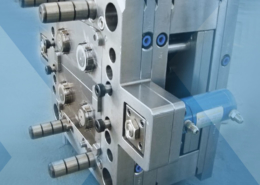
Injection Molding of Thin-Walled rPET Cups Is Now Possible - engel injection mou
Author:gly Date: 2024-09-30
The company initially purchased a nine-acre land in the evolving economic hub from the Brooks Development Authority in October 2016.
The demand for competitively priced medium to large scale production equipment is expected to grow in the US, with an increasing amount of manufacturing companies seeking local production capabilities.
Other major benefits include improved customer satisfaction with quick response times, reduced waiting times and faster delivery.
The air base was considered an ideal location for the plant for three main reasons, including San Antonio’s geographical location in the middle of North and South America, which will allow the company to address increasing demand in both regions.
The $20m facility is Nissei Plastic’s third manufacturing facility outside Japan, following two other plants in Taicang, China, and Rayong, Thailand, which were launched in 2009 and 2012 respectively.
“The integration of F&S Tool’s talented teams and market-leading innovation capabilities combined with Berry’s global operations reinforces the company’s commitment to providing customers across the globe with access to its industry-leading range of products in core markets while offering the benefits of local service and speed,” said Berry Global CEO Kevin Kwilinski in a prepared statement.
Nissei’s San Antonio plant will begin manufacturing moulding machines of the highest quality and reliability standards in a later phase.
The products will be branded as Made in USA and Made by Nissei products and will be supplied to Central and South America, US and Canada.
The facility manufactures and sells plastic injection moulding machines and related equipment to the US market, which is the company’s second-biggest export market after China.
The combination of a vast selection of tooling with Berry Global’s regionally-based knowledge offers customers a competitive advantage by providing faster turnaround from start to finish and greater assurance that the molds will fit its production lines, said the company in the news release.
San Antonio has also attracted a number of automobile manufacturing companies and is in close proximity to both the Midwestern US and Mexico, where automotive manufacturing clusters are located.
The self-described global leader in sustainable plastic packaging operates more than 11 tooling manufacturing locations across the world. With this acquisition, Berry’s customers will have access to a full suite of tooling capabilities, including injection, blow, compression, and thermoforming molds that can be integrated into their existing product orders.
The company’s wholly owned US-based subsidiary constructed a new injection moulding machine manufacturing plant in south San Antonio, Texas, US.
Packaging giant Berry Global Group Inc. has added to its portfolio F&S Tool, a specialized provider of high-output, high-efficiency hot-runner injection and high-volume compression molding applications.
Japanese plastic injection moulding machine manufacturer Nissei Plastic Industrial launched a new subsidiary named Nissei Plastic Machinery America in December 2016 as part of its growth strategy, which aims to boost the company’s global production and distribution network.
Japanese plastic injection moulding machine manufacturer Nissei Plastic Industrial launched a new subsidiary named Nissei Plastic Machinery America in December 2016 as part of its growth strategy, which aims to boost the company’s global production and distribution network.
The demand is expected to see a steady growth, especially in major categories such as packaging, daily goods, household products and automobiles.
F&S Tool operates a 90,000-square-foot facility in Erie, PA, with 11 issued or pending patents. Just over 100 employees serve a broad spectrum of plastics manufacturers. Founded in 1983, F&S Tool cites packaging, medical, and closures as core applications.
Berry said this acquisition will further enhance its global tooling capabilities as well as bring proprietary technologies in the closures and bottles space, specifically targeting high-end growth markets.
The plan also included the construction of a new technical centre, which is equipped with demonstration machines for moulds and materials in order to provide technical assistance to customers.
An on-site inventory will also enhance customer service and facilitate shorter lead-times as orders will no longer have to be shipped from Japan.
The Texas Department of Licensing and Regulation reported that the plant was designed by Atlanta-based design firm Appleby + Laccetti Architects.
Construction of the new manufacturing facility started in December 2016 and was completed in February 2018. The plant commenced operations in March 2018.
The main components for the assembly are supplied from the company’s manufacturing plants in Japan, Thailand and China, while procurement from local suppliers is slated to be increased gradually.
The Informa Markets Engineering network of B2B media sites includes Design News, Battery Technology, Medical Device & Diagnostic Industry (MD+DI), Packaging Digest, PlasticsToday, and Powder & Bulk Solids.
The plant is primarily involved in machining and the assembly of medium to large-scale hybrid injection moulding machines with clamping forces between 500 and 1,440 short tons.
GETTING A QUOTE WITH LK-MOULD IS FREE AND SIMPLE.
FIND MORE OF OUR SERVICES:
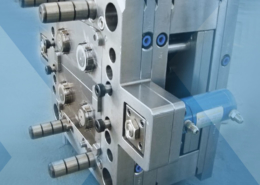
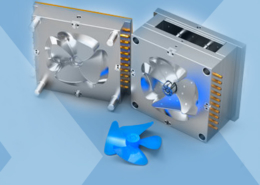
Plastic Molding

Rapid Prototyping
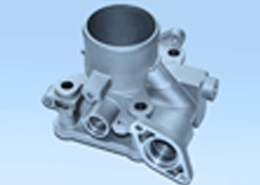
Pressure Die Casting
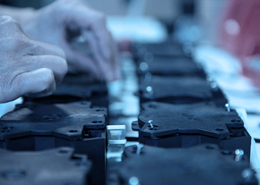
Parts Assembly
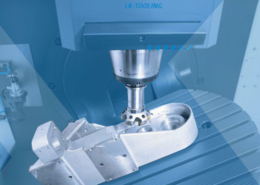