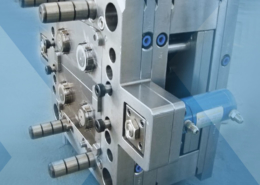
Kingfa Expanding in Step with New Energy Vehicle Growth in China - ppsu injectio
Author:gly Date: 2024-09-30
“It’s all too easy to blow the mould and damage the parting faces. But VISI Flow shows us all potential manufacturing issues such as welding lines, air traps and the best gate location, before the mould is trialled.”
In the future, it is also conceivable that process, quality, and patient data for each individual part will be 100% traceable via an RFID code.
VISI helps Formaplex create bespoke fixtures for their inspection process, ensuring absolute accuracy and repeatable tolerances
“Aluminium moulds, in particular, can be damaged if filled from the wrong position, in the wrong sequence or by excessive pressure with inadequate clamp tonnage,” he explains.
Summing up the company’s overall experience of using VISI, Adrian Chapman says: “It provides us with key information at the design stage and it supports the complete mould process, which ultimately ensures total end product satisfaction.”
Once the mould tool is complete, it undergoes a maturation procedure – a series of process trials that monitor and review the continuous improvement of the product until the component is ultimately accepted.
A crucial part of the Formaplex business is its Specialist Engineering division, which supports the Metrology Department. Here, moulded components are accurately inspected and measured with the latest CMM technology.
“The CAD data can come from our customers in a range of formats, but VISI handles it all seamlessly, which is a great advantage for our speed and efficiency of design.”
VISI plays a key role in this process, too, according to Keates, by ensuring absolute accuracy and repeatable tolerances. He says his team designs the fixture by importing the native CAD model into VISI and creating the fixture around the critical points of the component.
Specialist engineering manager Grant Keates (left) discusses a finer point of an automotive fixture with technical director Adrian Chapman
Formaplex designs and manufactures bespoke fixtures for the inspection process, under the guidance of specialist engineering manager Grant Keates.
With VISI, Chapman and his team can simulate the mould kinematics and correct any issues before they start cutting expensive metal.
The simulation then provides the ability to forecast and visualise how a component will be filled by the plastic melt front, making it possible to identify any potential aesthetic issues.
In order to ensure the long-lasting integrity of the company’s mould tools, Formplex relies on VISI Flow from Vero Software.
The next step is to send the finished CAD data of the fixture to the shop floor, where VISI Machining’s dedicated high-speed milling techniques and built-in smoothing algorithms create intelligent 3- and 5-axis toolpaths for the company’s Doosan and Kondia CNC machines.
With operations spread across 150,000 square feet in three state-of-the-art sites in Hampshire, UK, and a new 120,000 purpose built site set to come online in 2016, Formaplex can boast an impressively wide range of business activities.
All that calls for a wide armoury of tools. The company has over 40 CNC machines, both 3- and 5-axis, offering a range of machining envelopes up to 8m x 6.2m x 2m, to suit a wide variety of design projects. Its capabilities are further supported by 11 injection mould presses, from 55 tonnes to 3,500 tonnes.
The IML print-to-cut distance is only around 0.08 in. (0.2 mm) for the centrifuge tube application. With a wall thickness of only 57 micrometers, the labels must be precisely positioned in the mold cavities, and equally precisely aligned and applied. A label adjustment head equalizes the manufacturing tolerance to a few hundredths, which is an important requirement for functionality and significantly reduces quality fluctuations and rejects.
IML is standard for packaging products, but the process is rarely used in medical manufacturing, said Arburg in its announcment. The concept is all the more compelling because both the tube and label are made of polypropylene, thus promoting sustainability and adding value for customers in the pharmaceutical and medical sectors.
“We use the part splitting tools to create parting faces, enabling us to quickly design the main core and cavity block. Once we have those finalised, we model the sliders, lifters and any other small components – whether they’re automatic or manual – and incorporate them into the mould tool.
A temperature-sensitive element can be included that monitors interruptions in the cold chain. If the temperature of the filled tube exceeds 7°C, for example, the thermo-chromic printing ink irreversibly changes in appearance.
The injection simulation capabilities provided by the package, says Chapman, help the company to achieve cost-effective and reliable designs and optimum moulding conditions, such as well-balanced runners with symmetrical filling patterns, for example.
The Specialist Engineering division at Formaplex is keen to embrace new technology and is investing heavily year on year. It is now able to offer sheet metal fabrication, too, encompassing a wide range of steels, as well as more exotic metals such as titanium.
In addition to facilitating recycling, the mono-material construction and integrated processing of the tube and label contribute to the stability of the tube, enabling a reduction in wall thickness, if needed. The process also eliminates secondary operations, such as bonding and printing. No adhesives are required and there is no waste caused by contamination with liquid color.
Initial studies of moulded features and draft check analysis tell Chapman all he needs to know to complete his initial Design for Manufacturability (DFM) work. He then carries out initial fill studies, where VISI provides the same level of control over injecting molten polymer into the mould cavity as is available on the moulding machine itself.
“It gives a very clear indication of all areas where problems could arise. We can give our customers full and accurate information regarding the development of their mould tools. Without it, our dynamic approach and customer service would definitely be hindered.”
Editor in chief of PlasticsToday since 2015, Norbert Sparrow has more than 30 years of editorial experience in business-to-business media. He studied journalism at the Centre Universitaire d'Etudes du Journalisme in Strasbourg, France, where he earned a master's degree.
The company designs and manufactures aluminium and steel injection mould tools for the automotive, motorsports and aerospace industries. It produces low volume finished moulded components, from brackets and fixings to bumper assemblies and instrument panels. And it also supplies composite tooling and components and carries out specialist machining and finishing projects, component painting, flocking and assembly.
The electric Allrounder 520 A "Ultimate" is designed for ISO Class 7 cleanroom use and has a clamping force of 165 tons (1,500 kN). The ready-to-use 15-ml PP tubes are produced in an eight-cavity mold from Kebo at an approximate 10-second cycle time. Servo-electric drives ensure precise and reproducible mold positioning in the press, and a label adjustment head from Beck ensures that the labels are precisely aligned and applied. An integrated camera system from Intravis visually inspects the finished parts in real time. In a real application, the tubes could also be screwed together and packaged in tubular bags in the production cell, added Arburg.
NPE2024 visitors can see the system in operation at booth W3743. The event returns to the Orange County Convention Center in Orlando, FL, on May 6 to 10.
“We don’t have any real challenges or issues with designing and manufacturing our jigs and fixtures, because VISI helps us achieve everything we need to.”
“A conservative estimate is that, within the first month of using VISI Flow to analyse the correct filling pattern and maximise our process parameters, we saved the cost of the software by avoiding downtime, repairs, wasted toolmaking and setting time and reduced material costs.”VISI Flow mould injection simulation software pays dividends for FormaplexDefault
A scale on the scratch-resistant label indicates the exact fill level, which can be relevant for insulin pen and medical measuring cup applications, for example.
Formaplex technical director Adrian Chapman says the company’s strengths lie in being able to provide full design support and advice for tools, covering areas as diverse as plastic flow analysis, logistics project management, production, measurement, tool testing, design and manufacture.
A medical in-mold labeling (IML) application will be showcased by Arburg at NPE2024. First presented at Fakuma in 2023 as a proof of concept, the compact turnkey production cell anchored by Arburg’s electric Allrounder 520 A "Ultimate" press will produce a centrifuge tube with label on the NPE show floor.
“We can quickly analyse where the pressure will be too high, whether the material will freeze too quickly, if we need to have more than one gate and whether they’re in the right place,” he continues. “Once we’ve analysed and understood exactly what we need to do, we can advise the customer on necessary changes such as part-thickness modification, changing the material or re-engineering.”
“With VISI, I can quickly analyse the customer CAD data to verify moulding feasibility by checking for draft conditions and undercut features; then VISI Flow shows the capability of successfully moulding the required plastic part,” he says.
VISI Flow provides a number of analytical tools that allow the investigation of moulding variables such as pressure, temperature, shear stress, frozen skin, fibre orientation, clamping force and others.
Moldmaker Kebo, in-mold labeling specialist MCC Verstraete, automation developer Beck, and vision system supplier Intravis contributed to the joint IML project.
GETTING A QUOTE WITH LK-MOULD IS FREE AND SIMPLE.
FIND MORE OF OUR SERVICES:
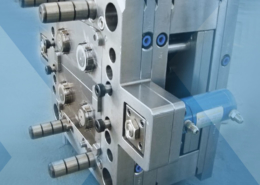
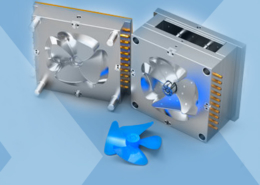
Plastic Molding

Rapid Prototyping
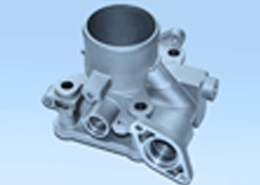
Pressure Die Casting
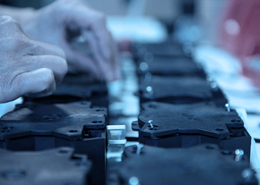
Parts Assembly
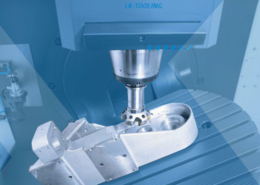