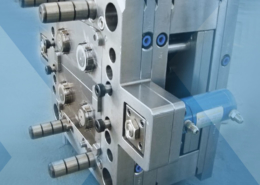
Injection Molding Guide: How to Improve Part Quality & Reduce Part Cost
Author:gly Date: 2024-09-30
In the meantime, Sabic expects incremental manufacturing process improvements at the Selkirk, New York, and Mt. Vernon plants to provide increases in Noryl PPE resin and Ultem PEI resin production by the end of 2018. The resulting supply gains will be used to meet growing demand and improve lead times for customers.
The global medical injection moulding market size was valued at $1.38 billion in 2019 and is expected to grow at a compound annual growth rate (CAGR) of 8.2% between 2020 and 2027. Much of this is being driven by advances in the home healthcare sector and an ageing population, which WHO predicts will double by 2050.
Gerard Henn, Avenue’s general manager, said: “All medical programmes are lengthy as it can take two to three years to obtain approvals from the authorities, so there are many months of testing before a component or mould is ready to be scaled up to mass production.”
Darren Herron, UK national sales manager at Sumitomo Demag, analyses the injection moulding market and what is driving new developments for medical applications.
“Increased customer demand, especially in Asia, prompted the further capacity expansion plans,”, said Ernesto Occhiello, Executive Vice President, Specialties, Sabic. “While interim capacity gains for both Ultem and Noryl resins have been achieved, global demand for both product lines has increased significantly, and Sabic is planning to expand its capacity to support our customers’ growth aspirations. We will continue to focus efforts to deliver the right capacity, in the right global locations, at the right time to support our customers’ needs.”
Advanced batch tracking, contact-free inspection using cameras, and highly automated assembly are among the latest developments to meet the medical device market’s precision and quality control requirements. Traceability is not just about mandatory information and supply chain tracking. Real-time traceability is about being able to call up data and verify the exact settings used on the injection moulding machine when that individual plastic part was made, making connectivity to a Management Executive System (MES) vital.
To enhance patient safety, there’s a drive towards using new and more innovative regulated materials with a better flow and high impact strength to mould components. The EU Medical Device regulations came into force 26 May 2021, following a one-year extension due to the pandemic. In Vitro Diagnostic medical device regulations (known as IVDR) become effective 26 May 2022. In the UK, the market is currently regulated by the UK Medicines and Healthcare products Regulatory Agency (MHRA).
This creates some complications in relation to the CE marking process on medical devices as the UKCA (UK Conformity Assessed) mark will replace the longstanding CE mark for goods, including medical devices, sold within England, Wales and Scotland. As there’s no hard border in Ireland, the CE mark still applies there.
For example, when parts are being produced on multi-cavity tools, like pipettes, robots are programmed to remove and place the components into cavity-assigned racks. This means that if an issue with cavity 1 arises, the rack containing all corresponding cavity 1 parts can be isolated and the rack recalled, with all the production information stored in the MES.
Sabic has announced projects in Asia and the Netherlands designed to increase global capacity for two of its high-performance engineering thermoplastic materials, Ultem polyetherimide (PEI) and Noryl polyphenylene ether (PPE) resins. To increase capacity for Ultem resins, Sabic plans to expand its existing footprint in Singapore where it currently has compounding operations. The planned new production facility in Singapore is expected to go online in the first half of 2021. The company also plans to recommission operations at its Bergen op Zoom PPE resin plant in the Netherlands by the end of 2019 to produce (PPE, the base resin for its line of Noryl resins and oligomers.
Sumitomo (SHI) Demag recently supplied a 75 tonne IntElect all-electric injection moulding machine to Avenue, a Nolato Company, in Sligo, Ireland. The investment supports the growth in the company’s healthcare division, providing dedicated capacity to mould precision parts during the product development phase. With demand for its medical device injection moulding and tool-building services increasing, Avenue recently installed a new 100 sqm ISO Class 8 cleanroom area.
Stephen has been with PlasticsToday and its preceding publications Modern Plastics and Injection Molding since 1992, throughout this time based in the Asia Pacific region, including stints in Japan, Australia, and his current location Singapore. His current beat focuses on automotive. Stephen is an avid folding bicycle rider, often taking his bike on overseas business trips, and is a proud dachshund owner.
With a large proportion of Sumitomo (SHI) Demag’s Irish customers in the medical market in Ireland, we last year opened a service and support office in Limerick, Ireland. This was to support its installed base of predominantly all-electric machines, providing on-the-ground preventative and reactive machine maintenance and troubleshooting support.
Establishing an Irish office is also part of a post-Brexit insulation strategy that will moderate any potential concerns Irish moulders may have about dealing with a UK machinery supplier. A permanent in-country service and support base will facilitate timely spare parts sourcing and trading in euros without incurring hefty exchange fees. We firmly believe that Ireland’s talent base and this supportive infrastructure will continue to make Ireland very attractive to inward investment, especially in medical and biotechology R&D.
The IntElect machine met Avenue’s brief for a small footprint machine for carrying out test runs during the development phase of projects.
Expansion of footprint in Singapore will localize Ultem resin production in Asia, increasing global production by 50%; recommissioning of Noryl resin manufacturing operations in Bergen op Zoom expected to increase global production more than 40%.
The machine’s small footprint is down to the use of its own motors and drives. The model also has wide tie bar spacing and high clamp force for its size, allowing the use of larger moulds than would normally be accommodated by a 75-tonne machine.
Ultem resins are currently produced in two locations, Mt. Vernon, Indiana, and Cartagena, Spain. The planned operations in Singapore will localize supply for customers in Asia, reducing lead times, especially for shorter qualification cycle applications. When fully operational, the Singapore facility is expected to increase capacity by 50% over a 2018 baseline. “With the addition of Singapore, Sabic will be the only petrochemical company with the ability to produce the high heat resin in Asia, the Americas and Europe, a significant advantage for the company’s customers,” Occhiello noted.
The decision to recommission the Bergen op Zoom Noryl resins facility provides customers with a second source of PPE resins globally, and affirms Sabic’s commitment to the European market and global customers who specify their material solution needs from Europe. When operational, the Bergen op Zoom facility is expected to add more than 40% global capacity over a 2017 baseline.
Plastic moulding continues to be used for many medical applications, including manufacturing implantable medical device components, test tubes, beakers, casings and housings for laboratory and medical equipment, drug delivery components and surgical equipment. With demand for medical devices at an all-time high across hospitals and laboratories thanks to COVID-19, this has had a positive impact on market growth.
GETTING A QUOTE WITH LK-MOULD IS FREE AND SIMPLE.
FIND MORE OF OUR SERVICES:
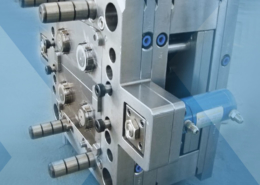
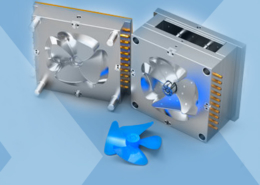
Plastic Molding

Rapid Prototyping
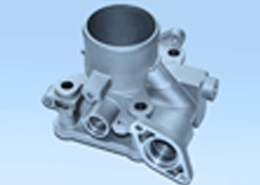
Pressure Die Casting
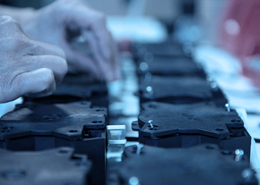
Parts Assembly
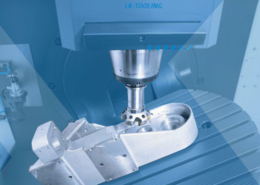