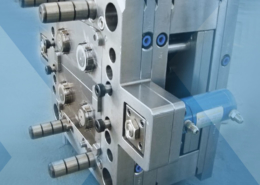
Man crushed to death after 12 ton manufacturing mold falls on top of him at
Author:gly Date: 2024-09-30
In 1920, Alexander Samuels, his brother Solomon Frank Samuels and two other men established Canadian Statuary and Novelty Company to produce stuffies in plush fabrics, smaller novelty toys, and dolls. Another brother, Ben Samuels, later joined the operation. The workspace was cramped into only 500 square feet at the Queen Street location. At first, the owners “imported bisque doll heads from Germany, put it on a body made from a U.S. company and assembled these into their own dolls,” said Delta Museum and Archives. The dolls were popular with customers, sparking a spurt of commercial growth.
MD: How does the introduction of Protolabs Network align with broader industry trends and customer needs in digital manufacturing?
Launching a business after the First World War was an operation of hope for the future after surviving the ache of gruesome war. In the mid-1900s, Reliable Toy Company Limited produced toy soldiers, dolls, riding tractors and an array of innovative, fun items. The Toronto factory transformed from a local business into the largest toy manufacturer in the British Empire.
Lucca Mazzei: Overall, the network allows for tighter tolerances down to ±0.001 in., larger and more complex parts, and more cost-efficient pricing on production orders (more than 5-10 machined parts, for example). Specifically with machining, more complete parts are possible with all features milled, holes tapped and post-process finishing applied.
During World War Two, the Canadian government and Reliable partnered to use injection molding to manufacture oil bottles and bullet tips for military weapons use. There was no factory waste involved—the leftover plastic was transformed into toys. Reliable designers turned their focus to what was considered boys’ toys. Miniature soldiers, fighter jets and Avro Aero fighters, ships, jeeps, tractors, and even a version of Sikorsky helicopters with three blades, came off the line.
In the past—if engineers needed parts within a day, for example—they may have used one manufacturer, but if they had flexibility in their development schedule, they may have had to use a different manufacturer for those parts to get them manufactured at a lower cost. This hybrid model brings both of those worlds together. It lets engineers tailor manufacturing to their specific use cases versus settling on a set of capabilities and constraints.
This website uses cookies to personalize your content (including ads), and allows us to analyze our traffic. Read more about cookies here. By continuing to use our site, you agree to our Terms of Service and Privacy Policy.
About to undergo even greater expansion, the firm “bought the assets of their former competitor, Dominion Toy, in 1933,” said CMC. The Canadian toy market was now their own and generations of children delighted in playtime with colourful Reliable toys. Moving beyond borders, Reliable-brand toys were sold in countries scattered across the globe.
Requiring more workspace, “the company was able to move to a larger building on King Street West where they occupied 3,000 square feet of space,” according to Canadian Museum of Civilization. (CMC) Still too small, the plant shifted again. More than quadrupling floorspace to 13,000 square feet, in 1928 the Reliable factory moved to Phoebe Street near downtown Toronto.
Our technology teams needed to be very creative to not overwhelm customers with newly available options and lose that ease of use, for example. We worked through that challenge by identifying a way to present the expanded offer with additional options appearing only when relevant so we don’t clutter the interface.
Winning the hearts of little girls, sweet-faced dolls were made in 300 engaging versions. By 1936, Reliable’s yearly production soared to 1.5 million dolls. One of the company’s first dolls was “Mama,” a baby doll with an internal device that produced crying sounds when turned over on its back.
MD: How does the transition affect the integration of digital manufacturing and systems, and what technical challenges were encountered (and overcome) during this transition?LM: Protolabs’ customers value our intuitive and streamlined ordering platform, so in everything we do, maintaining that ecommerce experience is vital. With that, the biggest challenge as we integrate Hubs.com into Protolabs.com is that the combined offer is much larger than the individual offers provided on each ordering platform.
Soon, this comprehensive offer will expand to our injection molding and 3D printing customers, with many today already working with their account managers to access the network if our factory capabilities are not a fit.
LM: There are several distributed manufacturing (or marketplace) models in the industry right now, which is what Protolabs Network is. The difference is that Protolabs Network is paired with Protolabs’ in-house factories so engineers essentially have the benefits of both manufacturing models combined into a new hybrid model of sorts. This is something completely unique right now.
Changes were afoot in the overcrowded workplace and the original partnership dissolved in 1922. Owned only by Samuels brothers, the business name changed to Reliable Toy Company Limited. That same year, processes were altered from outsourcing toy components to designing original dolls and producing their own parts.
Furthermore, longtime customers of our factory offering often rely on our automated design-for-manufacturability (DfM) experience. We look forward to expanding our automated DfM tool to network customers, so they can utilize it during early design work to ensure they are optimizing their design based on specific needs.
In addition, the collaboration between both our factory and network technologies allows us to use the best solutions available in each across the larger business. For example, we can use our industry leading DfM analysis tools from our digital factories for the network, along with the advanced geometry analysis we use for digital factory, to better match orders to manufacturing partners’ capabilities. We are also able to use the network’s advanced AI capabilities for our digital manufacturing process.
LM: The business model has “expanded,” as the network adds significant scope to what has been our core value proposition of speed. We can still produce parts fast but also offer the most comprehensive offer in the contract manufacturing space, fulfilling all customer needs from fast prototyping to bridge production to small scale production across all of our technologies. We can now empower customers to make the best outsourcing decisions while continuing to get the best digital experience in the marketplace.
Competitors from the United States and overseas slammed into the Canadian toy market, disrupting the Canadian toymaker’s dominance. In 1985, Allied Sign Letters acquired Reliable Toy Company Limited. The manufacturer was merged “into one of its divisions, Viceroy Manufacturing Company Limited of Toronto.” stated Fortier. “Production soon shifted to the factory of that well-known Canadian toy making firm.”
LM: Protolabs launched as a quick-turn injection molding company 25 years ago, and manufacturing speed was always at its core. But speed isn’t the only thing engineers need when they are procuring parts—they want a broad set of capabilities (larger part envelopes, materials options, finishing options), lower part costs, and higher part quantities. And we heard that through customer feedback.
MD: How has this rebranding/refocus shifted your business model? What, if any, legacy software programs will become obsolete as we iterate and evolve to further SaaS models?
So, that is what the network helps solve. With Protolabs Network layered on top of Protolabs’ existing rapid manufacturing capabilities, this help address those pain points. And since this is through a singular manufacturing source, it streamlines and simplifies the entire manufacturing experience for customers. Like most online-based companies, the end goal is to make the entire experience as user friendly as possible.
Digital manufacturer Protolabs launched its rebranded Protolabs Network service, which is designed to leverage global manufacturing partners for expanded capabilities and pricing options. Formerly known as Hubs, the company says the move signals its commitment to a singular global brand and unified customer experience. The transition comes almost three years after acquiring the Amsterdam-based manufacturing network, which has seen significant annual growth since the 2021 acquisition.
Plating (black oxide, nickel), anodizing (Type II, Type III), and chromate coating options are expanded and can be produced at higher volumes. Maximum part size increases to 40 in. (1,000 mm) with minimum part size down to 0.02 in. (0.5 mm). The network also expands materials to 50+ metals and plastic materials. This complements Protolabs’ factory (in-house, non-network facilities), which are geared towards quick-turn parts in low-volumes.
Machine Design reached out to Lucca Mazzei, strategic growth officer at Protolabs, to learn more about Protolabs Network. Below is the abridged Q&A:
Its business model combines Protolabs’ internal digital factories with a global network of suppliers to provide customers a manufacturing resource throughout a product’s entire life cycle.
By the early 1960s, Reliable pedalled into the ride-on toy department. “The grand champion Canadian toy that is recognized internationally is the world’s first plastic pedal toy—the Reely Ride-em Tractor introduced in 1961, this Reliable original is popular to this day in advanced design,” noted the company catalogue.
Reliable Toys offered the classics—cash registers, a “Tidy Miss Housekeeping Set,” plastic tools, toy telephones, several styles of small swimming pools… and let’s not forget the toy boats to keep every kid happy at the water’s edge. The “Souvenir” section featured a statue of a Mountie in red serge and First Nations dolls in stereotypical fashions. (No prices were listed in the catalogue.)
MD: What specific customer needs or pain points does Protolabs Network aim to address, and how does it affect customer experience?
Machine Design: What are the primary expanded capabilities that the rebranded Protolabs Network offers through its global manufacturing partners?
Dolls related to books and movies were designed as well, and in the 1930s, Reliable manufactured Shirley Temple dolls, plus “Snow White, and in 1949 Canada’s own sweetheart on skates, Barbara Ann Scott and the CBC’s Maggie Muggins,” said the introduction page, “Growing up with a Reliable Toy,” in the company’s 50th Anniversary Spring/Summer catalogue for 1970. (Maggie Muggins was an endearing character created by Mary Grannan (1900-1975), a Canadian children’s book author and CBC radio/tv personality.)
Plastic became a standard material for toy manufacturers, allowing for smooth edges and no splinters to pierce wee tender fingers. The toy company “founded Reliable Plastics Company Limited no later than 1948, and probably earlier,” wrote Rénald Fortier in “Toys, glorious toys,” at Ingenium Canada.
© 2024 The Kingston Whig Standard, a division of Postmedia Network Inc. All rights reserved. Unauthorized distribution, transmission or republication strictly prohibited.
Protolabs Network includes more than 250 supply partners to serve customers’ needs across the life cycle of their products—from innovation and prototyping to production and end-of-life product support. Customers can access tighter tolerances, enhanced finishing options and higher volumes at lower cost, among other benefits. The manufacturing partner network complements the low-volume, on-demand manufacturing services also available from Protolabs.
Manufacturing toys for energetic kids of all ages by the 1970s, Reliable built a lively foundation of entertainment for indoors and outside. Bow-and-arrow sets, skipping ropes, spin flyers, and a mountain of plastic trucks, buckets and shovels, plus riding horses, wagons, scooters… the list was nearly endless. The selection even included Easy-Lock Bricks, looking a lot like Lego®.
LM: Protolabs does not rely on “commercial packaged software,” but instead we have developed our own proprietary software to automate every aspect of the digital manufacturing thread. Our network offering will be fully integrated into our homegrown software, which continues to be streamlined to remove friction in the process and allow for direct connection with customers to make sure all critical issues are resolved quickly and effectively.
The toy manufacturing giant moved to Carlaw Street in Toronto with 72,000 square feet of space. Producing composite dolls with heads and limbs created from a recipe of cornstarch, sawdust, and glue or resin, the parts were attached to a cuddly soft body. Reliable then added full-service touches. “This factory contained a complete knitting mill to manufacture clothing for dolls and featured a hairdressing department,” described CMC. The factory had “specialty sections for making voice boxes and squeakers, shoes, and eyes.”
MD: What specific software tools, digital platforms or systems are used to facilitate the collaboration between Protolabs’ internal digital factories and the global network of suppliers within the Protolabs Network? Can you speak specifically on the topic of CAD/CAM/CAE?
As Machine Design’s technical editor, Sharon Spielman produces content for the brand’s focus audience—design and multidisciplinary engineers. Her beat includes 3D printing/CAD; mechanical and motion systems, with an emphasis on pneumatics and linear motion; automation; robotics; and CNC machining.
Postmedia is committed to maintaining a lively but civil forum for discussion. Please keep comments relevant and respectful. Comments may take up to an hour to appear on the site. You will receive an email if there is a reply to your comment, an update to a thread you follow or if a user you follow comments. Visit our Community Guidelines for more information.
Spielman has more than three decades of experience as a writer and editor for a range of B2B brands, including those that cover machine design; electrical design and manufacturing; interconnection technology; food and beverage manufacturing; process heating and cooling; finishing; and package converting.
Adapting amazing new technologies, management invested in injection-molding equipment for plastic toy components. Developed in the late 1800s, plastic was an industry-changing invention, and injection-molding added an enhanced level of progress. “In 1931 French Ivory Products of Toronto, making cellulose acetate caps for toothpaste tubes, operated the first injection-molding machine in North America,” said Charles Law in “Plastics-Processing Industry,” The Canadian Encyclopedia, edited December 16, 2013.
GETTING A QUOTE WITH LK-MOULD IS FREE AND SIMPLE.
FIND MORE OF OUR SERVICES:
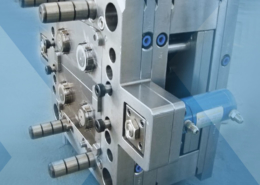
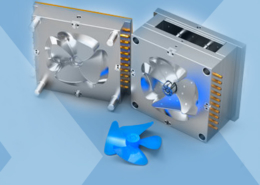
Plastic Molding

Rapid Prototyping
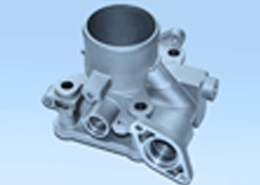
Pressure Die Casting
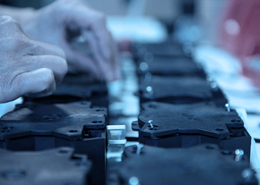
Parts Assembly
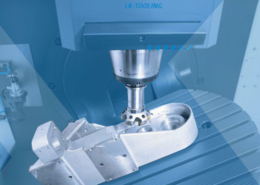