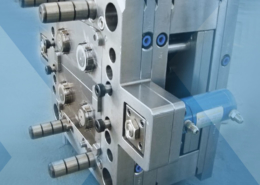
KraussMaffei and NIAR Propel Injection Molded Thermoplastic Composites - pt inje
Author:gly Date: 2024-09-30
“It is part of Swansea University’s mission to support the community we work in, and the coronavirus has challenged us to deliver for the people of Swansea and Wales. Swansea University has always had close, collaborative links with our health boards and with industry, and this is precisely the time when those networks come into their own”.
“I am immensely proud of the incredible hard work and effort everyone has put into this project, working evenings and weekends to make this happen. The team is made up of postgraduate students, undergraduate students, Engineering and Medicine staff, and key industry contacts.
SPT Vilecon said it has begun expanding the range of injection mold prototyping with silicone, metal, and ceramic materials to provide medical device manufacturers with an even wider selection of product development and verification services.
A supplier of development and manufacturing services to medical device OEMs used Freeform Injection Molding from Nexa3D to accelerate time-to-market and slash prototyping costs for a complex silicone-based IV device. SPT Vilecon explained the process in a recent press release.
Editor in chief of PlasticsToday since 2015, Norbert Sparrow has more than 30 years of editorial experience in business-to-business media. He studied journalism at the Centre Universitaire d'Etudes du Journalisme in Strasbourg, France, where he earned a master's degree.
“The call for a design team to take on the challenge was met with enthusiasm, speed, and professionalism by all involved. We are looking to help encourage the transfer of manufacturing medical equipment and PPE back to Welsh industry, so that these shortages are less likely in the future.”
Based on input collected from the first two iterations, the design of the silicone part was approved and manufacturing of a metal tool was initiated with full confidence of part moldability and performance. The in-house tool shop built the final metal tooling in four weeks without iterations.
Robust and valid prototyping and verification are key to minimizing cost, time, and risk factors in developing medical devices, said SPI Vilecon. FIM is a new toolbox for medical device companies seeking to accelerate their innovation and obtain early verification of part performance and moldability, added the company.
“These visors are comfortable to wear, give good visibility and feel sturdier and more robust than some other visors that have been supplied. Staff report feeling safe wearing them, appreciate the adjustable headband and have selected these as their visor of choice.”
Face shields to protect NHS staff, designed and 3D printed by a Swansea University team, have been awarded the CE safety mark, which means they can now be manufactured at larger scale for hospitals.
Design input collected from the first tests was integrated in a second iteration that took only a couple of hours to complete. By contrast, conventional metal tooling would have taken more than six weeks to design and procure, and the adjustments needed for the second iteration would have taken an in-house tool-shop a week to complete.
The 3D-printed molds for the first and second iterations cost less than €2,000 combined. And the technology enabled a two-day design cycle, which is more than 90% faster than conventional metal tooling.
SPT implemented Nexa3D’s Freeform Injection Molding (FIM) technology to help customers shorten time-to-market on complex medical devices in demanding medical-grade materials and to expand on the range of materials that can be quickly and reliably used in prototyping and early device test manufacturing.
Freeform Injection Molding technology from Nexa3D compresses design, iteration, and validation cycle times into a matter of hours rather than weeks.
After working around the clock, they set-up and manufactured an open-source Prusa design in the College of Engineering, with the addition of neoprene foam and a wide elastic strap for increased comfort. The design was then improved to increase eye coverage and in preparation for mass production.
Certified to ISO 13485, Denmark-based SPT Vilecon describes itself as a fully integrated provider of development and manufacturing services to the medical device industry. It offers in-house tool making and injection molding along with other manufacturing services to companies in northern Europe.
Medical device manufacturers are tasked with developing elaborate test protocols to ensure that the product in development is safe and meets essential requirements. If these tests are conducted late in the development process, the more onerous and risky they become. SPT Vilecon often works with silicone, a material that is extensively used in medical applications because of its chemical resistance, mechanical performance, and biocompatibility. However, silicone parts are notoriously difficult to prototype and test, since most grades need to be injection molded to achieve their full performance potential, said the company. FIM enabled SPT Vilecon to offer an alternative to a customer developing an intravenous (IV) silicone product — the use of 3D-printed tooling to perform early design and material verification at a fraction of the cost of conventional methods.
Injection-molded silicone parts were produced within two days, allowing early verification of key design and performance aspects.
“My wife is an intensive care consultant in the Royal Glamorgan Hospital, and we have many family and friends who work in a range of healthcare roles, putting themselves at risk.
Knowing that their expertise could help support the NHS, staff and students in Swansea University’s College of Engineering, supported by ASTUTE 2020 from the Future Manufacturing Research Institute, the Accelerate Healthcare Technology Centre, which are both co-funded by the European Regional Development Fund, through the Welsh Government, and the Welsh Centre for Printing and Coating, began researching designs and specifications for 3D printing protective face visors.
Now the visors have obtained the CE mark. CE is an abbreviation of "Conformité Européenne”, which indicates that a product meets mandatory EU regulations for safety.
Engineering Doctorate researcher David O’Connor, who also played a leading role, and is based in the Welsh Centre for Printing and Coating and the Future Manufacturing Research Institute at Swansea University, added:
The patented FIM process uses high-speed Nexa3D printers and xMOLD resin to print injection molding tools that are compatible with thousands of off-the-shelf injection molding materials, including reinforced high-performance feedstocks. The process reduces design, iteration, and validation cycles using end-product materials to a matter of hours rather than weeks.
After being quarantined for 72 hours, the visors were sent out to local hospitals for testing and feedback, which the team used to improve the design further.
The CE mark gives the team the green light to produce the masks using 3D printing. In future it is hoped the masks can be mass produced using injection moulding rather than 3D printing, thanks to local industrial partners FSG Tool, Die Ltd and Knight Plastics.
“These products are going to protect healthcare staff on the front line so it was essential that we developed them to a point where they meet the appropriate standards.
GETTING A QUOTE WITH LK-MOULD IS FREE AND SIMPLE.
FIND MORE OF OUR SERVICES:
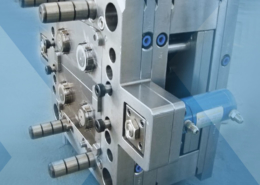
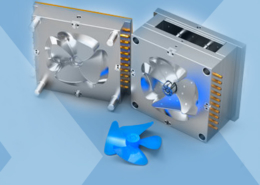
Plastic Molding

Rapid Prototyping
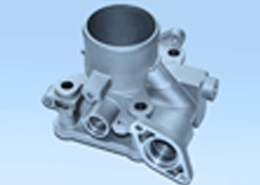
Pressure Die Casting
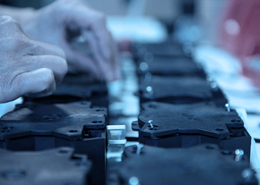
Parts Assembly
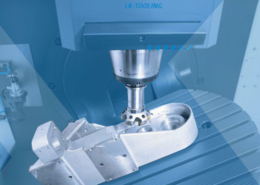