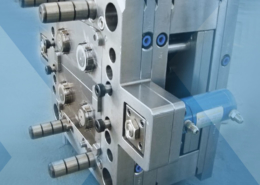
Injection Molding Cell Creates Plastic Beverage and Food Can Covers - soft plast
Author:gly Date: 2024-09-30
Arburg is exploring the theme of mass customization with its “Industry 4.0” exhibit, in which individualized toy buggies are produced in a series of independent stations networked by an Arburg ALS host-computer system, recording all the parameters and transmitting them to a web server. The process starts with a personalized chip card that is read by the cell’s Selogica control system. In the following cycle, the corresponding buggy is molded and an individual code is laser marked on its roof. A Multilift Select linear robot removes and assembles the buggy. The product is then checked for correct operation, and the code can be read by a mobile device to give access to all process data for 100% traceable production.
More dramatically, Milacron will also demonstrate the oPTI process for foam/solid preforms developed by Plastic Technologies Inc. (PTI). Using a rotating 2 x 4-cavity cube mold from Foboha of Germany, a Ferromatik Milacron K-Tec 200 Cube two-component press (200 m.t.) will mold foamed preforms using the MuCell process. After a 90° turn of the cube, the foam layer is sheathed with a solid outer layer by a second injection unit. Cycle time is 25 sec. The foamed layer produces a decorative metallic or pearlescent effect after blow molding, without pigments, thus preserving recyclability. Milacron, Foboha, and PTI recently joined in a partnership to commercialize oPTI bottles.
Oerlikon HRSflow showcased the special PCR-ready hot runners in two applications—a fruit crate and household compost bin—with the crate molded at K 2022 by Haitian.
In this three-part collection, veteran molder and moldmaker Jim Fattori brings to bear his 40+ years of on-the-job experience and provides molders his “from the trenches” perspective on on the why, where and how of venting injection molds. Take the trial-and-error out of the molding venting process.
• From Sumitomo (SHI) Demag comes a new version of its flagship SE-EV all-electric model. New “high-duty” (HD) models are designed specifically for thicker parts that require longer and higher pack/hold pressures (see February Keeping Up).
This Knowledge Center provides an overview of the considerations needed to understand the purchase, operation, and maintenance of a process cooling system.
For reliable performance, a slimline design and an unbeatable price, there is only one choice: the new ALLROUNDER 720 E GOLDEN ELECTRIC!
In this collection, which is part one of a series representing some of John’s finest work, we present you with five articles that we think you will refer to time and again as you look to solve problems, cut cycle times and improve the quality of the parts you mold.
Hot-runner exhibits are dominated by valve gates. Here, Incoe’s compact HEM hydraulic cylinder allows 50% closer spacing of gates.
Exhibitors and presenters at the plastics show emphasized 3D printing as a complement and aid to more traditional production processes.
Mike Sepe has authored more than 25 ANTEC papers and more than 250 articles illustrating the importance of this interdisciplanary approach. In this collection, we present some of his best work during the years he has been contributing for Plastics Technology Magazine.
The new MD110S7000 is a horizontal version with FDA-approved grease supply system suitable for medical cleanroom and food-grade applications. Eliminating lower side tiebar bushings on the moving platens improves cleanliness of the part-drop area. High nozzle touch force (similar to a hydraulic machine) now can be dialed down when appropriate for longer sprue-bushing life.
In this collection of content, we provide expert advice on welding from some of the leading authorities in the field, with tips on such matters as controls, as well as insights on how to solve common problems in welding.
There will be more liquid silicone rubber exhibits than ever this year, several of them involving two-component molding. In addition to the Wittmann Battenfeld two-component LSR medical micromolding demonstration mentioned above, two firms will demonstrate overmolding LSR onto thermoplastics. Arburg will overmold LSR onto PBT to produce suction pads in an electric Allrounder 570 A with a 4+4 cavity mold from Rico Elastomere of Austria. An Arburg Mutlilift Select robot will transfer parts from the PBT to the LSR cavities in the mold. Cycle time is around 40 sec.
Another hot ticket at this show will be multilayer coinjection for barrier packaging—whether gas barrier for retorted, shelf-stable foods and carbonated or oxygen-sensitive beverages; or light barrier for milk. Milacron, which acquired both Mold-Masters and Kortec technologies for coinjection, will demonstrate the Kortec (now called Milacron Co-Injection) Klear Can system on a Ferromatik 280 machine with Mold-Masters E-Multi secondary injection unit and Kortec multichannel nozzle for three-layer barrier packages. Milacron will also show a coinjection setup on its new Ferromatik 580 machine.
• Alba Enterprises will show the new DN5/3 multi-tip nozzles for balanced filling of long, tubular parts, which comes from Thermoplay of Italy (see February Keeping Up).
And KraussMaffei will mold a polycarbonate panel for a coffee machine incorporating both glossy and matte surfaces using MuCell and Roctool technologies.
In this collection of articles, two of the industry’s foremost authorities on screw design — Jim Frankand and Mark Spalding — offer their sage advice on screw design...what works, what doesn’t, and what to look for when things start going wrong.
• CBW Automation will debut the SSE side-entry robot with a strip stroke added, so it can handle more complex mold and part geometries and undercuts. It also allows the robot to follow the motion of the mold for unscrewing or more complex ejection sequences. This super-fast model has an intrusion time of less than 0.5 sec and can recognize that vacuum has been achieved in as little as 60 millisec.
AGS Automation Greifsysteme Schwope of Germany will show something unusual—a weighing system that mounts on the robot EOAT to detect short or damaged parts or missing inserts during the cycle. The quick-disconnect measuring cell has resolution of 0.33 g.
At Fakuma 2023, an ALLROUNDER MORE 2000 with two electric injection units will demonstrate how functional integration can save time and costs in multi-component injection moulding.
Another cell for in-mold assembly of a closure/cap with molded-in gasket and septum/stopper will be demonstrated by MGS Mfg. Group. Using a KraussMaffei CX 160 hybrid press and a Husky three-shot, valve-gate hot runner, MGS will add its new vertical-mount UMS E Micro servo injection unit with 8-mm screw and horizontal-mount (non-operator side) UMS Micro 10M hydraulic injection unit with 8-mm screw for the TPE gasket and septum. Also part of the system is the new MGS servo-driven rotary platen with four stations, 90° rotation increments, and indexing time of <0.8 sec. MGS also supplies a single integrated controller and operator interface for the two auxiliary injectors, turntable, and hot runner.
Also new to the U.S. is the GXH multicomponent press. A GHX 550 at NPE will mold two-component covers for automotive fog lights. The “H” indicates multiple injection units arranged horizontally in parallel.
Here’s a view from the trenches of a tooling manager who, over 30 years, has experienced the joys and pains of using virtually every type of hot runner on the market. Part 2.
The 1.3-g HDPE caps with tamper-evident band molded with mechanical slides will run in 96 cavities on a 472-ton El-Exis SP hybrid press (below) with a barrier screw.
Multi-material molding with in-mold assembly will be featured for medical and packaging applications. Engel will show a complex cell that also ran at K 2013, making drip chambers with an integrated filter for blood transfusions. An Engel e-victory 310H combi three-component, tiebarless, servo-hydraulic machine with cleanroom design will simultaneously produce drip-chamber components in ABS and PP, insert the filter, and join the components by overmolding more PP at the seam. It’s a more efficient process for producing hollow bodies with inlays than conventional molding of the two parts and adding the inlay and bonding the assembly in secondary operations. An Engel easix articulated robot handles the filters and assemblies and performs a 100% quality check.
Gifted with extraordinary technical know how and an authoritative yet plain English writing style, in this collection of articles Fattori offers his insights on a variety of molding-related topics that are bound to make your days on the production floor go a little bit better.
Additive technology creates air pockets in film during orientation, cutting down on the amount of resin needed while boosting opacity, mechanical properties and recyclability.
An example of the multi-shot action that will be plentiful at NPE: A three-shot cell molding PP caps with a TPE gasket and TPE septum. MGS built the four-station servo turntable and mold (below) with servo unscrewing while the mold is closed.
There will be other LSR exhibits at the show from Elmet North America (molds and dispensing equipment); 2KM North America (molds); and Elasmo Systems GmbH (molds and turnkey systems), in addition to LSR materials suppliers.
• Fast Heat is emphasizing new software for its Ion and Pulse controllers that allow for cloud-based computing. Said to be a first in the industry, a wireless chip allows remote access to the control from a PC or mobile device. Predictive analytics in the software reportedly anticipate problems in the mold before they happen and send out alerts if there is an actual failure. Also new are special diagnostic equipment—the CableXChecker that quickly identifies bad cables without using a labor-intensive multimeter, and the MoldXChecker, which quickly identifies thermocouple and heater short circuits before the mold goes into the press. It also identifies leaking tips before major repairs are needed.
Oerlikon says the HRScool Evo’s design eliminates separate, active water cooling for the hot runner pin’s hydraulic cylinder, reducing energy consumption by up to 10%.
• New from Engel is the e-pic servo robot with an unusual hinged swivel arm. It was introduced at Fakuma 2014 (see Dec. ’14 Close Up and Feb. ’15 Keeping Up). Engel also has overhauled its viper linear robot, adapting it for integration with the new CC300 machine control and adding the new, lightweight C70 touchscreen pendant.
• Wittmann Battenfeld will highlight its new W8 Pro series robots with stiffer arms, LED status display, high-efficiency proDrive, and R8.3 control system. Among them is the new, larger model W843 introduced at Fakuma 2014 (see October Keeping Up). Also new at Fakuma was the WP80 pneumatic picker with Net 8 control, which will also be at NPE.
• Among a host of new components introduced in the past year, AGS also will highlight a double-acting, round-clamping, self-retaining gripper finger that stops loss of parts in case of pressure drop. The GFI-DW-E gripper remains in closed position if there is an emergency stop.
Husky (which used to partner with Kortec) is the new challenger, with its own turnkey systems based on its HyPET HPP5 system for PET preforms. It will introduce new technology said to provide more even barrier distribution, allowing for savings up to 50% in barrier resin cost (see Close Up in this issue).
Join this webinar to explore the transformative benefits of retrofitting your existing injection molding machines (IMMs). Engel will guide you through upgrading your equipment to enhance monitoring, control and adaptability — all while integrating digital technologies. You'll learn about the latest trends in IMM retrofitting (including Euromap interfaces and plasticizing retrofits) and discover how to future-proof your machines for a competitive edge. With insights from industry experts, it'll walk you through the decision-making process, ensuring you make informed choices that drive your business forward. Agenda: Maximize the value of your current IMMs through strategic retrofitting Learn how to integrate digital technologies to enhance monitoring and control Explore the benefits of Euromap interfaces and plasticizing retrofits Understand how retrofitting can help meet new product demands and improve adaptability Discover how Engel can support your retrofitting needs, from free consultations to execution
Additional demonstrations of MuCell foam molding will take place at Milacron (automotive bezel), Negri Bossi (gear cam for bowling-pin sweeper), JSW (MuCell plus IML), Plastic Technologies, Inc. (see PET section below), and the German IKV (Plastics Processing Institute). At its own booth, Trexel will show the new T-100 model of its SCF (super-critical fluid) delivery system. First introduced at K 2013 (see Jan. ’14 report), the T series gas-delivery and dosing systems are said to be much simpler, more compact, and less expensive means of converting nitrogen gas (standard) or carbon dioxide (optional) into SCF for mixing with the melt in the injection barrel. The new 8-in. graphical touchscreen control is easier to use: The molder enters only the shot size and percentage of SCF desired, and the system calculates the rest. The T-100 is the smallest of three models, for shot sizes less than 140 g or 5 oz, a size range in which MuCell was not cost-competitive in the past.
• SIPA of Italy will display one of the first XForm 300 hybrid presses (300 metric tons) for molding PET preforms (see PET section).
• Athena Controls is highlighting the new version of its Bedros controller, originally introduced at NPE 2012 for 8-32 zones but now available for 8-64 zones. Both Bedros and Athena’s RMB series controls are now “Powered by ThingWorx,” enabling them to rapidly develop custom software to connect controls to servers and the cloud.
Despite price increase nominations going into second quarter, it appeared there was potential for generally flat pricing with the exception of a major downward correction for PP.
Multiple speakers at Molding 2023 will address the ways simulation can impact material substitution decisions, process profitability and simplification of mold design.
In addition to those medical demonstrations mentioned above, Arburg will mold 64 pipette tips in 4.8 sec on on a GMP-compliant, stainless-steel, all-electric Allrounder 520 A with a Hekuma robot. And Engel will present 96-cavity cleanroom production of needle holders for insulin pens on an all-electric e-motion 440 press with a Hekuma robot and vision inspection, all in about 3.5 sec.
• Ewikon also has something unusual to offer in its variable-position HPS III-FleX manifold with hinged arms that can be repositioned for molds with different cavity spacing. Also new is the MWB 100 portable mini fluidized bed for cleaning up to 24 small tips at a time. Both were introduced at Fakuma 2014 (see January Close Up).
After successfully introducing a combined conference for moldmakers and injection molders in 2022, Plastics Technology and MoldMaking Technology are once again joining forces for a tooling/molding two-for-one.
Core Technology Molding turned to Mold-Masters E-Multi auxiliary injection unit to help it win a job and dramatically change its process.
If you’re interested in lightweight composites, IML, LSR, multi-shot, inmold assembly, barrier coinjection, micromolding, variotherm molding, foams, energy-saving presses, robots, hot runners, and tooling—they’re all here in force.
• New from Mastip Technology of New Zealand is the TL-35 threaded nozzle to expand its product line into larger sizes. It has flow bores of 14-18 mm and lengths from 150 to 600 mm.
Thousands of people visit our Supplier Guide every day to source equipment and materials. Get in front of them with a free company profile.
Benefit from our expertise and lower the costs for your injection moulding production by optimising your energy requirement.
SIPA of Italy will display an XForm 300 hybrid press (300 metric tons) for molding PET preforms in up to 96 cavities. Like the XForm 150 that debuted at K 2013, it’s built by Athena Automation in Canada. It’s designed for quick mold changes and to accept legacy molds from all leading manufacturers. Said to have one of the smallest footprints in the industry for its tonnage, the machine can be fitted with Athena’s post-mold cooling system that cools preforms for up to six cycles.
Other multicomponent exhibits at the show will include Wittmann Battenfeld’s molding of a glass-filled nylon and HDPE automotive fuel flange on a two-shot EcoPower all-electric machine. Negri Bossi will mold a two-color PP container. Boy Machines will show off its new 2C XS auxiliary injection unit (introduced at K 2013) on a Boy 25 E press producing marbleized parts (as at Fakuma ’14). Billion of France will perform three-shot molding with in-mold assembly of hollow auto engine components (see Keeping Up).
“Go faster” and “integrate more functions” look to be the guiding principles of new injection molding developments to be shown by Engel Austria at K 2013 in Dusseldorf this October.
While the melting process does not provide perfect mixing, this study shows that mixing is indeed initiated during melting.
Also new at the show is the revamped CX line of small two-platen machines (35 to 160 m.t.) with servo-hydraulics now standard. Introduced at last fall’s Fakuma 2014 show, these machines are said to be 15% faster, 30% quieter, and 10% lower in energy consumption.
Husky will demonstrate its newest PET preform system, the HyPET HPP5, a fully integrated system based on its hybrid machine with an upgraded 19-in. touchscreen controller, improved resin drying system, and special sensors and other provisions to ensure longer mold life. Various tweaks to the system, introduced in late 2013, are said to provide up to 12% faster cycles than the HPP4 system and up to 5% increase in net uptime. Husky also boasts 60% longer intervals between mold maintenance, with tool life extended to 10 million cycles (see Feb. ’14 Keeping Up). A 400-ton HPP5 system will run at NPE.
KraussMaffei will demonstrate production of an airbag housing with its FiberForm process. A two-platen, servo-hydraulic CX 300 machine (one of the newly upgraded models) will preheat, form, and overmold fiberglass/nylon composite sheets in 45 sec, with no post-mold trimming. A KM LRX 150 linear robot assists the process.
The aim of this presentation is to guide you through the factors and the numbers that will help you determine if a robot is a smart investment for your application. Agenda: Why are you considering automation? What problems are you trying to solve? How and why automation can help Crunch the numbers and determine the ROI
• Boy Machines will feature three of the servohydraulic machines that made their debut at K 2013. These include the Boy 25 E, 60 E, and 100 E (a new, larger size for the company). All of them come standard with the new, patented EconPlast barrel, which reportedly cuts energy consumption by 40-60% through embedding the heater bands in deep grooves in the barrel and covering the barrel with insulation, as well as through more-efficient cooling of the feed section.
• Sytrama of Italy will demonstrate Cartesian robots that debuted at K 2013 (see Feb. ’14 report). Operating in the booth of sister company Negri Bossi will be models of the new S Series all-servo robots that handle higher payloads and higher speeds with less vibration than the older G Series. Also on display will be the low-cost, all-aluminum One Series all-servo units for small machines (50-250 tons).
LSR moldmaker M.R. Mold & Engineering will feature its stuffer boxes for LSR, including a new larger model holding up to 3.1 lb of material, vs. 1 lb for the original unit. These pneumatic devices hold and feed premixed LSR A and B components for short runs, micromolding, or prototyping.
• Three new Sodick presses will debut from Plustech Inc. All have Sodick’s V-Line system of two-stage injection with screw and plunger arranged in a “V.” Two are 3- and 20-ton micromolding systems (more below), and the third is the GL100, a 100-ton model in Sodick’s new “Global Platform” of mid-size horizontal presses. All three models have Sodick’s hybrid direct-pressure clamping system. Instead of a toggle, it has electric servomotors for opening and closing and for ejection. A short-stroke, hydraulic “pancake” cylinder builds tonnage, and mechanical side locks engage the central clamping cylinder.
NEW MACHINES & CONTROLS New machine models at NPE emphasize energy efficiency as well as speed, accuracy, and consistency. Several of these units first appeared at the K 2013 show in Dusseldorf (see Sept. ’13 and Jan. ’14 reports):
Two of four displays of the surface aesthetics attainable with variotherm molding: Above: an auto center console of PC/ABS molded by Engel using MuCell foam and Roctool induction mold heating shows a combination of laser texturing and glossy surface. Below: a PC part at the Roctool booth has sophisticated texture with a 3D effect, which Roctool says pushes the limits of decoration that can be achieved in the mold without secondary operations.
The MGS-built mold will provide servo-driven unscrewing of the closure while the mold is closed, during the molding cycle, thereby adding nothing to the overall cycle time. Also, A-side pneumatic ejection of the part will occur simultaneously with mold opening and turntable indexing.
While prices moved up for three of the five commodity resins, there was potential for a flat trajectory for the rest of the third quarter.
• Fortune International/Victor Taichung of Taiwan will show its new ES (Energy Saving) hydraulic press line of 50 to 1600 tons (see February Keeping Up).
• Mold-Masters is introducing its new premium hot-runner line, the Summit-Series. This stainless-steel system reportedly has one-fourth as much thermal variation from setpoint as typical nozzles with heater bands, suiting it to heat-sensitive resins like PC, acetal, and PBT and to medical markets. It offers new servo-actuated gating methods. Also on display is the Fusion G2 nozzle in larger sizes, such as the 7000 model introduced at Fakuma 2014 with bores up to 22 mm and lengths to 1000 mm (see January Close Up).
Learn about sustainable scrap reprocessing—this resource offers a deep dive into everything from granulator types and options, to service tips, videos and technical articles.
Formnext Chicago is an industrial additive manufacturing expo taking place April 8-10, 2025 at McCormick Place in Chicago, Illinois. Formnext Chicago is the second in a series of Formnext events in the U.S. being produced by Mesago Messe Frankfurt, AMT – The Association For Manufacturing Technology, and Gardner Business Media (our publisher).
Resin drying is a crucial, but often-misunderstood area. This collection includes details on why and what you need to dry, how to specify a dryer, and best practices.
Join Engel in exploring the future of battery molding technology. Discover advancements in thermoplastic composites for battery housings, innovative automation solutions and the latest in large-tonnage equipment designed for e-mobility — all with a focus on cost-efficient solutions. Agenda: Learn about cutting-edge thermoplastic composites for durable, sustainable and cost-efficient battery housings Explore advanced automation concepts for efficient and scalable production See the latest large-tonnage equipment and technology innovations for e-mobility solutions
Engel also will use robot transfer for thermoplastic/LSR molding, but in this case using two e-mac 170 all-electric presses—one to mold double-ended wrenches in carbon-fiber/nylon and the other to overmold an LSR grip. An Engel viper 12 linear robot will perform the transfer.
Plastics Technology covers technical and business Information for Plastics Processors in Injection Molding, Extrusion, Blow Molding, Plastic Additives, Compounding, Plastic Materials, and Resin Pricing. About Us
• The newest all-electric series from Toyo of Japan is the Si-6 series (55 to 1050 tons), shown in Orlando by Maruka USA. It’s designed for high-speed molding and simplified setup. Also on display will be servo-hydraulic models from FCS in Taiwan.
Join KraussMaffei for an insightful webinar designed for industry professionals, engineers and anyone interested in the manufacturing processes of PVC pipes. This session will provide a comprehensive understanding of the technology behind the production of high-quality PVC pipes: from raw material preparation to final product testing. Agenda: Introduction to PVC extrusion: overview of the basic principles of PVC pipe extrusion — including the process of melting and shaping PVC resin into pipe forms Equipment and machinery: detailed explanation of the key equipment involved — such as extruders, dies and cooling systems — and their roles in the extrusion process Process parameters: insight into the critical process parameters like temperature, pressure and cooling rates that influence the quality and consistency of the final PVC pipes Energy efficiency: examination of ways to save material and energy use when extruding PVC pipe products
• Hekuma provides the automation for the cell producing needle hubs for insulin pens in the Engel booth, noted above. Besides 20% higher productivity for this application, Hekuma notes that its EOAT handles all 96 parts at once, instead of 16 at a time. Vacuum sucks the parts into the gripper. Light barriers ensure that all cavities are clear. Camera inspection of the holes in the hubs can recognize whether any pins have been damaged. The system will demonstrate simultaneous production of hubs with holes of 0.3 and 0.5 mm through cavity-specific handling.
One of the more unusual developments in hot-runner control will be Husky’s introduction of Altanium Servo Control as an extension of its Altanium Matrix2 system. Beyond controlling just hot-runner valve-pin movements and temperatures, it can control speed, positioning, and sequencing of any servo actions in the cold half—such as unscrewing or collapsing cores, slides, stack rotation, and coining movements (see January Close Up on Fakuma 2014).
Other IML demonstrations will be by Arburg (PP lids in four cavities), Wittmann Battenfeld (stadium cups), and Niigata (drink cups, using automation from Campetella of Italy). Verstraete IML of the Netherlands, a maker of IML labels, offers a free, downloadable guide to more than 35 IML-related exhibits at the show.
• FIPA is bringing its latest suction cups for robot grippers. Varioflex cups have very soft sealing (30 Shore A) backed up by firmer bellows (60 Shore A). The soft cup reportedly keeps its grip on grained or irregular surfaces, while the bellows balances out height differences in parts.
One of two new Sodick V-Line micromolding systems from Plustech is the HC03VRE 3-ton vertical press with four tiebars and rotary table. It will mold a direct-gated, two-cavity micro-bobbin weighing 0.09 g in a cycle time of only 1.9 sec.
Netstal will demonstrate production of 44-oz stadium cups with IML on an Elion 3200 (320 m.t.) hybrid servo-hydraulic machine. Netstal will use this application to demonstrate its technology for thin-wall packaging with long flow lengths (flow length to wall-thickness ratio for these cups is 300:1). Netstal uses a “thin-wall centering” approach to prevent core shift by means of rheological flow paths and varying injection pressures.
Sustainability continues to dominate new additives technology, but upping performance is also evident. Most of the new additives have been targeted to commodity resins and particularly polyolefins.
Coming up March 23-27 at the Orange County Convention Center in Orlando, Fla., NPE2015 has plenty of new machines, robots, hot runners, and tooling fine-tuned for speed, energy savings, and better part quality. But even more to the point, the show emphasizes application-oriented capabilities such as lightweight composites for automotive, micromolding, thermoplastic/LSR overmolding, multicomponent molding with in-mold assembly or multilayer barrier coinjection, in-mold labeling, and smooth-surface foam molding with variotherm (hot/cold) mold cycling. Here are examples of what to look for, based on information supplied by a cross-section of exhibitors.
The Plastics Industry Association (PLASTICS) has released final figures for NPE2024: The Plastics Show (May 6-10; Orlando) that officially make it the largest ever NPE in several key metrics.
For reliable performance, a slimline design, and an unbeatable price, there is only one choice: the new ALLROUNDER 720 E GOLDEN ELECTRIC!
• SAS Automation will highlight its new eCommerce Center for online ordering of EOAT components and its Quick Tool program for fast shipping of simple EOAT using stock components in one to two weeks and more complex custom tools in three to four weeks.
Also new is the Adaptive Process Control (APC) system that corrects the process during each cycle. This patented development adjusts the changeover point and holding-pressure profile in each cycle to the current melt viscosity and current flow resistance in the mold—compensating for deviations in the same shot. Comparing it to cruise control in a car, KM says this significantly improves consistency of shot weight, regardless of changing plant temperature, climate conditions, or material batch characteristics. It reportedly also can compensate for screw/barrel wear or irregular closing of the nonreturn valve. Other benefits are said to include ability to restart production faster after downtime and to use high quantities of recycled material. Even energy consumption is reportedly improved, since molders can run lower barrel temperatures and backpressures and still ensure stable melt viscosity.
Mold maintenance is critical, and with this collection of content we’ve bundled some of the very best advice we’ve published on repairing, maintaining, evaluating and even hanging molds on injection molding machines.
Plastics Technology’s Tech Days is back! Every Tuesday in October, a series of five online presentations will be given by industry supplier around the following topics: Injection Molding — New Technologies, Efficiencies Film Extrusion — New Technologies, Efficiencies Upstream/Downstream Operations Injection Molding — Sustainability Extrusion — Compounding Coming out of NPE2024, PT identified a variety of topics, technologies and trends that are driving and shaping the evolution of plastic products manufacturing — from recycling/recyclability and energy optimization to AI-based process control and automation implementation. PT Tech Days is designed to provide a robust, curated, accessible platform through which plastics professionals can explore these trends, have direct access to subject-matter experts and develop strategies for applying solutions in their operations.
This cell will premiere a new concept from Beck Automation of Switzerland that greatly reduces the opening stroke of the clamp. Beck’s side-entry robot rearranges the cups during extraction from the 2 + 2 cavity arrangement to a 4 inline orientation that fits between the long mold cores.
• New from Synventive Molding Solutions are hydraulic and pneumatic valve-gate controls and compact hydraulic actuators (see Keeping Up).
The arburgXworld customer portal gives you access to a wide range of digital apps and features that make your daily work easier.
Trexel’s new T-100 SCF metering system is said to make MuCell foaming cost-effective now for small machines (<5-oz shot).
• Niigata will bring two new all-electric machines to the show. The MDVR110S7000 is a vertical 110-ton press with low table height (3.4 ft) for easier operator access. It takes larger molds than most verticals—up to 500 mm square. Table rotation takes under 1 sec. The S7000 also boasts ultralow-speed injection capability (0.1 mm/sec) for thick-walled insert jobs and ability to set different injection profiles for “A” and “B” mold halves on the turntable.
Boy Machines is bound to attract visitors to its molding cell that will produce polycarbonate beer glasses, laser inscribe them, place them on a conveyor belt, and then fill them with beer.
While the major correction in PP prices was finally underway, generally stable pricing was anticipated for the other four commodity resins.
August 29-30 in Minneapolis all things injection molding and moldmaking will be happening at the Hyatt Regency — check out who’s speaking on what topics today.
• HPM North America, a new old name in plastics machinery, now under Chinese ownership, will present two new lines of presses—all-electric and servohydraulic two-platen (see Keeping Up section for details).
Introduced by Zeiger and Spark Industries at the PTXPO, the nozzle is designed for maximum heat transfer and uniformity with a continuous taper for self cleaning.
Meanwhile, Roctool will conduct another demo in its own booth, using a KraussMaffei press to mold a polycarbonate casing for a USB connector that sports a diamond-pattern texture on a piano-black surface that gives a 3D effect. According to Roctool, this special surface is “pushing the limits” of what can be injection molded without secondary operations. Induction heating provides exact, uniform replication of the texture with no flow marks or blushing.
Successfully starting or restarting an injection molding machine is less about ticking boxes on a rote checklist and more about individually assessing each processing scenario and its unique variables.
Polyshot’s new hydraulic single-nozzle valve gate is said to be the first self-contained unit of this type that is housed entirely within the locating ring.
Sumitomo (SHI) Demag will run a medical micromolding application on its SE30DUZ direct-drive all-electric press with the unique zero-compression SL screw (see Aug. ’12 Close Up). An acetal gear used in a new cataract surgery device weighs just 0.524 g and measures 0.775-mm diam. with 85 microns between the gear teeth.
As noted above, Husky will also introduce its new barrier coinjection system for PET preforms, based on the HPP5 system, though it will not demonstrated at the booth.
Barrier PET containers for beverages, sauces, and other sensitive products become more cost-effective through more efficient use of expensive barrier resins.
Milacron LLC is also bringing out a new machine for PET preforms. Its M-PET 300 is a servo-hydraulic press designed for low energy consumption, and attractive output-to-capital ratio. It operates with Milacron’s and others’ preform tooling.
Across the show, sustainability ruled in new materials technology, from polyolefins and engineering resins to biobased materials.
And Nissei will introduce its NPX7 Advance micromolder, a 7-ton servo-hydraulic press with a 12-mm inline screw—something previously not thought possible, according to the company. It will be equipped with a Nissei Smart Feeder to help stabilize the cycle and a high-end TACT IV control with 15-in. touchscreen.
With interest still running high in lightweight composites for automotive structural parts, three companies will be demonstrating such processes at the show. Engel, in fact, will make this the main focus of its booth. It will reprise its K 2013 exhibit of molding a brake pedal, developed with ZF-Friedrichshafen. The part and process have gone through several upgrades since the award-winning debut in 2011. It is molded on a vertical hydraulic press with horizontal injection, using an Engel easix articulated six-axis robot and infrared oven. A continuous-fiber nylon fabric will be preheated and placed in the mold, where it will be preformed and overmolded with more nylon to produce a net-shape part that requires no trimming. Control of the robot is fully integrated into the injection machine controller. This allows the robot to enter the clamp area while the mold is opening, reducing cycle time.
If you haven’t been to a major international plastics show recently, NPE2015 may look quite different from what you remember. Injection molding exhibits no longer focus on machines in isolation, but as part of automated cells integrating multiple processes and/or performing post-molding operations like decorating, assembly, and quality inspection. And machine builders are going all out nowadays to relate more closely to visitors’ molding businesses by showing off their capabilities in target market sectors like packaging, automotive, medical, and electronics. Instead of showing a machine and letting you figure out what you might do with it, exhibitors are trying to anticipate what you want to accomplish and presenting live demonstrations of how it can be done.
One of Engel’s molding demonstrations will be the North American debut of its redesigned duo mid-sized hydraulic, two-platen machines, shown at K 2013 (see Aug. ’13 Close Up). Engel will also feature its brand-new customer web portal (a worldwide debut). The app lets customers make service requests and order spare parts more easily, and they can also track the status of a service request. The app can also monitor the status and availability of all a customer’s machines.
Mixed in among thought leaders from leading suppliers to injection molders and mold makers at the 2023 Molding and MoldMaking conferences will be molders and toolmakers themselves.
• Chinese machine builder Tederic Machinery Co. (office in Palmetto, Fla.) is bringing its new all-electric Dream-E (DE) Series, based on Japanese technology. These toggle presses have linear guides for the platen and injection unit, which swivels for screw changes.
MGS Mfg. Group will highlight an LSR version of its new servo-driven Universal Multishot Systems (UMS) portable injection units. The UMS Model E-LSR-V vertical, platen-mount will be shown with a Graco dispensing pump and barrel stack. It has 30-cc shot capacity and injection speed of 178 mm/sec.
While on the subject of thin-wall packaging, as reported in last month’s Keeping Up section, Nordson Xaloy will debut the Quantum barrier screw, said to reduced screw recovery time by 10-15% for high-speed molding of thin-wall packaging. It comes with a special poppet-style non-return valve designed to prevent resin degradation and ensure consistent shot size.
• As at Fakuma 2014 (January Close Up), Incoe will show expanded utility for its SoftGate valve-gate sequence control in direct gating onto in-mold decorating (IMD) films without wrinkling the film. Incoe will also show its compact HEM hydraulic cylinder for valve-gate actuation. Half the size of other hydraulic actuators, it allows closer gate positioning (see Feb. ’14 Keeping Up). The company also has a new, low-cost pneumatic valve-gate sequence controller, the GSC-Mini, for up to eight valves.
• Polyshot Corp. will feature its new single-nozzle valve-gate line, with greatly reduced stack height and very high pin force to handle the stiffest filled or engineering resins (April ’14 Keeping Up).
The MGS booth will also display a new UMS Model E750-P rotary platen with servo drive, capable of 180-0-180 alternating-direction or 180-360 continuous-direction rotation. Index time is <1 sec. A lock wedge provides precise positioning. This “Performance model” has heavier mold capacity, four water circuits instead of the standard two, an option to accommodate two additional media circuits for water, oil, or air.
• Boy Machines is now offering robots under its own label. At Fakuma 2014 these included a side-entry pneumatic model and an overhead servo model—both integrated with the machine controls (see December Keeping Up).
The newcomer in the composites action is Arburg. Its approach, first unveiled at K 2013 (see Jan. ’14 report), overmolds continuous-fiber thermoplastic sheet with long-fiber compound prepared on the machine. Continuous glass rovings feed into the barrel after the melting zone, where they are chopped by the screw. The latter approach, known as DLFT (direct long-fiber thermoplastic) saves the cost of purchasing long-fiber pellets and gives the molder flexibility to adjust fiber lengths up to 50 mm.
While prices moved up for three of the five commodity resins, there was potential for a flat trajectory for the rest of the third quarter.
More productivity with less energy consumption and capital investment; more operations in the machine or manufacturing cell with less time, labor, energy, and capital—these were the common themes of injection molding exhibits at October’s K 2013 show.
technotrans says climate protection, energy efficiency and customization will be key discussion topics at PTXPO as it displays its protemp flow 6 ultrasonic eco and the teco cs 90t 9.1 TCUs.
• MHS-Mold Hotrunner Solutions will show Rheo-Pro Black Box actuators and second-generation iVG internal valve-gate nozzles that are both able to operate at temperatures up to 450 C/850 F without cooling or seal damage. They accommodate high-temperature resins like PEEK. (See Feb. ’14 Close Up on K 2013).
Milacron will operate a cell overmolding LSR on nylon with an all-electric Roboshot 165 press, E-Multi secondary injection unit from Mold-Masters, and a Varian rotary turntable instead of robotic transfer.
Take a deep dive into all of the various aspects of part quoting to ensure you’ve got all the bases—as in costs—covered before preparing your customer’s quote for services.
Join Wittmann for an engaging webinar on the transformative impact of manufacturing execution systems (MES) in the plastic injection molding industry. Discover how MES enhances production efficiency, quality control and real-time monitoring while also reducing downtime. It will explore the integration of MES with existing systems, emphasizing compliance and traceability for automotive and medical sectors. Learn about the latest advancements in IoT and AI technologies and how they drive innovation and continuous improvement in MES. Agenda: Overview of MES benefits What is MES? Definition, role and brief history Historical perspective and evolution Longevity and analytics Connectivity: importance, standards and integration Advantages of MES: efficiency, real-time data, traceability and cost savings Emerging technologies: IoT and AI in MES
Hot runner supplier Mastip used K 2022 to introduce the customized and valve-gated Aquilo liquid silicone rubber (LSR) cold deck.
Discover how artifical intelligence is revolutionizing plastics processing. Hear from industry experts on the future impact of AI on your operations and envision a fully interconnected plant.
This process will be demonstrated on a servo-hydraulic Allrounder 820 S. Two reinforced-thermoplastic sheets of different thicknesses are picked up by a six-axis robot with new gripper technology, preheated, and placed in the mold. Total cycle is around 55 sec.
• Potential for energy savings through more-efficient drive systems is generally held to increase along with machine size. If you want to explore that proposition, visit Ube Machinery’s booth, where a 950-ton all-electric UN950 and a 1000-ton Servomax US1000 servo-hydraulic press will demonstrate energy savings claimed to be up to 85% and 70% respectively.
Say “manufacturing automation” and thoughts immediately go to the shop floor and specialized production equipment, robotics and material handling systems. But there is another realm of possible automation — the front office.
The other new micromolder is the LP20EH3 (20-ton) horizontal press that dry cycles in only 0.97 sec. It will mold an LCP part simulating a medical-device cover.
• Among the 20 robots at Sepro’s booth will be units previously introduced at Fakuma 2012 and K 2013: 5X Cartesian robots with servo wrist (five axes total), 6X articulated robots (six-axes), and the S3 servo sprue picker.
Across all process types, sustainability was a big theme at NPE2024. But there was plenty to see in automation and artificial intelligence as well.
KM’s machines feature the new MC6 Multitouch control that uses gesture-based commands, like a smartphone or tablet, on its large, 24-in. touchscreen. Each operator can customize the screen display and retrieve the settings with an RFID card. A brand-new feature called SlideX uses a guiding line engraved on the glass to give the operator haptic (“feel”) control over all moving axes without looking at the control panel. Instead, the operator can feel the acceleration on the axes and configure them intuitively.
As a fluorescent marker has been added to the thermoplastic component, the box – which is not identifiable by the end consumer – is clearly marked. Even a fraction is enough to clearly identify it with a laser detector through its characteristic fluorescence. This technology from Arburg's partner Polysecure allows products to be clearly traced, distinguished from counterfeits and, if necessary, sorted by material.
The first shot is the gasket (0.36 g of TPE). The second shot is the PP cap (5.2 g). And the third shot is the TPE septum (0.32 g).
Ultradent's entry of its Umbrella cheek retractor took home the awards for Technical Sophistication and Achievement in Economics and Efficiency at PTXPO.
• Milacron LLC, whose 25,000 ft2 is the largest NPE booth ever, will bring out two new presses. One is the M-PET 300 servo-hydraulic PET preform system (see PET section below). Also new is the Ferromatik 580 machine (580 m.t.), introduced in Germany last May, which will be shown in a coinjection setup (see below). Ferromatik machines are modular, allowing for electric, hydraulic, and hybrid drive options.
When, how, what and why to automate — leading robotics suppliers and forward-thinking moldmakers will share their insights on automating manufacturing at collocated event.
Another growing application area will be represented by three exhibitors. Wittmann Battenfeld will have two all-electric MicroPower machines at the show. One in its booth will mold two-component LSR tear-duct plugs. Another will mold micro parts at the booth of moldmaker Burteck LLC.
• KraussMaffei will introduce to the U.S. its newest and largest model of GX hydraulic two-platen presses. The GX 900 (900 m.t.) first appeared at K 2013. The medium-sized GX line (starting at 450 m.t.) arrived in the U.S. in 2013 (see July ’12 and March ’13 Keeping Up).
One of the impressive molding cells running at NPE will be production of more than 180,000 still-water caps/hr by Sumitomo (SHI) Demag, said to be a world record.
• Among the six molding cells running at the Wittmann Battenfeld booth (see February Keeping Up) will be an example of the new SmartPower servo-hydraulic presses, introduced at the Fakuma 2014 show in Germany (see December Close Up) to replace the HM hydraulic series.
In a time where sustainability is no longer just a buzzword, the food and beverage packaging industry is required to be at the forefront of this innovation. By adopting circular packaging processes and solutions, producers can meet regulatory requirements while also satisfying consumer demand and enhancing brand reputation. Join Husky to learn more about the broader implications of the circular economy — as well as how leading brands are leveraging this opportunity to reduce costs, increase design flexibility and boost product differentiation. Agenda: The cost and operational benefits of embracing circularity Key materials in circular packaging — including rPET and emerging bioplastics How to design a circular food and beverage package Strategies for selecting sustainable closures to future-proof packaging solutions Optimization and streamlining of production processes for enhanced efficiency How Husky Technologies can enable your sustainable success
• Engel will make the U.S. introduction of its e-speed hybrid for packaging, which was launched at the K 2013 show in Dusseldorf. It has an electric screw and toggle clamp and accumulator-assisted hydraulic injection. Special features include the flywheel energy-storage mechanism and the long opening stroke that accommodates large stack molds (see February Keeping Up).
• Absolute Haitian will exhibit new models from Haitian of China. NPE will also be the U.S. debut of the Zhafir Zeres all-electric series (45 to 259 tons) with integrated hydraulics for core pulls, etc. (see October ’14 Keeping Up). Integrated hydraulics save the floorspace for a separate hydraulic power pack. Also running at the show will be new smaller sizes (440 to 1069 tons) of Jupiter II servo-hydraulic two-platen machines, available with new wide-platen options (see February Keeping Up).
One of two new Sodick V-Line micromolding systems from Plustech is the HC03VRE 3-ton vertical press with four tiebars and rotary table. It will mold a direct-gated, two-cavity microbobbin weighing 0.09 g in a cycle time of only 1.9 sec.
An ALLROUNDER MORE 2000 in the Comfort performance variant and with two electric injection units will produce a two-component multifunctional box made of thermoplastic and self-adhesive liquid silicone. The two components are injected directly via a cold or hot runner system, resulting in waste-free production. The associated LSR dosing unit is integrated via OPC UA and the Euromap interface 82.3 into the GESTICA controller. The cycle time is around 60 seconds. First to be produced is the PBT pre-moulded part, which is then converted in the 1+1-cavity mould so that the LSR component can finally be injected. The complex 3D contour of the component and precise positioning of the pre-moulded part in the second mould station place high demands on the gripper and robotic system. The 164-gram box is finally removed by a MULTILIFT V 30 linear robotic system and placed on a conveyor belt.
• Two examples of Negri Bossi’s “Evolution” program of redesigns and upgrades (signified by a small “e” added to the name) will appear in Orlando. First shown at K 2013, these include a Canbio eV300 all-electric model (300 m.t.) with new “prismatic” linear bearings on the moving platen, expanded tiebar spacing, and re-engineered platens to reduce mass. There will also be a Canbimat eV210 (210 m.t.) two-component press with rotary table (more below).
• MHT Mold & Hotrunner Technology is featuring upgrade sets for Husky’s HyPET preform molds. Through more compact cavity spacing, they allow twice as many cavities as the machine could previously handle. The newest additions are upgrade sets for HyPET 120 and 225 at the small end of the range. MHT also has new pre-engineered, economically priced manifold systems for quick delivery (see January Keeping Up).
At least three exhibits at NPE demonstrate that structural foam parts need not have the swirly rough surface typical in the past. The secret is use of the ever more popular variotherm process for hot/cold mold cycling. Both Engel and KraussMaffei will produce appearance parts using the MuCell microcellular foam process from Trexel and rapid induction heating and quick cooling of molds with technology from Roctool. Engel will produce automotive center console components of PC/ABS. The foam fills a part with varying wall thickness and surface structures, including undercuts, with no sink marks. Roctool technology replicates a surface that ranges from laser textured to a high-gloss, piano-black finish. The part will be molded on a redesigned duo hydraulic two-platen machine (610 tons, see above).
This month’s resin pricing report includes PT’s quarterly check-in on select engineering resins, including nylon 6 and 66.
Second quarter started with price hikes in PE and the four volume engineering resins, but relatively stable pricing was largely expected by the quarter’s end.
Nylon composite brake pedal (Engel) and airbag housing (KraussMaffei) will be made at the show from thermoplastic continuous-fiber sheet and injection overmolding with no need for post-mold trimming. Arburg will also do a composite demonstration.
Processors with sustainability goals or mandates have a number of ways to reach their goals. Biopolymers are among them.
GETTING A QUOTE WITH LK-MOULD IS FREE AND SIMPLE.
FIND MORE OF OUR SERVICES:
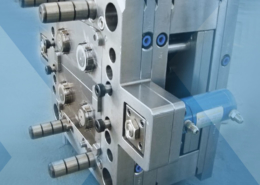
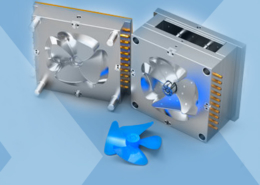
Plastic Molding

Rapid Prototyping
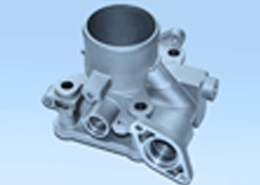
Pressure Die Casting
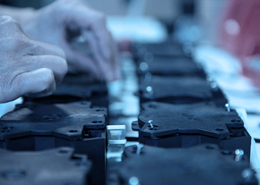
Parts Assembly
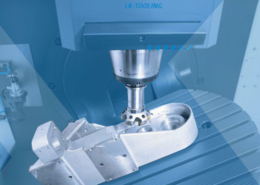