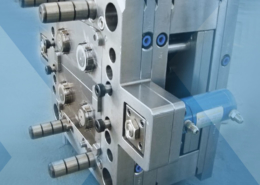
Make Polycarbonate Flow Easily Without Losing Toughness or Clarity - molded poly
Author:gly Date: 2024-09-30
Brett Saddoris, Accumold’s Technical Marketing Manager says, “We are excited to be at MEDevice Boston, and we are proud to have collaborated with numerous leading medical device manufacturers globally, working strategically with each to ensure the most efficient product development process. The key to success lies in medical device OEMs viewing their micro molder not just as a job shop but as a partner from the earliest stages of the design-to-market process to avoid costly errors. Manufacturing micro medical plastic products necessitates a genuine partnership between OEMs and micro molding specialists, distinct from traditional OEM/supplier relationships. In micro manufacturing, the most critical issues often arise during the design and prototyping stages, including material selection and packaging considerations. A true partnership ensures faster time-to-market with more efficient and cost-effective products.”
In case I access protected data on Internet portals of Vogel Communications Group including any affiliated companies according to §§ 15 et seq. AktG, I need to provide further data in order to register for the access to such content. In return for this free access to editorial content, my data may be used in accordance with this consent for the purposes stated here.
Naturally, we always handle your personal data responsibly. Any personal data we receive from you is processed in accordance with applicable data protection legislation. For detailed information please see our privacy policy.
Environmental regulations for painting plants are tightening globally, not just in Europe but also in countries like China, according to Krauss-Maffei. However, these challenges can be effectively addressed ...
I understand that I can revoke my consent at will. My revocation does not change the lawfulness of data processing that was conducted based on my consent leading up to my revocation. One option to declare my revocation is to use the contact form found at https://contact.vogel.de. In case I no longer wish to receive certain newsletters, I have subscribed to, I can also click on the unsubscribe link included at the end of a newsletter. Further information regarding my right of revocation and the implementation of it as well as the consequences of my revocation can be found in the data protection declaration, section editorial newsletter.
By clicking on „Subscribe to Newsletter“ I agree to the processing and use of my data according to the consent form (please expand for details) and accept the Terms of Use. For more information, please see our Privacy Policy.
Cookie-Manager Imprint Media Privacy General Terms & Conditions Help AI-Guidelines
In terms of painting, increasingly strict environmental regulations have to be observed almost worldwide. Subsequent processes also consume more and more resources for logistics and further handling. However, with the Colorform process from Krauss-Maffei, the color is applied directly in the injection molding tool, as the Bavarians emphasize. This works by coating components made of thermoplastic material with a polyurethane or polyurea layer (PUR/PUA), as it is further explained. For this, the new, as it is emphasized, industry's largest laboratory facility is now available at the Krauss-Maffei site in Parsdorf. It can be used, for example, for the production of outer skin components for vehicles.
This portal is a brand of Vogel Communications Group. You will find our complete range of products and services on www.vogel.com
The automation was also designed to be practical, as some thermoplastic materials (such as PP, PA, PE) must first be surface-activated in order to achieve good adhesion between the polymer and PUR. For this purpose, a flaming station is integrated into the laboratory system. The system will be supplemented by a trimming cell, which can be used to remove the sprues from the components, as it is further explained. This technology also comes from Krauss-Maffei. And two unique products on the market from the digital portfolio round off the overall offer, as is emphasized. On the one hand, the machine function "APCplus" on the MXW 4500, which serves as an autopilot for the injection molding process and ensures extremely weight-consistent components by adapting the switch point and after pressure from shot to shot to the melt viscosity, as Krauss-Maffei explains. On the other hand, the Dataxplorer monitors the entire plastic processing process and records over 1,000 machine signals at a resolution of up to 200 Hertz in curve form. In this way, the user gets a microscopically detailed view of all the processes in the Colorform process and enjoys full traceability of the events. By the way, Krauss-Maffei develops and manufactures all the components required for the Colorform process described here. Therefore, interface and function problems are not to be expected.
At the MEDevice show in Boston on September 25-26, Accumold will showcase a variety of innovative medical parts and components at booth 815. These products reflect the company’s extensive experience and deep understanding of design for micro manufacturing (DfMM). Accumold stands out due to its vertical integration, enabling it to serve as a comprehensive partner in developing and manufacturing medical devices. Their offerings include design and material support, micro tool fabrication, proprietary micro molding services, advanced metrology, assembly, and automation. This integration streamlines the medical product development process, optimizing timeliness, innovation, cost, and accuracy.
Saddoris continues, “Medical device OEMs are under pressure to maintain profitability despite decreasing prices, which necessitates the development of innovative products that meet increasingly stringent end-user demands. There will be a growing need for versatile devices that leverage the potential of 'smart' diagnostics and treatment through the proliferation of 'big data,' as well as cost-effective alternatives to traditionally expensive diagnostic and therapeutic devices. Micro molding is the preferred solution for many medical device OEMs to meet these rigorous manufacturing requirements.”
Newsletter content may include all products and services of any companies mentioned above, including for example specialist journals and books, events and fairs as well as event-related products and services, print and digital media offers and services such as additional (editorial) newsletters, raffles, lead campaigns, market research both online and offline, specialist webportals and e-learning offers. In case my personal telephone number has also been collected, it may be used for offers of aforementioned products, for services of the companies mentioned above, and market research purposes.
But simply making the machine bigger is not that easy when it comes to complex technical processes. This also required careful planning for the new Colorform laboratory facility. It should depict the entire production process for users ("all in one")—injection molding, PUR flooding, parts handling, post-processing, and surface treatment. It should also be flexibly applicable for medium and (very) large components, as Krauss-Maffei notes. The possible production of sample plates was also taken into account. The result is the MXW 4500 with a turntable and widened clamping plates—plus several so-called wet parts that provide the polyurethane. A dose system Rimstar Flex 8/8 with the mixing heads MK5/MK8 takes over flow rates up to 50 or 250 grams per second. The also available Rimstar Compact 16/29 with the newly developed mixing head MK10-3K achieves output quantities up to 500 grams per second, as Krauss-Maffei says. Depending on the component weight, the color is dosed via a modular color building block (with the 2K mixing heads) or added directly, as for example with the mixing head MK10-3K. This enables the complex media guidance in the new overall system.
I hereby consent to Vogel Communications Group GmbH & Co. KG, Max-Planck-Str. 7/9, 97082 Würzburg, Germany, including any affiliated companies according to §§ 15 et seq. AktG (hereafter: Vogel Communications Group) using my e-mail address to send editorial newsletters. A list of all affiliated companies can be found here
The medical device industry demands increasingly smaller products with precise, micron-level tolerances, necessitating partnerships with micro molding experts like Accumold. These experts provide the precision, repeatability, and zero failure rates crucial for safety-critical applications.
Micro molding for medical device OEMs requires years of expertise and the right business culture, personnel, and equipment to ensure project success. Micro molders handle low, medium, and high volume runs with various materials, requiring different validation levels. They must also expertly manage the handling, storage, and processing of costly, sensitive materials used in critical implantable applications.
Accumold’s micro molding process enables the production of tiny, complex, and feature-rich components efficiently, cost-effectively, and in large volumes. The expert use of micro molding technologies provides medical device OEMs with a competitive edge, driving both product innovation and profitability. High-quality parts with precise dimensional accuracy are crucial for sensitive medical applications, including specialized devices for cancer treatment and diagnosis, small molded catheter tips, micro-needles, small surgical instruments, dental implants, infection control devices, and staples, among others.
Accumold invites all medical OEMs at MEDevice Boston to visit and discuss how micro molding with Accumold can drive the manufacture of innovative, timely, and cost-effective medical devices.
GETTING A QUOTE WITH LK-MOULD IS FREE AND SIMPLE.
FIND MORE OF OUR SERVICES:
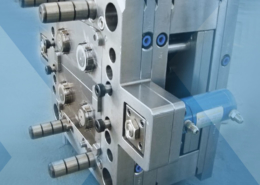
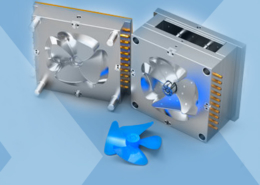
Plastic Molding

Rapid Prototyping
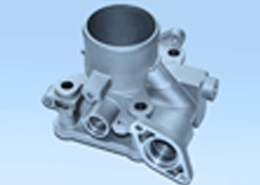
Pressure Die Casting
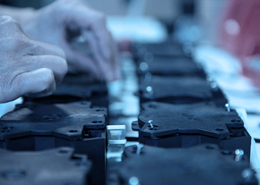
Parts Assembly
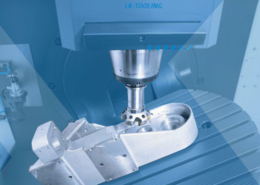