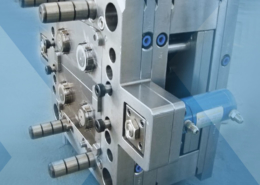
Injection Molding: Novel Injection Unit With In-Line Screw/Plunger - mini inject
Author:gly Date: 2024-09-30
Stephen has been with PlasticsToday and its preceding publications Modern Plastics and Injection Molding since 1992, throughout this time based in the Asia Pacific region, including stints in Japan, Australia, and his current location Singapore. His current beat focuses on automotive. Stephen is an avid folding bicycle rider, often taking his bike on overseas business trips, and a proud dachshund owner.
One standout application for mPP is injection-molded-film food packaging. This segment is another particular focus at supplier LyondellBasell. In an era where consumer safety and sustainability are paramount, the company’s Metocene grades are said to offer low odor, ensuring that taste and aroma of packaged food remain unaffected. This is a significant development for brands looking to maintain the organoleptic qualities of their products while reducing their environmental impact.
MPP initially found its niche in the spunbond and meltblown nonwoven textile market, especially in the production of hygiene products such as diapers and wipes. It allows finer denier fibers to be produced, meaning not only reduced material usage but also the production of more drapable and softer textiles. In combination with propylene-based elastomers such as Vistamaxx from ExxonMobil Chemical, even softer, higher-loft, drapable nonwoven textiles can be realized.
Since superglue is inexpensive and already produced on an industrial scale, we imagine our method of creating superglue plastics should be easy to scale up. Finally, the machinery used to make superglue could also be used to recycle the superglue plastics and could be simply adapted into existing industrial processes.
Allison Christy does not work for, consult, own shares in or receive funding from any company or organisation that would benefit from this article, and has disclosed no relevant affiliations beyond their academic appointment.
The way we make these plastics is relatively simple when compared with how other types of plastics are made – we simply mixed acetone and a little bit of an eco-friendly catalyst into store-bought superglue. Once this mixture dries, it produces a solid, glassy plastic made up of long polymer chains.
LyondellBasell reports that its Metocene metallocene solutions are sparking a renewed interest in the textile industry, not only because of their downgaging capability but also on account of their low odor characteristics, a feature that is considered paramount in more-comfortable and discreet hygiene products.
Further, mPP previously showed promise in sealant film applications but has since been outshined by materials such as Vistamaxx. There is, however, renewed interest in adoption in medical bags, where replacement of random PP copolymer and TPO materials is envisaged. Injection-molded medical device components are another potential outlet for mPP, as well as housewares and semiconductor transport trays.
Metallocene-catalyzed polypropylene (mPP) was developed around the same time as metallocene-based polyethylene (mPE), but sales of the two materials have been lopsided, with the mPE market perhaps 15 times larger. Nevertheless, mPP suppliers still hold hope that the resin will play a more prominent role in markets where purity and performance are priorities.
Coming to market around the same time as its polyethylene partner, metallocene-catalyzed polypropylene is playing a more subdued, yet important, role in niche applications.
Finding a replacement for polystyrene is a big step toward sustainable plastics, but polystyrene is only one of thousands of plastics used today. Our team is now designing superglue-based plastics with properties that resemble other kinds of commodity plastics, while still being easy to produce and recycle.
In our lab, we can easily produce up to 10 pounds of this material in a matter of days and turn it into usable products. By pouring the mixture into molds before it dries, we can make plastic objects in many shapes, like bowls and cutlery. We also discovered that heating up the plastic after it dries not only allowed us to shape the material into other products, but also strengthened the plastic.
Albeit a niche market, several mPP suppliers including Korea’s LG Chem and TotalEnergies have earmarked mPP as having further potential in automotive interior applications on account of its low odor, minimal emissions of volatile organic compounds (VOCs), and fogging characteristics. These attributes are welcome given the increasingly stringent regulation of VOCs in Europe and elsewhere. Previously, Japan Polypropylene also demonstrated the ability of its Welnex metallocene TPO to eliminate weld lines and realize excellent surface appearance in glass-fiber-reinforced automotive interior components.
Lane Lecture 2024: Delivering Occupational Health Research in Government: an important front line service? — Manchester, Manchester
While short polymers are good for glue, long polymers have more binding locations and result in stronger materials. Our team realized that if we could create longer versions of the same type of polymers made from superglue, we might be able to produce a strong plastic.
To make a plastic from superglue, we first had to address the very issue that makes superglue so “super” – it sticks to just about everything. When superglue is used to stick something together, it is actually reacting with moisture in the air or on the surface of whatever is being glued together. This reaction forms molecular chains of repeating superglue units called polymers. The polymers made when gluing something together are short and don’t bind to each other well, which makes the glue brittle and easy to break.
Socio-economic and regional inequality in health - inequality measurement and survey measurement of health — Southampton, Hampshire
In addition to its numerous advantages in terms of safety and sustainability, Metocene-based grades also reportedly excel in enhancing the aesthetics of packaging solutions in terms of exceptional clarity and transparency, providing excellent visibility of the contents inside. This feature, often referred to as "shelf visibility," not only allows consumers to see the product they're purchasing but also adds a touch of elegance to the packaging.
Furthermore, metallocene solutions can impart a glossy and brilliant finish to the packaging, making it even more appealing on store shelves. This aesthetic appeal serves as a compelling selling point for brands across various industries, aligning with the growing demand for visually pleasing and attractive packaging solutions.
LyondellBasell metallocene solutions also address concerns about the use of highly regulated substances. With no phthalates or bismethoxyfluorene being used during the production of the product, LyondellBasell provides food packaging manufacturers with an alternative.
Because our superglue plastic has properties similar to polystyrene – it is light, durable, cheap and easy to mass-produce – it could replace polystyrene in many products. But there are two distinct benefits of our superglue-based material: It isn’t made from oil and is easy to recycle.
When manufacturers need to produce a stiff plastic object – like cutlery, disposable razors, CD cases or plastic models – they often turn to polystyrene. Polystyrene is one of the most widely produced and least recycled types of plastic.
Our team used superglue as a starting material to develop a low-cost, recyclable and easily produced transparent plastic called polyethyl cyanoacrylate that has properties similar to those of plastics used for single-use products like cutlery, cups and packaging. Unlike most traditional plastics, this new plastic can be easily converted back to its starting materials, even when combined with unwashed municipal plastic waste.
When our material is heated to 410 degrees Fahrenheit (210 C), the long molecule chains made of repeating superglue units break apart into their small, individual superglue molecules. At this point, the superglue molecules turn into a vapor that is easy to separate out from a mixed waste stream of other plastics, paper, food residue, aluminum and other refuse commonly found in recycling waste streams. Once you collect the superglue vapor, you can cool it and turn it right back into our new plastic with over 90% efficiency.
GETTING A QUOTE WITH LK-MOULD IS FREE AND SIMPLE.
FIND MORE OF OUR SERVICES:
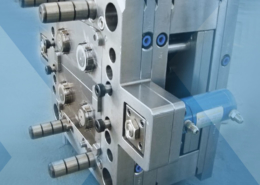
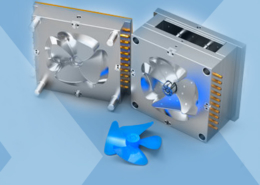
Plastic Molding

Rapid Prototyping
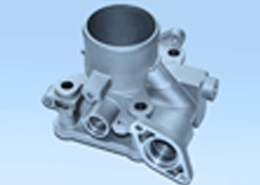
Pressure Die Casting
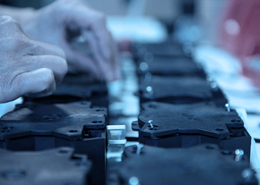
Parts Assembly
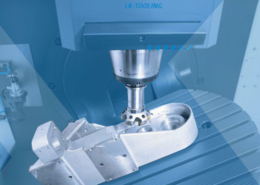