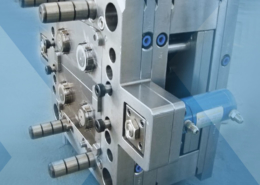
Lund University students cast household items in glass instead of plastic - cast
Author:gly Date: 2024-09-30
AkvisIO IME from Kistler aims to bridge this gap and enables customers to manage and analyse data across devices and processes. The data analysis software for recording, storing and analysing high-frequency sensor and machine signals during injection moulding is intended for use by both process engineers and data scientists. It replaces the previous ComoDataCenter (CDC) data management solution from Kistler and provides a comprehensive analysis function including automatic data synchronisation with all connected systems.
The AkvisIO IME data analysis software is available for the process monitoring system ComoScout since September. This entry-level solution from Kistler analyses all available machine signals and is ideal as a retrofit for the digital connection of injection moulding machines that are not yet equipped with mould sensors or which have sensors that are used for the analysis of temperature signals at voltage inputs. Starting in January 2024, the data analysis software will also be available for use with the process monitoring system ComoNeo, which monitors the injection moulding process with the help of cavity pressure and temperature sensors.
A QPC mold is designed with two major components: frame and modules. The frame is designed to remain in the machine with all water, air, and electrical hookups remaining in place. The modules consist of core/cavity assemblies and p0late systems. Every QPC mold can be converted from single fact to a stack mold configuration. The QPC approach has built-in features for the alignment of modules to the frame, as well as plate-to-plate connections for services. This dramatically reduces change-over time, Morra explained.
StackTeck announced an unconventional application for a big stack mold with Quick Product Change (QPC) features. This mold runs 2000 tons of production in a 1000-ton injection molding machine, in a 2x4 format enabling molding of eight large, flat panels per cycle of the machine.
StackTeck's client selected the QPC approach with manufacturing flexibility in mind. According to Angelo Morra, business development manager at StackTeck, "This customer was looking for a way to mold multiple part types using the same machine and they have achieved a change-over time of less than one hour using StackTeck's proved Quick Product Change technology. They are using high performance Husky 1000-ton injection molding machines, and with stack mold technology they have reduced the number of machines needed for the program by half."
In addition to suitable machines and tools, transparent injection moulding processes often require more in-depth optimisation with sensors and continuous production monitoring. Moreover, when it comes to designing processes that are optimal over the long term, data management and data analysis play a decisive role: they are the missing, often underutilised, link in the value chain of modern plastics processing.
Until she retired in September 2021, Clare Goldsberry reported on the plastics industry for more than 30 years. In addition to the 10,000+ articles she has written, by her own estimation, she is the author of several books, including The Business of Injection Molding: How to succeed as a custom molder and Purchasing Injection Molds: A buyers guide. Goldsberry is a member of the Plastics Pioneers Association. She reflected on her long career in "Time to Say Good-Bye."
Some of the advantages of the QPC technology include the ability to fulfill last-minute demand changes from customers; only one hot runner and frame needed per machine; reducing produce change-over times and maximizing production times. Additionally, growth of capital investment can be "cascaded" with "module-only" purchases as the market demand increases; and identical modules can be moved between multiple frames including a single face frame and stack mold frames up to four levels. Standard QPC modules heights and part pitches facilitate the use of robotic standards.
With the AkvisIO IME (Injection Moulding Edition) data analysis software, Kistler is aiming to help its customers take a further step towards the digitalisation of injection moulding.
AkvisIO IME simplifies the setting up and configuration of the connected injection moulding machines and process monitoring systems from Kistler such as ComoNeo and ComoScout. Thanks to seamless synchronisation, digital assets like tool configuration, reference curves and monitoring objects can be easily transferred and consistently managed – both on the master computer (AkvisIO) and directly on the machine. All data is saved on a cyclical basis and can be compared and analysed across cycles, giving customers a single source of truth for all their plastics processing product data. Furthermore, the cross-machine and cross-device monitoring of all injection moulding processes simplifies the creation of customised reports for quality assurance.
StackTeck, located just outside Toronto, Canada, manufactures a wide range of injection molds for plastic parts such as closures, personal care, medical, thin-wall packaging as well as mold bases. StackTeck has dedicated R&D testing and part sampling facilities, in addition to plastic part design and prototyping capabilities.
As a modular, scalable software solution, AkvisIO already comes equipped with a number of analysis features that are being continually expanded. These are the well-known monitoring functions of ComoScout and ComoNeo (known as evaluation objects or EOs) as well as working with reference curves. Other features include cross-cycle trend analysis and statistic statistical process control (SPC) with output of characteristic values for process capability and stability such as cp, cpk, mean value and standard deviation. All of the analysis data obtained can be visualised and integrated into various reports.
StackTeck announced an unconventional application for a big stack mold with Quick Product Change (QPC) features. This mold runs 2000 tons of production in a 1000-ton injection molding machine, in a 2x4 format enabling molding of eight large, flat panels per cycle of the machine.
All of the data from machines and process monitoring systems like ComoNeo and ComoScout can now be visualised and analysed synchronously and across processes.
In the trend visualisation, recorded characteristic values of the machine and sensors can be compared across cycles with regard to their intervention limits, similar to statistical process control (SPC).
Customers can individually determine the scope of AkvisIO IME based on their requirements. Additional modules such as trend monitoring with artificial intelligence will be released over time. Users of the previous database solution CDC can simply upgrade to AkvisIO, which will be the standard software for ComoNeo and ComoScout as of 2024. Thanks to integrated user management and rights management via lightweight directory access protocol (LDAP), AkvisIO also leaves nothing to be desired in terms of auditing, data security and traceability.
GETTING A QUOTE WITH LK-MOULD IS FREE AND SIMPLE.
FIND MORE OF OUR SERVICES:
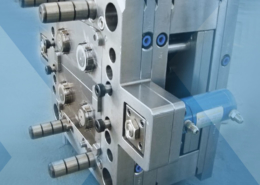
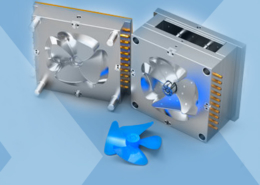
Plastic Molding

Rapid Prototyping
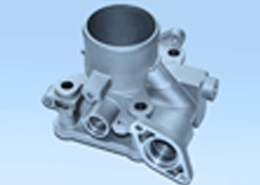
Pressure Die Casting
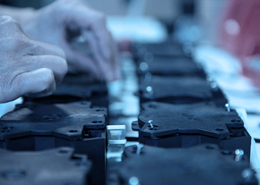
Parts Assembly
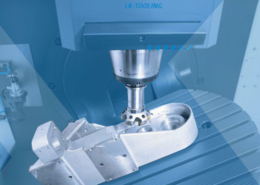