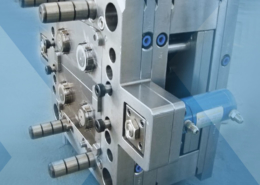
IPL Plastics introduces new food containers - plastic bucket mould
Author:gly Date: 2024-09-30
Join Engel in exploring the future of battery molding technology. Discover advancements in thermoplastic composites for battery housings, innovative automation solutions and the latest in large-tonnage equipment designed for e-mobility — all with a focus on cost-efficient solutions. Agenda: Learn about cutting-edge thermoplastic composites for durable, sustainable and cost-efficient battery housings Explore advanced automation concepts for efficient and scalable production See the latest large-tonnage equipment and technology innovations for e-mobility solutions
Across all process types, sustainability was a big theme at NPE2024. But there was plenty to see in automation and artificial intelligence as well.
This high-fiber, MIC, injection molded, Class A console hinge bracket features more sustainable basalt rather than E-glass fiber reinforcement. No reduction in performance or durability was seen in these color-matched 50% basalt/PA6 parts, but the switch addressed fiberglass shortages, reduced costs and improved CO2 footprint.
Sustainability continues to dominate new additives technology, but upping performance is also evident. Most of the new additives have been targeted to commodity resins and particularly polyolefins.
technotrans says climate protection, energy efficiency and customization will be key discussion topics at PTXPO as it displays its protemp flow 6 ultrasonic eco and the teco cs 90t 9.1 TCUs.
Say “manufacturing automation” and thoughts immediately go to the shop floor and specialized production equipment, robotics and material handling systems. But there is another realm of possible automation — the front office.
Additive technology creates air pockets in film during orientation, cutting down on the amount of resin needed while boosting opacity, mechanical properties and recyclability.
Allegheny Performance Plastics specializes in molding parts from high-temperature resins for demanding applications as part of its mission to take on jobs ‘no one else does.’
Introduced by Zeiger and Spark Industries at the PTXPO, the nozzle is designed for maximum heat transfer and uniformity with a continuous taper for self cleaning.
Core Technology Molding turned to Mold-Masters E-Multi auxiliary injection unit to help it win a job and dramatically change its process.
The swappable battery cell holder meets stringent regulatory standards and requirements. It features an injection molded long fiber thermoplastic (LFT) polypropylene (PP) with an intumescent, halogen-free, flame-retardant package selected for safety, mechanical performance and compliance with environmental regulations.
Plastics Technology’s Tech Days is back! Every Tuesday in October, a series of five online presentations will be given by industry supplier around the following topics: Injection Molding — New Technologies, Efficiencies Film Extrusion — New Technologies, Efficiencies Upstream/Downstream Operations Injection Molding — Sustainability Extrusion — Compounding Coming out of NPE2024, PT identified a variety of topics, technologies and trends that are driving and shaping the evolution of plastic products manufacturing — from recycling/recyclability and energy optimization to AI-based process control and automation implementation. PT Tech Days is designed to provide a robust, curated, accessible platform through which plastics professionals can explore these trends, have direct access to subject-matter experts and develop strategies for applying solutions in their operations.
Before the official market launch, the new solution had already won two internationally renowned awards. For example, the Smart Pallet Mover won the Red Dot Award, Product Design 2021, for its exceptional design quality and degree of innovation. At the same time, the solution was chosen by the independent experts of the International Intralogistics and Forklift Truck of the Year Award (Ifoy Award) in March 2021 as a finalist of this globally renowned intralogistics award.
In a time where sustainability is no longer just a buzzword, the food and beverage packaging industry is required to be at the forefront of this innovation. By adopting circular packaging processes and solutions, producers can meet regulatory requirements while also satisfying consumer demand and enhancing brand reputation. Join Husky to learn more about the broader implications of the circular economy — as well as how leading brands are leveraging this opportunity to reduce costs, increase design flexibility and boost product differentiation. Agenda: The cost and operational benefits of embracing circularity Key materials in circular packaging — including rPET and emerging bioplastics How to design a circular food and beverage package Strategies for selecting sustainable closures to future-proof packaging solutions Optimization and streamlining of production processes for enhanced efficiency How Husky Technologies can enable your sustainable success
Join this webinar to explore the transformative benefits of retrofitting your existing injection molding machines (IMMs). Engel will guide you through upgrading your equipment to enhance monitoring, control and adaptability — all while integrating digital technologies. You'll learn about the latest trends in IMM retrofitting (including Euromap interfaces and plasticizing retrofits) and discover how to future-proof your machines for a competitive edge. With insights from industry experts, it'll walk you through the decision-making process, ensuring you make informed choices that drive your business forward. Agenda: Maximize the value of your current IMMs through strategic retrofitting Learn how to integrate digital technologies to enhance monitoring and control Explore the benefits of Euromap interfaces and plasticizing retrofits Understand how retrofitting can help meet new product demands and improve adaptability Discover how Engel can support your retrofitting needs, from free consultations to execution
Join Wittmann for an engaging webinar on the transformative impact of manufacturing execution systems (MES) in the plastic injection molding industry. Discover how MES enhances production efficiency, quality control and real-time monitoring while also reducing downtime. It will explore the integration of MES with existing systems, emphasizing compliance and traceability for automotive and medical sectors. Learn about the latest advancements in IoT and AI technologies and how they drive innovation and continuous improvement in MES. Agenda: Overview of MES benefits What is MES? Definition, role and brief history Historical perspective and evolution Longevity and analytics Connectivity: importance, standards and integration Advantages of MES: efficiency, real-time data, traceability and cost savings Emerging technologies: IoT and AI in MES
Up to a 25% weight reduction with no loss of stiffness and 25% CO2 reduction were achieved in this MIC, Class A TPO door panel (carrier + map pocket) by combining core-back molding and chemical foaming in a multicavity tool with significant volumetric differences between cavities. A key enabler was use of a proprietary pressure regulation system with in-mold sensors, a TPO material specially developed for core-back/foaming and a chemical foaming technology that achieved uniform and well-defined cell structure in both parts.
Mold maintenance is critical, and with this collection of content we’ve bundled some of the very best advice we’ve published on repairing, maintaining, evaluating and even hanging molds on injection molding machines.
While the major correction in PP prices was finally underway, generally stable pricing was anticipated for the other four commodity resins.
This portal is a brand of Vogel Communications Group. You will find our complete range of products and services on www.vogel.com
Gifted with extraordinary technical know how and an authoritative yet plain English writing style, in this collection of articles Fattori offers his insights on a variety of molding-related topics that are bound to make your days on the production floor go a little bit better.
When, how, what and why to automate — leading robotics suppliers and forward-thinking moldmakers will share their insights on automating manufacturing at collocated event.
Resin drying is a crucial, but often-misunderstood area. This collection includes details on why and what you need to dry, how to specify a dryer, and best practices.
A formulated flexible and intumescent PVC is designed to prevent arcing during thermal runaway events in high-voltage EV batteries. The high-temperature, high-voltage insulator is used to injection mold various terminal caps and barriers. Safety is increased during thermal runaway since the material maintains high dielectric strength, reducing arcing risk and ignition of gases, and forms a structured char barrier, helping reduce spread of fire from one module to another.
Replacing magnesium with unsaturated polyester BMC yielded structural brackets meeting high dimensional requirements at comparable or improved mechanical performance — especially toughness. The bracket was made more sustainable with inclusion of 6% PIR PMMA and 5% PIR BMC scrap, which replaced calcium carbonate filler. It took 2 years of work to develop the process to recover and reclaim thermoset BMC scrap and reuse it in new parts with a lower CO2 footprint. Key to the success of the program were grinding, sizing and formulation strategies. No tooling changes were required versus virgin BMC.
This is reported to be the first broad-scale shift from virgin to PIR PA66 in cable management parts, a drop-in-change offering comparable performance, aesthetics and processing at lower cost and 35% lower carbon footprint without any part design or tooling changes. Although the parts are small, they are produced in high-cavitation injection tooling and offer best-in-class mechanical, thermal and chemical performance. In just the first year, the change removed 138,000 kilograms of CO2 and saved 70,000 kilograms of coal and 144 billion barrels of crude oil from being used.
This patented interconnect board (ICB) design supports, cools and isolates cell tabs/busbars, provides support and structure to the module between the top cover and cold plates and aids assembly by guiding, supporting and constraining cell tabs. The overmolded busbar design, which reduces copper use by approximately 25%, enables cooling through the frames from the cold plate. Honeycomb and rib features on the back reduce mass, increase clearance to cells, improving structure, especially during critical manufacturing processes, and contribute to finger-proofing requirements. Additionally, the hinged ICB ships flat, reducing shipping space by 78%, then folds for assembly.
Discover how artifical intelligence is revolutionizing plastics processing. Hear from industry experts on the future impact of AI on your operations and envision a fully interconnected plant.
The Smart Pallet Mover solution consists of various modules. The center of the solution is a mobile unit (SM1000 Mover) that runs underneath non-driven conveyor sections and moves pallets lying on them. A transfer car (SM2000 Transfer Car) which moves on a rail can transport pallets between parallel conveyor sections.
This high-gloss, MIC PC block copolymer with self-healing capabilities offers better UV stability, scratch resistance and thermal performance than painted ABS or PC/ABS, while reducing cost significantly owing to elimination of paint. No tooling changes were required, the CO2 footprint was reduced, parts are now recyclable at end of life (owing to elimination of paint) and multiple color options are available.
A novel hybrid pultrusion process can cost-effectively produce up to 20 million load-bearing and E-coat-capable structural composite beams annually thanks to a fully automated process. Beams provide the primary load path to pass IIHS side and pole impact tests, protecting occupants and on onboard battery packs while achieving a 30% increase in impact resistance versus roll-formed steel. An injection box added to the pultrusion line infuses high-performance epoxy into unidirectional carbon fiber and woven fiberglass reinforcement, reducing mass/vehicle by 12 kilograms and tool cost by 30% versus metallic benchmarks. Beams are attached to the body-in-white (BIW) via structural adhesives and blind rivets.
Imprint Cookie-Manager About Media Subscription cancellation Privacy General Terms and Conditions Help AI-Guidelines
Plastics Technology covers technical and business Information for Plastics Processors in Injection Molding, Extrusion, Blow Molding, Plastic Additives, Compounding, Plastic Materials, and Resin Pricing. About Us
Finalists display a variety of plastics and composites innovations. Winners will be announced Nov. 8, 2023, during the 52nd SPE Automotive Innovation Awards Gala.
Learn about sustainable scrap reprocessing—this resource offers a deep dive into everything from granulator types and options, to service tips, videos and technical articles.
Tight packaging space and the space for an HVAC outlet in the console meant a traditional through-pin-type hinge could not be used on the armrest to keep it latched during a crash. A friction hinge with inertial lock — previously only used in the furniture industry — solved the problem, but required unique tooling innovation to be feasible. The triple-action, two-stage slide featuring a horn-pin driven slide with collapsible lifters on top of a hydraulic main bottom slide was developed, enabling direct edge gating on top of the slide to optimize filling conditions.
This is reported to be the world’s first all-thermoplastic split gate rear-closure system, which is delivered to the assembly line as a ready-to-install module. The complex, deep draw (>80 millimeter) design offers improved perceived quality at lower mass, NVH and cost versus metals, and is offered in a two-tone execution. By commonizing grades between the liftgate and the benchgate and focusing on sustainability, parts were reduced from nine to three, and only two materials are used (injection molded LFT-PP and thermoplastic olefin/TPO). The CHMSL and tail lamps were carried over from the pickup model.
Moving from drilled metal to molded plastic tubes on spray bars can reduce mass and cost and reduce contamination concerns involving the presence of metal shavings from drilling operations. To create an enclosed structure with the holes needed to spray fluid via injection molding, parts must be molded in two complex, contoured halves and joined. The cleanest joining process proved to be laser welding. The high-flow, heat-stabilized PA6/6 grade was selected for its high thermal resistance, low contamination, consistent quality and resistance to automatic transmission fluid.
The Smart Pallet Mover is a pallet management solution for automating pallet transport in the vicinity of manufacturing machines and for production-related picking and sequencing processes, which can also be used in Industry 4.0 environments. The SPM is designed to transport, sort and buffer boxes or pallets weighing up to 1000 kilograms. It represents a mobile and autonomously acting material flow system that can be used, for example, as a cost-efficient supplement or substitute for forklifts or automated guided vehicles (AGVs).
Two BDUs have been integrated into a single system supporting two 400-volt systems, which enable fast and safe recharging of electric vehicles (EVs) and disconnects power in an over-current situation to protect passengers. The meter-long parts feature a complex design that offers improved thermal management and reduced component mass. Two UL94 V0 halogen-free materials — one with very high CTI — replaced die-cast aluminum while maintaining improved physical properties and ease of processing. Complex simulation and process optimization were also key to success.
After successfully introducing a combined conference for moldmakers and injection molders in 2022, Plastics Technology and MoldMaking Technology are once again joining forces for a tooling/molding two-for-one.
The Plastics Industry Association (PLASTICS) has released final figures for NPE2024: The Plastics Show (May 6-10; Orlando) that officially make it the largest ever NPE in several key metrics.
With the new Smart Pallet Mover, Interroll has launched a awarded solution that can be adapted as a flexible and modular pallet management system to meet a wide range of application requirements in industrial manufacturing.
In this three-part collection, veteran molder and moldmaker Jim Fattori brings to bear his 40+ years of on-the-job experience and provides molders his “from the trenches” perspective on on the why, where and how of venting injection molds. Take the trial-and-error out of the molding venting process.
Despite price increase nominations going into second quarter, it appeared there was potential for generally flat pricing with the exception of a major downward correction for PP.
Processors with sustainability goals or mandates have a number of ways to reach their goals. Biopolymers are among them.
This month’s resin pricing report includes PT’s quarterly check-in on select engineering resins, including nylon 6 and 66.
In this collection of articles, two of the industry’s foremost authorities on screw design — Jim Frankand and Mark Spalding — offer their sage advice on screw design...what works, what doesn’t, and what to look for when things start going wrong.
Take a deep dive into all of the various aspects of part quoting to ensure you’ve got all the bases—as in costs—covered before preparing your customer’s quote for services.
This interior trim lighting system is hidden until lit, yet provides these backlit wrapped interior parts with the feel of leather and vibrant special lighting effects in a limited design space. Key to the execution is a transluscent TPO extrusion molding process and a precise ink coating layer between surface and translucent 3D mesh backing fabric. Light transmission and emitted colors are controlled by colorant concentration. Versus TPE injection molding and PVC with punched holes filled with adhesive, cost and weight are reduced while recyclability is improved versus PVC.
Across the show, sustainability ruled in new materials technology, from polyolefins and engineering resins to biobased materials.
By replacing E-glass with basalt fiber in this injection molded ADAS bracket, which also contained 60% PIR PA6, cost and weight were neutral, the part met all performance requirements, no tooling changes were needed, but a CO2 reduction of 74% was achieved and 180,000 kilograms of material annually is kept from landfills. The drop-in change is more sustainable, addresses issues with glass shortage and provides the same performance as virgin material.
Key to the crisp and uniformly lit appearance of these animated taillamps are micro-optical features on injection molded light guides produced via a specialized manufacturing technique. Using an algorithm, the process starts by generating a pseudo-randomized topology that is machined into a master that is then used to create an electroform nickel insert. The technology produces a smooth appearance with far fewer LEDs, eliminates hot spots from point light sources and permits crisper animation in tighter packaging depths versus traditional approaches.
While prices moved up for three of the five commodity resins, there was potential for a flat trajectory for the rest of the third quarter.
By replacing metals with RTP 299 K X 138337 E Black Para material to injection mold the side plates for this battery module, extremely flat parts with high dimensional accuracy, stiffness and strength were achieved in a complex geometry. The high-modulus, creep-resistant FR polymer eliminated the need for compression limiters and electrical isolation films, yet withstood extreme pressures from cell expansion and met all mechanical requirements. Additionally, four components were reduced to one and many functional features were incorporated in the patented side plates that would not have been possible in metals. Mass was reduced by 37% and cost by 55%.
The patented hybrid battery interconnect board features small and delicate metal current collectors, bus bars and sensing lines in a compact design to fit in limited packaging space. The 20% glass fiber-reinforced PA6 grade was selected for its ability to offer high levels of functional integration in limited space plus be compatible with snap-fits, heat staking, ultrasonic welding and adhesive bonding. The material also is heat stabilized and flame retardant. Laminated core-block inserts are used in rotary injection tooling for venting and to control stampings during overmolding.
This patented injection molded module for seats incorporates both temporary and permanent holding features to control cables and dramatically reduce both components and labor at the seat manufacturer. Cables are delivered to the Tier 1 pre-routed on the module plate, eliminating the brackets, cable ties and clips typically used to control seat cables, and greatly reducing labor for an assembly operator. The module also reduces rework and scrap due to cable misalignments. Additionally, lever pull effort for consumers is reduced because direct cable routing enables use of shorter cables.
The Society of Plastics Engineers (SPE) Automotive Division (Troy, Mich., U.S.) has named the finalists for its 52nd annual Automotive Innovation Awards Gala. Nominations were first subjected to a pre-qualification review and then were presented before a panel of industry experts. That panel sent forward the most innovative nominations (category finalists) to the Blue Ribbon judging round. Category and Grand Award winners selected during the Blue Ribbon judging round will be announced on the evening of Nov. 8, 2023, during the 52nd SPE Automotive Innovation Awards Gala.
Owing to the vehicle’s shallow sloped windshield, it was necessary to modify the typical U or Y design on the PAB chute door and hinge design to facilitate proper airbag deployment and prevent inadvertent cracking of the windshield. A combination of injection molding, vibration welding, in-mold grain lamination and laser scoring are used to create a modified U/Y door/hinge design that opens as a U shape and then folds during windshield contact. After opening, momentum of the door is slowed via the hinge design.
Join KraussMaffei for an insightful webinar designed for industry professionals, engineers and anyone interested in the manufacturing processes of PVC pipes. This session will provide a comprehensive understanding of the technology behind the production of high-quality PVC pipes: from raw material preparation to final product testing. Agenda: Introduction to PVC extrusion: overview of the basic principles of PVC pipe extrusion — including the process of melting and shaping PVC resin into pipe forms Equipment and machinery: detailed explanation of the key equipment involved — such as extruders, dies and cooling systems — and their roles in the extrusion process Process parameters: insight into the critical process parameters like temperature, pressure and cooling rates that influence the quality and consistency of the final PVC pipes Energy efficiency: examination of ways to save material and energy use when extruding PVC pipe products
Multiple speakers at Molding 2023 will address the ways simulation can impact material substitution decisions, process profitability and simplification of mold design.
To meet application specifications and tight timing requirements, two different polymer additive manufacturing processes (MJF and SLA) and two different polymers (PA12 and epoxy) were combined to produce the compressor housing for this low-volume, autonomous vehicle. MJF offered high throughput and cost effectiveness for the bulk of the compressor housing while SLA offered higher dimensional tolerances and smoother surface finish on the connector, which facilitated passing USCAR push/pull requirements. By using each process’ strength and bonding parts together, cost and performance were optimized, tooling was eliminated and program delays were avoided.
This patented sealing system enables separation of the glass guidance rails/sliders from the weatherstrip/seal on framed doors, permitting improved aesthetics similar to frameless doors at lower mass, better noise/vibration/harshness (NVH), reduced complexity and faster assembly. The cost-neutral system also permits window regulators on framed doors and some competitive flush-glazing options to be converted from dual to single rails for both front and rear doors. A combination of injection molding and extrusion are used to produce the thermoplastic system, which maintains ±0.1 millimeter tolerances. Virtual validation technology was used to eliminate the need for physical prototypes.
Replacing aluminum with flexible rubber hose, an injected plastic fitting is laser welded to plastic tubing and assembled to an aluminum block with a steel plate for structural rigidity while permitting the current system interfaces to be used in limited packaging space. Mass was reduced by 30% and direct cost by 23% while improving the oil cooling circuit pressure drop by 51% versus benchmark technology. The neat, semi-flexible PA6/10 polymer contains 62% bio-based monomer and offers good cold-temperature impact, chemical resistance and short-term temperature peaks.
This Knowledge Center provides an overview of the considerations needed to understand the purchase, operation, and maintenance of a process cooling system.
Use of a 30% GR/PP material with intumescent fire-retardant (FR) package reduces weight 10% and cost 20% while improving fire safety versus FR 30% GR/PA6. This is also the first thermoplastic to pass China’s GB/T 41467.3-2015 fire safety regulation for EVs surviving 5 minutes at 1,000°C. Improved flow properties versus PA6 permitted higher cavitation tooling to be used, doubling productivity in the same cycle time, while also lowering molding temperatures for energy and CO2 improvements. Versus metals, mass reduction of 18 kilograms/vehicle is achieved. The design also features an integral overmolded busbar.
Since 1970, the SPE Automotive Innovation Awards Competition has highlighted the positive changes that polymeric materials have brought to automotive and ground transportation industries, such as weight and cost reduction, parts consolidation, increased safety, and improved aesthetics and design freedom. At the time the competition started, many OEM designers and engineers thought of plastics as inexpensive replacements for more “traditional” materials. To help communicate that plastics were capable of far more functionality than their typical use as decorative knobs and ashtrays indicated, members of the board of directors of SPE’s Automotive Division created the competition to recognize successful and innovative plastics applications and to communicate their benefits to OEMs, media and the public.
Mike Sepe has authored more than 25 ANTEC papers and more than 250 articles illustrating the importance of this interdisciplanary approach. In this collection, we present some of his best work during the years he has been contributing for Plastics Technology Magazine.
Formnext Chicago is an industrial additive manufacturing expo taking place April 8-10, 2025 at McCormick Place in Chicago, Illinois. Formnext Chicago is the second in a series of Formnext events in the U.S. being produced by Mesago Messe Frankfurt, AMT – The Association For Manufacturing Technology, and Gardner Business Media (our publisher).
In this collection, which is part one of a series representing some of John’s finest work, we present you with five articles that we think you will refer to time and again as you look to solve problems, cut cycle times and improve the quality of the parts you mold.
The Smart Pallet Mover is easy to install, operate and maintain. The modular plug-and-play solution can therefore be put into operation without lengthy interruptions to production, even during modernisation projects, the company claims. Networking capabilities based on global data standards such as Rest API and JSON ensure maximum compatibility and ease of use. The conveyor modules can be reconfigured very easily if required, and height-adjustable supports allow the system to be installed even on uneven floors.
This all-thermoplastic battery structure combines two side plates and 45 repeating spacers bolted together to hold pouch-style batteries. The patented, volumetrically efficient design withstands high cell expansion forces during battery use while eliminating the need for 55 compression limiters plus isolation countermeasures necessary with metals. Side plates are injection molded with 50% GR/Para while spacers are injection molded with 45% GR/PPA. Both materials required high molding precision, dimensional accuracy, flame retardance and the ability to integrate a variety of functional features that facilitate assembly. Versus aluminum, both mass and cost are reduced.
Ultradent's entry of its Umbrella cheek retractor took home the awards for Technical Sophistication and Achievement in Economics and Efficiency at PTXPO.
This is the first time a 20% PCR recycled material has been used in a color-matched, MIC, Class A structural funk application. Versus virgin TPO, the more sustainable grade lowered density slightly and offered better impact at -15°C. Concurrent redesign reduced component count from six to one, including eliminating two metal brackets, saving 3 kilograms of mass, increasing cargo volume and functionality, improving water management, reducing cost and labor and saving an estimated 1,125 tons of CO2 annually. PCR content is sourced from yogurt cups and packaging materials.
To increase safety and prevent accidental contact with high-voltage connections during assembly and service, and to reduce warpage that could cause manufacturing concerns, the component was redesigned to include alternating coring patterns along the top and bottom surfaces, which reduced warpage by 81%. The component also features slots to permit use of forward-looking infrared (FLIR) cameras to view busbar connections below the component surface. The FR UL94 V0 material is supplied in safety orange.
While the melting process does not provide perfect mixing, this study shows that mixing is indeed initiated during melting.
By converting from compression molded painted sheet molding compound (SMC) to injection molded MIC LFT-PP to produce this large Class A composite frunk — currently the industry’s largest — mass was reduced 48%, productivity was increased owing to a 37% cycle time reduction, the cost and environmental burden of paint were eliminated, seal interfaces were improved, secondary routering of holes is no longer needed and the frunk is fully recyclable at end of life. A 4,000-ton injection press and a tool equipped with a 16-drop hot runner system are used to mold parts.
During its Mobility Days in Austria, Engel and KTM Technologies debuted an all-plastic molded motorcycle seat base produced via a tape-sandwich process that can run in a standard molding process.
In this collection of content, we provide expert advice on welding from some of the leading authorities in the field, with tips on such matters as controls, as well as insights on how to solve common problems in welding.
Kevin Pageau, owner and president of International Marketing Alliance, and a major contributor to the SPE Automotive Division Lifetime Awards Program, will be honored at the awards gala on Nov. 8.
The aim of this presentation is to guide you through the factors and the numbers that will help you determine if a robot is a smart investment for your application. Agenda: Why are you considering automation? What problems are you trying to solve? How and why automation can help Crunch the numbers and determine the ROI
While prices moved up for three of the five commodity resins, there was potential for a flat trajectory for the rest of the third quarter.
Second quarter started with price hikes in PE and the four volume engineering resins, but relatively stable pricing was largely expected by the quarter’s end.
Successfully starting or restarting an injection molding machine is less about ticking boxes on a rote checklist and more about individually assessing each processing scenario and its unique variables.
Mixed in among thought leaders from leading suppliers to injection molders and mold makers at the 2023 Molding and MoldMaking conferences will be molders and toolmakers themselves.
Exhibitors and presenters at the plastics show emphasized 3D printing as a complement and aid to more traditional production processes.
It is not the performance of modern production machines but their material supply that promises the greatest potential for further productivity increases in industrial companies today. Interroll supports these efforts with their new Smart Pallet Mover (SPM). Those who use it can now automate work processes in front of the machine production to avoid manual activities in safety-critical areas and manage the pallet work flow by buffering, sorting, sequencing and carrying at the right time to deliver significant improvement of the machine down time optimizing the return on investment (ROI) of the machine production cells. This not only eliminates costly production interruptions for material supply to machines, but also the risk of accidents during operation. In this way, productivity increases of up to 30 percent are possible compared to manual operation.
August 29-30 in Minneapolis all things injection molding and moldmaking will be happening at the Hyatt Regency — check out who’s speaking on what topics today.
Thousands of people visit our Supplier Guide every day to source equipment and materials. Get in front of them with a free company profile.
GETTING A QUOTE WITH LK-MOULD IS FREE AND SIMPLE.
FIND MORE OF OUR SERVICES:
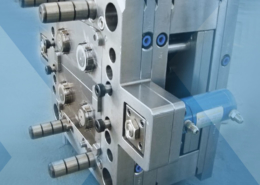
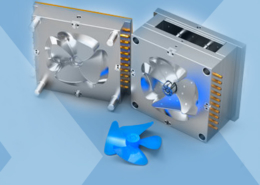
Plastic Molding

Rapid Prototyping
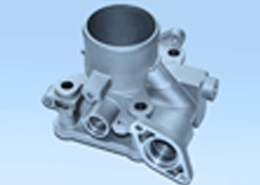
Pressure Die Casting
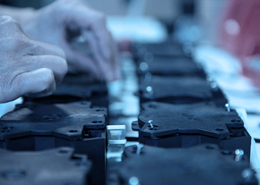
Parts Assembly
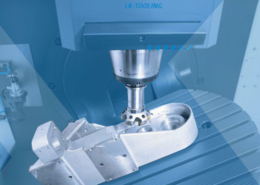