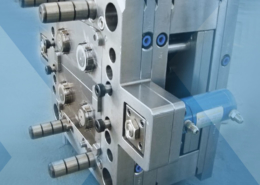
LEGO Removes Oil from Blocks: All About LEGO Manufacturing - abs plastic molding
Author:gly Date: 2024-09-30
Avenue elected several add-on options — activeFlowBalance, activeRemote activeLock and a VNC connection — to enhance control over the moulding process and guarantee the dimensional precision that is demanded by the healthcare industry. activeFlowBalance uses machine-control technology to balance filling fluctuations, ensuring shot-to-shot consistency, and activeRemote in conjunction with the VNC (Virtual Network Cable) allows remote diagnosis from Sumitomo personnel for both technical and process issues on-line.
At the start of 2020, Avenue instigated discussions with Sumitomo, with a view to the new press coming on-stream by June/July.
Sumitomo’s 75 tonne IntElect all-electric injection moulding machine ticked all the boxes in Avenue’s brief for a small footprint machine for performing test runs during the development phase of projects.
Avenue has, in recent years, decided that any new presses should be all-electric on the grounds of the energy-efficiency, consistency and low noise advantages they offer compared with their hydraulic counterparts.
Avenue, a Nolato Company, has taken delivery of a 75 tonne IntElect all-electric injection moulding machine at its site in Sligo, Ireland, describing it as “the ideal machine for medical start-up projects”. The investment will support growth in the company’s healthcare division, providing dedicated capacity to mould precision parts during the product development phase.
It's worth noting that the LDPE didn't stick to the molds, i.e. they didn't require any release agents. They did, however, get a little flash. And they report that the cycle time was three minutes per shot.
“Our business was already experiencing strong natural growth, yet the COVID crisis has augmented this growth — test products and IV fitments are in demand across the world,” says Henn.
With demand for its medical device injection moulding and tool-building services on the rise, in summer 2019, Avenue installed a new 100 sqm ISO Class 8 cleanroom area at its Sligo facility. This expansion necessitated an increase in capacity for moulding tools for producing components such as vials, test trays, luer lock fitments & connectors, as well as shell housing mouldings & mating components, for medical device assemblies.
Next they used a desktop (okay, benchtop) Galomb Model B-100 Injection Molder, which is relatively affordable at about four grand. They squirted low-density polyethylene into the mold--LDPE was specifically chosen for its low-melt temperature--and were successfully able to produce these parts:
Avenue, a Nolato Company, has taken delivery of a 75 tonne IntElect all-electric injection moulding machine at its site in Sligo, describing it as the ideal machine for medical start-up projects.
“A lot of our medical device projects start with a development phase, when we need to produce a single- or two-cavity tool before scaling up,” explains Gerard Henn, general manager of the Ireland-based Avenue operation, which is an integral part of Nolato GW & the Nolato Medical Solutions business area.
The IntElect also comes with a choice of five screw diameters for maximum flexibility - Avenue can run a variety of tools with different shot weights.
“All medical programmes are lengthy as it can take 2–3 years to obtain approvals from the authorities, so there are many months of testing before a component or mould is ready to be scaled up to mass production. Test runs might be anything from 10,000 to 100,000 units. “To satisfy this range of volume requirements, the mould size and cavitation suits this press perfectly,” explains Henn.
“Usually, if you want to use a larger mould, you have to go to a larger machine, say a 100-tonne one. With the IntElect 75 you can run a larger mould in a smaller machine,” explains Darren Herron, Sumitomo’s National Sales Manager for the UK and Ireland.
“The medical industry demands that components are produced within extremely tight tolerances and the allowable tolerances are getting tighter all the time. We find that these process control features are invaluable in ensuring customer acceptance of tools, instilling confidence that that they will work as intended to produce a precision component with high repeatability and accuracy,” says Henn.
RainIs this the White Paper you referred to?https://archive-media.formlabs.com/upload/injection-molding-from-3d-printed-molds.pdf
"For low-volume production (approximately 10-100 parts), 3D-printed molds save time and money. They also enable a more agile manufacturing approach, allowing engineers and designers to easily modify molds and continue to iterate on their designs with low lead times and cost."
The medical industry demands that components are produced within extremely tight tolerances The process control features on the IntElect are invaluable in ensuring customer acceptance of tools, producing precision components with high repeatability and accuracy.
Now that desktop 3D printing has become widespread, there's another production method crossing over into the DIY realm: Desktop injection molding. It's now possible "to create molds in-house to produce small, functional parts in production plastics," writes Formlabs.
With a stereolithography (SLA) 3D printer, you can produce molds that are smooth and strong enough--at least with a little help--to use for injection-molding small runs (10 to 100 parts, Formlabs reckons). What they've done in their testing is placed the molds--which have cavities, gates and sprues, they're the real deal--into aluminum frames, which prevent the mold from warping. You can work with standardized aluminum frames from injection molder manufacturers, or spend the bread to have something custom fabricated at a machine shop.
For the mold material they used both clear and high-temperature resin. Obviously you need something that can withstand a higher temperature than the plastic that's going to be squirted into it.
He continues: “The footprint of the IntElect is nice and compact — not overly long or wide; it comes with a number of process control features and has all the interfaces needed to seamlessly connect with other pieces of supporting equipment.”
The machine’s exceptionally small footprint is down to the use of Sumitomo’s own motors and drives — some competitors buy these parts in, making a compact design more difficult to achieve.
This model has particularly wide tie bar spacing and high clamp force for its size, allowing the use of larger moulds than would normally be accommodated by a 75 tonne machine.
While it's free to download, there is a catch--you need to enter your e-mail address, and they openly state "We will also opt you into other relevant marketing communication," so you can presumably expect some spam.
GETTING A QUOTE WITH LK-MOULD IS FREE AND SIMPLE.
FIND MORE OF OUR SERVICES:
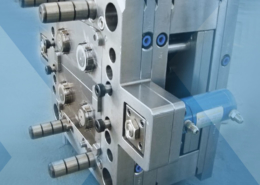
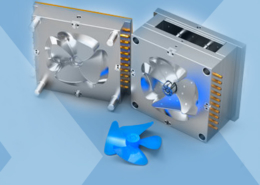
Plastic Molding

Rapid Prototyping
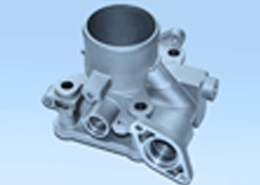
Pressure Die Casting
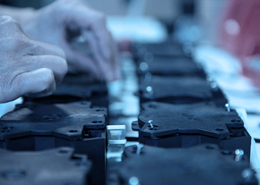
Parts Assembly
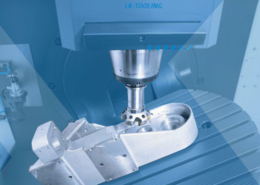