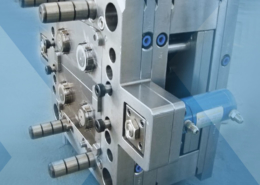
Injection molding class teaches valuable lessons in mass production - plastic in
Author:gly Date: 2024-09-30
The company now has 20 employees and is "looking to bring on or two more," Gaglianese said. Six months ago, East Pattern moved from two buildings on Saginaw Drive in Henrietta to one consolidated facility on North Main Street in Fairport. The company occupies 23,000 square feet, about half the space in the building, Gaglianese said.
East Pattern's molding capabilities include injection molding, insert molding and reaction injection molding, or RIM. Thefreedictionary.com defines RIM as a "process in which two streams of highly reactive, low-molecular-weight, low-viscosity resin systems are combined to form a solid material." Gaglianese described the procedure as "two chemicals coming together to make stronger plastics."
East Pattern & Model Corp. started a year before the movie The Graduate came out. There are similarities, so bear with us.
Husky currently produces hot runners and controllers on three continents in more than 54,000 square meters of manufacturing space. Additional investments are planned for hot runner manufacturing in its U.S. and China facilities. Husky’s goal is to be the industry’s first choice for melt delivery systems, as seen by its innovative approach to reducing sources of waste and variability in the injection molding process.
That process makes for thicker plastic products, Gaglianese said. Car bumpers and dashboards are among the products made via RIM at East Pattern, he said, as well as a rifle frame for Crosman Corp.
Thermoplastic injection molding is used for items ranging from small medical components to large heating-ventilation-air conditioning components. Insert molding is a process in which parts like electromechanical components and filtration materials are molded over bushings — essentially, linings — and combined into a single component. That process results in lower costs, reduced size and weight, and increased reliability, according to the industry's trade publications.
Until she retired in September 2021, Clare Goldsberry reported on the plastics industry for more than 30 years. In addition to the 10,000+ articles she has written, by her own estimation, she is the author of several books, including The Business of Injection Molding: How to succeed as a custom molder and Purchasing Injection Molds: A buyers guide. Goldsberry is a member of the Plastics Pioneers Association. She reflected on her long career in "Time to Say Good-Bye."
East Pattern also has computer-controlled automated machine tools like mills and lathes for production parts, prototypes and tooling. The company provides "downstream machining" on molded components and does finishing work for customer castings. The in-house moldmaking provides customers speed and flexibility to develop projects and make engineering changes with high levels of control at the lowest possible cost, according to the company website.
The company also makes its own tooling, provides secondary assembly and helps customers with design, prototypes and product development.
“As our global customer base for hot-runner and controller systems continues to grow so does the complexity of the molded parts for which we help find solutions,” said Stafano Mirti, Husky’s President of Hot Runners and Controllers. “I’m very excited about where we are taking our business and how this significant technology investment will enable us to support our customers and help them to grow their businesses. Our new manufacturing line will enable shorter lead times and provide even more capability to produce highly repeatable manifolds of the best quality.”
Executives: The company owners are Warren and Michelle Kellogg and Mark Landers. Warren Kellogg is president; Michelle Kellogg, Landers and Rosario Gaglianese are vice presidents.
RIM tooling is much cheaper than injection molding, so large products can be launched more quickly and less expensively. RIM is the top choice for high-temperature resistance and insulation applications, according to East Pattern, and is used for foam in seating for vehicles like motorcycles, all-terrain vehicles, tractors and snowmobiles.
A character in the 1967 movie tells Dustin Hoffman's character about a great future in plastics. East Pattern founder Warren Kellogg heeded the advice.
East Pattern started as a foundry, where metal is melted and poured into molds, back in 1966. Kellogg soon switched over to injection molding to complement the existing business. As the company website states, "He sensed that plastic was the direction the industry was moving."
Kellogg, East Pattern's president as well as founder, was a pattern maker at Gleason Works when he got the idea to start his own company, Gaglianese said. He's never looked back.
"We make plastic parts for Xerox that go into copiers," said Rosario Gaglianese, East Pattern's vice president of operations. "We make plastic parts for the medical field."
Husky Injection Molding Systems (Bolton, ON, Canada), a global provider of injection molding technology, equipment and services to the plastics industry, announced that a state-of-the-art, automated manufacturing line is now in operation at its Luxembourg facility. This is the third straight year that Husky has made a significant investment in new manufacturing equipment to support its growing base of hot runner and controller customers. In January of this year, Husky began producing hot-runner manifolds on one of the most advanced automated manufacturing lines in the industry, said Husky’s release.
GETTING A QUOTE WITH LK-MOULD IS FREE AND SIMPLE.
FIND MORE OF OUR SERVICES:
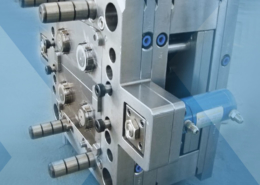
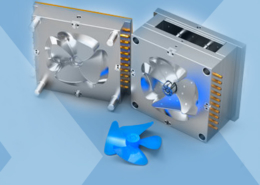
Plastic Molding

Rapid Prototyping
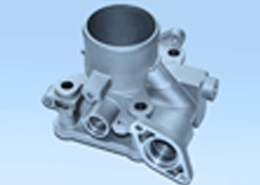
Pressure Die Casting
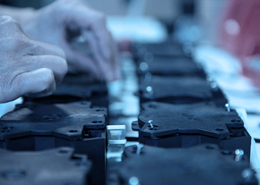
Parts Assembly
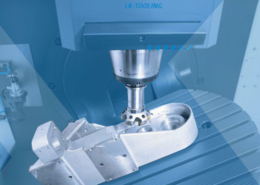