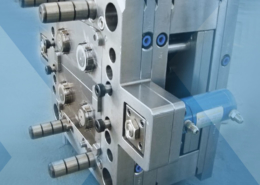
IPEX Opens Injection Molding Facility in North Carolina - plastic molding electr
Author:gly Date: 2024-09-30
"Our services accompany the customer from the design to the manufacturing process in the sense of integral planning with the aim of placing the product on the market in the best possible way."
Additionally, Baerlocher’s upstream collaboration with polymer company ExxonMobil Chemical supports the company’s efforts to create virgin polyethylene (PE) resins that are easier to recycle. Baerlocher’s RST solution, along with ExxonMobil Chemical’s modification of the resin architecture, helped to successfully develop these novel recycle-ready resins.
“Brand owners are increasing their use of PCR content in end products in response to growing consumer demand for greater sustainability and [the requirements of] new regulations,” said Andreas Holzner, Global Head of the Special Additives Business Unit at Baerlocher. “Historically, the inconsistent quality of PCR content has limited its use in extrusion blow molding applications. Working with industry leaders, Baerlocher continues to invest in cutting-edge application development that enhances the value of recycled HDPE and expands its use in extrusion blow molding.”
Stephen has been with PlasticsToday and its preceding publications Modern Plastics and Injection Molding since 1992, throughout this time based in the Asia Pacific region, including stints in Japan, Australia, and his current location Singapore. His current beat focuses on automotive. Stephen is an avid folding bicycle rider, often taking his bike on overseas business trips, and is a proud dachshund owner.
“Baerlocher’s technical expertise supported our development of a new generation of high- performance and recycle-friendly resins,” said Mark Canright, HDPE Principal Engineer, ExxonMobil Chemical. “Baerlocher provided us with a cutting-edge stabilization package that supports our effort to increase the number of recycling cycles for our resin.”
However, many of the frames and plastic components snapped in use, most of the parts were proprietary and therefore difficult replace, and the Itera was said to be uncomfortable to ride. Nevertheless, it’s estimated that in the four years the Itera was made 30,000 units were sold around the world.
Plastics additives supplier Baerlocher has collaborated with processor Envision Plastics machinery OEMs Bekum America and W. Müller, and polyethylene supplier ExxonMobil Chemical to develop new sustainable plastics for the packaging industry. Baerlocher’s innovative Baeropol T-Blends stabilization solutions significantly enhance the recyclability of virgin polyolefin resins and the quality of recycled high-density polyethylene (re-HDPE) resins used in extrusion blow molding (EBM) applications. The blends are equally applicable to post-industrial recycled (PIR) and post-consumer recycled (PCR) content used in polyethylene (PE) film. Baerlocher is involved in numerous commercial projects with leading members of the US Association of Plastic Recyclers (APR), such as Little Rock, AR–based recycler Revolution, as well as companies in the UK and Canada (Cascades Flexible Packaging).
Graphics in the video above show that Plastic Innovation has been working wih Peugeot to produce CAD drawings of its proposed frames, which could be made from recycled plastics.
“We are delighted to work with Baerlocher on additives to enhance recycled content used in a broad base of commercial applications, including those for direct food contact,” said Jean Bina, Director of Sales and Market Development at Envision Plastics. “The new PCR grade is available for trials today and is being tested by world-class consumer packaged goods companies and their blow molders.”
Further experiments at Bekum demonstrated that Baeropol T-Blend has a significant positive impact on the processability and final properties of PCR materials that have varying concentrations of virgin material.
So, if Plastic Innovation GmbH has truly figured out a way to mass-produce rideable, long-lasting, non-floppy injection-molded cycle frames it would be on to a winner. As reported by Cycling Industry News, the company has already won an award: its “bicycle of the future” concept bagged an Austrian Greenstart gong.
In fact, injection moulding has a long history in bicycle manufacturing. One of the first was made from injection-molded Lexan in 1973. The Original Plastic Bike Inc had been founded in 1971, and took out magazine adverts, but it sold very few, if any, of its proposed products.
“Mechanical recycling utilizes only 20% of the energy of chemical recycling and much less water,” says Ed Hall, President and CEO, North America, at Baerlocher. “This means mechanical recycling is the most obvious choice right now, but high-quality PCR is rare.” This is where Baeropol T-Blends stabilization additives come in.
The benefits of an injection-molded cycle frame are obvious – manufacturing is swift (just pop them out of mold every minute or so), and they won’t rust. Complex shapes can also be achieved.
"The business model of Plastic Innovation GmbH combines two major innovations," claims the company. "The implementation of the bicycle industry’s new method of manufacturing frames using injection molding together with the innovative business model of rethinking bicycle design."
The company’s website is yet to be populated. However, from the awards information it appears that the company is seeking to mainly license its technology rather than make its own products. "The awareness of the new design options must first be created at the OEMs," says a company blurb.
Baerlocher also worked with W. Müller, a leading German EBM technology provider, to validate new PCR materials formulated with Baeropol T-blends. Results showed that these materials exhibit less variation in die pressure and parison length, while producing bottles with top load performance that matches those made with virgin resin.
Plastic Innovation of Austria is hoping to resurrect the 1980s idea of injection-molded cycle frames. Such frames used to snap, made by companies which flopped in more ways than one.
The most famous plastic bicycle (if we discount carbon composite bicycle frames, that is) was the Itera bicycle of Sweden. This was born from a massive 1978 grant from the Swedish National Board for Technical Development. By 1980 a rideable bicycle – of sorts – was demonstrated by the Itera Development Center AB, and in the following year the first mass-produced Itera bikes were shown to prospective retailers and to the press.
Baerlocher’s work with leading HDPE plastics recycler Envision Plastics enabled the development of a new grade of HDPE PCR content with improved consistency and processability, and ultimately resulted in high-quality packaging applications. The new re-HDPE grade was tested at Bekum America’s facility using an F-style 10-liter bottle with a handle. Results revealed the re-HDPE 100% PCR content displayed more robust processability and enhanced final bottle specifications versus the control.
Additive package from Baerlocher enhances the inconsistent quality of PCR content, opening up avenues in extrusion blow molding applications.
Baeropol T-Blends are formulated with Baerlocher’s Resin Stabilization Technology (RST), customizable additive blends that act as an antacid and produce a synergistic effect with primary and secondary antioxidants to stabilize polyolefin resins. Baerlocher’s advanced RST packages create value far beyond the use of typical binary antioxidant blends. The technology enables companies to achieve superior stabilization in PCR content used in a variety of packaging applications and meets global calls for greater corporate responsibility and to better support the circular economy.
GETTING A QUOTE WITH LK-MOULD IS FREE AND SIMPLE.
FIND MORE OF OUR SERVICES:
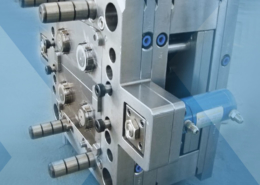
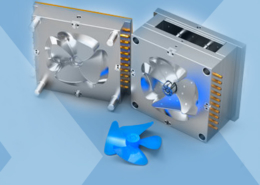
Plastic Molding

Rapid Prototyping
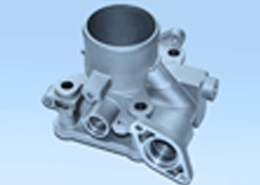
Pressure Die Casting
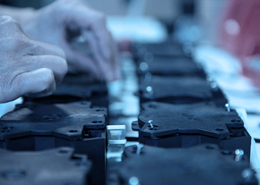
Parts Assembly
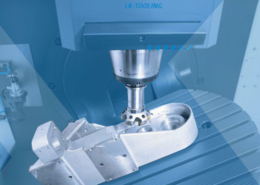