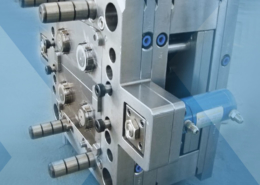
Investing in the UK’s injection moulding sector: The case for all-electric
Author:gly Date: 2024-09-30
That said, the M&A picture remained in line with historical averages, according to the new “2022 Plastics Industry Update” by the Stout Plastics group.
The indelible imprint of injection moulding in medical manufacturing underscores its pivotal role in delivering efficient, high-quality, and cost-effective solutions to the industry. As the medical field continues to evolve, the synergy between injection moulding and emerging technologies like 3D printing is poised to drive innovation further, ensuring the continual enhancement of patient care and medical advancements.
Perhaps intriguingly is the fact that 3D printing and injection moulding are not exclusive of one another. Injection moulding is frequently preceded by 3D printing, which assists with prototyping and even helps create moulds for the injection moulding process.
Polytech Plastic Molding (Prairie Grove, AZ), a maker of custom injection molded and extruded components, was acquired by a subsidiary of Arcane Capital Partners because Polytech’s deep connections and expertise in the HVAC and water-treatment industries broaden Arcane’s plastics portfolio.
“Given the somewhat unevenness of the current economic environment, one of the most important factors is the end markets that they serve and how that end market is performing and expected to perform in the future,” said Michael Benson, Stout’s managing director for plastics and industrials. “Healthcare end markets are generally considered to be fairly immune to short-term setbacks in the economy as opposed to more cyclical end markets like automotive, consumer discretionary, and housing. Other companies that will weather setbacks well include those businesses that are not subject to constraints in a supply chain as well as a tightness in their regional labor markets.”
Luke Smoothy, founder and director, Get It Made, delves into why injection moulding still holds the sceptre in the medical industry and highlights the key benefits it brings.
Liquid silicone injection moulding: This produces pliable, durable parts in high volume, and is used in fabricating tubes and respiratory masks requiring high levels of hygiene and chemical resistance.
Since the need for devices and components in the medical sector is always increasing, injection moulding stands out for its effectiveness and capacity to handle large-scale orders. The method is best suited for high-volume production, making it the preferred method for mass-producing medical components. That said, even though 3D printing is hailed for having cheaper initial costs in small-scale production, its cost advantage diminishes as production volume rises.
To attract the attention of buyers, a lot will ride on the end markets a company serves, as well as the fluidity of its supply chain and labor market.
In terms of the deals that fueled 2022, international and cross-border activity “held up better than domestic,” the report noted. The latter decreased 36%.
In terms of processing, six of the 10 plastics processes Stout tracks were flat or down in 2022. Plastics machinery dropped the most at 46%, while injection molding transactions fell 36% and resin/compounding was down by 30%. Blow molding, rotational molding, and plastics distribution activity grew.
Geoff Giordano is a tech journalist with more than 30 years’ experience in all facets of publishing. He has reported extensively on the gamut of plastics manufacturing technologies and issues, including 3D printing materials and methods; injection, blow, micro and rotomolding; additives, colorants and nanomodifiers; blown and cast films; packaging; thermoforming; tooling; ancillary equipment; and the circular economy. Contact him at [email protected].
The 417 plastics industry M&A transactions of 2022 reflected a 20% decline over the previous year, the report noted, and this year the industry is facing uncertainty thanks to emerging geopolitical issues accompanying continued inflation and interest-rate increases.
Seaway Plastics Engineering, with locations in Port Richey and Brooksville, FL, makes highly engineered plastic components. Seaway was acquired by ICG thanks to Seaway’s commitment to expanding its medical end-market mix.
Thin wall moulding: A specialised form of conventional injection moulding that focuses on the mass production of ultra-thin (less than 1mm) and light plastic parts to make material cost savings. This is used to create portable medical devices enabling clinicians and patients to transport and operate them more easily - such as wearable devices, micro surgical tools, and invasive equipment like catheter ablation tools and endoscopes.
An expansive range of materials are available with injection moulding, making it easier to produce medical equipment that adheres to the strict biosafety and chemical stability criteria of the medical sector. Techniques such as thin wall moulding and gas-assisted injection moulding enable the production of both practical and aesthetically appealing parts.
Gas-assisted injection moulding: In certain medical device applications, gas-assist moulding can provide solutions that conventional injection moulding can’t. The process consists of injecting a pressurised gas into the mould cavity after the initial plastic injection, expelling the molten plastic and forming hollow areas within the final product. It is suited to the manufacturing of complex parts without visual blemishes, for instance, tube- or rod-shaped parts which typically include handles and foot pedals, as well as large, cover-shaped structural parts e.g. side panels and covers for medical devices.
Well-suited for products with straightforward shapes, injection moulding delivers unrivalled precision and finish quality. For medical applications such as moving machine parts or implantable devices, the procedure gives a vital smoother finish.
Merger and acquisition (M&A) activity in the plastics industry dipped slightly in 2022 as the economy struggled to emerge from post-COVID effects only to enter a period of rising interest rates and inflation.
Blow molding, rotational molding, thermoforming, and plastics distribution were bright spots in the end-market segment, the report noted.
Buyers will be looking for companies that serve "attractive end markets” and exhibit desirable characteristics, including “a highly diversified customer base, best-in-class EBITDA margins, and growth profiles. Those companies holding a niche with a process and/or process technology and a history of investing and upgrading in new equipment, facilities, and infrastructure and systems will also be attractive.”
In the realm of medical device manufacturing, the tussle between traditional injection moulding and modern 3D printing technologies continues. However, injection moulding has held its ground firmly, especially when high-volume production, cost-effectiveness, and precision are all paramount.
GETTING A QUOTE WITH LK-MOULD IS FREE AND SIMPLE.
FIND MORE OF OUR SERVICES:
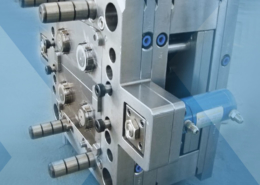
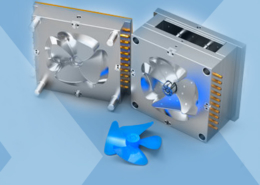
Plastic Molding

Rapid Prototyping
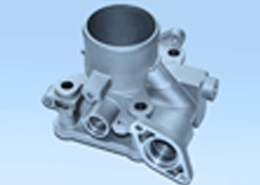
Pressure Die Casting
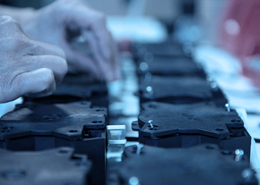
Parts Assembly
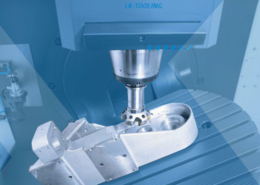