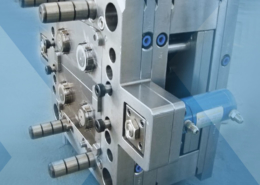
Limex: An Injection-Moldable Material Derived from Limestone - molding polystyre
Author:gly Date: 2024-09-30
The global semiconductor market has entered an exciting period. Demand for chip technology is both driving the industry as well as hindering it, with current chip shortages predicted to last for some time. Current trends will likely shape the future of the industry, which is set to continue to show
While the major correction in PP prices was finally underway, generally stable pricing was anticipated for the other four commodity resins.
In this three-part collection, veteran molder and moldmaker Jim Fattori brings to bear his 40+ years of on-the-job experience and provides molders his “from the trenches” perspective on on the why, where and how of venting injection molds. Take the trial-and-error out of the molding venting process.
In recent years, the IoT is rapidly being introduced into almost all sectors, but it has particular importance in the EV industry.
Across the show, sustainability ruled in new materials technology, from polyolefins and engineering resins to biobased materials.
New micromolding system from hot-runner supplier MHSMold Hotrunner Systems has a novel, 4-ton magnetic clamping system and onboard robotic parts handling and vision QC.
While the melting process does not provide perfect mixing, this study shows that mixing is indeed initiated during melting.
Measure material stiffness and resiliency with precision up to 10,000 units with Taber's Stiffness Tester. Learn more here.
Plastics Technology covers technical and business Information for Plastics Processors in Injection Molding, Extrusion, Blow Molding, Plastic Additives, Compounding, Plastic Materials, and Resin Pricing. About Us
Despite price increase nominations going into second quarter, it appeared there was potential for generally flat pricing with the exception of a major downward correction for PP.
Your questions, but not your email details will be shared with OpenAI and retained for 30 days in accordance with their privacy principles.
Join Wittmann for an engaging webinar on the transformative impact of manufacturing execution systems (MES) in the plastic injection molding industry. Discover how MES enhances production efficiency, quality control and real-time monitoring while also reducing downtime. It will explore the integration of MES with existing systems, emphasizing compliance and traceability for automotive and medical sectors. Learn about the latest advancements in IoT and AI technologies and how they drive innovation and continuous improvement in MES. Agenda: Overview of MES benefits What is MES? Definition, role and brief history Historical perspective and evolution Longevity and analytics Connectivity: importance, standards and integration Advantages of MES: efficiency, real-time data, traceability and cost savings Emerging technologies: IoT and AI in MES
You can find a wealth of information and regional contacts at our website or you can follow us on LinkedIn to learn about new products and applications. We will also be exhibiting at the K Show in Dusseldorf, Germany from Oct. 16-23, so please come visit us at Hall 5, Booth A23!
Plastics Technology’s Tech Days is back! Every Tuesday in October, a series of five online presentations will be given by industry supplier around the following topics: Injection Molding — New Technologies, Efficiencies Film Extrusion — New Technologies, Efficiencies Upstream/Downstream Operations Injection Molding — Sustainability Extrusion — Compounding Coming out of NPE2024, PT identified a variety of topics, technologies and trends that are driving and shaping the evolution of plastic products manufacturing — from recycling/recyclability and energy optimization to AI-based process control and automation implementation. PT Tech Days is designed to provide a robust, curated, accessible platform through which plastics professionals can explore these trends, have direct access to subject-matter experts and develop strategies for applying solutions in their operations.
Next month’s mammoth triennial plastics show in Düsseldorf, Germany, challenges injection molding machine builders to demonstrate technological leadership in addressing the needs of the marketplace. This year, that means shaving down energy costs to the bare minimum, while also achieving ever greater feats of speed and productivity. It also means combining multiple functions into one compact and automated process through integrating multiple materials, in-mold decorating and assembly, foaming or gas assist, insert molding, and quality inspection. The latter requires complex and sophisticated tooling and hot runners, as well as robotics, both of which will be front and center at K. Here, then, is a quick rundown of the new developments of interest to North American processors—at least those that exhibitors would reveal in advance. FAST, EFFICIENT MACHINES New injection presses at K will be mostly all-electric or partially electric hybrids, but almost all machines using hydraulics will trim energy consumption through use of variable-speed electric motors to drive the pumps.
In this collection, which is part one of a series representing some of John’s finest work, we present you with five articles that we think you will refer to time and again as you look to solve problems, cut cycle times and improve the quality of the parts you mold.
Victrex plc.. "Replacing Metals with PEEK (Polyetheretherketone)". AZoM. 29 September 2024.
In this collection of content, we provide expert advice on welding from some of the leading authorities in the field, with tips on such matters as controls, as well as insights on how to solve common problems in welding.
Introduced by Zeiger and Spark Industries at the PTXPO, the nozzle is designed for maximum heat transfer and uniformity with a continuous taper for self cleaning.
Additive technology creates air pockets in film during orientation, cutting down on the amount of resin needed while boosting opacity, mechanical properties and recyclability.
In this interview, AZoM talks to Philippe Wilson about benchtop NMR and its role in different fields, focusing on its main use in biofluid analysis.
Currier Plastics has added substantial capacity recently in both injection and blow molding for medical/pharmaceutical products, including several machines to occupy a new, large clean room.
Join Engel in exploring the future of battery molding technology. Discover advancements in thermoplastic composites for battery housings, innovative automation solutions and the latest in large-tonnage equipment designed for e-mobility — all with a focus on cost-efficient solutions. Agenda: Learn about cutting-edge thermoplastic composites for durable, sustainable and cost-efficient battery housings Explore advanced automation concepts for efficient and scalable production See the latest large-tonnage equipment and technology innovations for e-mobility solutions
Processors with sustainability goals or mandates have a number of ways to reach their goals. Biopolymers are among them.
The beauty of the injection molding process, once mastered, is that it can be optimized for faster processing cycles and easy part-to-part repeatability which means lower overall costs compared to metals.
Multi-component molding with in-mold assembly will be performed at two exhibits running Foboha rotating cube molds. Above: Arburg 720A all-electric machine with second horizontal injector on the moving platen produces two-piece, HDPE/PP closures that are cooled and demolded on two sides transverse to the mold axis while the mold is closed, saving cycle time. Below: Foboha cube mold at Ferromatik Milacron’s booth molds two parts of a closure and then screws them together.
Learn about sustainable scrap reprocessing—this resource offers a deep dive into everything from granulator types and options, to service tips, videos and technical articles.
Mike Sepe has authored more than 25 ANTEC papers and more than 250 articles illustrating the importance of this interdisciplanary approach. In this collection, we present some of his best work during the years he has been contributing for Plastics Technology Magazine.
Victrex plc.. (2019, May 30). Replacing Metals with PEEK (Polyetheretherketone). AZoM. Retrieved on September 29, 2024 from https://www.azom.com/article.aspx?ArticleID=10147.
Kai Düffels from Microtrac discusses the CAMSIZER 1, a particle size analyzer designed for simplicity. Read the interview here.
John Walling is the Americas Strategic Marketing Manager for Victrex Polymer Solutions. He holds a Bachelor of Mechanical Engineering Degree from the University of Michigan and a Masters in Business Administration from the Anderson School at UCLA.
The primary distinction between graphene-based batteries and solid-state batteries lies in the composition of either electrode. Although the cathode is commonly changed, carbon allotropes can also be employed in fabricating anodes.
The inherent low specific gravity of VICTREX PEEK (1.3 g/cm3) is less than half that of aluminium and one sixth that of steel. Carbon or glass fibers are added as structural reinforcements in PEEK compounds that have high strength and modulus properties similar to aluminium, but still much lower in density. This results in a superior strength-to-weight ratio so VICTREX PEEK-based compounds can offer equivalent strength and stiffness with up to 70% weight reduction.
Ultradent's entry of its Umbrella cheek retractor took home the awards for Technical Sophistication and Achievement in Economics and Efficiency at PTXPO.
VICTREX PEEK can improve fuel economy and reduce emissions in two ways. First, by reducing energy losses due to excess weight, and second, by reducing friction losses in the powertrain. A 68% weight reduction in gears, for example, results in a 78% reduction in the moment of inertia which leads to a 9% increase in efficiency. The reason: low weight – i.e. reduced moving masses – and the lower friction losses typical of plastic, both of which help considerably when optimising response or when accelerating or decelerating masses.
Carbon Steel, Stainless Steel, Titanium, Aluminum, Magnesium, Brass and Bronze have all been replaced with VICTREX PEEK over the years.
Besides weight reduction, we see three more major benefits: enhanced performance, greater design freedom, and lower total system cost. Enhanced performance benefits include everything from extending lifetime by eliminating corrosion, increasing fuel efficiency with lower friction, and handling higher loads/speeds to operating in more extreme chemical environments.
There are approximately 15,000 clamps used to secure the wiring and cables on a given plane which results in substantial weight savings. This translates to $23,000 per year in fuel savings as well as a CO2 emission reduction of 80 tons for each plane using this technology. Not only can this application help save airlines money and reduce air travel’s effect on the environment, but the clamps are much easier to install.
Multiple speakers at Molding 2023 will address the ways simulation can impact material substitution decisions, process profitability and simplification of mold design.
In this interview, Prolific North's Managing Director Alexandra Balazs discusses the launch of the inaugural STEM Marketing Awards, sharing insights into why they’re crucial for the sector and how they aim to shape the future of STEM marketing.
Join KraussMaffei for an insightful webinar designed for industry professionals, engineers and anyone interested in the manufacturing processes of PVC pipes. This session will provide a comprehensive understanding of the technology behind the production of high-quality PVC pipes: from raw material preparation to final product testing. Agenda: Introduction to PVC extrusion: overview of the basic principles of PVC pipe extrusion — including the process of melting and shaping PVC resin into pipe forms Equipment and machinery: detailed explanation of the key equipment involved — such as extruders, dies and cooling systems — and their roles in the extrusion process Process parameters: insight into the critical process parameters like temperature, pressure and cooling rates that influence the quality and consistency of the final PVC pipes Energy efficiency: examination of ways to save material and energy use when extruding PVC pipe products
Some of the first VICTREX PEEK applications were wear components for industrial equipment such as seal rings, bushings, bearings and valves, especially in extreme environments. Hydraulic valves in automotive anti-lock brake systems started in Europe and quickly became a global industry standard.
While we only use edited and approved content for Azthena answers, it may on occasions provide incorrect responses. Please confirm any data provided with the related suppliers or authors. We do not provide medical advice, if you search for medical information you must always consult a medical professional before acting on any information provided.
Join this webinar to explore the transformative benefits of retrofitting your existing injection molding machines (IMMs). Engel will guide you through upgrading your equipment to enhance monitoring, control and adaptability — all while integrating digital technologies. You'll learn about the latest trends in IMM retrofitting (including Euromap interfaces and plasticizing retrofits) and discover how to future-proof your machines for a competitive edge. With insights from industry experts, it'll walk you through the decision-making process, ensuring you make informed choices that drive your business forward. Agenda: Maximize the value of your current IMMs through strategic retrofitting Learn how to integrate digital technologies to enhance monitoring and control Explore the benefits of Euromap interfaces and plasticizing retrofits Understand how retrofitting can help meet new product demands and improve adaptability Discover how Engel can support your retrofitting needs, from free consultations to execution
Across all process types, sustainability was a big theme at NPE2024. But there was plenty to see in automation and artificial intelligence as well.
Disclaimer: The views expressed here are those of the interviewee and do not necessarily represent the views of AZoM.com Limited (T/A) AZoNetwork, the owner and operator of this website. This disclaimer forms part of the Terms and Conditions of use of this website.
Automation is a must-have for molders of pipettes. Make sure your supplier provides assurances of throughput and output, manpower utilization, floor space consumption and payback period.
The combined MD&M East and Plastec East shows in N.Y.C. in June presented intriguing developments for medical injection molders.
Gifted with extraordinary technical know how and an authoritative yet plain English writing style, in this collection of articles Fattori offers his insights on a variety of molding-related topics that are bound to make your days on the production floor go a little bit better.
August 29-30 in Minneapolis all things injection molding and moldmaking will be happening at the Hyatt Regency — check out who’s speaking on what topics today.
Not only is PEEK a lightweight solution, it also provides a productivity solution in manufacturing with the opportunity to consolidate and simplify part designs through the injection molding process. Designing with thermoplastics like PEEK allows engineers to take a current metal component, re-visit the design, and simplify it to make it easier on the installation and manufacturing teams at the tier and OEM level.
technotrans says climate protection, energy efficiency and customization will be key discussion topics at PTXPO as it displays its protemp flow 6 ultrasonic eco and the teco cs 90t 9.1 TCUs.
In this collection of articles, two of the industry’s foremost authorities on screw design — Jim Frankand and Mark Spalding — offer their sage advice on screw design...what works, what doesn’t, and what to look for when things start going wrong.
Sustainability continues to dominate new additives technology, but upping performance is also evident. Most of the new additives have been targeted to commodity resins and particularly polyolefins.
•One of the first 150-m.t. hybrid presses from Athena Automation, Vaughan, Ont., the new venture of Robert Schad (founder and former owner of Husky), will appear as part of a PET preform molding system from SIPA of Italy (U.S. office in Atlanta). The machine’s design, with servo-electric and servo-hydraulic drives, is fine-tuned for energy savings, space savings, and high repeatability (see July Close Up). •SP stands for Speed Performance in the new Systec SP 280 (280 m.t.) hybrid toggle press for packaging from Sumitomo (SHI) Demag (U.S. office in Strongsville, Ohio). It has electric plastication and activeDrive servo-hydraulic clamp. It is a more economical alternative to the high-performance EL-Exis SP hybrid. The new press will mold two 1.2-liter PP buckets(84 g each) with in-mold labeling (IML) in 5.3 sec. •Two new presses from Wittmann Battenfeld (U.S. office in Torrington, Conn.) are two-platen types. The MacroPower 1500 (1500 m.t.) is a new size in this hydraulic line, shown with optional ServoPower servo-hydraulic pump technology. Also new is the MacroPower E 450 hybrid (450 m.t.) with servo pump (see June Close Up). It will mold a bucket with IML. INTEGRATED MULTIFUNCTION PROCESSES Accomplishing multiple operations within a single machine and mold has brought ever more complex automated cells to recent shows. Next month, Engel, for example, will mold medical drip chambers with three materials and a filter insert. The body of the drip chamber is molded of ABS and TPE in one step; the filter is inserted by a six-axis robot; and the filter is joined to the body by overmolding with PP. The robot then demolds the parts for seal inspection. For automotive, Engel will show a new method of multi-component, soft-touch molding of interior components. The Varysoft process developed by Georg Kaufmann Formenbau in Switzerland will produce Hyundai Kia dashboards. A decorative, grained TPO film is preheated and preformed in one station of the automated cell, while the rigid substrate is molded of ABS/PC using the MuCell microcellular foam process from Trexel, Wilmington, Mass. The TPO film is then transferred to the mold on a rotating table, where the film is placed in the cavity with the substrate. After the mold closes, PUR foam is injected between the film and substrate by a Hennecke metering system (U.S. office in Pittsburgh). KraussMaffei will combine thermoplastic and thermoset PUR in a SpinForm process with a swiveling center stack on a GXW 550 press integrated with the company’s RimStar Nano PUR metering machine. The latter delivers a high-gloss lacquer surface. Both Engel and Wittmann Battenfeld will combine gas assist and IML in one process. One of Engel’s new e-duo hybrid two-platen machines will mold beverage crates, while Wittmann Battenfeld will produce a hockey stick of long-glass/PP with a gas channel 1300 mm long, using a new nitrogen and pressure generator developed by the company. The cycle time is 105 sec and cooling time is 60 sec. Motors of the EcoPower all-electric machine are switched off, consuming no energy, during the long cooling phase. Another Wittmann Battenfeld cell using an EcoPower press will combine structural foam with the BFMold variothermal process and HiP High Precision Opening program to mold an auto-interior part with a high-quality finish. Both Arburg and Ferromatik Milacron (U.S. office in Batavia, Ohio) will demonstrate multi-component molding with in-mold assembly to produce caps in Foboha rotating-cube molds (see tooling section below). And Wittmann Battenfeld will produce a cosmetics atomizer from PP and TPE using in-mold assembly. In a 4+ 4+ 4 cavity mold, the two half-shells are brought into overlapping position by an indexing platen and a Wittmann robot. The parts are then joined and sealed by overmolding. Fully automated production of a 5-in. touchscreen display in a complex automated cell will be a highlight of the Sumitomo (SHI) Demag exhibit. It uses a Systec 210 hybrid press and a six-axis robot to perform both IML and IMD (in-mold decoration) in one cycle. The robot positions the conductive IML touchscreen film on the fixed half of the single-cavity mold, while the IMD carrier on the moving half positions a carrier foil with a decorative “piano-black” finish for the display frame. The frame is injected in acrylic using variotherm mold-temperature control. The molded part is transported to a sealed station where a laser degates the part and UV light cures the acrylic topcoat on the decorative foil. MICROMOLDING, LSR, COMPOSITES There’s a new player in micromolding machines. MHS-Mold Hotrunner Solutions, Georgetown, Ont., is the second case of a hot-runner supplier developing a self-contained micromolding system. (The first was Otto Männer GmbH, U.S. office in Lawrenceville, Ga.; see Aug. 2011 Close Up.) The new M3 from MHS produces 32 direct-gated, runnerless parts with shot weights under 10 mg in less than 5 sec, or over 150 million parts/yr. This all-electric system has a tiebarless magnetic clamp (4 tons) said to embody a new type of clamping principle using embedded magnets. It also uses a novel, patented injection system and non-traditional tooling consisting of four modular inserts, each with eight micro-cavities. That allows molding eight different parts per cycle. Compatible with clean rooms, the compact system comes with onboard automation for robotic takeout and part handling, plus an integrated vision system that inspects each part and cavity in less than 1 sec between shots. Another micromolding exhibit will tie together two Wittmann Battenfeld MicroPower 15-m.t. machines for two-component molding of “lab-on-a-chip” blood analyzers. Using a two-cavity mold, one machine makes the carrier parts, which are removed by an integrated SCARA robot and vision inspected. Then the parts are placed on an electric linear axis, which transports them to the second MicroPower machine for overmolding with TPE. As at every major plastics show lately, there will be several LSR molding demonstrations. For example, Arburg will show a twocomponent application in which a metal insert is overmolded with both LSR and thermoplastic. Engel will demonstrate overmolding of LSR onto thermoplastic in a flow-sensor housing. This will be the first showing of Engel’s new, patented iQ weight control software used for LSR. It analyzes the injection-pressure profile and screw position for real-time correction of injection speed and switchover point to adjust for changes in material viscosity. And Elmet Elastomere, a maker of LSR metering systems (U.S. office in Lansing, Mich.), will address LSR and micromolding with a new mold concept for precision molding of items measuring less than 2 mm and weighing under 1 mg with dimensional tolerances in the range of 10 microns. Elmet will also present new transparent tooling for “cool” molding of LSR with UV light from LED lamps. This approach allows lower-temperature thermoplastics to be overmolded with LSR. The main feature of Elmet’s exhibit will be its new-generation TOP 3000 metering system, a top-of-the-line model that was shown at NPE2012. It’s now offered in front-loading or side-loading versions to make best use of floor space. Redesigned controls are said to be easier to use and allow production data to be extracted via USB interface in a format compliant with the ISO/TS 16949 automotive quality standard. Another recurrent theme at the show is the growing interest in injection molding structural composites with very long or continuous fibers. Two of the leaders in exploring this field have been Engel and KraussMaffei, both of which will show multiple examples of composites molding at K. Engel, for example, will show applications of “hybrid” composites with continuous fibers in preimpregnated organic sheets and tapes, which are overmolded with chopped-fiber or unreinforced material. One will use a vertical press with a six-axis robot and infrared oven to mold a brake pedal. Another demonstration will use preformed carbon-fiber organic sheets overmolded with PC/ABS to make cases for tablet PCs, smartphones, or e-book readers on a new Engel e-mac 170-m.t. all-electric press. Roctool variothermal (hot/cold cycling) molds will both preform the sheet and overmold them with a high-gloss “piano-black” finish. The automated cell will also perform inline vacuum metallization of parts for EMI shielding. A third exhibit will use a new 700-m.t. v-duo vertical two-platen hydraulic press with servo-pump “ecodrive” to produce latch covers for a sports car. Dry carbon-fiber and glass fabrics will be impregnated with a new “snap-cure” PUR thermoset resin from BASF Polyurethanes in a liquid reactive molding process, called HP (high-pressure) RTM. The PUR is dispensed by a Hennecke metering system integrated with the Engel press. KraussMaffei will also demonstrate HP-RTM to produce a car roof shell with carbon-fiber fabric infused in the mold with PUR thermoset resin. It comes out of the mold with a directly paintable surface, free of fiber “read-through.” The automated cell utilizes a new RTM mold carrier with 380 m.t. clamp force and 1300 x 1300 mm mold area. It offers fast movements and access from all sides. PUR is metered by a KM RimStar Nano 4/4 machine. KM also will demonstrate its FiberForm process for overmolding continuous-fiber organic sheet with thermoplastic on a 300-m.t. CX two-platen press with servo pump. A six-axis articulated robot is mounted on the fixed platen. Arburg is now jumping into the fray, overmolding continuous-fiber thermoplastic sheets with long-fiber direct injection molding. For the first time, it will show glass rovings chopped inline to up to 50 mm length being added to the liquid melt, rather than starting with more costly long-fiber pellets. Arburg will use a six-axis robot to pick up the sheets, place them in a heating station, and transfer them to the mold. And the IKV (Institute for Plastics Processing) in Aachen, Germany, will demonstrate in-situ reaction molding and impregnation of complex fiber preforms with a monomer that cures to a thermoplastic matrix in the injection mold. MORE SPECIALTIES Sumitomo (SHI) Demag will show off rapid color changes via multiple liquid-color dosing on the machine. Its activeColor-Change system can switch among up to five liquid-color feeders integrated with the NC5 machine control. The colorant is fed directly into the melt-filled metering zone of the screw, bypassing the upstream feed and compression zones, thereby shortening considerably the portion of the screw that must be purged during color changes. The metering zone has a special mixing section. Color changes reportedly take only a few shots. Sumitomo Demag will also demonstrate the novel SL plastication system from Spiral Logic Ltd. of Hong Kong (see Aug. 2012 Close Up). This zero-compression screw (shown at NPE 2012) works with an upstream dosing screw feeder to provide what’s said to be unprecedented melt homogeneity without viscosity variations or shear-induced resin degradation. In optical molding, Engel will show an unusual multi-injection process for auto headlamp lenses. The process requires just one injector to mold the thick lens in two steps to save cooling time and avoid sinks. First, the core is molded and demolded while its center is still molten. After cooling outside the press, it is returned to the mold and overmolded with thinner layers of the same material on both sides. The total cycle is 440 sec vs. 1550 sec for a single shot. Arburg will show an unusual overmolding process whereby a TPE wheel rim is overmolded onto a tire molded of expanded thermoplastic bead foam. Here are some other specialties to look for at the show: •Cap molding: Ferromatik Milacron will have three cap-molding demonstrations, including one cell for two-component barrier closures. •Microcellular foam: KraussMaffei will use the MuCell technology on an all-electric AX machine with a new space-saving gas-metering system from Trexel, shown for the first time. •In-mold thermography: As at K 2010 and NPE 2012, Wittmann Battenfeld will show this novel system using an infrared camera to “read” the surface-temperature profile of freshly molded parts and adjust the cooling circuits to minimize differentials. •Process monitoring: Kistler (U.S. office in Amherst, N.Y.) has a new non-contact cavity-pressure sensor that won’t leave marks on Class A parts or optical lenses. This longitudinal measuring pin Type 9239A installs in the mold behind the cavity wall. Its 3 mm diameter suits it to small or complex molds. Kistler also has added new features to its CoMo injection process-monitoring system with firmware upgrade V2.4. These include automatic mold recognition through automatic loading of mold data during mold changes. And the MultiFlow automatic hot-runner balancing function now allows finer control of nozzle-tip temperatures. ROBOTS: SMARTER, STRONGER, FASTER Robot displays at K will emphasize easier programming, higher speeds, and higher payload capability. Look for numerous demonstrations of IML and medical applications, as well as utilization of six-axis articulated-arm robots—often in cooperation with linear Cartesian robots. Arburg will introduce an unusual arrangement of a six-axis robot suspended on a linear axis transverse to the machine. This is said to permit faster mold entry and shorter cycles, as well as greater working area for a small robot (10-kg payload). The robot is an Agilus model from Kuka Robotics (U.S. office in Shelby Township, Mich.), which has integrated Arburg’s Selogica user interface. Beck Automation of Switzerland claims to set a new standard for IML speed with a system for applying labels to two half-liter, oval food containers in less than 3 sec, using a side-entry robot. The touchscreen-controlled system is supplemented by a vision inspection system. Engel will show its newest and largest linear robot, the viper 120. Introduced last fall at the Fakuma show in Germany, this unit can carry 120 kg (264 lb) and has a demolding stroke of 3000 mm and reach of 3550 mm. Also new is the C70 compact handheld teach pad with 7-in. high-definition display. It weighs only 850 g. A patented automation system for filter separation and assembly of medical pipette tips will be demonstrated by Hekuma (U.S. office in Ann Arbor, Mich.). With cycle times of 1.5 sec between bulk-fed filters entering the feeder system and filling the turntable plate, Hekuma claims to have reduced the entire assembly process to just 5 sec. The system has been tested with assembly of 16 pipettes per cycle, but it reportedly can be scaled up to 96 per cycle, or 1100/min, while comparable systems manage only about 500/min, the company says. Such performance is accomplished within a “tiny” footprint. Another space-saving automation system for pipette tips and blood-test tubes is the Vario TIP system from Waldorf Technik (U.S. office in Geneva, Ill.), which will operate in the booth of Sumitomo (SHI) Demag. The 64-cavity system at K is said to achieve “world record-breaking cycle time of just 4.5 sec” while reducing floor space by 50-75%. Eliminating compressed air as a transport medium reduces operating costs and the risk of product contamination. Instead of compressed air and free-fall, the parts are collected by a patented gripper and placed in a storage unit in cavity groups. Whereas previous methods often damaged parts by impact with the storage rack; Vario TIP avoids such collisions. Waldorf will also highlight three versions of IML automation—one that’s flexible in terms of cavity numbers and label geometries, one for stack molds, and one that offers low cost with high speed. KraussMaffei will emphasize new robot programming and control technology. The company’s new MC6 control has a handheld pendant for robot setup and operation that can also directly control the press. In addition, the new WizardX online programming assistant for linear robots is said to guide the user through just four steps to construct basic programs with the aid of a graphic interface. To simplify programming of six-axis articulated robots, ProgTechX software uses a graphic interface through which commands are selected from a library and added to the program with the click of a button. This eliminates logic and typing errors, the company says. And for operating the six-axis robot, KM’s VisuX software presents an interface with information grouped into seven pages, similar to the interface for a linear robot. As for hardware improvements, KM will show off a six-axis robot pre-installed on a platform that only has to be docked to the machine to be ready to use. KM will also demonstrate a fast-cycle automation system which pairs up highspeed versions of two linear robots (LRX 250 HS). One robot demolds parts and transfers them to the second robot via a “handshake.” The entire cycle is 7 sec. An “automation ballet” teaming two six-axis jointed-arm robots with three five-axis linear robots will enliven Sepro’s exhibit. The company (U.S. office in Pittsburgh) will exhibit 23 robots, several of which were introduced at last fall’s Fakuma show. For example, the 5X and 6X Visual robots in the “ballet” were developed last year in partnership between Sepro of France and Staübli Robotics in Germany (U.S. office in Duncan, S.C.). The 5X line is based on Sepro three-axis Cartesian servo robots plus a Staübli two-axis servo wrist. Both 5X and 6X models use the Sepro Visual 3 control (new at Fakuma), which increases data-processing speed via double-CPU architecture, in which one CPU is dedicated to the operator interface and one to real-time control of the robot. Digital vacuum switches (standard) can be set on the control pendant rather than on the robot. Shown for the first time will be the Sepro Multi-Inject 20 robot for multi-component injection presses. It’s designed not to interfere with a vertical injection unit on the press. It will operate on a 210-ton Sumitomo Demag machine with a two-position rotating mold for making ice scrapers with soft-touch grips. In this demo, the robot picks a decorative label from a feeder and places it on the molded scraper body before the soft gripper material is overmolded. Then the robot demolds the finished parts. Sepro will also show its smallest linear robot, the S5-15, which appeared at NPE 2012, as well as the Success range of affordable, general-purpose linear servo robots. The line includes four models, three of which were introduced at Fakuma, and the S3 all-servo sprue picker, also new at Fakuma. Compared with pneumatic pickers, the S3 offers higher speed, accuracy, and repeatability with less maintenance. Meanwhile, Sumitomo (SHI) Demag will demonstrate an IML system combining a Sepro side-entry robot and modular label-handling automation from Machines Pagès of France. Sumitomo will also demonstrate an SDR 11S linear robot, which is a private-labeled Sepro Success robot whose control is integrated with the Sumitomo Demag press. Star Automation (U.S. office in Menomonee Falls, Wis.) will show two new high-speed units for presses up to 200 tons. One is the SWA-150S full-servo sprue picker and the other is the SWA-3K-R5 robot for payloads up to 3 kg. The picker is mounted on a traversing beam, while the robot has a jointed arm for vertical travel. Also new from star is its Y-3 top-entry robot, which has a T-shaped traverse beam so it can “jump over” the traverse axis to deposit parts on either side of the beam and on both the operator and non-operator sides of the press. This quadruples the usual area available for release of parts. The Y-3 is for presses of 100-350 tons. At K, Star will show a new pendant said to have a unique design “very similar to a modern smartphone.” Two other new developments will include a brand-new user interface for easier programming and a new robot series with dramatically lower price for its performance range. Among three new products from Staübli Robotics is the TX340 SH shelf robot, a lightweight, six-axis articulated model suitable for mounting on a press platen. It can heft 165 kg and reach out to 3.68 meters, while maintaining repeatability of ±0.1 mm over its entire working range. Also new are the Fast Picker TP80 (shown at NPE 2012), a four-axis model capable of up to 200 picks/min, and the RS170 hsm machining robot for trimming carbon-fiber composites. Its reach of 1835 mm can handle large parts with repeatability of ±0.04 mm. Wittmann Battenfeld will show off its new W842 robot, which has larger payload (25 kg) than the W832 model. Suited to presses up to 800 tons, it has a rack-and-pinion drive for the vertical axis and a horizontal axis up to 20 meters. Sytrama (U.S. office in Windsor, Conn.) will showcase its new Cartesian-S robots together with sister company Negri Bossi (see above). HOT RUNNERS & TOOLING Sophisticated valve-gate control and new approaches to turning-stack molds for in-mold assembly top the advance billing for show news in tooling. There will also be some new mold components. Electrically actuated hot-runner valve gates have been in the headlines of late. One new entry of this type is the FLEXflow system from HRSflow of Italy. Aimed especially at large Class A automotive parts, it offers completely independent management of each valve pin’s position, acceleration, velocity, and stroke. Placing the electrical cylinder alongside the flow nozzle reduces the height of the manifold. Pin position can be set with accuracy of 0.01 mm, and system operation can be monitored remotely via WiFi. Despite the buzz about electric valve-gate actuation, don’t count pneumatics out yet. MHS-Mold Hotrunner Solutions is introducing the Rheo-Pro VA4010 Black Box pneumatic valve-gate actuator. It reportedly performs under even the most extreme operating conditions by doing away with elastomer seals, lubricants, and cooling. That suits the Black Box to molding high-temperature resins like PEEK, LCP, PSU, PEI, and PPS. MHS also calls it “the first economical alternative to electric valve gates for clean rooms.” Suitable for sequential valve gating, the Black Box offers “instantaneous switching accuracy in the millisecond range.” Height of the valve stem is adjusted with the easily accessible, 1-mm thread in the piston for quicker fine-tuning than with standard valve gates, MHS says. Two innovators in cube-mold technology for multi-component molding and in-mold assembly will demonstrate new systems at K. Foboha of Germany (U.S. office in Beverly, Mass.) will show what it calls the first cube system with all-electric drive on all axes, from the ejector to the turning unit to parts removal. One example will be running at the Ferromatik Milacron booth, a 4 x 8 + 8 mold for making a two-piece cap for drinks or food supplements. Eight top and eight bottom parts are injected for each parting surface. In the 90° position, transverse to the machine and mold axis, a handling system built into the mold removes the upper cap parts and screws them onto the bottom parts remaining in the cavities. A second Foboha all-electric stack mold will run at the Arburg booth, making a two-component cap for juice carton packs. This 12 + 12 pilot mold for a high-volume project uses two incompatible materials—PP and HDPE—that are freely movable relative to each other in the final product. Parts are ejected to the side while the mold is closed. Zahoransky Formenbau of Germany is presenting its new TIM Light system, described as “the little brother” of its TIM (Total Integrated Manufacturing) cube concept. As reported in March (see Close Up), this is a lower-cost version with flexibility to accommodate different parts. It mounts two standard single-component molds on a turning stack with a common hot-runner adapter plate and ejector plate. It can mold two parts and assemble them outside the mold—either above or below, instead of on the sides. The system is less complex than a standard cube system and requires no tiebar extension, allowing use of standard presses. In mold components, Hasco (U.S. office in Fletcher, N.C.) promises to have several new items. Among them will be Z 57 and Z 571 support pillars for larger mold bases, a new thermal insulating sheet, components with DLC “diamondlike coating,” new cooling hoses and couplings, and refined mounting tolerances for location elements. AST Technology, represented here by sister company Progressive Components, Wauconda, Ill., will show an upgraded version of its CVe mold monitor with new features such as tamper evidence and maintenance countdowns. It also incorporates the new CVe Live system allowing users to view mold activity in real time. A web interface provides access to data such as cycle times, cycle counts, and tool maintenance. It can generate graphs and reports on individual or groups of tools, and can provide alerts when maintenance is overdue.
Sumitomo (SHI) Demag will show a new system that mounts multiple liquid-color feeders on the machine and injects colorant at the end of the screw, minimizing the amount of purging necessary for color changes.
Thousands of people visit our Supplier Guide every day to source equipment and materials. Get in front of them with a free company profile.
The need for high wear performance combined with heat and chemicals translated into high purity environments such as food, beverage and semiconductor industries where electrostatic dissipative (ESD) PEEK compounds were developed for wafer handling in IC chip fabrication. Over the past two decades the number of applications for VICTREX PEEK has exploded to include aircraft brackets, clamps and insulation, oil drilling tool seals and connectors, transmission gears, and now even more into consumer applications like vacuum impellers, refrigerator compressors, and mobile device speakers.
Successfully starting or restarting an injection molding machine is less about ticking boxes on a rote checklist and more about individually assessing each processing scenario and its unique variables.
John has more than 20 years of experience with high performance polymer and composite material suppliers serving in various technical and market development roles with GE Plastics and Owens Corning Composites Systems prior to joining Victrex in 2003.
Exhibitors and presenters at the plastics show emphasized 3D printing as a complement and aid to more traditional production processes.
Resin drying is a crucial, but often-misunderstood area. This collection includes details on why and what you need to dry, how to specify a dryer, and best practices.
Say “manufacturing automation” and thoughts immediately go to the shop floor and specialized production equipment, robotics and material handling systems. But there is another realm of possible automation — the front office.
More sprue pickers are going servo, boosting speed and versatility. Above: Star Automation Swing-Axel 150S. Below: Sepro S3.
PEEK also has low moisture absorption, stable dielectric (insulating) properties and inherently low flammability. The amazing thing about PEEK is the wide range of processing options from injection molding, compression molding, and extrusion into shapes, film or fibers, to thermoforming, spray coating, or stock shape machining – it is truly one of the most versatile structural materials available.
Absolutely. Victrex is committed to developing advanced materials that leverage our knowledge and expertise with polyketones. We are led by market needs and look to innovate with our customers who are leaders in their respective industries. With a focus on solving challenging engineering problems, we have identified several unmet needs that can be addressed by new polymers that we are actively working on.
This Knowledge Center provides an overview of the considerations needed to understand the purchase, operation, and maintenance of a process cooling system.
Next month’s mammoth triennial plastics show in Düsseldorf, Germany, challenges injection molding machine builders to demonstrate technological leadership in addressing the needs of the marketplace.
After successfully introducing a combined conference for moldmakers and injection molders in 2022, Plastics Technology and MoldMaking Technology are once again joining forces for a tooling/molding two-for-one.
The switch from metal to plastic injection molding allowed for a re-design that led to the integration of a new locking hinge that helped reduce installation times by 30%. The “lock-open, lock-closed” feature of the clamp provides manufacturers with the opportunity to install the clamps with one hand leaving the other free for other tasks. This really demonstrates how VICTREX PEEK is solving multiple problems to gain acceptance versus metal in one of the world’s most conservative industries.
This month’s resin pricing report includes PT’s quarterly check-in on select engineering resins, including nylon 6 and 66.
In late April, Wittmann Battenfeld GmbH hosted around 1100 visitors at its headquarters plant in Kottingbrunn, Austria, for a comprehensive demonstration of its latest injection molding technologies.
One recent case study highlights the benefits of metal replacement in aircraft system attachment clamps. One of the world’s leading suppliers of interconnect products has worked to replace aluminum and stainless steel in their line of wire and tubing clamps. One electrical wire bundle clamp made with VICTREX PEEK is 20% lighter than the aluminum clamp it replaced.
Study shows the plastic compounding process is being used to boost electrical properties and UV resistance while custom compounding is increasingly being used to achieve high-performance in plastic-based goods.
Greater design freedom comes from PEEK’s amazing processing versatility which allows complex geometries to be molded-in without labor intensive post-machining steps. This, in turn, helps engineers improve on performance while reducing total system cost.
Second quarter started with price hikes in PE and the four volume engineering resins, but relatively stable pricing was largely expected by the quarter’s end.
•Arburg (U.S. office in Newington, Conn.) is introducing the Allrounder 820 A (400 metric tons), which completes its all-electric Alldrive series. It fills the gap between 320 and 500 m.t. The same clamp and injector size will be available later for an additional model of the Hidrive hybrid machine. •Boy Machines (U.S. office in Exton, Pa.) will bring out the Boy 25 E servo-hydraulic press (25 m.t.) as a successor to the Boy 22 E. Also new will be a vertical-clamp, horizontal-injection version, Boy 25 E VH. •Several new machines from Engel (U.S. office in York, Pa.) were previewed last month (see Close Up). These include the e-speed 650 (650 m.t.) hybrid with novel flywheel energy-recovery and storage system under the electric clamp. The press boasts injection speeds up to 1000 mm/sec and less than 2.5 sec clamp dry cycle. Also new is the e-motion 30 TL electric tiebarless press (30 m.t.) with injection speed to 800 mm/sec and dry cycle well under 1 sec. Higher speed is also one feature of the next-generation duo line of hydraulic two-platen presses and is the main attraction of a new series of electric injection units capable of up to 800 mm/sec at 2000 bar pressure. All the new machines—and a few more in Engel’s composites molding demonstrations (see below)—will sport the new CC 300 control with 21.-in. touchscreen. •Haitian of China (represented here by Absolute Haitian, Worcester, Mass.) will highlight its second-generation machines, such as the all-electric Zhafir Venus II series, now available in additional sizes of 300 to 550 m.t. It’s also offered in a high-speed “p” version for packaging (150 to 380 m.t.) with injection speeds up to 350 mm/sec. But even standard models have higher speeds and acceleration (200 mm/sec for up to 430 m.t. and 160 mm/sec for larger sizes), as well as wider tiebar spacing. New this year, second-generation Haitian Jupiter II servo-hydraulic models have been updated with new servos and drive technology from the Mars series, new controls, and more compact footprint. Additional models are coming next year—550, 750, and 950 m.t., as well as wide-platen versions of 950, 1200, and 1600 m.t. •KraussMaffei (U.S. office in Florence, Ky.) will show the newest and largest model in its year-old GX series of hydraulic two-platen machines. Two new models extend the range beyond 650 m.t. to 750 and 900 m.t. The GX 900 will mold industrial packaging in 7 sec, establishing its claim to be “the fastest two-platen machine on the market.” The GX also introduced the MC6 control, now available also on AX and CX models. Together with EAS Mold & Die Change Systems, Menomonee Falls, Wis., KM will demonstrate fully automated horizontal mold change within 3 min, using a preheating table and magnetic clamping plates. •Negri Bossi (U.S. office in New Castle, Del.) will show off its new Eleos 65-m.t. all-electric two-platen press and a liquid silicone rubber (LSR) version of the Eos 120-m.t. hydraulic machine with electric inverter drive on the pump. The Eos line was introduced at NPE 2012, as was the all-electric Vesta toggle press, a 300-m.t. version of which will appear at K with a new “ultra-rapid” ballscrew designed for fast-cycle packaging. Also new is the Bi-Power VH 1000, the firm’s smallest two-platen machine (100-m.t. hybrid with electric plastication) and a version of the Canbio 210 hydraulic toggle with new Smart Flex clamp boasting improved rigidity and oil-free V-rail platen guides. •Netstal (U.S. office in Florence, Ky.) will launch three machines. One is the all-electric Elion 2200 (220 m.t.), molding 1-ml PP syringes (1.54 g) in a 48-cavity mold with a cycle time around 9.6 sec. Second, the new Elion 4200 hybrid (420 m.t.) with EcoPower variable-speed, synchronous pump motor will mold HDPE 29/25 water caps in 96 cavities in just 2 sec. It has the high-performance injection unit of the Evos hydraulic series, capable of speeds to 2000 mm/sec. Netstal will also unveil the hybrid Evos 4500 (450 m.t.) with the EcoPower drive of the Elion series. It will mold PS drink cups in 12 cavities in 2.5 sec. Another cell will feature an all-electric Elion 1200 (120 m.t.) molding HDPE irrigation drippers in 64 cavities in 2.5 sec.
When, how, what and why to automate — leading robotics suppliers and forward-thinking moldmakers will share their insights on automating manufacturing at collocated event.
Victrex plc.. 2019. Replacing Metals with PEEK (Polyetheretherketone). AZoM, viewed 29 September 2024, https://www.azom.com/article.aspx?ArticleID=10147.
Simply put, PEEK is “best all around” when it comes to high performance and processing versatility. PEEK (polyetheretherketone) is a semi-crystalline thermoplastic with a linear aromatic polymer structure. The fully recyclable material melts at 343°C and possesses exceptional mechanical properties with resistance to chemicals, wear, fatigue and creep even at high operating temperatures where it is commonly used in service.
Mold maintenance is critical, and with this collection of content we’ve bundled some of the very best advice we’ve published on repairing, maintaining, evaluating and even hanging molds on injection molding machines.
Take a deep dive into all of the various aspects of part quoting to ensure you’ve got all the bases—as in costs—covered before preparing your customer’s quote for services.
Mixed in among thought leaders from leading suppliers to injection molders and mold makers at the 2023 Molding and MoldMaking conferences will be molders and toolmakers themselves.
John Walling, Strategic Marketing Manager for Victrex Polymer Solutions, talks to AZoM about metal replacement with PEEK (polyetheretherketone).
Formnext Chicago is an industrial additive manufacturing expo taking place April 8-10, 2025 at McCormick Place in Chicago, Illinois. Formnext Chicago is the second in a series of Formnext events in the U.S. being produced by Mesago Messe Frankfurt, AMT – The Association For Manufacturing Technology, and Gardner Business Media (our publisher).
While prices moved up for three of the five commodity resins, there was potential for a flat trajectory for the rest of the third quarter.
The aim of this presentation is to guide you through the factors and the numbers that will help you determine if a robot is a smart investment for your application. Agenda: Why are you considering automation? What problems are you trying to solve? How and why automation can help Crunch the numbers and determine the ROI
In a time where sustainability is no longer just a buzzword, the food and beverage packaging industry is required to be at the forefront of this innovation. By adopting circular packaging processes and solutions, producers can meet regulatory requirements while also satisfying consumer demand and enhancing brand reputation. Join Husky to learn more about the broader implications of the circular economy — as well as how leading brands are leveraging this opportunity to reduce costs, increase design flexibility and boost product differentiation. Agenda: The cost and operational benefits of embracing circularity Key materials in circular packaging — including rPET and emerging bioplastics How to design a circular food and beverage package Strategies for selecting sustainable closures to future-proof packaging solutions Optimization and streamlining of production processes for enhanced efficiency How Husky Technologies can enable your sustainable success
Victrex plc.. "Replacing Metals with PEEK (Polyetheretherketone)". AZoM. https://www.azom.com/article.aspx?ArticleID=10147. (accessed September 29, 2024).
"While heavier metals were first replaced with aluminium, titanium and magnesium, we now see engineers looking to further optimize their designs by replacing these “light metals” with VICTREX® PEEK. We now have over 35 years of experience in working with customers on metal replacement and a growing list of applications across all industries."
Core Technology Molding turned to Mold-Masters E-Multi auxiliary injection unit to help it win a job and dramatically change its process.
While the automotive industry drives for weight reduction to achieve increased fuel efficiency needed to meet aggressive government mandates, noise reduction and low maintenance are also important design goals. In the gear example, noise, vibration, and harshness was lowered by 3dB – this is equivalent to a 50% noise level reduction for the human ear.
Discover how artifical intelligence is revolutionizing plastics processing. Hear from industry experts on the future impact of AI on your operations and envision a fully interconnected plant.
The Plastics Industry Association (PLASTICS) has released final figures for NPE2024: The Plastics Show (May 6-10; Orlando) that officially make it the largest ever NPE in several key metrics.
While prices moved up for three of the five commodity resins, there was potential for a flat trajectory for the rest of the third quarter.
GETTING A QUOTE WITH LK-MOULD IS FREE AND SIMPLE.
FIND MORE OF OUR SERVICES:
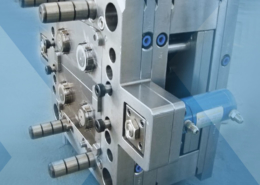
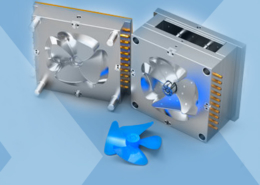
Plastic Molding

Rapid Prototyping
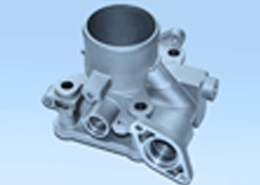
Pressure Die Casting
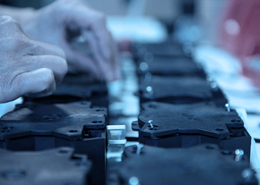
Parts Assembly
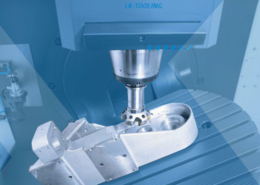