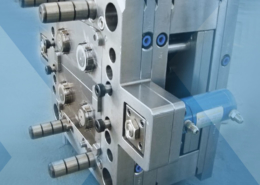
Injection Molding: Safety First—Know the Compatibility of Different Resins - del
Author:gly Date: 2024-09-30
“A low-cost, high-quality part with tamper evidence, a living hinge, and multi-shot too, and to be able to get it all from a single source, for us is significant. We expect this part to be the next big thing in medication delivery,” says Oshgan. He adds that this was “the most money we have ever spent on a single four-cavity tool; however, it cost about the same as sourcing four separate tools.”
In this collection of content, we provide expert advice on welding from some of the leading authorities in the field, with tips on such matters as controls, as well as insights on how to solve common problems in welding.
With advocacy, communication and sustainability as three main pillars, Seaholm leads a trade association to NPE that ‘is more active today than we have ever been.’
Formerly a showroom for early-aughts-era Van Dorn hydraulics, the newest additions to Drummond Industries’ transforming fleet are all-electric Niigata injection molding machines.
Despite price increase nominations going into second quarter, it appeared there was potential for generally flat pricing with the exception of a major downward correction for PP.
Successfully starting or restarting an injection molding machine is less about ticking boxes on a rote checklist and more about individually assessing each processing scenario and its unique variables.
Mike Sepe has authored more than 25 ANTEC papers and more than 250 articles illustrating the importance of this interdisciplanary approach. In this collection, we present some of his best work during the years he has been contributing for Plastics Technology Magazine.
Gifted with extraordinary technical know how and an authoritative yet plain English writing style, in this collection of articles Fattori offers his insights on a variety of molding-related topics that are bound to make your days on the production floor go a little bit better.
Hospira was sold on the combination of MGS’ core competencies: “They could assist in selecting the multi-component tooling process and could play a part in mold building and hot-runner design. MGS also contributed in-house custom automation solutions, and they molded the part,” says Oshgan.
The aim of this presentation is to guide you through the factors and the numbers that will help you determine if a robot is a smart investment for your application. Agenda: Why are you considering automation? What problems are you trying to solve? How and why automation can help Crunch the numbers and determine the ROI
Sustainability continues to dominate new additives technology, but upping performance is also evident. Most of the new additives have been targeted to commodity resins and particularly polyolefins.
MGS has been involved in multi-shot molding and moldmaking since the 1980s and it is now a mainstay of the company’s business. The latest enhancement is in-mold assembly, such as the MGS-patented valves with a PP petcock molded into a PC housing with at TPE seal.
Berg adds that despite the added equipment and tooling cost, “Multi-shot molding doesn’t have to have a million-shot volume to be viable. It can simplify your downstream operations. It allows for insert molding with metal, wood, fabric, metal, or even magnets.” To date, the most elaborate multi-shot project at MGS involves a six-shot manufacturing cell for a high-end consumer application.
While the major correction in PP prices was finally underway, generally stable pricing was anticipated for the other four commodity resins.
After successfully introducing a combined conference for moldmakers and injection molders in 2022, Plastics Technology and MoldMaking Technology are once again joining forces for a tooling/molding two-for-one.
The Hehl family company, which grew into Arburg, marks its centennial this year with a new generation of energy and resource efficient hybrid injection molding machines.
Arburg will show its all-electric Allrounder 720 A press utilizing injection compression molding to create thin-wall IML cups from PP.
The previous generation of the iSecure device was molded as two separate parts, requiring two molds and semi-automated downstream assembly equipment. Producing all the plastic parts in a single mold with no secondary assembly vastly reduced the overall manufacturing cost. Multi-shot in-mold assembly (IMA) saved $1.5 million to $2 million in custom-built downstream equipment costs alone. Hospira also saved six to eight months lead time by not having to calibrate a complicated assembly system. IMA also improves quality control. With IMA, what would have been critical dimensions for post-mold assembly are no longer required to ensure proper fit, says Oshgan.
Sustainability continues to dominate new additives technology, but upping performance is also evident. Most of the new additives have been targeted to commodity resins and particularly polyolefins.
For another IMA job, MGS consolidated the design of a buckle for a safety helmet, previously molded in six separate components. MGS redesigned the process to mold them all together on an indexing plate system using two materials.
In this collection, which is part one of a series representing some of John’s finest work, we present you with five articles that we think you will refer to time and again as you look to solve problems, cut cycle times and improve the quality of the parts you mold.
One recent project put MGS in the forefront of the new trend to in-mold assembly. The product, a disposable syringe drug delivery system, won two awards at the NPE 2009 show in June in Chicago. SPI’s Alliance of Plastics Processors named it best medical part in its International Plastics Design competition. It also received a joint design award at NPE from the Industrial Designers Society of America and Plastics News magazine. The part was molded by MGS’s All West Plastics division in Antioch, Ill., for Hospira, Inc., a global maker of drug delivery devices based in Lake Forest, Ill.
In electric drives, PEEK film-based electrical insulation can help improve thermal management, reliable operation and reduce overall system cost. With the automotive industry transitioning to electric vehicles, the quest for more efficient high-density e-motors and lower cost is still on. Most e-motor manufacturers have opted to use the Permanent Magnet Synchronous Machine (PMSM) in which the design of the insulating system is instrumental. Computer simulation from highly regarded third party specialists on an established 80 kW EV e-motor have shown a potential 5% increase torque output in a same size e-motor, enabled by 40% thinner Aptiv slot liner, enabling a 2% increased copper content (slot-fill factor). Additional simulation has indicated that the excellent thermal conductivity of Aptiv film results in improved thermal management and a reduction of peak winding temperatures by 2-3°C (36-37°F) versus traditional laminates.
Join Wittmann for an engaging webinar on the transformative impact of manufacturing execution systems (MES) in the plastic injection molding industry. Discover how MES enhances production efficiency, quality control and real-time monitoring while also reducing downtime. It will explore the integration of MES with existing systems, emphasizing compliance and traceability for automotive and medical sectors. Learn about the latest advancements in IoT and AI technologies and how they drive innovation and continuous improvement in MES. Agenda: Overview of MES benefits What is MES? Definition, role and brief history Historical perspective and evolution Longevity and analytics Connectivity: importance, standards and integration Advantages of MES: efficiency, real-time data, traceability and cost savings Emerging technologies: IoT and AI in MES
This Knowledge Center provides an overview of the considerations needed to understand the purchase, operation, and maintenance of a process cooling system.
One pioneer in this expanding field has made multi-shot molding a cornerstone of its business and is championing its spread to other manufacturers. MGS Mfg. Group in Germantown, Wis., was started by Mark G. Sellers in 1982 as Moldmakers Incorporated. It soon got involved in custom injection molding as well.
The aim of this presentation is to guide you through the factors and the numbers that will help you determine if a robot is a smart investment for your application. Agenda: Why are you considering automation? What problems are you trying to solve? How and why automation can help Crunch the numbers and determine the ROI
The unique material delivers a combination of cost reduction, light weight, design freedom, strength and production speed in next-generation components. This includes: up to 6.5x faster for in-situ processing for laser welded AFP processing, up to 40% cost savings vs. metals, and up to 70% lighter than metals with equivalent strength and stiffness.
Across the show, sustainability ruled in new materials technology, from polyolefins and engineering resins to biobased materials.
Say “manufacturing automation” and thoughts immediately go to the shop floor and specialized production equipment, robotics and material handling systems. But there is another realm of possible automation — the front office.
When, how, what and why to automate — leading robotics suppliers and forward-thinking moldmakers will share their insights on automating manufacturing at collocated event.
This application embodies one of the key enabling technologies of in-mold assembly: Incompatible materials can be overmolded onto each other in the melt form and not stick to each other once cooled and solidified. This principle allows the LDPE tamper-evident band to be removed from the PP plunger and the plunger to slide freely along guide elements of the PETG body.
Mold maintenance is critical, and with this collection of content we’ve bundled some of the very best advice we’ve published on repairing, maintaining, evaluating and even hanging molds on injection molding machines.
The MGS equipment division offers its UMS series of portable add-on injection units in mold-mounted, horizontal, and vertical press-mounted designs, including versions for LSR. MGS also makes servo-driven and hydraulic rotary platens, hot-runner controllers, and a mold-vacuum unit that pulls air from the mold prior to injection to ensure complete filling. This business unit also produces complete turnkey manufacturing cells, as well as custom equipment such as extruders and automation systems for in-mold labeling and decorating, parts removal, and press-side parts handling.
When, how, what and why to automate — leading robotics suppliers and forward-thinking moldmakers will share their insights on automating manufacturing at collocated event.
Using the theme “The Element of Invention” at the upcoming K 2019 show, Victrex will spotlight the latest additions to its portfolio of PEEK and PAEK polymers. Included are additive manufacturing (AM/3D printing filaments and powders), composites, films, gear solutions, and a new food-grade family, all of which complement the innovations that followed the invention of PEEK over 40 years ago, which have ranged across key industrial sectors in advanced applications, often replacing metals.
Despite price increase nominations going into second quarter, it appeared there was potential for generally flat pricing with the exception of a major downward correction for PP.
Take a deep dive into all of the various aspects of part quoting to ensure you’ve got all the bases—as in costs—covered before preparing your customer’s quote for services.
Solvay’s KetaSpire KT-857 PEEK extrusion compound eliminates adhesion and sustainability constraints of conventional PEEK or enamel insulation processes.
▪ Energy: Survive and thrive in the extremes.—In 2018, Victrex introduced Victrex CT 200 for applications at cryogenic temperatures [-150°C to -200°C (-238°F to -328°F)]. As the latest member of the Victrex CT PEEK polymers, the 200 grade series reportedly exhibits improved sealing over a wider range of temperatures, compared to commonly used materials such as PCTFE. It does so at low temperatures on account of its greater ductility, and at high temperatures due to its superior creep resistance.
Say “manufacturing automation” and thoughts immediately go to the shop floor and specialized production equipment, robotics and material handling systems. But there is another realm of possible automation — the front office.
Join KraussMaffei for an insightful webinar designed for industry professionals, engineers and anyone interested in the manufacturing processes of PVC pipes. This session will provide a comprehensive understanding of the technology behind the production of high-quality PVC pipes: from raw material preparation to final product testing. Agenda: Introduction to PVC extrusion: overview of the basic principles of PVC pipe extrusion — including the process of melting and shaping PVC resin into pipe forms Equipment and machinery: detailed explanation of the key equipment involved — such as extruders, dies and cooling systems — and their roles in the extrusion process Process parameters: insight into the critical process parameters like temperature, pressure and cooling rates that influence the quality and consistency of the final PVC pipes Energy efficiency: examination of ways to save material and energy use when extruding PVC pipe products
In electric drives, use of Aptiv film has been shown to result in improved thermal management and a reduction of peak winding temperatures vs. traditional laminates.
In this collection of content, we provide expert advice on welding from some of the leading authorities in the field, with tips on such matters as controls, as well as insights on how to solve common problems in welding.
While prices moved up for three of the five commodity resins, there was potential for a flat trajectory for the rest of the third quarter.
Mold maintenance is critical, and with this collection of content we’ve bundled some of the very best advice we’ve published on repairing, maintaining, evaluating and even hanging molds on injection molding machines.
Baystar's Borstar technology is helping customers deliver better, more reliable production methods to greenhouse agriculture.
Victrex CT 200 PEEK have been shown to meet the increasingly demanding turbine requirements (e.g., wind energy) which are pushing the limits of metals and traditional polymer solution
Though it grabs a lot of headlines, multi-material, multi-shot processing still makes up only about 10% of injection molding activity in North America. However, the consumer appeal of multi-color and hard/soft material combinations is growing in applications from power tools to toothbrushes. And designers like the cost and quality advantages of eliminating separate molding steps and assembly operations. That creates opportunities for adventurous molders who can manage more complex processes and more sophisticated and expensive machinery and tooling. Those opportunities are multiplied by the nascent trend toward “in-mold assembly”—producing and joining what would normally be separate functional parts in a single machine and mold.
Learn about sustainable scrap reprocessing—this resource offers a deep dive into everything from granulator types and options, to service tips, videos and technical articles.
▪ Manufacturing & Engineering: Reducing part production costs, while increasing reliability and maintenance intervals.—The reduction of maintenance costs and downtime are just two of many needs across a range of manufacturing and engineering industries. Using VICTREX PEEK solutions can contribute to keeping highly automated industrial environments moving, with minimal maintenance and at the highest safety standard. The metal replacement polymer can enable durable solutions that improve the lifetime of components—for example up to 40% for conveyor belts or two times the operating lifetime for rotor shaft bushings.
In a time where sustainability is no longer just a buzzword, the food and beverage packaging industry is required to be at the forefront of this innovation. By adopting circular packaging processes and solutions, producers can meet regulatory requirements while also satisfying consumer demand and enhancing brand reputation. Join Husky to learn more about the broader implications of the circular economy — as well as how leading brands are leveraging this opportunity to reduce costs, increase design flexibility and boost product differentiation. Agenda: The cost and operational benefits of embracing circularity Key materials in circular packaging — including rPET and emerging bioplastics How to design a circular food and beverage package Strategies for selecting sustainable closures to future-proof packaging solutions Optimization and streamlining of production processes for enhanced efficiency How Husky Technologies can enable your sustainable success
MGS’s TecStar custom manufacturing division has an 180,000-ft2 main plant in Germantown, Wis.; a 30,000-ft2 facility in Libertyville, Ill.; and a 100,000ft2 plant in Chihuahua, Mexico. The division has more then 140 presses from 28 to 880 tons. All are multi-shot capable via UMS add-on injectors. TecStar also offers value-added secondary operations such as pad printing, ultrasonic welding, heat staking, manual assembly, and packaging. TecStar also has five continuous-extrusion shuttle blow molders and one industrial blow molding press.
▪ AM/3D Printing—There is a new PAEK filament for filament fusion (FF) systems and a fine PAEK powder for selective sintering (SS) units. They are said to deliver better results with improved mechanical properties in printed parts and easier printing than past attempts to use PEEK in additive manufacturing. Victrex is investing in these new materials optimized for AM and pairing them with new machine technology in order to create integrated solutions, while working directly both with key industry partners and customers.
Join this webinar to explore the transformative benefits of retrofitting your existing injection molding machines (IMMs). Engel will guide you through upgrading your equipment to enhance monitoring, control and adaptability — all while integrating digital technologies. You'll learn about the latest trends in IMM retrofitting (including Euromap interfaces and plasticizing retrofits) and discover how to future-proof your machines for a competitive edge. With insights from industry experts, it'll walk you through the decision-making process, ensuring you make informed choices that drive your business forward. Agenda: Maximize the value of your current IMMs through strategic retrofitting Learn how to integrate digital technologies to enhance monitoring and control Explore the benefits of Euromap interfaces and plasticizing retrofits Understand how retrofitting can help meet new product demands and improve adaptability Discover how Engel can support your retrofitting needs, from free consultations to execution
While the melting process does not provide perfect mixing, this study shows that mixing is indeed initiated during melting.
This application also uses another critical enabling technology—rotating stack-type tooling. This job was made possible by the SpinStack tooling concept of Gram Technology. It uses a four-sided rotating center stack between the stationary and moving platens. The center stack indexes in 90° intervals. The turning mechanism and servo motors are contained within the mold assembly. The device is molded in three separate positions within the mold, with one position molding two of the four components.
technotrans says climate protection, energy efficiency and customization will be key discussion topics at PTXPO as it displays its protemp flow 6 ultrasonic eco and the teco cs 90t 9.1 TCUs.
The Plastics Industry Association (PLASTICS) has released final figures for NPE2024: The Plastics Show (May 6-10; Orlando) that officially make it the largest ever NPE in several key metrics.
In this collection of articles, two of the industry’s foremost authorities on screw design — Jim Frankand and Mark Spalding — offer their sage advice on screw design...what works, what doesn’t, and what to look for when things start going wrong.
“The invention of PEEK polymer has clearly had a very positive impact across industries and, in fact, across the globe. We could never have imagined the continuous stream of innovation this high performing versatile polymer would make possible. Visitors to the Victrex K 2019 show booth can look forward to pioneering new grades as well as exciting progress on forms and parts in critical applications where high performance polymers deliver a strong advantage in the development of new markets,” said Victrex CEO Jakob Sigurdsson.
Victrex CT polymers have also been shown to maintain better dimensional stability, with a lower coefficient of thermal expansion than incumbent materials. The higher thermal conductivity of the PEEK material enables a fast response to temperature changes, ensuring the material is engaged with the counter-surface at all times. In addition, laboratory testing indicates that they may require less torque to actuate since they have a lower static and dynamic coefficient of friction compared to PCTFE. This results in less wear, higher performance and a potential for cost savings.
Core Technology Molding turned to Mold-Masters E-Multi auxiliary injection unit to help it win a job and dramatically change its process.
Given decades of experience in delivering innovative PEEK thermoplastic solutions for the energy industry in both onshore and offshore oil and gas markets, Victrex understands the need for component reliability and efficiency in harsh environments. These requirements are especially relevant in wind energy which is currently faced with the critical challenge of reducing its Levelized Cost of Energy (LCOE). Reducing the LCOE requires the wind industry to design larger turbines to generate greater power output, improve reliability to reduce repair and maintenance costs and deploy turbines in remote and harsh offshore environments. These increasingly demanding turbine requirements are pushing the limits of metals and traditional polymer solutions.
MGS began building multi-shot tooling systems in the 1980s. “By the mid- to late ’90s, multi-shot had become such a driving force for our company that we found that sampling the molds was impacting our lead times,” says marketing director John Berg. “There simply was not enough open capacity in the market. Multi-material molding was definitely a specialty and very few molders had the equipment. A two-shot press was expensive and the lead times were long.” MGS recognized that multi-shot molding was an opportunity to differentiate itself and its customers, so it created its own processing equipment. By the early 1990s, MGS started developing its own rotary mold tables and add-on injection units to assist its own operations. These are now available for sale to other molders.
Multiple speakers at Molding 2023 will address the ways simulation can impact material substitution decisions, process profitability and simplification of mold design.
Across all process types, sustainability was a big theme at NPE2024. But there was plenty to see in automation and artificial intelligence as well.
Exhibitors and presenters at the plastics show emphasized 3D printing as a complement and aid to more traditional production processes.
As illustrated by the Hospira iSecure device, assemblies with moving parts appear to be an immediate area of opportunity for multi-shot IMA parts. MGS patented a valve with a polypropylene petcock molded into polycarbonate housing using MGS’s own tooling (see photo above). The petcock can rotate 360° inside the housing because the dissimilar materials do not bond to each other after molding. A third shot in this application applies a soft TPE seal that chemically bonds to the PC housing. The valve leaves the mold fully assembled.
▪ Aerospace: The next dimension of PAEK thermoplastic composites—The aircraft industry has forecast that more than 35,000 new aircraft will be required within the next 20 years. Meeting this kind of escalating demand clearly calls for new approaches and new technologies in aerospace engineering.
Processors with sustainability goals or mandates have a number of ways to reach their goals. Biopolymers are among them.
The award-winning all-thermoplastic drive-shaft for aircraft utilizes Victrex AE 250 PAEK unidirectional tape for the Organo Tube and gears and PEEK polymers in combination with innovative processing technologies.
Join this webinar to explore the transformative benefits of retrofitting your existing injection molding machines (IMMs). Engel will guide you through upgrading your equipment to enhance monitoring, control and adaptability — all while integrating digital technologies. You'll learn about the latest trends in IMM retrofitting (including Euromap interfaces and plasticizing retrofits) and discover how to future-proof your machines for a competitive edge. With insights from industry experts, it'll walk you through the decision-making process, ensuring you make informed choices that drive your business forward. Agenda: Maximize the value of your current IMMs through strategic retrofitting Learn how to integrate digital technologies to enhance monitoring and control Explore the benefits of Euromap interfaces and plasticizing retrofits Understand how retrofitting can help meet new product demands and improve adaptability Discover how Engel can support your retrofitting needs, from free consultations to execution
Join Engel in exploring the future of battery molding technology. Discover advancements in thermoplastic composites for battery housings, innovative automation solutions and the latest in large-tonnage equipment designed for e-mobility — all with a focus on cost-efficient solutions. Agenda: Learn about cutting-edge thermoplastic composites for durable, sustainable and cost-efficient battery housings Explore advanced automation concepts for efficient and scalable production See the latest large-tonnage equipment and technology innovations for e-mobility solutions
Formnext Chicago is an industrial additive manufacturing expo taking place April 8-10, 2025 at McCormick Place in Chicago, Illinois. Formnext Chicago is the second in a series of Formnext events in the U.S. being produced by Mesago Messe Frankfurt, AMT – The Association For Manufacturing Technology, and Gardner Business Media (our publisher).
In a time where sustainability is no longer just a buzzword, the food and beverage packaging industry is required to be at the forefront of this innovation. By adopting circular packaging processes and solutions, producers can meet regulatory requirements while also satisfying consumer demand and enhancing brand reputation. Join Husky to learn more about the broader implications of the circular economy — as well as how leading brands are leveraging this opportunity to reduce costs, increase design flexibility and boost product differentiation. Agenda: The cost and operational benefits of embracing circularity Key materials in circular packaging — including rPET and emerging bioplastics How to design a circular food and beverage package Strategies for selecting sustainable closures to future-proof packaging solutions Optimization and streamlining of production processes for enhanced efficiency How Husky Technologies can enable your sustainable success
Today, multi-shot molding accounts for 25% to 40% of the 300 to 400 molds it builds each year, as well as 20%, of the 2400 active tools used in its custom molding business. Last year, 65% of the firm’s $115 million revenues came from molding, 30% from moldmaking, and 5% from multi-shot equipment. MGS now has more than 600 employees in eight plants in the U.S. and Mexico.
Core Technology Molding turned to Mold-Masters E-Multi auxiliary injection unit to help it win a job and dramatically change its process.
August 29-30 in Minneapolis all things injection molding and moldmaking will be happening at the Hyatt Regency — check out who’s speaking on what topics today.
Hospira is a world leader in the specialty injectable pharmaceuticals market. It had little familiarity with multi-shot processes beyond two-shot molding with TPE seals. But Hospira knew that the previous method of producing the syringe needed to be upgraded. “In the past it didn’t matter how long it took to make the part, but now all aspects of medical molding are changing, and OEMs have to think smarter about their parts,” says Oshgan. Hospira looked at how part design could be changed to accomplish more manufacturing steps inside the mold. The company conducted extensive interviews with four molders and five toolmakers. “We went to these vendors to see what they had done before and what solutions they could propose,” says Oshgan.
The part is produced on a 300-ton KraussMaffei press. The clear body is molded first, then the plunger, and finally the living-hinge locking band and tamper-evident seal are molded simultaneously. The second and third shots are delivered by two MGS add-on injection units mounted vertically and on the non-operator side.
Join KraussMaffei for an insightful webinar designed for industry professionals, engineers and anyone interested in the manufacturing processes of PVC pipes. This session will provide a comprehensive understanding of the technology behind the production of high-quality PVC pipes: from raw material preparation to final product testing. Agenda: Introduction to PVC extrusion: overview of the basic principles of PVC pipe extrusion — including the process of melting and shaping PVC resin into pipe forms Equipment and machinery: detailed explanation of the key equipment involved — such as extruders, dies and cooling systems — and their roles in the extrusion process Process parameters: insight into the critical process parameters like temperature, pressure and cooling rates that influence the quality and consistency of the final PVC pipes Energy efficiency: examination of ways to save material and energy use when extruding PVC pipe products
While prices moved up for three of the five commodity resins, there was potential for a flat trajectory for the rest of the third quarter.
During its Mobility Days in Austria, Engel and KTM Technologies debuted an all-plastic molded motorcycle seat base produced via a tape-sandwich process that can run in a standard molding process.
Across the show, sustainability ruled in new materials technology, from polyolefins and engineering resins to biobased materials.
technotrans says climate protection, energy efficiency and customization will be key discussion topics at PTXPO as it displays its protemp flow 6 ultrasonic eco and the teco cs 90t 9.1 TCUs.
A breakthrough in the time- and cost-efficient production of complex aircraft parts was recognized with a JEC Innovation Award 2019 earlier this year, for an all-thermoplastic drive-shaft system overmolded with an integral gear that is set to advance the use of thermoplastic composites in aerospace. The OrganoTube and gears of the drive-shaft system are using Victrex AE 250 PAEK unidirectional tape (UDT) and PEEK polymers in combination with innovative processing technologies. This innovation is expected to open up enormous potential for reduced cycle times and large-scale industrial production.
The MGS Prototypes, Molds & Design (PMD) business group in Menomonee Falls builds injection, transfer, compression, thermoset, rubber, thermoforming, and cutting/trimming tools. Injection molds encompass single- and multi-shot designs, powdered-metal injection (MIM), liquid silicone rubber (LSR), and in-mold decorating (IMD). PMD produces multi-shot tooling with indexing cores or platens, as well as core-back and shut-off tooling, stack molds with robot transfer, and rotary-stack tools.
Ultradent's entry of its Umbrella cheek retractor took home the awards for Technical Sophistication and Achievement in Economics and Efficiency at PTXPO.
This Knowledge Center provides an overview of the considerations needed to understand the purchase, operation, and maintenance of a process cooling system.
Additive technology creates air pockets in film during orientation, cutting down on the amount of resin needed while boosting opacity, mechanical properties and recyclability.
This month’s resin pricing report includes PT’s quarterly check-in on select engineering resins, including nylon 6 and 66.
Any molder will tell you there’s a difference in working with electric vs. hydraulic drives. Servohydraulic is still hydraulic; a hybrid machine is something different. Imprecise use of terms causes needless confusion.
Another example is a small filter gasket for a blood analyzer that has three o-rings. “No way can it be made conventionally,” says Berg. “How to get the o-rings in place, and have no flash or part dimension issues narrows the technology choice.”
Gifted with extraordinary technical know how and an authoritative yet plain English writing style, in this collection of articles Fattori offers his insights on a variety of molding-related topics that are bound to make your days on the production floor go a little bit better.
Thousands of people visit our Supplier Guide every day to source equipment and materials. Get in front of them with a free company profile.
Mixed in among thought leaders from leading suppliers to injection molders and mold makers at the 2023 Molding and MoldMaking conferences will be molders and toolmakers themselves.
This month’s resin pricing report includes PT’s quarterly check-in on select engineering resins, including nylon 6 and 66.
Hospira designed the iSecure device to deliver a pre-measured dose of a drug. This is a four-piece, three-material assembly with a sliding part, a tamper-evident seal, and a living hinge. After shipment to Hospira, a prefilled drug cartridge is placed inside the clear PETG copolyester body of the iSecure device. The yellow LDPE component on the lower end of the device swings on a living hinge to lock the drug cartridge in place. The same yellow PP is molded into a separate tamper-evident band around the upper end of the syringe body. When that band is broken (by means of the prominent tab), the purple plunger of talc-filled polypropylene is free to slide along a track on the outside of the syringe body while simultaneously engaging an internal plunger inside the drug cartridge. This disposable product has a useful lifespan of “about 10 seconds,” says Robert Oshgan, Hospira senior tooling engineer. Yet the life of the application could span decades, encompassing hundreds of millions of units.
Cost-effective polymers, forms and parts for the automotive industry include Victrex’s thin Aptiv films and robust HPG gears.
MGS has a number of successful multi-shot applications that cannot be molded any other way, according to Berg. “Take a hand-held device with two lenses—there is no way to make it outside of multi-shot, because you would have to handle the lens, place it correctly and repeatedly, and bond it to the substrate. Ultrasonic welding would destroy the lens.”
While prices moved up for three of the five commodity resins, there was potential for a flat trajectory for the rest of the third quarter.
The tool was built under license from Gram by KTW Group in Austria. The rotating center stack has four cavities on each of its four faces. Cycle time is under 10 sec.
In this three-part collection, veteran molder and moldmaker Jim Fattori brings to bear his 40+ years of on-the-job experience and provides molders his “from the trenches” perspective on on the why, where and how of venting injection molds. Take the trial-and-error out of the molding venting process.
Join Engel in exploring the future of battery molding technology. Discover advancements in thermoplastic composites for battery housings, innovative automation solutions and the latest in large-tonnage equipment designed for e-mobility — all with a focus on cost-efficient solutions. Agenda: Learn about cutting-edge thermoplastic composites for durable, sustainable and cost-efficient battery housings Explore advanced automation concepts for efficient and scalable production See the latest large-tonnage equipment and technology innovations for e-mobility solutions
Additive technology creates air pockets in film during orientation, cutting down on the amount of resin needed while boosting opacity, mechanical properties and recyclability.
Across all process types, sustainability was a big theme at NPE2024. But there was plenty to see in automation and artificial intelligence as well.
Multiple speakers at Molding 2023 will address the ways simulation can impact material substitution decisions, process profitability and simplification of mold design.
Exhibitors and presenters at the plastics show emphasized 3D printing as a complement and aid to more traditional production processes.
Discover how artifical intelligence is revolutionizing plastics processing. Hear from industry experts on the future impact of AI on your operations and envision a fully interconnected plant.
The firm got into equipment manufacturing because it found that existing multi-shot machinery was too inflexible. After the initial job was done, “Future applications had to have the exact same screw and barrel location or that rather expensive equipment would become a white elephant,” says Bob Bordignon, director of business development. Soon after, the company developed its own solution, Universal Multishot (UMS) portable injection units that can be mixed and matched and moved to different locations for each job. Today, the company has evolved into a full-service provider of manufacturing solutions—engineering, design, tooling, sampling, development, production molding, value-added secondary operations, turnkey manufacturing systems, and automation systems. It has expanded into three core divisions, including toolmaking, equipment manufacturing, and parts production (see sidebar). MGS serves mainly consumer, medical, and electronics customers, but it also looks to grow in packaging, industrial, computer, automotive, telecommunications, and appliances.
Driven by brand owner demands and new worldwide legislation, the entire supply chain is working toward the shift to circularity, with some evidence the circular economy has already begun.
Victrex AE 250 composites have been shown to have mechanical, physical and chemical resistance properties typical of members of the polyaryletherketone (PAEK) polymer family such as PEEK, but with a 40°C (104°F) lower crystalline melting temperature, at only 305°C (581°F).
In this three-part collection, veteran molder and moldmaker Jim Fattori brings to bear his 40+ years of on-the-job experience and provides molders his “from the trenches” perspective on on the why, where and how of venting injection molds. Take the trial-and-error out of the molding venting process.
With its gears solutions, Victrex is enabling Tier 1/OEM customers to work with one partner, from concept to commercialization, who supports the development and testing of high-precision Victrex HPG gears, as well as the manufacturing of these gears as a component for integration into larger systems (e.g. within the engine, transmission, pump, actuator, and chassis).
Thousands of people visit our Supplier Guide every day to source equipment and materials. Get in front of them with a free company profile.
Plastics Technology’s Tech Days is back! Every Tuesday in October, a series of five online presentations will be given by industry supplier around the following topics: Injection Molding — New Technologies, Efficiencies Film Extrusion — New Technologies, Efficiencies Upstream/Downstream Operations Injection Molding — Sustainability Extrusion — Compounding Coming out of NPE2024, PT identified a variety of topics, technologies and trends that are driving and shaping the evolution of plastic products manufacturing — from recycling/recyclability and energy optimization to AI-based process control and automation implementation. PT Tech Days is designed to provide a robust, curated, accessible platform through which plastics professionals can explore these trends, have direct access to subject-matter experts and develop strategies for applying solutions in their operations.
Join Wittmann for an engaging webinar on the transformative impact of manufacturing execution systems (MES) in the plastic injection molding industry. Discover how MES enhances production efficiency, quality control and real-time monitoring while also reducing downtime. It will explore the integration of MES with existing systems, emphasizing compliance and traceability for automotive and medical sectors. Learn about the latest advancements in IoT and AI technologies and how they drive innovation and continuous improvement in MES. Agenda: Overview of MES benefits What is MES? Definition, role and brief history Historical perspective and evolution Longevity and analytics Connectivity: importance, standards and integration Advantages of MES: efficiency, real-time data, traceability and cost savings Emerging technologies: IoT and AI in MES
Plastics Technology’s Tech Days is back! Every Tuesday in October, a series of five online presentations will be given by industry supplier around the following topics: Injection Molding — New Technologies, Efficiencies Film Extrusion — New Technologies, Efficiencies Upstream/Downstream Operations Injection Molding — Sustainability Extrusion — Compounding Coming out of NPE2024, PT identified a variety of topics, technologies and trends that are driving and shaping the evolution of plastic products manufacturing — from recycling/recyclability and energy optimization to AI-based process control and automation implementation. PT Tech Days is designed to provide a robust, curated, accessible platform through which plastics professionals can explore these trends, have direct access to subject-matter experts and develop strategies for applying solutions in their operations.
Plastics Technology covers technical and business Information for Plastics Processors in Injection Molding, Extrusion, Blow Molding, Plastic Additives, Compounding, Plastic Materials, and Resin Pricing. About Us
The molding cell employs an innovative parts-removal concept that helps shorten cycle time. A cutout section of the mold base allows a Wittmann top-entry servo robot to take finished parts off of the cores while the mold remains closed during injection and cooling. Very precise robot movements are essential. MGS designed the end-of-arm tooling.
“If there is a new equipment or process technology on the market, we try it out and see how it works,” says Bordignon. We look to establish a learning curve of the new technology early on, so that when the prices for that technology come down and market interest grows, we are dialed in and have something ready to offer.”
Coverage of single-use plastics can be both misleading and demoralizing. Here are 10 tips for changing the perception of the plastics industry at your company and in your community.
After successfully introducing a combined conference for moldmakers and injection molders in 2022, Plastics Technology and MoldMaking Technology are once again joining forces for a tooling/molding two-for-one.
Expansion of Victrex’s PEEK portfolio ranges from 3D printing and films to composites, gear solutions and a food-grade family.
Clean-room and other medical applications are molded at MGS’ All West Plastics facility in Antioch, Ill. The plant has 21 presses in a Class 8 (100,000) clean room and a “white room” (not yet certified clean room).
Mixed in among thought leaders from leading suppliers to injection molders and mold makers at the 2023 Molding and MoldMaking conferences will be molders and toolmakers themselves.
Formnext Chicago is an industrial additive manufacturing expo taking place April 8-10, 2025 at McCormick Place in Chicago, Illinois. Formnext Chicago is the second in a series of Formnext events in the U.S. being produced by Mesago Messe Frankfurt, AMT – The Association For Manufacturing Technology, and Gardner Business Media (our publisher).
Leading-edge processing: The iSecure disposable medical syringe is a three-shot part with four components of three materials. It is molded in a complex tool with a four-sided rotary center stack in a sub-10-sec cycle. Photo shows two of MGS’s add-on injectors above and beside the mold. The servo robot demolds parts while the mold is closed through a special cutout in the mold base.
▪ Automotive: Driving innovation in powertrain—Cost-effective polymers, forms and parts for the automotive industry include the tribologically optimized Victrex PEEK polymer, thin Aptiv films and robust Victrex HPG high precision gears. Together, says Victrex, they contibute greater CO2 efficiency and improved durability, as well as a potential reduction in total system cost in conventional, hybrid, and electrical powertrains.
Processors with sustainability goals or mandates have a number of ways to reach their goals. Biopolymers are among them.
Mike Sepe has authored more than 25 ANTEC papers and more than 250 articles illustrating the importance of this interdisciplanary approach. In this collection, we present some of his best work during the years he has been contributing for Plastics Technology Magazine.
Though it grabs a lot of headlines, multi-material, multi-shot processing still makes up only about 10% of injection molding activity in North America.
Second quarter started with price hikes in PE and the four volume engineering resins, but relatively stable pricing was largely expected by the quarter’s end.
While the melting process does not provide perfect mixing, this study shows that mixing is indeed initiated during melting.
Ultradent's entry of its Umbrella cheek retractor took home the awards for Technical Sophistication and Achievement in Economics and Efficiency at PTXPO.
While prices moved up for three of the five commodity resins, there was potential for a flat trajectory for the rest of the third quarter.
Take a deep dive into all of the various aspects of part quoting to ensure you’ve got all the bases—as in costs—covered before preparing your customer’s quote for services.
Aptiv films reportedly deliver all the benefits of PEEK polymer in a thin format and so provide the versatility and high-performance needed to address complex demands for a variety of electronic devices.
In this collection, which is part one of a series representing some of John’s finest work, we present you with five articles that we think you will refer to time and again as you look to solve problems, cut cycle times and improve the quality of the parts you mold.
Coverage of single-use plastics can be both misleading and demoralizing. Here are 10 tips for changing the perception of the plastics industry at your company and in your community.
Introduced by Zeiger and Spark Industries at the PTXPO, the nozzle is designed for maximum heat transfer and uniformity with a continuous taper for self cleaning.
Discover how artifical intelligence is revolutionizing plastics processing. Hear from industry experts on the future impact of AI on your operations and envision a fully interconnected plant.
Second quarter started with price hikes in PE and the four volume engineering resins, but relatively stable pricing was largely expected by the quarter’s end.
In addition, with the adoption of Industry 4.0 technology, PEEK can offer manufacturers the opportunity to optimize efficiency and also reduce production costs, when compared to the use of metals, as these may require costly multi-step machining to manufacture. Applications on display at K 2019 will include Victrex PEEK injection molded bushing, bearings, and scroll compressors as well as dryer conveyer belts using PEEK-based Zyex fibers.
Resin supplier Celanese turned to startup Rafinex and its Möbius software to optimize the design for an engine bracket, ultimately reducing weight by 25% while maintaining mechanical performance and function.
While the major correction in PP prices was finally underway, generally stable pricing was anticipated for the other four commodity resins.
Resin drying is a crucial, but often-misunderstood area. This collection includes details on why and what you need to dry, how to specify a dryer, and best practices.
Resin drying is a crucial, but often-misunderstood area. This collection includes details on why and what you need to dry, how to specify a dryer, and best practices.
Plastics Technology covers technical and business Information for Plastics Processors in Injection Molding, Extrusion, Blow Molding, Plastic Additives, Compounding, Plastic Materials, and Resin Pricing. About Us
The Plastics Industry Association (PLASTICS) has released final figures for NPE2024: The Plastics Show (May 6-10; Orlando) that officially make it the largest ever NPE in several key metrics.
Still, taking such a radically new approach was a “huge leap of faith” for Hospira. “Good communication is mandatory on a program that pushes molding technologies to the limit like this one,” says Berg. “The emphasis was on getting all vendors involved early in the development process.” MGS developed a single-cavity prototype tool that showed what the IMA process could do.
August 29-30 in Minneapolis all things injection molding and moldmaking will be happening at the Hyatt Regency — check out who’s speaking on what topics today.
Introduced by Zeiger and Spark Industries at the PTXPO, the nozzle is designed for maximum heat transfer and uniformity with a continuous taper for self cleaning.
Successfully starting or restarting an injection molding machine is less about ticking boxes on a rote checklist and more about individually assessing each processing scenario and its unique variables.
In this collection of articles, two of the industry’s foremost authorities on screw design — Jim Frankand and Mark Spalding — offer their sage advice on screw design...what works, what doesn’t, and what to look for when things start going wrong.
▪ Electronics: Aptiv films for advanced performance in next-generation electronic devices.—As 'high tech' continues to advance, the trend is to electronic devices that offer improved performance and reliability in new and lighter form factors, while packed with a range of features. Aptiv films reportedly deliver all the benefits of high-performance PEEK polymer in a thin format and so provide the versatility and high performance required to address customers' complex demands for a variety of devices in this fast-moving market. The benefits of Aptiv film include: proven mechanical strength; resistance to wear, high temperatures and harsh chemicals; and electrical stability and low moisture absorption. These outstanding attributes mean that Aptiv film can be applied in a wide range of products, such as micro speakers, 5G RF antenna substrates, and battery insulation, and also in chip and display manufacturing.
Learn about sustainable scrap reprocessing—this resource offers a deep dive into everything from granulator types and options, to service tips, videos and technical articles.
In the food and beverage industry, developing the next generation manufacturing equipment is a particularly complex challenge. Companies are facing numerous requirements for health, safety and hygiene established by regulatory authorities, the industry and consumers. To help OEMs meet these demands, Victrex has introduced a dedicated food grade portfolio. Compared to metals, the Victrex FG family of high-performing PEEK thermoplastics offers additional benefits in terms of productivity and performance for OEMs.
GETTING A QUOTE WITH LK-MOULD IS FREE AND SIMPLE.
FIND MORE OF OUR SERVICES:
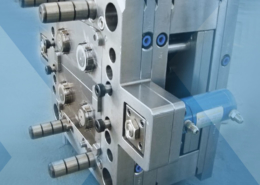
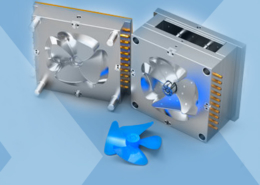
Plastic Molding

Rapid Prototyping
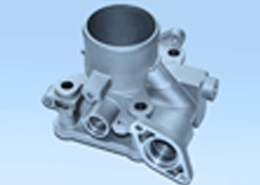
Pressure Die Casting
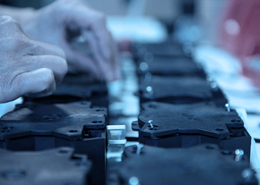
Parts Assembly
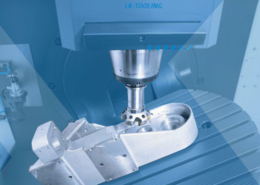