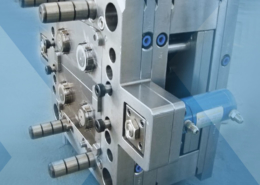
Low-pressure injection molding machine rebuild business takes off at
Author:gly Date: 2024-09-30
Weight reduction and lean manufacturing are key focuses in the aerospace sector as designers seek to the reduce operating costs of their aircraft. Consequently, thermoplastic composites that can perform with at least the same assurance as traditional metals and thermosets are in demand.
Previously, Coca-Cola Europacific Partners and Innovative Tap Solutions worked together to develop a pay-per-use beverage dispensing solution for consumers.
Weight reduction and lean manufacturing are key focuses in the aerospace sector as designers seek to the reduce operating costs of their aircraft. Consequently, thermoplastic composites that can perform with at least the same assurance as traditional metals and thermosets are in demand.
PEEK/carbon fiber thermoplastic composite offers 70% weight saving versus stainless steel, with better manufacturability to boot.
In response to these requirements, Tri-Mack Plastics Manufacturing Corporation, a molder of high-temperature engineering thermoplastics located in Bristol, RI, has developed Victrex PEEK (polyetheretherketone) composite manufacturing capabilities and produced brackets for use in aircraft structural applications. The brackets weigh approximately 45g each, and are employed in primary and secondary structural applications in commercial and military aircraft. Tri-Mack specified the material due to its technical features and proven track record of 25 years of use in injection molded aerospace components.
All production cells delivered as part of the pay-per-use model are said to be regularly maintained by ENGEL service technicians and feature e-connect.24, an online support and remote maintenance tool. While the in-person support is expected to facilitate early planning for maintenance work and minimise machine downtime, e-connect.24’s machine utilisation serves as the basis for billing.
Component integrity is also critical to keeping aircraft in service in order to minimize maintenance and downtime. Thermoplastic composites made from Victrex PEEK can provide the chemical and corrosion resistance to jet fuel, hydraulic fluid, de-icing solution, salt, steam, water and other commonly used service fluids that would typically undermine the longevity of metals. "Victrex PEEK composites can offer between four- and five-times higher fatigue strength, specific stiffness, and specific strength when compared to traditional metals such as aluminum," says Weidig. "These mechanical properties along with vibration and noise dampening improvements make Victrex PEEK composites an attractive and viable solution for engineers looking to replace heavy metals and thermosets."
The composite has a density of 1.6 g/cm3 versus 8 g/cm3 for stainless steel. Based on current fuel prices, the removal of one kilogram (2.2 lb) of weight from a short-range aircraft can save airlines up to $100 in annual fuel costs. "Assuming that the composite brackets can remove 100 kg (220.5 lb) of weight, an airline with 500 short-range aircraft could save up to $5 million per year in fuel costs by making the switch from metal," explains Ralf Weidig, Composites Business Leader for Victrex (West Conshohocken, PA).
Besides up to 70% weight savings compared to metals such as stainless steel, aluminum, and titanium, the innovative composite manufacturing process used by Tri-Mack provides several benefits leading to faster part manufacturing cycle times compared to thermosets. "Thermoset composite parts typically take several hours to complete," said Tom Kneath, director of sales and marketing at Tri-Mack. "The Victrex PEEK composite brackets have manufacturing cycle times measured in minutes. That speed, paired with the ability to recycle the material for other applications, takes us to a whole new level of processing efficiency that isn't achievable with thermosets."
ENGEL has expanded its injection moulding machinery range with a pay-per-use model in the hopes of reducing investment risk while boosting flexibility in production.
Thought to avoid the risk of binding capital and freeing customers from the need to seek investment approval, the new model is said to speed up the procurement process. The payment is made once a unit price has been agreed, either per unit produced or unit of machine operating time.
Once the agreed contractual term comes to an end, customers have the option of buying the machine. If they choose to return it, the machine can be sent back to the pre-owned machine company ENGEL Used Machinery in a bid to make use of its full service life and facilitate a more sustainable purchase process.
Another recent project saw ENGEL collaborate with ALPLA Group, Brink, and IPB Printing to produce thin-walled containers made of PET and rPET in a single injection moulding process step using ENGEL’s e-speed machine with a newly-developed injection unit.
GETTING A QUOTE WITH LK-MOULD IS FREE AND SIMPLE.
FIND MORE OF OUR SERVICES:
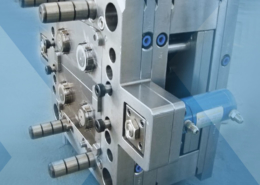
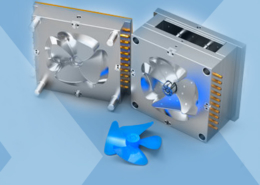
Plastic Molding

Rapid Prototyping
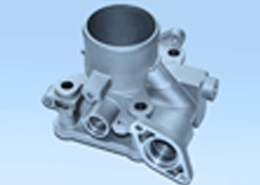
Pressure Die Casting
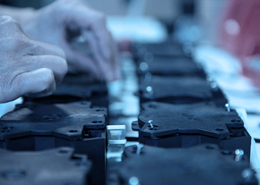
Parts Assembly
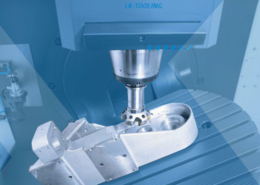