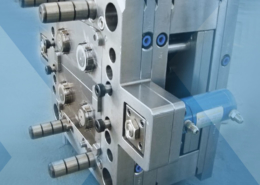
LEGO House The Brick Moulding Machine (40502) Officially Revealed - injection mo
Author:gly Date: 2024-09-30
Stephen has been with PlasticsToday and its preceding publications Modern Plastics and Injection Molding since 1992, throughout this time based in the Asia Pacific region, including stints in Japan, Australia, and his current location Singapore. His current beat focuses on automotive. Stephen is an avid folding bicycle rider, often taking his bike on overseas business trips, and is a proud dachshund owner.
Engel is presenting a mold at the K show which can process different labels at the same time. This sees the partners respond to the globally different trends in in-mold labeling which are in line with the EPBP and/or Recyclass recommendations in the EU, and with the specifications from the Association of Plastic Recyclers (APR) for the USA.
Also, recycling schemes for these materials lack the approval of the European food authority, European Food Safety Authority (EFSA). rPET offers a solution for avoiding penalties and special taxes. Although the price for PET is currently high, this concept makes the material a cost-effective alternative. EFSA has approved numerous recycling processes for PET, thus ensuring that rPET is available in Europe.
Negri Bossi brought a molding machine to the K that is older than the show itself, which is marking its 70th anniversary this year.
The new model 280 e-speed high-performance injection unit for K 2022 (shown above) achieves injection speeds up 1,400 mm/55 inches per second at a maximum injection pressure of up to 2,600 bar when processing small shot weights with an extreme wall-thickness-to-flow-path ratio.
With the use of integrated in-mold labeling (IML), the containers are ready-for-filling as soon as they leave the production cell. The special feature in this application is the material. The thin-walled containers are produced directly from rPET in a single step.
Engel and partners’ development yields thin-walled food containers made in a single injection-molding step using up to 100% recycled PET.
Until now, it has only been possible to process PET in thick-walled parts such as bottle preforms in injection molding. In that standard process, the final packaging format was created in a second step of the process — by blow molding, for example.
A different technology is used in Europe: an in-mold label that floats during the recycling process makes it easy to separate the dyes and the label from the PET.
The modified rPET being processed at the K show is sourced from PET beverage bottles recycled in the plants of packaging and recycling specialists ALPLA Group, which is headquartered in Hard, Austria. Other partner companies involved in the show exhibit are Brink (Harskamp, Netherlands) for the mold and IML automation and IPB Printing (Reusel, Netherlands) for the labels.
Featuring a wall thickness of 0.32mm/0.013 inch, the transparent, round 125-mL containers are representative of a whole category of plastic packaging, especially in the food industry.
For the first time, thin-walled containers made of PET, specifically recycled PET (rPET), can be produced in a single injection-molding process step.
Both celebrate their 75th anniversary this year, both companies have red in their logo, and both are now under the same roof at K 2022 in Düsseldorf, Germany. Japan’s Nissei Plastic Industrial and Italy’s Negri Bossi are exhibiting jointly for the first time in hall 15, booth B22, after Nissei acquired Negri Bossi in 2020. Also present at the booth is robot maker Sytrama, part of the Negri Bossi group.
An Engel e-speed 280/50 injection molding machine is the heart of the production cell. Engel specifically developed this hybrid machine with its electrical clamping unit and hydraulic injection unit for the high-performance requirements of thin-wall injection molding.
The dyes used on in-mold labels for the American market and its requirements can be washed off as the intent is to recycle the labels and the packaging.
Negri Bossi, for its part, has shipped in a hand-operated unit that was built in 1946 (background in the photo), one year before the company was officially incorporated. The NB28 15-tonne press was the first machine manufactured in Italy and it was sold to a factory near Bergamo for 450,000 lira (€232 in today’s money) to mold buttons from polystyrene.
In cooperation with partners Alpla Group, Brink Recycling, IPB Printing, injection molding machine manufacturer Engel is presenting a step forward for the packaging industry at K 2022 by processing recycled material, rPET, at its stand. Featured will be an Engel e-speed injection molding machine with a newly developed and extremely powerful injection unit.
Rick Lingle is Senior Technical Editor, Packaging Digest and PlasticsToday. He’s been a packaging media journalist since 1985 specializing in food, beverage and plastic markets. He has a chemistry degree from Clarke College and has worked in food industry R&D for Standard Brands/Nabisco and the R.T. French Co. Reach him at [email protected] or 630-481-1426.
To process rPET, Engel combines the new injection unit with a plasticizing unit from in-house development and production specifically designed for processing recycled material. During plasticizing and injection, the viscosity of the PET is configured for thin-wall injection molding. The new Engel e-speed supports the processing of arbitrary recycled materials up to 100% rPET.
Engel will present this technology and other developments at K 2022 in Düsseldorf, Germany, from Oct. 19 to 26, in booth C58 in Hall 15.
More recent highlights at the joint Nisse/Negri Bossi booth include an injection molding machine outfitted with an injection blow molding tool from Spanish mold builder Molmasa that employs factory compressed air. The production cell is being demonstrated molding 500-ml biodegradable PLA jars with in-mold PLA labeling.
Under the European Plastics Pact, the intent is for all plastic packaging to contain 30% recycled material and to be 100% recycling capable by 2025. Typical materials used for packaging foods in thin-walled containers are polyolefins (polyethylene, polypropylene) or polystyrene.
To date, PET is the only packaging material which can be processed as a recycled material on an industrial scale to create food packaging. This innovation sees partner companies pave the way for removing the need to downcycle packaging products other than bottles, and opens an opportunity for recycling or upcycling. This would substantially extend the range of uses for PET and rPET. In addition to the bottle-to-bottle cycle, this also means that the establishment of bottle-to-cup or even a cup-to-bottle recycling is conceivable.
An Engel spokesperson tells PlasticsToday that, among others, “the [rPET] cups can be used for food products such as dairy products, gourmet salads, or sandwich spreads.”
Nissei and Negri Bossi have brough some of their oldest injection molding machines to the show. The YD-2 in the foreground of the photo dates back to 1960; it was Nissei’s first production model after it was incorporated as an injection machine maker in 1957. With a clamping force of 30 tonnes, the YD-2 on show was used for more than 40 years by a processor molding various resins, including polyacetal, polystyrene, and PVC, before being donated to the Nissei museum.
GETTING A QUOTE WITH LK-MOULD IS FREE AND SIMPLE.
FIND MORE OF OUR SERVICES:
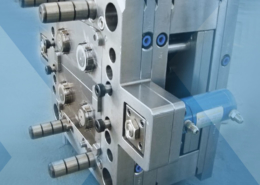
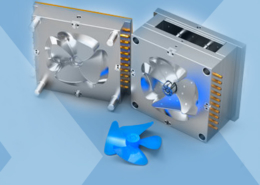
Plastic Molding

Rapid Prototyping
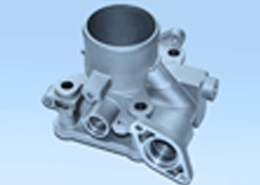
Pressure Die Casting
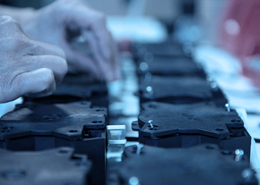
Parts Assembly
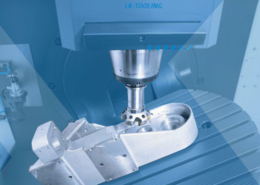