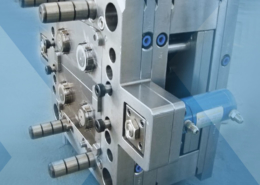
Bottle Cap Injection Molding: Revolutionizing Beverage Packaging
Author:gly Date: 2024-06-08
Bottle cap injection molding stands at the forefront of beverage packaging innovation, shaping the way we seal our favorite drinks. This manufacturing process not only ensures the integrity and safety of beverages but also contributes to environmental sustainability. In this comprehensive exploration, we delve into the intricacies of bottle cap injection molding, unveiling its significance, applications, and future prospects.
Introduction
The humble bottle cap, often overlooked, plays a crucial role in preserving the freshness and quality of beverages. Bottle cap injection molding, a sophisticated manufacturing technique, involves injecting molten materials into a mold cavity to form intricately designed caps with precision and efficiency. This process has revolutionized the beverage industry, offering airtight seals, tamper-evident features, and customizable designs.
Materials and Technology
Material Selection
The choice of materials in bottle cap injection molding is critical to ensure durability, flexibility, and compatibility with different beverage types. Common materials include polyethylene (PE), polypropylene (PP), and polystyrene (PS), each offering unique properties suited for specific applications.
Molding Process
Bottle cap injection molding employs advanced machinery and computerized controls to precisely inject molten material into molds at high pressures and temperatures. The process involves several stages, including mold preparation, material melting, injection, cooling, and ejection, all orchestrated with precision to achieve optimal results.
Design Considerations
Designing bottle caps involves meticulous attention to detail, considering factors such as size, shape, thread specifications, and tamper-evident features. Advanced CAD software allows for intricate designs, ensuring seamless compatibility with various bottle necks and closure systems.
Quality Control and Assurance
Inspection Techniques
Stringent quality control measures are paramount in bottle cap manufacturing to uphold industry standards and consumer safety. Inspection techniques such as visual inspection, dimensional analysis, and leak testing are employed to detect defects and ensure uniformity across production batches.
Regulatory Compliance
Bottle cap manufacturers adhere to stringent regulations and standards set forth by regulatory bodies such as the FDA and ISO. Compliance with these regulations ensures that caps meet hygiene, safety, and environmental requirements, safeguarding consumer health and well-being.
Environmental Sustainability
Material Recycling
The shift towards recyclable and biodegradable materials in bottle cap manufacturing reflects a growing commitment to environmental sustainability. Recycling initiatives and closed-loop systems mitigate plastic waste, reducing the carbon footprint associated with beverage packaging.
Lightweighting
Advancements in lightweighting technologies have led to the development of thinner and lighter bottle caps, conserving resources and minimizing material usage without compromising functionality or performance. These eco-friendly caps contribute to resource efficiency and waste reduction throughout the product lifecycle.
Market Trends and Future Outlook
Innovation and Customization
The beverage industry continually seeks innovative solutions to differentiate products and enhance consumer experiences. Customizable bottle cap designs, interactive features, and branding opportunities offer new avenues for brand engagement and market differentiation.
Automation and Efficiency
Automation and robotics play an increasingly pivotal role in bottle cap manufacturing, driving efficiency, precision, and scalability. The integration of smart technologies and predictive maintenance optimizes production processes, reducing downtime and enhancing overall productivity.
Emerging Technologies
The future of bottle cap injection molding is shaped by emerging technologies such as 3D printing, nanotechnology, and bio-based materials. These innovations promise to further enhance sustainability, functionality, and cost-effectiveness, opening new possibilities for the beverage packaging industry.
Conclusion
In conclusion, bottle cap injection molding represents a cornerstone of beverage packaging innovation, combining precision engineering, quality assurance, and environmental responsibility. As consumer preferences evolve and sustainability imperatives intensify, the industry must continue to embrace technological advancements and best practices to meet the demands of a dynamic market landscape. By prioritizing innovation, sustainability, and consumer safety, bottle cap manufacturers can shape a future where every sip is sealed with excellence.
GETTING A QUOTE WITH LK-MOULD IS FREE AND SIMPLE.
FIND MORE OF OUR SERVICES:
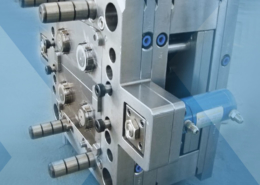
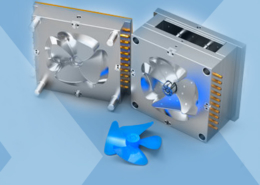
Plastic Molding

Rapid Prototyping
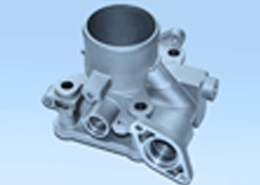
Pressure Die Casting
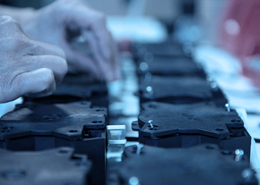
Parts Assembly
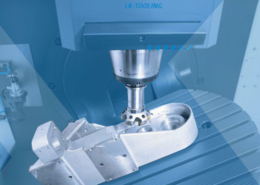