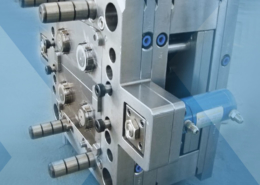
Unveiling the Potential of Rapid Injection Molding: Shaping the Future of Manufa
Author:gly Date: 2024-06-08
In the dynamic landscape of manufacturing, rapid injection molding emerges as a disruptive force, offering unparalleled speed, flexibility, and cost-effectiveness in the production of high-quality plastic components. This article explores the realm of rapid injection molding, delving into its applications, advantages, challenges, and future prospects.
The Rise of Rapid Injection Molding
Rapid injection molding represents a paradigm shift in traditional manufacturing processes, leveraging advanced technologies to accelerate product development cycles and streamline production workflows. Unlike conventional injection molding methods that entail lengthy lead times and high tooling costs, rapid injection molding enables swift prototyping and low-volume production without sacrificing quality or precision.
The advent of digital design tools, such as computer-aided design (CAD) software and simulation technologies, has revolutionized the product development process, allowing manufacturers to iterate designs rapidly and validate concepts before proceeding to production. This iterative approach minimizes time-to-market and empowers businesses to respond swiftly to market demands and consumer feedback.
Advantages of Rapid Injection Molding
The allure of rapid injection molding lies in its myriad advantages, ranging from accelerated production timelines to cost-efficient prototyping and customization capabilities. By leveraging rapid tooling techniques, such as 3D printing and aluminum molds, manufacturers can significantly reduce lead times and tooling costs compared to traditional methods, enabling faster market entry and reduced upfront investment.
Moreover, rapid injection molding facilitates on-demand production and mass customization, allowing manufacturers to tailor products to specific customer requirements and market segments without incurring exorbitant costs or production delays. This agility and flexibility are particularly valuable in industries characterized by rapid technological advancements and changing consumer preferences, such as consumer electronics and automotive.
Challenges and Considerations
Despite its myriad benefits, rapid injection molding poses certain challenges and considerations that manufacturers must navigate to maximize its potential. These include material selection, part complexity, and scalability issues, as well as the need for robust quality control measures to ensure consistency and reliability in mass production.
Material selection plays a critical role in rapid injection molding, with manufacturers balancing performance requirements, cost constraints, and compatibility with rapid tooling techniques. Additionally, the complexity of parts and geometries may pose challenges in terms of mold design, cooling efficiency, and ejector pin placement, necessitating careful consideration and optimization to achieve optimal results.
Future Directions and Opportunities
Looking ahead, rapid injection molding is poised to play an increasingly prominent role in the manufacturing landscape, fueled by advancements in materials science, digital technologies, and automation. The integration of artificial intelligence, machine learning, and robotics holds promise for further enhancing efficiency, quality, and scalability in rapid injection molding processes.
Furthermore, the convergence of rapid injection molding with sustainable materials and circular economy principles presents new opportunities for eco-friendly manufacturing practices and closed-loop supply chains. By embracing sustainable alternatives to traditional plastics and optimizing production processes for minimal waste and energy consumption, manufacturers can reduce environmental impact while meeting growing consumer demand for eco-conscious products.
Conclusion:
In conclusion, rapid injection molding stands as a transformative force in modern manufacturing, offering agility, efficiency, and customization capabilities that drive innovation and competitiveness. By harnessing advanced technologies, addressing challenges, and seizing emerging opportunities, manufacturers can unlock the full potential of rapid injection molding, shaping the future of manufacturing and fueling economic growth in the years to come.
GETTING A QUOTE WITH LK-MOULD IS FREE AND SIMPLE.
FIND MORE OF OUR SERVICES:
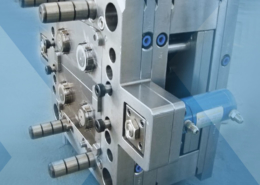
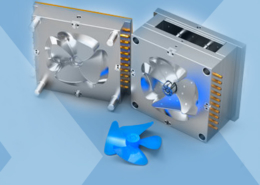
Plastic Molding

Rapid Prototyping
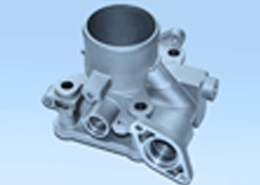
Pressure Die Casting
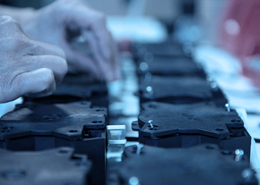
Parts Assembly
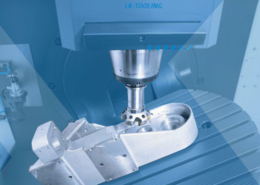