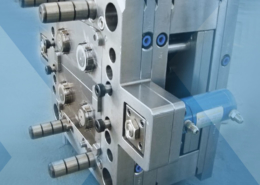
Injection Molding: Safety First—Know the Compatibility of Different Resins - pt
Author:gly Date: 2024-09-30
Incoe’s EGM process applies nitrogen at up to 1500 psi to the molten plastic in the cavity through the core side of the mold. Gas enters through a porous-metal insert, gas pin, or poppet. The gas controller requires a signal from the press to release the gas at or near the end of fill. That signal can be generated according to time or screw position.
While prices moved up for three of the five commodity resins, there was potential for a flat trajectory for the rest of the third quarter.
Additive technology creates air pockets in film during orientation, cutting down on the amount of resin needed while boosting opacity, mechanical properties and recyclability.
External gas molding is a low-pressure process, requiring only up to 2000 psi of pressure to squeeze out sink marks, even in thin-wall applications. An internal gas process may require two to three times that amount (approx. 1000 to 3700 psi), and conventional injection molding uses even higher pressure (approx. 4400 to 10,000 psi) without necessarily solving the problem, says Pearson.
Textron also offers two variations of its IntelliMold process: Xtralite for molding foamed products and Xtrasoft, a process for molding dual-durometer, hard/soft parts with a single barrel. Textron recently launched a website dedicated to the process, www.intellimold.com.
Despite price increase nominations going into second quarter, it appeared there was potential for generally flat pricing with the exception of a major downward correction for PP.
Battenfeld’s Ehritt says its external gas process is used commercially in North America, but the details are proprietary to the customer.
At the MEDevice show in Boston on September 25-26, Accumold will showcase a variety of innovative medical parts and components at booth 815. These products reflect the company’s extensive experience and deep understanding of design for micro manufacturing (DfMM). Accumold stands out due to its vertical integration, enabling it to serve as a comprehensive partner in developing and manufacturing medical devices. Their offerings include design and material support, micro tool fabrication, proprietary micro molding services, advanced metrology, assembly, and automation. This integration streamlines the medical product development process, optimizing timeliness, innovation, cost, and accuracy.
Suppliers of external gas techniques are intimately acquainted with internal gas-assist molding. Incoe has sold mold components for successful gas-assist jobs, and both Battenfeld and CGI market both internal and external gas processes. So their views of the limitations of internal gas assist are presumably unbiased.
Pearson adds that it is a challenge to get internal gas to flow down into a rib. “If you have a lot of parallel ribs, it is virtually impossible to get the gas to flow uniformly down each rib.” Family tools with dissimilar cavities can also present problems of satisfactory gas penetration with internal gas assist, he notes.
The Plastics Industry Association (PLASTICS) has released final figures for NPE2024: The Plastics Show (May 6-10; Orlando) that officially make it the largest ever NPE in several key metrics.
External gas also can assist with part ejection from the core, minimizing or eliminating ejector marks. It can allow thinner part walls for lower material usage. Lower clamp pressures and elimination of overpacking help produce stress-free parts. Thinner walls and improved material contact with the mold can also lead to faster cooling and shorter overall cycle times.
Introduced by Zeiger and Spark Industries at the PTXPO, the nozzle is designed for maximum heat transfer and uniformity with a continuous taper for self cleaning.
When, how, what and why to automate — leading robotics suppliers and forward-thinking moldmakers will share their insights on automating manufacturing at collocated event.
In this collection, which is part one of a series representing some of John’s finest work, we present you with five articles that we think you will refer to time and again as you look to solve problems, cut cycle times and improve the quality of the parts you mold.
Textron’s IntelliMold external gas process differs from the others in two respects. First, it pre-charges the mold cavity with air before melt is introduced. Second, it continuously measures and controls the internal melt pressure as the cavity fills, with the goal of achieving uniform part density. The concept behind this technology is that in conventional injection molding, the melt initially encounters low pressure on entering the mold and then very high pressure at the end of fill. This is especially true when high packing pressures are used in an attempt to fight sinks. The difference in density between the first and last material to solidify is itself the source of sinks, stresses, and warpage, Textron says.
Core Technology Molding turned to Mold-Masters E-Multi auxiliary injection unit to help it win a job and dramatically change its process.
Flat parts like this housing cover are contenders for external gas molding. Battenfeld’s Airmould Contour process removed the sink opposite the support ribs where conventional molding with packing could not.
Ultradent's entry of its Umbrella cheek retractor took home the awards for Technical Sophistication and Achievement in Economics and Efficiency at PTXPO.
Formnext Chicago is an industrial additive manufacturing expo taking place April 8-10, 2025 at McCormick Place in Chicago, Illinois. Formnext Chicago is the second in a series of Formnext events in the U.S. being produced by Mesago Messe Frankfurt, AMT – The Association For Manufacturing Technology, and Gardner Business Media (our publisher).
Across the show, sustainability ruled in new materials technology, from polyolefins and engineering resins to biobased materials.
“With internal gas molding, gas follows the path of least resistance, and therein lie potential problems,” says Incoe’s Blundy. “If the mold is hotter or cooler in one section, it can cause the gas channel to spread or branch into smaller channels, creating a fingering effect.” Fingering is not the only gas-assist phenomenon that can disrupt surface quality, adds CGI’s Pearson. Any hesitation in the flow of gas through the part can produce visible lines on the surface, similar to blemishes caused by hesitation in melt filling. Internal gas assist can also leave a “shadow” mark on the part at the point of gas injection, where the gas pressure is highest. As gas pressure drops farther away from the gas inlet, indentations or weld lines can result. Internal gas molding also requires an entry and exit hole that remain as a blemish on the part. (One internal gas system, from Hettinga Equipment, keeps the gas in the part after molding.)
CGI claims users of its process can reduce part wall thickness by as much as 50%, cycle times by up to 40%, and mold pressure by at least 25%.
While prices moved up for three of the five commodity resins, there was potential for a flat trajectory for the rest of the third quarter.
Gifted with extraordinary technical know how and an authoritative yet plain English writing style, in this collection of articles Fattori offers his insights on a variety of molding-related topics that are bound to make your days on the production floor go a little bit better.
Part design also contributes to effective gas seals. “Part geometries near the parting line must be modified slightly to create the seal,” says Incoe’s Blundy. Often, a rib or boss in a part naturally cordons off the gas so that it acts on a local area between the ribs.
Incoe charges a one-time fee of $5000 to $15,000 per mold for the use of EGM technology, based on the total projected area of the part. Incoe charges an additional $7500 to $9000 for gas-control equipment, although molders can use gas controllers from other suppliers. Incoe can demonstrate EGM at its lab on 125- and 425-ton presses.
Join KraussMaffei for an insightful webinar designed for industry professionals, engineers and anyone interested in the manufacturing processes of PVC pipes. This session will provide a comprehensive understanding of the technology behind the production of high-quality PVC pipes: from raw material preparation to final product testing. Agenda: Introduction to PVC extrusion: overview of the basic principles of PVC pipe extrusion — including the process of melting and shaping PVC resin into pipe forms Equipment and machinery: detailed explanation of the key equipment involved — such as extruders, dies and cooling systems — and their roles in the extrusion process Process parameters: insight into the critical process parameters like temperature, pressure and cooling rates that influence the quality and consistency of the final PVC pipes Energy efficiency: examination of ways to save material and energy use when extruding PVC pipe products
Wittmann Battenfeld says its upgraded Airmould 4.0 technology, which features a more compact footprint, saves material and cycle time — thereby also cutting energy use.
Three external gas injection techniques are being promoted by five firms in the U.S.: the Airmould Contour process from Battenfeld of America; external gas molding technology developed by Asahi Kasei Corp. in Japan and licensed to Incoe and also Cinpres Gas Injection (CGI) Inc.; and the IntelliMold process, a gas counterpressure method offered by Textron Automotive through its IntelliMold Systems Div.
Plastics Technology’s Tech Days is back! Every Tuesday in October, a series of five online presentations will be given by industry supplier around the following topics: Injection Molding — New Technologies, Efficiencies Film Extrusion — New Technologies, Efficiencies Upstream/Downstream Operations Injection Molding — Sustainability Extrusion — Compounding Coming out of NPE2024, PT identified a variety of topics, technologies and trends that are driving and shaping the evolution of plastic products manufacturing — from recycling/recyclability and energy optimization to AI-based process control and automation implementation. PT Tech Days is designed to provide a robust, curated, accessible platform through which plastics professionals can explore these trends, have direct access to subject-matter experts and develop strategies for applying solutions in their operations.
technotrans says climate protection, energy efficiency and customization will be key discussion topics at PTXPO as it displays its protemp flow 6 ultrasonic eco and the teco cs 90t 9.1 TCUs.
Mixed in among thought leaders from leading suppliers to injection molders and mold makers at the 2023 Molding and MoldMaking conferences will be molders and toolmakers themselves.
Join Wittmann for an engaging webinar on the transformative impact of manufacturing execution systems (MES) in the plastic injection molding industry. Discover how MES enhances production efficiency, quality control and real-time monitoring while also reducing downtime. It will explore the integration of MES with existing systems, emphasizing compliance and traceability for automotive and medical sectors. Learn about the latest advancements in IoT and AI technologies and how they drive innovation and continuous improvement in MES. Agenda: Overview of MES benefits What is MES? Definition, role and brief history Historical perspective and evolution Longevity and analytics Connectivity: importance, standards and integration Advantages of MES: efficiency, real-time data, traceability and cost savings Emerging technologies: IoT and AI in MES
Discover how artifical intelligence is revolutionizing plastics processing. Hear from industry experts on the future impact of AI on your operations and envision a fully interconnected plant.
Learn about sustainable scrap reprocessing—this resource offers a deep dive into everything from granulator types and options, to service tips, videos and technical articles.
Special hardware such as a nitrogen generator or delivery system, a regulator, and a control device (shown here from Battenfeld) add cost that offsets savings gained with the use of external gas molding.
Although adoption of external gas technology has been slow in coming, suppliers report growing interest by molders—interest that is impossible to verify because of customer secrecy. “We have a dozen applications that are active and commercial right now, but all are proprietary,” says John Blundy, v.p. of business development at Incoe.
Micro molding for medical device OEMs requires years of expertise and the right business culture, personnel, and equipment to ensure project success. Micro molders handle low, medium, and high volume runs with various materials, requiring different validation levels. They must also expertly manage the handling, storage, and processing of costly, sensitive materials used in critical implantable applications.
External gas molding holds process advantages over conventional injection molding, as well. “Conventional molding tries to solve the problem of sink by high-pressure pack and hold. To offset shrinkage, conventional molders inject more material in the cavity for packing, but that creates stress within the part, and may not fully solve the issue of sink,” says Pearson. In some cases, molders will sustain the pack and hold time to prevent sink, at the expense of added cycle time.
With advocacy, communication and sustainability as three main pillars, Seaholm leads a trade association to NPE that ‘is more active today than we have ever been.’
Battenfeld’s Airmould Contour process is an extension of its Airmould technique for internal gas assist. It uses a mobile gas-delivery unit with graphical touchscreen controls. “We don’t control the volume of gas into the part, we look at the pressure,” says Ehritt. The closed-loop gas-pressure control system introduces and maintains the gas pressure in the cavity on a time or melt-pressure trigger signal. Gas enters through a nozzle or needle that is designed to install flush with the inner cavity surface.
Resin drying is a crucial, but often-misunderstood area. This collection includes details on why and what you need to dry, how to specify a dryer, and best practices.
The process can be licensed by the mold or by the press. The fee is typically from $5000 to $20,000, depending on the size of the mold and the equipment needed. The fee lasts for the life of the mold, and there are no ongoing royalties. CGI also provides a service to modify molds for external gas molding.
The IntelliMold system uses two pressure transducers, one in the nozzle, and the other in the cavity at or near the farthest point of fill. As the melt enters the mold, the compressed air is forced back out the vents from which it entered. The cavity transducer senses the pressure of the gas initially, and then the melt pressure when the cavity is almost filled. A controller receives pressure data from the two sensors every 2 millisec and processes those data with proprietary algorithms to arrive at a nominal value for the melt pressure in the cavity. The controller adjusts the speed of the injection ram to maintain the setpoint value for in-mold melt pressure. That setpoint is selected by trial and error or previous experience with the process.
Internal gas injection also requires special gas-delivery nozzles and venting devices, as well as spillover valves for the melt displaced by the gas. These items are eliminated or re-engineered into the mold with external gas.
Brett Saddoris, Accumold’s Technical Marketing Manager says, “We are excited to be at MEDevice Boston, and we are proud to have collaborated with numerous leading medical device manufacturers globally, working strategically with each to ensure the most efficient product development process. The key to success lies in medical device OEMs viewing their micro molder not just as a job shop but as a partner from the earliest stages of the design-to-market process to avoid costly errors. Manufacturing micro medical plastic products necessitates a genuine partnership between OEMs and micro molding specialists, distinct from traditional OEM/supplier relationships. In micro manufacturing, the most critical issues often arise during the design and prototyping stages, including material selection and packaging considerations. A true partnership ensures faster time-to-market with more efficient and cost-effective products.”
CGI’s External Gas Assist process has a number of commercial applications in Europe and Asia, and at least one North American molder is looking into it for an automotive application, reports Terry Pearson, chairman and director. CGI was created in August from the merger of two U.K. companies—Cinpres, a supplier of internal gas-assist technology, and Gas Injection Ltd., an early promoter of Asahi’s external gas method. Pearson says Asahi Kasei has issued 30 licenses for the technology since the mid-’90s. “Several applications are being developed for automotive parts where sink marks cannot be eliminated by any other means,” Pearson says.
Textron says it has three commercial IntelliMold gas counterpressure applications at its own Trim division in Troy, Mich. That operation now has 24 presses equipped for IntelliMold—most of them over 1000 tons— and plans to have a minimum of 100 systems installed on its machines by the end of this year, says Jerry Mosingo, executive v.p. of manufacturing. More than a dozen licenses for the process were issued to other firms before Textron bought the technology last year, along with its original developer, M&C Advanced Processes of Ann Arbor, Mich.
Accumold invites all medical OEMs at MEDevice Boston to visit and discuss how micro molding with Accumold can drive the manufacture of innovative, timely, and cost-effective medical devices.
The pressurized air acts as a constant force that pushes material uniformly against the walls of the cavity. “This achieves better dimensional stability and reduced warping, sinks, knit lines, and shrinkage,” Spalding says.
The aim of this presentation is to guide you through the factors and the numbers that will help you determine if a robot is a smart investment for your application. Agenda: Why are you considering automation? What problems are you trying to solve? How and why automation can help Crunch the numbers and determine the ROI
Processors with sustainability goals or mandates have a number of ways to reach their goals. Biopolymers are among them.
This Knowledge Center provides an overview of the considerations needed to understand the purchase, operation, and maintenance of a process cooling system.
Cinpres Gas Injection has licenses to two external gas technologies owned by Asahi. One is similar to that offered in North America by Incoe. The second covers external gas injection with the added packing function. “Even with external gas there may be some volumetric shrinkage. Packing helps minimize the shrinkage further,” says Pearson. He declined to say in what circumstances CGI would recommend one process over the other or to specify in detail how the two processes differ. Parts made on either process are indistinguishable from each other, according to Pearson.
Exhibitors and presenters at the plastics show emphasized 3D printing as a complement and aid to more traditional production processes.
Across all process types, sustainability was a big theme at NPE2024. But there was plenty to see in automation and artificial intelligence as well.
Sources at CGI, Incoe, and Battenfeld also warn that external gas molding is limited to parts requiring a high-quality finish on only one side. External gas pressure can leave a wavy effect on the non-critical side of the part. “So a molder of clear parts may not want to use this process,” cautions Battenfeld’s Ehritt.
Saddoris continues, “Medical device OEMs are under pressure to maintain profitability despite decreasing prices, which necessitates the development of innovative products that meet increasingly stringent end-user demands. There will be a growing need for versatile devices that leverage the potential of 'smart' diagnostics and treatment through the proliferation of 'big data,' as well as cost-effective alternatives to traditionally expensive diagnostic and therapeutic devices. Micro molding is the preferred solution for many medical device OEMs to meet these rigorous manufacturing requirements.”
In a time where sustainability is no longer just a buzzword, the food and beverage packaging industry is required to be at the forefront of this innovation. By adopting circular packaging processes and solutions, producers can meet regulatory requirements while also satisfying consumer demand and enhancing brand reputation. Join Husky to learn more about the broader implications of the circular economy — as well as how leading brands are leveraging this opportunity to reduce costs, increase design flexibility and boost product differentiation. Agenda: The cost and operational benefits of embracing circularity Key materials in circular packaging — including rPET and emerging bioplastics How to design a circular food and beverage package Strategies for selecting sustainable closures to future-proof packaging solutions Optimization and streamlining of production processes for enhanced efficiency How Husky Technologies can enable your sustainable success
August 29-30 in Minneapolis all things injection molding and moldmaking will be happening at the Hyatt Regency — check out who’s speaking on what topics today.
Evacuation of the gas also requires some mold modification. Textron connects the existing vents in a conventional mold by machining a single channel that acts as an air manifold. Other systems, like Incoe’s EGM, rely on a porous-metal insert in the mold that allows for the gas to enter and exit. “When the supply of gas is turned off, gas flow reverses back through the insert, following the path of least resistance,” says Blundy. In addition, special valve-gate technology may be needed to prevent the gas from escaping through hot-runner nozzles.
The medical device industry demands increasingly smaller products with precise, micron-level tolerances, necessitating partnerships with micro molding experts like Accumold. These experts provide the precision, repeatability, and zero failure rates crucial for safety-critical applications.
While the melting process does not provide perfect mixing, this study shows that mixing is indeed initiated during melting.
Both mold and part design contribute to gas sealing. As shown here, ribs and bosses help confine the gas to specific areas of the part surface. (Source: Incoe)
Suppliers note that material and cycle-time savings will be partly offset by licensing fees, mold modifications, and additional equipment costs to run the process. Also, some sources concede that cycle-time reductions with external gas can be minimal. In order to be effective, there is typically a delay between cavity filling and introduction of the gas. “You must give the material a little time to set up, so that the gas has something to push against,” says Blundy. The time for the gas to enter, pack, and exit the tool is about the same as the pack and hold time of conventional injection.
Plastics Technology covers technical and business Information for Plastics Processors in Injection Molding, Extrusion, Blow Molding, Plastic Additives, Compounding, Plastic Materials, and Resin Pricing. About Us
Second quarter started with price hikes in PE and the four volume engineering resins, but relatively stable pricing was largely expected by the quarter’s end.
CGI offers a nitrogen-injection system that delivers gas at pressures up to 1470 psi, controlled by sensors installed in the mold and machine.
Two alternative process technologies designed to remedy molded surface imperfections have been available since the early 1990s. One approach applies a gas to one exterior surface of the part after the mold has been filled about 98-99% with melt. The gas enters the mold from the core side and presses the critical appearance surface against the opposite mold face. Another method is a gas counterpressure method, in which a gas (air) is used to prepressurize the mold before melt is injected to ensure continuous pressure of melt against the mold before the cavity fills. Both approaches act to hold the material to the mold surface while the melt cools. “They affect the material in a way similar to compression molding,” says Juergen Ehritt, process engineering and development manager at Battenfeld.
Internal gas assist has been used to solve sink problems by making the ribs even thicker and then partially hollowing them out with gas. Drawbacks of this approach are said to include the likelihood of higher material usage, higher packing pressures, and longer cooling times—with still no guarantee of sink removal.
External gas injection is finally getting molders’ attention as a means to improve part surface quality. Two different approaches are available for licensing. Here’s a look at the processes, the potential benefits, and the commercial players.
In this three-part collection, veteran molder and moldmaker Jim Fattori brings to bear his 40+ years of on-the-job experience and provides molders his “from the trenches” perspective on on the why, where and how of venting injection molds. Take the trial-and-error out of the molding venting process.
Setting up the IntelliMold process does not use a conventional injection-speed or pressure profile. There is no speed profile, and the pressure profile is essentially flat. This approach is said to make the injection process “transparent,” or immune, to variations in oil viscosity, mold and ambient temperatures, and material viscosity.
External gas technology is not a panacea for all molders, suppliers caution. “There are many molding jobs where a degree of stress in a part is acceptable and doesn’t have adverse effects on the product,” says Pearson.
To illustrate the advantages of external gas, Incoe molded a 100-in.2 scanner cover of ABS/PC alloy using a conventional process with and without packing, as well as its External Gas Molding (EGM) process. Cycle time was the same in all cases. The part made without packing weighed 246.5 g, required 41 tons of clamp force, and had sink marks. The part produced with the packing phase weighed 261.5 g, required 125 tons of clamping, and still had sinks. The EGM part weighed 246.5 g, needed only 41 tons of pressure, and was sink-free, Blundy reports.
Join this webinar to explore the transformative benefits of retrofitting your existing injection molding machines (IMMs). Engel will guide you through upgrading your equipment to enhance monitoring, control and adaptability — all while integrating digital technologies. You'll learn about the latest trends in IMM retrofitting (including Euromap interfaces and plasticizing retrofits) and discover how to future-proof your machines for a competitive edge. With insights from industry experts, it'll walk you through the decision-making process, ensuring you make informed choices that drive your business forward. Agenda: Maximize the value of your current IMMs through strategic retrofitting Learn how to integrate digital technologies to enhance monitoring and control Explore the benefits of Euromap interfaces and plasticizing retrofits Understand how retrofitting can help meet new product demands and improve adaptability Discover how Engel can support your retrofitting needs, from free consultations to execution
Accumold’s micro molding process enables the production of tiny, complex, and feature-rich components efficiently, cost-effectively, and in large volumes. The expert use of micro molding technologies provides medical device OEMs with a competitive edge, driving both product innovation and profitability. High-quality parts with precise dimensional accuracy are crucial for sensitive medical applications, including specialized devices for cancer treatment and diagnosis, small molded catheter tips, micro-needles, small surgical instruments, dental implants, infection control devices, and staples, among others.
Timing of the gas injection can be important. Suppliers like Battenfeld delay gas injection so the polymer can set up slightly, giving the gas a firmer surface to push against.
After successfully introducing a combined conference for moldmakers and injection molders in 2022, Plastics Technology and MoldMaking Technology are once again joining forces for a tooling/molding two-for-one.
“We charge the mold with 200-psi shop air, which helps to control the flow front of the material and achieves uniform density from the beginning to the end of part fill,” explains Textron’s Spalding. “The counterpressure packs the part as we fill, so we do not need to overpack the mold or stress the material.”
While the major correction in PP prices was finally underway, generally stable pricing was anticipated for the other four commodity resins.
In this collection of articles, two of the industry’s foremost authorities on screw design — Jim Frankand and Mark Spalding — offer their sage advice on screw design...what works, what doesn’t, and what to look for when things start going wrong.
Thousands of people visit our Supplier Guide every day to source equipment and materials. Get in front of them with a free company profile.
In this collection of content, we provide expert advice on welding from some of the leading authorities in the field, with tips on such matters as controls, as well as insights on how to solve common problems in welding.
Mold maintenance is critical, and with this collection of content we’ve bundled some of the very best advice we’ve published on repairing, maintaining, evaluating and even hanging molds on injection molding machines.
Take a deep dive into all of the various aspects of part quoting to ensure you’ve got all the bases—as in costs—covered before preparing your customer’s quote for services.
Textron’s IntelliMold eliminates sink, even if the part is intentionally short shot, as this radio bezel is. A sink mark appears on the conventionally molded, fully filled part at right.
External gas injection typically requires a pressure sensor in the mold or in the gas-delivery lines, as well as a gas generator and control technology. The speed of gas injection is important, as well as the pressure. Mold modifications can add 5% to 20% to tool costs. The most critical aspect of tool modification is tight sealing of the mold to hold uniform gas pressure during molding. Critical areas for sealing are the parting lines, ejector pins, cores, and vent holes. In molds with moveable cores or other components, suppliers suggest adding a seal block to the outer part of the mold. Silicone rubber is the most commonly used seal material.
External gas injection introduces gas on the core side of the mold to squeeze sink marks and other imperfections out of the Class A surface of a part. In Incoe’s EGM process, gas enters through a porous metal insert.
Multiple speakers at Molding 2023 will address the ways simulation can impact material substitution decisions, process profitability and simplification of mold design.
Internal supporting structures of a part are typically thicker than the external part wall and therefore cool more slowly. This difference in cooling creates internal stresses within the part that can show up on the part surface as sink marks, blemishes, indentations, shiny spots, and warpage. “When the structural section [rib or boss] cools, it pulls the material around it due to normal volumetric shrinkage, attracting material that is on the surface of the part,” Incoe’s Blundy explains.
Mold sealing technology is vital to external gas molding. Texton deploys a silicone sealant around the mold edges, pins, and valves to prevent leakage. O-rings and other devices also prevent gas escape.
These concerns have opened the door to external gas injection. Besides solving surface-quality problems, which may also eliminate downstream painting, external gas techniques can yield a variety of process benefits. One is the reduction or elimination of pack and hold phases of the cycle. “At least 50% of the clamp tonnage is needed for the packing phase,” notes Battenfeld’s Ehritt. Packing is accomplished by the gas pressure, so clamp tonnage requirements may drop by 30% or more. Lower clamp forces may mean extended mold life, adds Pearson.
“The use of an external gas system gives the molder an opportunity to use lower-cost, higher-shrink materials such as PP,” says CGI’s Pearson.
In addition, the force of the gas holds the appearance side of the part in contact with the mold-cavity surface longer by preventing it from shrinking away. This, along with the elimination of pack and hold, can trim cycle times by 25%, Textron claims.
Successfully starting or restarting an injection molding machine is less about ticking boxes on a rote checklist and more about individually assessing each processing scenario and its unique variables.
Implementing a production monitoring system as the foundation of a ‘smart factory’ is about integrating people with new technology as much as it is about integrating machines and computers. Here are tips from a company that has gone through the process.
However, Textron technical-services manager Anthony Spalding says his firm is optimizing its process to minimize that effect. The firm has a made a blemish-free sample panel from clear ABS.
The process is installed on 500-ton and 4000-ton presses at the Auburn Hills, Mich., lab of Solvay Engineered Polymers. These presses are available to Battenfeld for customer demonstrations Licensing costs depend on the application.
This month’s resin pricing report includes PT’s quarterly check-in on select engineering resins, including nylon 6 and 66.
Wittmann Battenfeld will introduce the new EcoPower B8X injection molding machine line and show direct current as an energy source for a concept machine that will power its own robot.
Coverage of single-use plastics can be both misleading and demoralizing. Here are 10 tips for changing the perception of the plastics industry at your company and in your community.
Textron conducts IntelliMold trials on four machines at its lab—Van Dorn 230- and 350-tonners, a 500-ton Engel, and an 880-ton HPM press. Textron licenses the technology on a per-machine basis. Cost is determined on a sliding scale based on press size. Installation and training are included in the license fee. Engel and Van Dorn Demag are licensed to offer the IntelliMold process on their machines.
Join Engel in exploring the future of battery molding technology. Discover advancements in thermoplastic composites for battery housings, innovative automation solutions and the latest in large-tonnage equipment designed for e-mobility — all with a focus on cost-efficient solutions. Agenda: Learn about cutting-edge thermoplastic composites for durable, sustainable and cost-efficient battery housings Explore advanced automation concepts for efficient and scalable production See the latest large-tonnage equipment and technology innovations for e-mobility solutions
Some suppliers also say high-purity (at least 98%) nitrogen gas is the best for their process. Higher oxygen content in the pressurized gas can cause oxidation of some plastic melts. Using nitrogen adds equipment and/or operating costs. But Textron spokesmen say they have seen no problems with using compressed air in the IntelliMold counterpressure technique. Also, Incoe recently tested its EGM process with clean, dry shop compressed air and is encouraged by the initial results, Blundy reports.
Mike Sepe has authored more than 25 ANTEC papers and more than 250 articles illustrating the importance of this interdisciplanary approach. In this collection, we present some of his best work during the years he has been contributing for Plastics Technology Magazine.
Sustainability continues to dominate new additives technology, but upping performance is also evident. Most of the new additives have been targeted to commodity resins and particularly polyolefins.
Say “manufacturing automation” and thoughts immediately go to the shop floor and specialized production equipment, robotics and material handling systems. But there is another realm of possible automation — the front office.
Injection molding a part with Class-A surface finish and ribs or bosses has proven an elusive goal for molders, despite their best efforts with conventional injection or internal gas-assist technology. Yet demand is rising for sink-free surfaces over ribs and bosses in products for a wide variety of industries. Demand is particularly keen in thin-wall applications such as cell phones, automotive body side moldings, car interior panels, and computer monitors. Besides thin-wall parts, suppliers say external gas molding has its greatest potential in large, flat parts such as cover panels, housings, fascias, and grilles.
GETTING A QUOTE WITH LK-MOULD IS FREE AND SIMPLE.
FIND MORE OF OUR SERVICES:
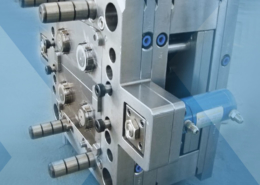
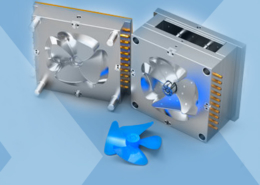
Plastic Molding

Rapid Prototyping
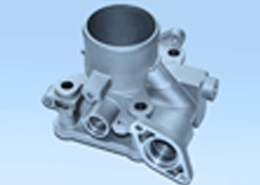
Pressure Die Casting
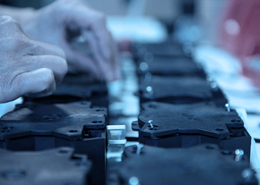
Parts Assembly
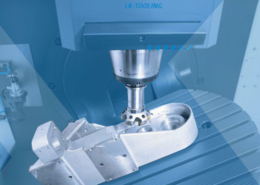