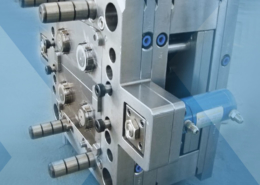
Lakeshore Plastics Expands Capacity, Turnkey Services to Meet Demand - molds for
Author:gly Date: 2024-09-30
The ABC understands the Clayton site was given $3.5 million by the government remediation fund to fix the cladding, but builders could not rectify the issues because the damage underneath was so substantial. They requested millions more to finish the job and left the site without completing the works.
VCAT documents reveal the VBA found the company had contravened the Building Act by carrying out work in breach of building regulations and the building permit and had "engaged in conduct ... that was negligent".
"It is an absolute catastrophe because if there's significant mould issues, the cost to rectify might well exceed the value," she said.
While the major correction in PP prices was finally underway, generally stable pricing was anticipated for the other four commodity resins.
This new family of clear engineering thermoplastics made its first big splash in extrusion, but now injection molders are learning how to process these amorphous resins into optical and medical parts.
CSV said in a statement it was "working with the owners on a solution for a highly complex building. Works will resume shortly".
Say “manufacturing automation” and thoughts immediately go to the shop floor and specialized production equipment, robotics and material handling systems. But there is another realm of possible automation — the front office.
In Australia, builders are required to comply with the National Construction Code, and each state has variations within it.
In this collection of articles, two of the industry’s foremost authorities on screw design — Jim Frankand and Mark Spalding — offer their sage advice on screw design...what works, what doesn’t, and what to look for when things start going wrong.
"The difficulty is their (CSV's) total budget is $600 million, and they need something in the order of two and a half to three billion dollars."
Ticona introduced Topas COCs five years ago as a lower-cost alternative to other COC materials produced by non-metallocene technologies. The first commercial plant (66 million lb/yr) started up in 2000. Metallocene-catalyzed COCs offer excellent optical properties, high flow, and ultra-low moisture absorption. In addition, their density is 3% lower than that of polystyrene and 15% less than polycarbonate and acrylics.
Mold temperature for COCs should not be more than 90° F below the Tg for lower-temperature grades and not more than 54° below Tg for high-heat grades. Warmer molds minimize silver streaks, decrease molded-in stresses, and preserve clarity. Because COCs set up rapidly and their viscosity rises steeply as they cool towards Tg, molds should be hot enough to minimize weld-line formation.
A number of residents who spoke to the ABC were unable to comment publicly because of legal proceedings against body corporates and building managers.
COC parts can be solvent bonded using a 15% solution of COC in cyclohexane, heptane, or other aliphatic solvent. Some commercial adhesives, such as those based on polyurethane, also work well with this polymer.
With advocacy, communication and sustainability as three main pillars, Seaholm leads a trade association to NPE that ‘is more active today than we have ever been.’
But experts say in some cases the material has led to building damage so severe that apartment complexes could be deemed worthless.
Successfully starting or restarting an injection molding machine is less about ticking boxes on a rote checklist and more about individually assessing each processing scenario and its unique variables.
When asked about compensation to residents of the Clayton apartments, in a statement a company spokesman said the situation was "very complicated and currently before the tribunal".
Tracey, whose name has been changed to protect her identity for legal reasons, has been fighting legal and health battles for years that she says stem from flooding and mould in her Queensland apartment.
Across all process types, sustainability was a big theme at NPE2024. But there was plenty to see in automation and artificial intelligence as well.
"He has all the questionable practitioners shaking in their boots. He goes to building sites, he looks at drawings, he talks to people – and he is actually making a difference."
Shangri-La Construction successfully appealed a suspension from the Victorian Building Authority (VBA) in the Victorian Civil and Administrative Tribunal (VCAT) earlier this year.
"The funding models have to be changed so that they can build these technical capabilities to go out and do the sort of enforcement and proactive work that we're seeing done in New South Wales.
We acknowledge Aboriginal and Torres Strait Islander peoples as the First Australians and Traditional Custodians of the lands where we live, learn, and work.
The Plastics Industry Association (PLASTICS) has released final figures for NPE2024: The Plastics Show (May 6-10; Orlando) that officially make it the largest ever NPE in several key metrics.
"I got a thermal test done out of my own pocket ... And they confirmed that my whole dining room area had moisture in the field," she said.
"Everybody wants to make money. There's nothing wrong with making money. There is something wrong with making money when you're cutting corners. And that is where we need a regulator."
While prices moved up for three of the five commodity resins, there was potential for a flat trajectory for the rest of the third quarter.
Development of new filled, reinforced, flame-retardant, and impact-modified COC grades will open up applications like this business-machine deck (above) and automotive air-conditioning fan (top).
Workers have uncovered significant mould damage inside the framework of this apartment building in Clayton, Victoria. (Supplied)
(2021 Update: Topas COC was developed in the 1990s by Hoechst Celanese, and initially marketed by Ticona. After a couple of reorganizations and ownership changes, Topas COC is today manufactured by Topas Advanced Polymers GmbH, a company of the Polyplastics Group, and outside EMEA is sold by Polyplastics. The company will soon be adding a second plant for the manufacture of COC, thanks to growing global demand in medical and packaging applications.)
"What's happened in Victoria with these cladding projects where EPS has been removed is they have found a prevalence of mould inside the wall system," said building regulation consultant Bronwyn Weir.
COCs absorb almost no water and do not need drying. If the resin does become wet, surface water can be driven off by about 2 hr of heating at 54° F below the resin’s HDT.
COCs can be ultrasonically welded to depths of 0.5 to 1.0 mm in 1 to 3 sec. Vibration amplitudes are typically 15 to 35 microns.
Tools can be made of standard mold steels but should be polished well to eliminate surface imperfections. This is vital for optical applications, where a finish down to a quarter of a wavelength of light may be required.
Tracey bought her 2004 apartment in 2014 and said the home had multiple issues with leaking, which stemmed from failed waterproofing from her balcony doorway and an external wall.
Injection molding grades of COC from Ticona have a glass-transition temperature (Tg) between 70 and 185 C (158 to 365 F). As a result, their heat-deflection temperature (HDT) ranges from 75 to 170 C (167 to 338 F). Grades with Tg above about 140 C (284 F) have a flexural modulus in the vicinity of 500,000 psi and elongation at break of 3% to 4%. Those with a lower Tg have a lower modulus but greater elongation (up to 10%).
Across the show, sustainability ruled in new materials technology, from polyolefins and engineering resins to biobased materials.
Ultradent's entry of its Umbrella cheek retractor took home the awards for Technical Sophistication and Achievement in Economics and Efficiency at PTXPO.
Exhibitors and presenters at the plastics show emphasized 3D printing as a complement and aid to more traditional production processes.
So far, COCs have been molded almost exclusively on reciprocating-screw injection presses. Though there is little industry experience with COCs in two-stage screw/ plunger systems, their thermal stability should be adequate for use in such a system.
"CSV was not created to provide taxpayer funds to private owners to fix defects in their buildings but to help owners to reduce the risk of fire where combustible cladding is present," they said.
Plastics Technology covers technical and business Information for Plastics Processors in Injection Molding, Extrusion, Blow Molding, Plastic Additives, Compounding, Plastic Materials, and Resin Pricing. About Us
The authority found the building company did not have a permit for the EPS cladding and failed to install it "in accordance with the Act, building regulations and permit," thereby breaching their duty by carrying out work that would "significantly compromise the safety of the building occupants".
technotrans says climate protection, energy efficiency and customization will be key discussion topics at PTXPO as it displays its protemp flow 6 ultrasonic eco and the teco cs 90t 9.1 TCUs.
Common factors included poor ventilation, rain ingress, water-damaged ceilings and incorrectly installed exterior walls, all of which appear to have contributed to the proliferation of mould.
The building is one of hundreds of Melbourne blocks covered in expanded polystyrene (EPS) cladding, an exterior material that can pose a significant fire hazard due to its combustibility.
The Victorian Building Authority said as of November 2022, they have identified 1,934 buildings with combustible cladding and referred 631 buildings to Cladding Safety Victoria.
COCs retain mechanical properties well over multiple regrind cycles and as much as 20% regrind can be used in many parts. Reground COC may yellow slightly during molding, so regrind cannot be used in optical applications or where very high clarity is needed.
Post-molding shrinkage of COCs typically falls between 0.4% and 0.7%. Shrinkage is greater with higher Tg grades and tends toward lower values as cavity pressure rises. Shrinkage in the flow direction is only slightly greater than that in the transverse direction, so very flat parts can be molded. COCs’ good stiffness and flow means that parts can have walls down to 1 mm or less.
The Victorian government scheme, set up to remove the cladding, is helping some owners pay for its removal but the funding does not cover mould damage.
Oversight by licensing bodies can be weak, and experts claim the oversight from regulators of the commercial building industry is inadequate and ineffective.
In this collection, which is part one of a series representing some of John’s finest work, we present you with five articles that we think you will refer to time and again as you look to solve problems, cut cycle times and improve the quality of the parts you mold.
COCs should be processed in hot molds to maximize flow length and weld-line strength and prevent shock freezing that can embrittle parts and make them prone to stress cracking. Hot molds also reduce haze, splay marks, and streaks and improve surface quality. Mold temperature is often the determining factor in reducing haze in optical parts. Each COC grade has an optimum mold temperature that minimizes part haze. Streaking can be controlled by using the proper balance between injection speed and mold temperature. Bubble formation and nozzle drool can be reduced by using moderate backpressure (between 20% and 30% of maximum). If discoloration occurs in parts that need extreme clarity, it helps to use a nitrogen blanket over the hopper to keep oxygen away from the resin.contaminants in COCs can cause bubbling, black specks, haze, and smoky swirls in clear parts. To prevent this, molders should thoroughly purge other materials from the barrel and feed areas and from material-transfer systems. It is best to remove the screw and clean both it and the barrel.
Gifted with extraordinary technical know how and an authoritative yet plain English writing style, in this collection of articles Fattori offers his insights on a variety of molding-related topics that are bound to make your days on the production floor go a little bit better.
"The interesting thing is before the statewide cladding audit, I would learn about unsafe, or non-compliant cladding, because of mould. It seems that mould and cladding go together, especially when we have expanded polystyrene walls," he said.
In a time where sustainability is no longer just a buzzword, the food and beverage packaging industry is required to be at the forefront of this innovation. By adopting circular packaging processes and solutions, producers can meet regulatory requirements while also satisfying consumer demand and enhancing brand reputation. Join Husky to learn more about the broader implications of the circular economy — as well as how leading brands are leveraging this opportunity to reduce costs, increase design flexibility and boost product differentiation. Agenda: The cost and operational benefits of embracing circularity Key materials in circular packaging — including rPET and emerging bioplastics How to design a circular food and beverage package Strategies for selecting sustainable closures to future-proof packaging solutions Optimization and streamlining of production processes for enhanced efficiency How Husky Technologies can enable your sustainable success
The company who constructed the Clayton apartment block, which practitioners described as posing an "extreme" fire risk to occupants, continues to operate in the Victorian construction industry.
The first substantial wave of molded applications for the Topas family of metallocene-catalyzed cyclic olefin copolymers (COCs) is just now arriving on the market. Some limited molding activity with these new transparent engineering thermoplastics dates back to 1969, but injection molded (and injection-blow molded) medical and optical applications are only now starting to appear in force. Emerging uses include optical lenses, light guides, microtiter plates, syringe bodies, tubing connectors, catheter manifolds, and lids.
Shangri-La Construction did not respond to questions from the ABC about whether they were responsible for the extensive mould damage in the Clayton building.
Normal fill times are about 1 to 2 sec and cycle times typically extend from 10 sec for small, thin parts to 360 sec for parts 0.5-in. to 1-in. thick. Fill times for optical parts may be extended to 5 or 10 sec when using a mold temperature within 50° F of Tg.
When feeding COC pellets, allow them to warm up in the feed throat to 45° to 54° below the HDT by throttling back on the cooling water. This makes the pellets less brittle and therefore less likely to generate fines that can affect part homogeneity.
Shangri-La argued the suspension was "harsh and excessive" and "not consistent with disciplinary action taken against other building practitioners".
The ABC received hundreds of responses from across Australia as part of a crowdsource investigation into black mould, earlier this year.
Dr Tim Law, an architectural scientist and design specialist, said the problems facing apartment owners with faulty cladding across the country were serious and ongoing.
Thousands of people visit our Supplier Guide every day to source equipment and materials. Get in front of them with a free company profile.
A lot has been learned in the last few years about how to injection mold COC materials for best results in sensitive medical and optical applications. Micro-vial holders, syringe bodies, and lenses are just now making a commercial impact
Don’t assume you know everything there is to know about PE because it’s been around so long. Here is yet another example of how the performance of PE is influenced by molecular weight and density.
Because of COC’s low shrinkage, draft angles should be as large as possible—especially for parts with longer bearing lengths—to avoid distortion and demolding difficulties. Sticking can be a problem on parts with a shallow draft. Draft usually falls between 2° and 5°, though draft as low as 0.5° has been used successfully in some cases.
Resin drying is a crucial, but often-misunderstood area. This collection includes details on why and what you need to dry, how to specify a dryer, and best practices.
Mike Sepe has authored more than 25 ANTEC papers and more than 250 articles illustrating the importance of this interdisciplanary approach. In this collection, we present some of his best work during the years he has been contributing for Plastics Technology Magazine.
COCs can be used with all types of nozzles, although free-flow, open types are best because they allow for easier sprue pullout. The resin also can be used with nearly all gating styles. Fan gates are recommended because of their relatively low shear. Gate size should be generous enough to prevent excessive shear heating or premature freeze-off. Gating preferably should be into the thick end of a part and gate diameter should be at least 60% of the wall thickness. COCs with Tg above about 280 F should be run on oil-heated tooling. Grades with a lower Tg can use a circulating hot-water system for mold-temperature control.
Screw speed is usually in the moderate-to-fast range (50 to 150 rpm), depending on screw diameter and barrel size. The smaller the screw, the higher the rpm needed. Take care to homogenize the melt well, but without undue shear heating.
The aim of this presentation is to guide you through the factors and the numbers that will help you determine if a robot is a smart investment for your application. Agenda: Why are you considering automation? What problems are you trying to solve? How and why automation can help Crunch the numbers and determine the ROI
Core Technology Molding turned to Mold-Masters E-Multi auxiliary injection unit to help it win a job and dramatically change its process.
"In Frankston, probably one of the most infamous buildings ... because the cladding was done so poorly, it's breaking up, there are cracks.
This service may include material from Agence France-Presse (AFP), APTN, Reuters, AAP, CNN and the BBC World Service which is copyright and cannot be reproduced.
August 29-30 in Minneapolis all things injection molding and moldmaking will be happening at the Hyatt Regency — check out who’s speaking on what topics today.
Plastics Technology’s Tech Days is back! Every Tuesday in October, a series of five online presentations will be given by industry supplier around the following topics: Injection Molding — New Technologies, Efficiencies Film Extrusion — New Technologies, Efficiencies Upstream/Downstream Operations Injection Molding — Sustainability Extrusion — Compounding Coming out of NPE2024, PT identified a variety of topics, technologies and trends that are driving and shaping the evolution of plastic products manufacturing — from recycling/recyclability and energy optimization to AI-based process control and automation implementation. PT Tech Days is designed to provide a robust, curated, accessible platform through which plastics professionals can explore these trends, have direct access to subject-matter experts and develop strategies for applying solutions in their operations.
COC parts emerge from the mold with smooth surfaces and need little or no deflashing or finishing. They have a soft surface until they cool completely, so just-molded parts should be handled carefully. If possible, degate COC parts when they are still warm. For degating cold parts, use a band saw because snipping can cause fractures.
"Mould is a result of poor building construction or maintenance or both rather than the product of a specific type of cladding," a Cladding Safety Victoria (CSV) spokesperson said.
Given COCs’ low shrinkage, lubricated grades and mold-release agents can help in removing parts from a mold, especially if long cores are present. Choose mold sprays carefully to ensure they do not leave part surfaces hazy. Mold release can be helped by maintaining holding pressure a bit longer so the part relaxes before it is extracted.
This Knowledge Center provides an overview of the considerations needed to understand the purchase, operation, and maintenance of a process cooling system.
"There are numerous parties involved in the current litigation, including insurers. Because the matter is before the tribunal, no further comment will be made.
Learn about sustainable scrap reprocessing—this resource offers a deep dive into everything from granulator types and options, to service tips, videos and technical articles.
In this collection of content, we provide expert advice on welding from some of the leading authorities in the field, with tips on such matters as controls, as well as insights on how to solve common problems in welding.
Despite price increase nominations going into second quarter, it appeared there was potential for generally flat pricing with the exception of a major downward correction for PP.
"We have no [commissioner] in Victoria. We need a champion for the public. We need a champion for the consumer. We don't have that person," he said.
Introduced by Zeiger and Spark Industries at the PTXPO, the nozzle is designed for maximum heat transfer and uniformity with a continuous taper for self cleaning.
COCs can be finished by printing, coating, and metalizing as well as joining and machining. COCs are nonpolar materials, so relatively few materials stick to them. Before a COC part can be printed or coated, it needs corona or plasma pretreatment to functionalize its surface and allow bonds to form. Metal coatings are an exception: Vacuum-deposited aluminum, chromium, silver, nickel, and other metals adhere well to COCs without pretreatment.
Residual stress in parts can be limited by increasing injection speed in steps and by using mold temperatures as close to the resin’s Tg as possible. For low-stress parts, you should also avoid overpacking and long hold times. Try reducing holding pressure in stages to between 4000 and 7000 psi.
Shangri-La Construction said it was "currently assisting the VBA with responses to notices issued by the BA. In Shangri-La Construction's view, it would be inappropriate to discuss those matters before the VBA process is complete".
Workers have laid bare wall cavities riddled with black mould and rotten timber in poorly constructed apartment buildings that have been assessed under Victoria's cladding rectification regime.
In this three-part collection, veteran molder and moldmaker Jim Fattori brings to bear his 40+ years of on-the-job experience and provides molders his “from the trenches” perspective on on the why, where and how of venting injection molds. Take the trial-and-error out of the molding venting process.
Tracey and her partner commissioned a mould report in early 2022 which confirmed there was a high level of black mould growing in the walls, and throughout the apartment.
Discover how artifical intelligence is revolutionizing plastics processing. Hear from industry experts on the future impact of AI on your operations and envision a fully interconnected plant.
Take a deep dive into all of the various aspects of part quoting to ensure you’ve got all the bases—as in costs—covered before preparing your customer’s quote for services.
Mold maintenance is critical, and with this collection of content we’ve bundled some of the very best advice we’ve published on repairing, maintaining, evaluating and even hanging molds on injection molding machines.
While the melting process does not provide perfect mixing, this study shows that mixing is indeed initiated during melting.
Neither the VBA nor VCAT ruling makes specific reference to mould damage in the property, but the ABC has spoken to building experts with knowledge of the project who claim that the black mould growth is related to defects stemming from the poor construction and installation of EPS cladding on the building's exterior.
"And so the mould in some cases has begun to rot those timber frames and make them structurally compromised, as well as of course getting to the plaster and other components or elements of wall systems."
Sustainability continues to dominate new additives technology, but upping performance is also evident. Most of the new additives have been targeted to commodity resins and particularly polyolefins.
Multiple speakers at Molding 2023 will address the ways simulation can impact material substitution decisions, process profitability and simplification of mold design.
Up to now, these properties have been exploited mainly in extruded film and sheet. For injection molders, COCs offer glass-like transparency and excellent barrier to water vapor with high HDT and good electrical properties. COCs are amorphous polymers with high modulus and surface hardness. Chemically, they resist hydrolytic degradation, aqueous acids and bases, and most polar and oxygenated solvents. In injection molding, they provide high precision, and they flow well to fill complex, thin-walled parts with low shrinkage and warpage. Because COCs’ stiffness is 25% greater than that of polycarbonate, they lend themselves to molding thinner walls.
A National Health and Medical Research Council-funded research project commenced this year at Macquarie University, researching chronic respiratory symptoms in relation to biotoxin mould illness.
A lot has been learned in the last few years about how to injection mold COC materials for best results in sensitive medical and optical applications. Micro-vial holders, syringe bodies, and lenses are just now making a commercial impact.
In machining COC parts by cutting, drilling, and diamond turning, cuts should be conservative and made at relatively low speeds. This keeps the applied force low, so the COC does not shatter, and it prevents excessive heat build-up. Common machine oils attack COCs and can cause cracking, so coolants must be water-based and machine surfaces and tools must be free of oil.
After successfully introducing a combined conference for moldmakers and injection molders in 2022, Plastics Technology and MoldMaking Technology are once again joining forces for a tooling/molding two-for-one.
The NSW Building Commissioner says he wants to know why an apartment complex being built in the Sydney suburb of Castle Hill has "structural issues", and will refer the principal engineers to the industry's peak body.
Join Engel in exploring the future of battery molding technology. Discover advancements in thermoplastic composites for battery housings, innovative automation solutions and the latest in large-tonnage equipment designed for e-mobility — all with a focus on cost-efficient solutions. Agenda: Learn about cutting-edge thermoplastic composites for durable, sustainable and cost-efficient battery housings Explore advanced automation concepts for efficient and scalable production See the latest large-tonnage equipment and technology innovations for e-mobility solutions
Join Wittmann for an engaging webinar on the transformative impact of manufacturing execution systems (MES) in the plastic injection molding industry. Discover how MES enhances production efficiency, quality control and real-time monitoring while also reducing downtime. It will explore the integration of MES with existing systems, emphasizing compliance and traceability for automotive and medical sectors. Learn about the latest advancements in IoT and AI technologies and how they drive innovation and continuous improvement in MES. Agenda: Overview of MES benefits What is MES? Definition, role and brief history Historical perspective and evolution Longevity and analytics Connectivity: importance, standards and integration Advantages of MES: efficiency, real-time data, traceability and cost savings Emerging technologies: IoT and AI in MES
Bronwyn Weir said no government had implemented all recommendations from her report into systemic failures in the building industry, despite being five years on from its delivery.
Jonathan Barnett, a technical expert in fire safety engineering with more than 42 years' experience, said there was nowhere near enough funding needed to fix the problems.
The resin replicates extremely fine mold features. One precision COC laboratory component, for instance, has complex channels as small as 10 microns. COCs also faithfully reproduce sub-micron surface patterns, such as those found on diffraction gratings and optical data-storage media. Only neat grades of Topas COC have been offered until now, but glass-reinforced, mineral-filled, flame-retardant (UL 94V-2 and V-0), and impact-modified grades have been developed. Ticona has also made grades containing stainless-steel fibers to impart electrical conductivity. These new modified grades will open up potential in business machines, communications equipment, and automotive parts like headlight reflectors and air-conditioning fans.
An initial fine of $57,000 was more than halved on appeal, despite the building company being found to be "negligent" and to have conducted works in breach of permits and regulations.
Second quarter started with price hikes in PE and the four volume engineering resins, but relatively stable pricing was largely expected by the quarter’s end.
When molding optical parts, use a high mold temperature and keep injection speed as fast as possible to prevent flow marks. On the other hand, slower injection may be needed to overcome sinks, voids, and birefringence in thick optical parts. Some suck-back may be needed to prevent nozzle drool. Higher backpressure—as much as half of a machine’s maximum pressure—helps improve optical properties but should not be so high as to yellow the part or hinder screw retraction. Low holding times and pressures are also usually good for optical parts. Holding time varies from 30 to 60 sec, depending on part thickness. Cooling time can last from 60 to 120 sec. Longer cooling time helps reduce stress level in the part. Total cycle time for optical parts is typically 2 to 5 min.
Draft is affected by part length and must be higher with textured surfaces. Molders switching to COC from a material with greater shrinkage should modify the tool so it has sufficient draft for part release. If the tool was previously used for polycarbonate or acrylic, it can typically run COC without any modification.
Additive technology creates air pockets in film during orientation, cutting down on the amount of resin needed while boosting opacity, mechanical properties and recyclability.
"The cladding issues were widespread in the industry and have affected many builders and other professionals involved in building. These issues will not be repeated as combustible cladding is now banned," the spokesman said.
Dozens of residents from Melbourne, Sydney, Brisbane, and Canberra claimed structural defects in their apartments had led to water damage and mould growth.
"The VBA has and continues to investigate and take action against practitioners who have endangered the safety of Victorians by installing non-compliant combustible cladding," it said.
Join KraussMaffei for an insightful webinar designed for industry professionals, engineers and anyone interested in the manufacturing processes of PVC pipes. This session will provide a comprehensive understanding of the technology behind the production of high-quality PVC pipes: from raw material preparation to final product testing. Agenda: Introduction to PVC extrusion: overview of the basic principles of PVC pipe extrusion — including the process of melting and shaping PVC resin into pipe forms Equipment and machinery: detailed explanation of the key equipment involved — such as extruders, dies and cooling systems — and their roles in the extrusion process Process parameters: insight into the critical process parameters like temperature, pressure and cooling rates that influence the quality and consistency of the final PVC pipes Energy efficiency: examination of ways to save material and energy use when extruding PVC pipe products
Processors with sustainability goals or mandates have a number of ways to reach their goals. Biopolymers are among them.
"My poor dad who is retired has been paying for all of this out of his own pocket with a loan against his property and paying off that loan from superannuation ...which breaks my heart."
Join this webinar to explore the transformative benefits of retrofitting your existing injection molding machines (IMMs). Engel will guide you through upgrading your equipment to enhance monitoring, control and adaptability — all while integrating digital technologies. You'll learn about the latest trends in IMM retrofitting (including Euromap interfaces and plasticizing retrofits) and discover how to future-proof your machines for a competitive edge. With insights from industry experts, it'll walk you through the decision-making process, ensuring you make informed choices that drive your business forward. Agenda: Maximize the value of your current IMMs through strategic retrofitting Learn how to integrate digital technologies to enhance monitoring and control Explore the benefits of Euromap interfaces and plasticizing retrofits Understand how retrofitting can help meet new product demands and improve adaptability Discover how Engel can support your retrofitting needs, from free consultations to execution
COCs are usually molded on conventional machines having general-purpose, low-compression screws with ratios of 2.2:1 to 2.5:1. Screws are typically shallow single-flighted or barrier models made from standard tool steels. The screw should homogenize the melt gently because excessive shear heating can cause yellowing and optical inhomogeneity. A high-compression screw can generate too much shear and even shatter the pellets.
When, how, what and why to automate — leading robotics suppliers and forward-thinking moldmakers will share their insights on automating manufacturing at collocated event.
Optical parts are best processed in machines with higher screw L/D ratios, which tend to produce less splay and improve recovery times with lubricated grades. Barrels do not need venting because of the resin’s negligible water absorption.
Cylinder temperatures should be matched to the Tg of the grade used (see table). Melt temperatures are typically 200° to 215° F above the Tg and usually fall between 464 F and 572 F. (Molders tend to run at the high end of this range.)
Formnext Chicago is an industrial additive manufacturing expo taking place April 8-10, 2025 at McCormick Place in Chicago, Illinois. Formnext Chicago is the second in a series of Formnext events in the U.S. being produced by Mesago Messe Frankfurt, AMT – The Association For Manufacturing Technology, and Gardner Business Media (our publisher).
Tracey said since living in the waterlogged and mouldy apartment she has been diagnosed with a skin fungus that is "all over" her body.
The surveyor on the project was also fined $14,000 and suspended for nine months, but is appealing the decision at VCAT.
Baystar's Borstar technology is helping customers deliver better, more reliable production methods to greenhouse agriculture.
In the wake of the 2017 fatal Grenfell Tower fire in London, authorities in Victoria have been working to audit and rectify buildings using dangerous combustible cladding.
One of the buildings identified — an 81-dwelling apartment complex in Clayton in Melbourne's south-east — has internal framework which has been substantially rotted out by water damage and mould.
Coverage of single-use plastics can be both misleading and demoralizing. Here are 10 tips for changing the perception of the plastics industry at your company and in your community.
While prices moved up for three of the five commodity resins, there was potential for a flat trajectory for the rest of the third quarter.
"It's no longer weatherproof you're finding that you've got water running through the buildings and mushrooms growing there."
Residents have reported mould build-up in bedrooms and wardrobes due to the water damage, and many claimed the conditions had led to a negative impact on their health, including respiratory conditions.
This new family of clear engineering thermoplastics made its first big splash in extrusion, but now injection molders are learning how to process these amorphous resins into optical and medical parts.
Mixed in among thought leaders from leading suppliers to injection molders and mold makers at the 2023 Molding and MoldMaking conferences will be molders and toolmakers themselves.
Black mould is being uncovered in the walls of defective apartment blocks, in what experts describe as an "absolute catastrophe".
Injection moldable COCs have melt flow rates between 1 and 56 g/10 min at 260 C. Shot size should be one-quarter to one-half the capacity of the barrel. COCs can withstand barrel residence time of about 15 min at normal molding temperatures. If process interruptions are likely to be longer, maximum barrel temperature should be reduced to 302 F to avoid yellowing.
This month’s resin pricing report includes PT’s quarterly check-in on select engineering resins, including nylon 6 and 66.
In a statement, the company said the fine had been paid and further training required by VCAT orders would be undertaken in early 2023.
Tobe Packaging’s breakthrough was to create its Ecolefin PE multilayer film that could be applied with a specialized barrier coating.
Implementing a production monitoring system as the foundation of a ‘smart factory’ is about integrating people with new technology as much as it is about integrating machines and computers. Here are tips from a company that has gone through the process.
GETTING A QUOTE WITH LK-MOULD IS FREE AND SIMPLE.
FIND MORE OF OUR SERVICES:
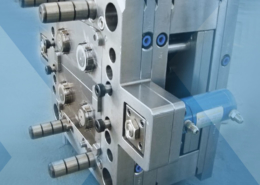
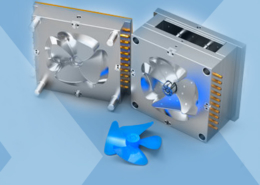
Plastic Molding

Rapid Prototyping
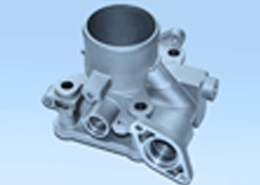
Pressure Die Casting
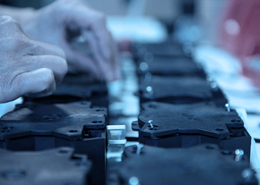
Parts Assembly
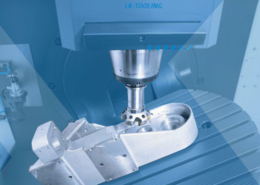