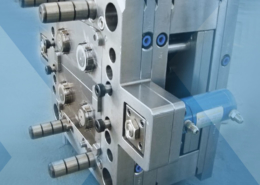
Injection Molding IPhone Cases From Trash - mini injection molding
Author:gly Date: 2024-09-30
A system of this type in a real-world application might be a bit of a stretch, but it is quite stunning to witness the metamorphosis of a plastic vial into a bottle opener in such an all-encompassing manner.
In October 2021, Recycler EFS-plastics Inc., a Canada post-consumer plastics recycler with a focus on processing bales of low-value plastics, acquired Exi-Plast Custom Moulding for an undisclosed amount. Through this acquisition, EFS can directly manufacture finished products with high levels of post-consumer recycled plastic for its customers. Exi-Plast Custom Moulding is a Canadian company that provides custom plastic molding services, particularly in blow-molded solutions for designers, manufacturers, and distributors.
KraussMaffei has set up a rather remarkable example of closed-loop circularity at booth 600 in the west hall at NPE2024.
The new facility offers a full-service mold prototyping lab as well as a specialized mold sample and development machine, allowing customers to quickly move from concept through design, prototype, and full production.
The vials are first molded using ExxonMobil PP 9074 MED on an all-electric PX 251-1400 injection molder. Thirty-two vials are produced per shot. For the purposes of this demonstration, the vials are transported to a grinder via the tubes and transformed into pellets in a matter of minutes.
Success stories at the seminar included the biodegradability of proprietary bioplastic material; biopolymer solutions for sustainable agriculture; and a method for measuring biodegradation in compost, fresh and waste waters, soil, and marine environments.
Blood-collection vials made from medical-grade polypropylene are injection molded on the show floor, transported via a series of what look like pneumatic tubes to a shredder, upcycled via a twin-screw extruder, processed with various additives, and injection molded anew to produce the bottle opener pictured here. The process is apparently seamless.
For the packaging sector, AIMPLAS presented results of projects that included biodegradable barrier packaging made from food waste, plastic film derived from coffee waste, active packaging that extends the shelf life of cheese and is made from cheese-industry waste, and cartridges for 3D food printing.
Editor in chief of PlasticsToday since 2015, Norbert Sparrow has more than 30 years of editorial experience in business-to-business media. He studied journalism at the Centre Universitaire d'Etudes du Journalisme in Strasbourg, France, where he earned a master's degree.
Asia-Pacific was the largest region in the blow-molded plastics market in 2021 and is expected to remain the largest through the forecast period.
The global blow-molded plastics market grew from $89.39 billion in 2022 to $92.93 billion in 2023 at a compound annual growth rate (CAGR) of 4.0%. The blow-molded plastics market is expected to grow to $108.75 billion in 2027 at a CAGR of 4.0%, according to a report published in February by Reportlinker. The market consists of sales coveringcompound blowmolding and compression blowmolding.
Watch the circular economy in action at booth W600 at NPE, running through May 10 at the Orange County Convention Center in Orlando, FL.
Companies are investing in research and development to produce new industrial plastics to keep up with market competitiveness and meet evolving end-user demands.
For instance, in 2020, Comar, a US manufacturer and designer of innovative plastic solutions, announced locating a custom facility in Rancho Cucamonga, CA. The 230,000-square-foot facility is Current Good Manufacturing Practice regulation (cGMP)-compliant, ISO 13485-certified, and FDA-registered, with dedicated injection blowmolding, injection-stretch blowmolding, and injection-molding cells.
Major types of blow-molded plastics are polypropylene, acrylonitrile butadiene styrene (ABS), polyethylene, polystyrene, polyvinyl chloride PVC, PET, and others. Polypropylene (also known as propane or propylene) is a tough, rigid, crystalline thermoplastic derived from the monomer propane or propylene.
Producing hollow plastic products from thermoplastic materials is a quick manufacturing solution and offers versatile products with broad industrial appeal. Markets include food suppliers, medical and pharmaceutical companies, and others.
Polypropylene is used in a variety of applications, including plastic packaging, machinery and equipment parts, and fibers and textiles. Extrusion, injection, and stretch are the various technologies used in blowmolding plastics for packaging, consumables, electronics, automotive and transport, building and construction, medical, and other applications.
They are then processed with a ZE 28 BluePower twin-screw extruder and, following the mixing and blending of adhesive and liquid color additives, the compound is sent to an all-electric PX 81-180 press, where the bottle opener is molded. The PX 81-180 is equipped with APCplus, which compensates for process fluctuations that may result from recyclates with different viscosities.
This allows components to be produced with consistently high quality and little waste, another important contribution to greater sustainability, said KraussMaffei.
GETTING A QUOTE WITH LK-MOULD IS FREE AND SIMPLE.
FIND MORE OF OUR SERVICES:
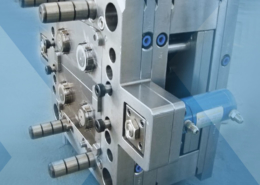
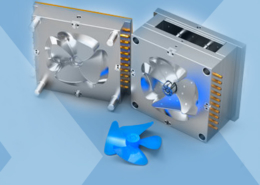
Plastic Molding

Rapid Prototyping
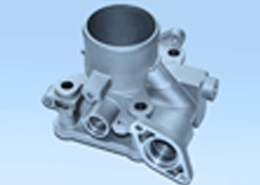
Pressure Die Casting
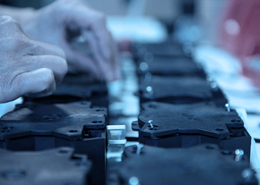
Parts Assembly
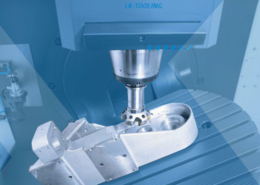