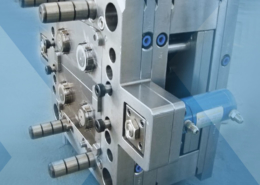
Krones Expands Injection Moulding Portfolio with €170 Million Acquisition
Author:gly Date: 2024-09-30
The strength and sturdiness of the Varibox ensures maximum protection so that product quality is maintained throughout the logistics chain.
ENGEL claims sim link makes problem-free data exchange between simulation and the injection moulding machine possible. This, in theory saves time consuming co-ordination loops between mould development and production.
Time-consuming and error-prone manual input of data at the machine is no longer necessary. sim link fulfils this data exchange between simulation software and injection moulding machine without errors.
ENGEL claims by using sim link, the number of repetitions could be significantly reduced. The quality of the simulation has also improved and become more accurate. Difficulties in the coordination could thus be successfully overcome.
Roto moulded in polyethylene, the robust construction of the Varibox features an inner container enclosed within a strong outer cover, and incorporates a special discharge valve for easy dispensing of product with no need to remove a cap.
The easy-to-clean design prevents product contamination and large recessed label areas provide plenty of room for all required product information, and a built-in RFID tag enables the Varibox to be tracked at every stage of its journey.
Integrated vents automatically open for safe dispensing and a pressure release system is available for products that cause a product build-up.
To meet the specific needs of the UK and Irish markets, the standard two-way secured entry pallet has been augmented with the availability of a four-way secured entry version, allowing even greater flexibility in the4 movement of the container by a forklift or pallet jack without compromising on safety.
Thanks to effective simulation of injection moulding, cost-intensive looping is reduced when optimising a new component. Where mould makers had to find the values manually for the initial sampling of the moulds, target values are now automatically transferred from the simulation to the injection moulding machine.
RPC Promens is introducing its proven Varibox IBC into the UK and Ireland, offering the ideal solution for the safe and cost-effective handling of hazardous chemicals.
ENGEL says experimental methods such as filling studies are often not sufficient and analytical methods lead to better results. however, the problem often arises of establishing a smooth data exchange between software and production.
Several experts are involved in the creation of a new product. sim link simplifies cooperation between simulation and production staff.
Equally importantly, the internal container can be reused by up to five years, providing a cost-effective means of transporting and storing chemicals while delivering an improved carbon footprint.
Every injection moulder faces challenges in achieving its production targets. The most important factor in the development of new products is a short time to market. At the same time, the costs for the development and the optimisation of the moulds must be kept low.
The individual machine dynamics are taken into account and the simulation can be carried out more realistically. The measured production data can be fed back into the simulation very easily. This improves the quality of the simulation.
GETTING A QUOTE WITH LK-MOULD IS FREE AND SIMPLE.
FIND MORE OF OUR SERVICES:
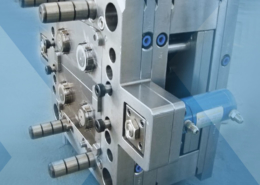
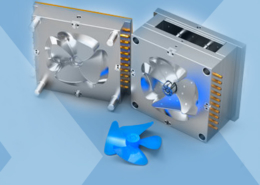
Plastic Molding

Rapid Prototyping
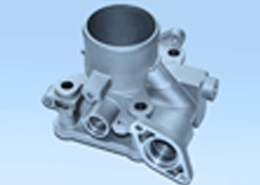
Pressure Die Casting
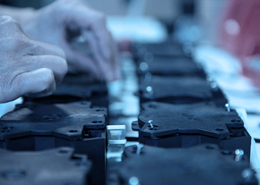
Parts Assembly
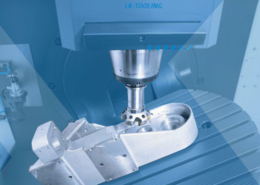