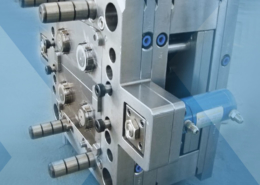
KraussMaffei Presents Recyclate-based ‘Sandwich’ Molding at Fakuma - injection t
Author:gly Date: 2024-09-30
Wittmann’s new beside-the-press blade granulator is suited for grinding large injection molded parts up to 500 x 200 mm (19.7 x 7.9 in.) in size.
Looking for more? Our expert team of researchers can create market analysis reports for any of your needs.
Because of their corrosion resistance and electrical insulation qualities, polypropylene components are widely used in food packaging and electrical contacts. Due to the aforementioned factors, the segment is anticipated to grow at the fastest rate during the forecast period. However, a reduction or cessation of manufacturing activities to fight the spread of the coronavirus has resulted in a decline in PP consumption and a negative impact on its demand in a variety of applications. Manufacturers are having difficulty operating their production units due to logistical constraints and limits on people's movement, which has impacted product demand.
Asia Pacific injection molded plastics market is projected to be worth over USD 140 billion by 2032. The regional growth can be credited to the flourishing automotive and construction sectors owing to the increasing demand and uptake of autonomous high-end luxury vehicles and the rising infrastructural investments. In addition, the robust economic outlook across countries such as China and India, coupled with the rapid industrial growth, will create positive growth prospects for the injection molded plastics industry in the Asia Pacific.
Because of its compact footprint, performance, and maximum material throughput of 100 kg per hour, the G-Max XL can be used as a beside-the-press granulator for inline recycling of sprues and reject parts during machine startup. It can also be used as a central granulator.
A new rail-guided die changing table for transporting heavy dies and molds is available in three versions for loads up to 15, 25, or 40 tonnes per die. The electric RWS system from Roemheld is equipped with two different pull-push mechanisms for the safe, automatic transport of dies to set-up presses. It is compatible with most machines.
The construction sector has witnessed an upward trend over recent years owing to the escalating rollouts of infrastructure development projects and the advent of several technological breakthroughs. Besides, the improving economic landscape and the significant rise in investments focused on building an energy-efficient infrastructure across numerous economies.
The open design of the three-blade cutting rotor makes the G-Max XL ideal for grinding heat-sensitive materials that still retain heat from processing, according to Wittmann. Open spaces between the blades and rotor shaft ensure ventilation, and the knives can be easily changed. The rotating and fixed blades, which are angled in opposite directions, ensure a clean scissor cut.
The new Airtect Plastic Leak Detection System from PCS Co. is designed to provide 24/7 protection of injection molding machine nozzles and manifold systems, reducing downtime and costly repairs.
No tools are required to access the cutting chamber or the screen fixture, which also facilitates cleaning and maintenance operations. Even material and color changes can be carried out very quickly, further increasing productivity.
The injection molded plastics industry depicted a decent growth potential during the COVID-19 pandemic, owing to a remarkable rise in demand for gloves, masks, personal protective equipment, and associated packaging materials. Based on investigations by Frontline, plastic resin production in the U.S. increased by 0.9% compared to COVID-19 restrictions and industry closures. Besides, the strict movement restrictions and social distancing norms resulted in a transformer buyer behavior and caused a massive boom across the e-commerce industry, further pushing the demand for packaging boxes and containers.
New T-Flow HRS control units from Oerlikon HRSflow increase the precision and reliability of temperature control in hot-runner injection molding. Modular in design, three models are configurable to multiples of six zones.
Regarding the application landscape, the packaging applications are expected to amass more than USD 135 billion by 2032, exhibiting a 3.5% growth rate throughout the projection period. To meet regulatory guidelines and end-user criteria, finished goods used in packaging go through several development stages. Plastics must satisfy several requirements for packaging applications, including improving food product shelf life, improved wear and tear resistance, and high durability. Plastic injection molding has enormous promise. Particularly in the medicinal and automotive fields. The medical devices and components sector is anticipated to grow the most in the industry. Product demand in the medical industry is anticipated to be driven by biocompatibility, optical clarity, and cost-effective manufacturing methods.
Home > Chemicals & Materials > Polymers > Industrial Polymers > Injection Molded Plastics Market
Editor in chief of PlasticsToday since 2015, Norbert Sparrow has more than 30 years of editorial experience in business-to-business media. He studied journalism at the Centre Universitaire d'Etudes du Journalisme in Strasbourg, France, where he earned a master's degree.
The Injection molded plastics market research report includes in-depth coverage of the industry with estimates & forecasts in terms of volume in kilo tons & in terms of revenue in USD billion from 2018 to 2032 for the following segments: Click here to Buy Section of this Report
A stringent regulatory environment for medical-grade polymer use in healthcare industries is expected to fuel the injection molded plastics market growth. Over the forecast period, a growing preference for biodegradable polymers among medical device makers is expected to generate profitable opportunities in the medical industry. A significant shift in the automotive industry's trend towards replacing steel with plastics is anticipated to fuel product demand over the forecast period. In recent years, government rules have compelled automakers to use plastics instead of other materials such as iron and steel. Automobile makers have been concentrating on reducing vehicle weight in order to increase fuel efficiency.
A standardized base plate accepts dies of various sizes, and the integrated control system enables semi- and fully automatic die changes and precise positioning to within ±0.3 mm.
“The Airtect Plastic Leak Detection System is an essential tool that can be installed directly onto the injection molding machine nozzle or hot runner manifold system," said PCS VP of sales Derrick Jones. “It quickly alerts users of leaks in the form of an alarm and/or the suspension of production, enabling faster operator response and repair. The system can be adapted to any hot runner system, either new or retrofit.”
Unlike stamping punches, which are sometimes used as core pins in molds, the heads of TI pins are precision ground to mold tolerances. Also, rather than beginning with a fractional-diameter core pin, step grinding can be eliminated with mold inserts fabricated to the molded part diameter via wire electrical discharge machining. The TI pins only need to be cut to the finished length.
Global Market Insights Inc. 4 North Main Street, Selbyville, Delaware 19975 USA Toll Free: +1-888-689-0688 USA: +1-302-846-7766 Europe: +44-742-759-8484 APAC: +65-3129-7718 Email: sales@gminsights.com
Injection Molded Plastics Market size garnered over USD 300 billion in 2022. With the consistent expansion of the construction sector globally, the industry is set to witness 3.5% CAGR from 2023 to 2032.
From nozzle leak-detection systems to precision-ground ejector pins, these recently introduced products promise to save injection molders time and money.
The system sends tiny volumes of low-pressure air through robust stainless-steel sensor tubes to quickly detect most leaks thanks to a self-teaching algorithm, said PCS.
The starter kit comes with a small controller, an air regulator, silicone tubing, stainless-steel tubing, and polyurethane tubing. Users can build onto the starter kit with additional accessories that make it possible to perform full hot-runner manifold leak detection.
The combination of integrated touchscreen, clear text display, smart navigation, and guided operation results in a particularly user-friendly concept without the need for instruction or prior knowledge, according to Oerlikon HRSflow. Recipes and test reports can be installed and transferred quickly and efficiently via the integrated USB port. Data is exchanged with the injection molding machine via the OPC UA interface in accordance with the new Euromap 82.2 standard protocol for hot-runner controllers. The integrated VNC server also enables convenient operation via notebook, tablet, or smartphone.
T-Flow HRS precisely controls the nozzle temperatures, allowing universal use, even in demanding high-performance applications with compact nozzles. Several heating options are available, and different recipes can be saved, stored, compared, and quickly called up.
Players in the market have been widely integrating advanced technologies to develop state-of-the-art products to gain a competitive edge over their counterparts and expand their existing consumer base. For instance, in July 2022, Sabic introduced a specially personalized portfolio of new mineral-reinforced Sabic PP compounds, PPc F9015, PPc F9005, and PPc F9005 grades for foam injection molding (FIM). The newly introduced product range help provide stunning aesthetics for visible automotive interior parts with complicated geometries, such as seat and trunk cladding, door panels and trim, center consoles, and A/B/C/D pillar covers.
With respect to raw material, the injection molded plastics market is segregated into Acrylonitrile Butadiene Styrene (ABS), polypropylene (PP), High-Density Polyethylene (HDPE), Polystyrene (PS), and others. The Polypropylene segment is expected to expand at over 4% CAGR and exceed USD 160 billion by 2032. Because of the growing consumption of PP in automotive components, packaging applications, and household goods, the polypropylene (PP) segment held the biggest revenue share of more than 34% in 2021. Increasing PP-based product penetration in protective caps for electrical contacts and battery housings, as well as food packaging, is expected to fuel demand over the projection period.
Designed to fit into small, crowded cavity and core inserts, the pins are manufactured with hardened M-2 steel and are available in diameters from 0.060 to 0.320 in. and in 2.5- and 5.5- in. lengths. Cut-to-length and custom options are also available.
The integrated pull-push mechanism moves dies on and off the press bed via the roller rails. A safety device ensures that loads can only be moved when the RWS die changing table is firmly attached to the press or storage space.
The RWS system, for example, can help car manufacturers integrate numerous individual parts into increasingly large castings, which are processed with heavier dies in larger presses and punches.
These trends, in covalence with the adoption of distinctive growth initiatives by premier product manufacturers and rising investments across the construction sector, will boost the industry revenue trajectory over the next ten years.
Plastic injection molding is widely utilized across several industrial verticals ranging from electronics, automobiles, and construction to kitchen utensils and toys. The stringent government regulation pertaining to minimizing plastic pollution and the increased adoption of effective waste management techniques may restrict industry growth during the forecast period. On the other hand, the consolidated competitive landscape and the increasing strategic exchanges among leading product manufacturers will accelerate business growth through the ensuing years.
The die changing table travels on floor-level round rails, with a rolling resistance so low that up to five-ton loads can be moved manually by one person. In addition, the rails are designed to facilitate precise carriage guidance and to prevent dirt deposits and tripping hazards in the floor.
GETTING A QUOTE WITH LK-MOULD IS FREE AND SIMPLE.
FIND MORE OF OUR SERVICES:
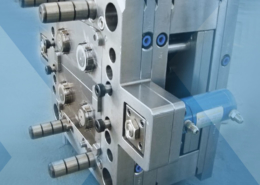
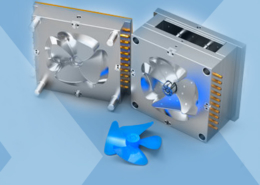
Plastic Molding

Rapid Prototyping
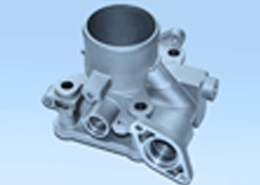
Pressure Die Casting
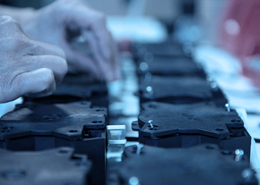
Parts Assembly
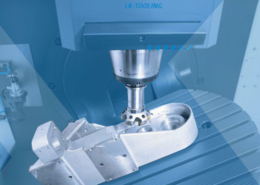