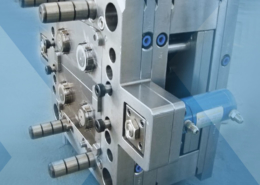
Exploring the Innovation of Two-Shot Molding
Author:gly Date: 2024-06-08
Two-shot molding is a groundbreaking manufacturing process that has revolutionized the production of intricate and multi-material components. This technique allows for the creation of complex parts by injecting two different materials into a single mold, sequentially or simultaneously. Its versatility and efficiency make it a preferred method in various industries, from automotive to consumer electronics. This article aims to delve into the intricacies of two-shot molding, exploring its mechanisms, applications, advantages, challenges, and future prospects.
Mechanisms and Process
Two-shot molding involves injecting two different materials into a single mold to produce a component with two or more colors, materials, or layers. The process typically consists of several steps: mold preparation, material injection, and part ejection. During mold preparation, the mold is designed with multiple cavities to accommodate the different materials. The first material is injected into the mold, followed by the second material after the first shot solidifies partially. This sequential or simultaneous injection ensures proper bonding between the materials, resulting in a cohesive final product.
Applications Across Industries
The versatility of two-shot molding makes it suitable for a wide range of applications across various industries. In the automotive sector, it is used to produce interior trim components, such as instrument panels and door handles, with a combination of rigid and soft materials for enhanced aesthetics and functionality. In the medical field, two-shot molding is employed to manufacture devices with antimicrobial coatings or soft-touch grips for improved patient experience and safety. Additionally, in consumer electronics, it enables the production of products with integrated buttons, seals, or gaskets, enhancing both design and functionality.
Advantages and Benefits
Two-shot molding offers several advantages over traditional manufacturing methods. Firstly, it allows for the creation of complex geometries and multi-material components in a single operation, reducing assembly time and costs. Secondly, it improves part quality by eliminating the need for secondary operations such as bonding or welding, resulting in stronger and more durable products. Furthermore, it enhances design flexibility, enabling designers to incorporate various colors, textures, and materials into their products without compromising performance or functionality.
Challenges and Considerations
Despite its numerous benefits, two-shot molding presents some challenges and considerations. One significant challenge is material compatibility, as different materials may have varying shrinkage rates, melt temperatures, or adhesion properties, affecting part quality and performance. Moreover, tooling complexity and maintenance can be demanding, requiring precise alignment and control to ensure accurate material distribution and bonding. Additionally, optimizing process parameters such as injection pressure, temperature, and cooling time is crucial to achieving consistent results and minimizing defects.
Conclusion
In conclusion, two-shot molding is a highly versatile and efficient manufacturing process that offers numerous benefits across various industries. Its ability to produce complex, multi-material components in a single operation has transformed the way products are designed and manufactured. However, addressing challenges such as material compatibility and tooling complexity is essential to fully harnessing its potential. As technology advances and materials science continues to evolve, the future of two-shot molding holds promising opportunities for innovation and growth. By embracing this advanced manufacturing technique, companies can stay competitive in an increasingly demanding market landscape and deliver high-quality products that meet the evolving needs of consumers.
GETTING A QUOTE WITH LK-MOULD IS FREE AND SIMPLE.
FIND MORE OF OUR SERVICES:
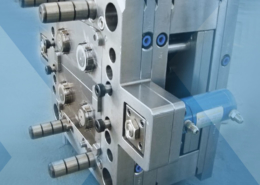
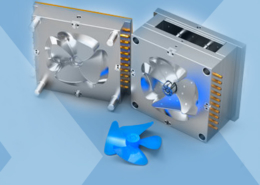
Plastic Molding

Rapid Prototyping
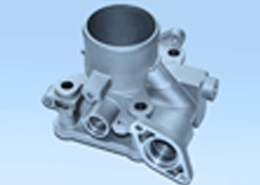
Pressure Die Casting
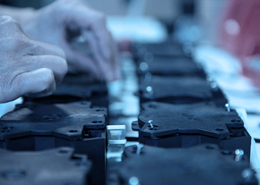
Parts Assembly
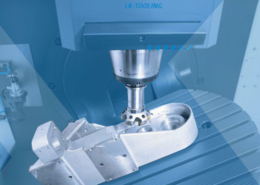