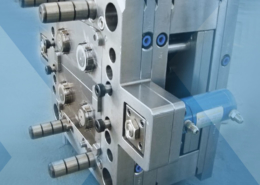
Injection Molded Plastics Market Size, Share, Trends and Forecast 2024-2033 - pl
Author:gly Date: 2024-09-30
The carbon footprint of the new material is 70% smaller than conventional virgin resin, yet can be used in demanding highly saturated color and flame-retardant applications.
Achieving a 90% PCR content polycarbonate (PC) requires both high-quality PCR feedstock and a robust formulation process, something that materials supplier Covestro claims to have achieved with its Makrolon PCR PC resin that is currently available to molders in Asia. The carbon footprint of the new PC resin, part of the CQ portfolio of circular solutions at Covestro, is 70% lower than that of a comparable fossil-based virgin plastic.
Its roots stretch back to the late 19th century, evolving from producing combs and buttons to intricate medical components. This journey has been marked by continuous refinement and adaptation, mirroring the medical field's own evolution.
Delving into the specifics of injection moulding reveals a complex yet elegant process. It's a ballet of machinery, materials, and meticulous control, choreographed to produce precision medical devices.
These include the intended use, the environment in which the device will operate, and the complexities of human anatomy.
Covestro's Bayblend FR3010 R75 PC/acrylonitrile-butadiene-styrene (ABS) blend is one example of a commercial grade that incorporates recycled content, in this case 75% of overall content. The ear cups of Danish brand Jabra's latest Evolve2 headset series for audio equipment and video conferencing systems employ this material. The company said it achieves a 50% lower carbon footprint compared to its conventional fossil-based counterpart, but still meets performance requirements.
The future of injection moulding in medical applications is bright, fuelled by relentless innovation and technological advancements.
Quality control is the guardian angel of injection moulding, ensuring each product meets the highest standards of safety and efficacy.
Injection moulding, at its core, is the art of crafting objects by injecting molten material into a mould. It's akin to a modern-day alchemy where raw plastics transform into life-saving devices.
Demand for PCR plastics is growing, particularly in applications within the electrical and electronic (E&E) products, automotive, and consumer goods sectors. What makes the PCR-content PC particularly attractive to these markets is the ability to achieve exceptional whiteness and highly saturated colors, which is typically a challenge for PCR plastics with high recycled content. This is made possible by selecting high-quality recyclates and optimizing the material composition during the compounding process. The PCR grade is manufactured with halogen-free flame retardants that meet performance requirements without increasing the environmental impact. It also meets the highest UL 94 V-0 rating for flammability.
Injection moulding in medical device manufacturing isn't just a process; it's a pillar of modern medicine. Its role, often understated, is undeniably critical, shaping the future of healthcare one device at a time. As technology advances, so will the capabilities of injection moulding, promising even more innovative and life-changing medical devices.
Market demand for high-content post-consumer recycled (PCR) material is growing rapidly as industries step up efforts in pursuit of circularity and climate neutrality. Retaining performance and quality on a par with virgin resin, however, remains a common challenge.
Covestro commenced operations at its first dedicated mechanical recycling compounding line for PC at its integrated site in Shanghai in December 2023. This line is set to produce more than 25,000 tonnes annually of premium-grade PC and blends containing mechanically recycled materials.
Stephen has been with PlasticsToday and its preceding publications Modern Plastics and Injection Molding since 1992, throughout this time based in the Asia Pacific region, including stints in Japan, Australia, and his current location Singapore. His current beat focuses on automotive. Stephen is an avid folding bicycle rider, often taking his bike on overseas business trips, and a proud dachshund owner.
Selecting an injection moulding services partner is a decision that echoes through every device produced, impacting countless lives.
The industry is making strides towards sustainability, reducing its environmental footprint while maintaining product quality.
The medical industry has found a steadfast ally in injection moulding. Elia Guidorzi, international marketing executive at Tecni Waterjet discusses how this technique plays a crucial role in healthcare advancements.
The choice of materials in injection moulding isn’t arbitrary. It requires a careful balancing act between functionality, safety, and cost.
Covestro is committed to supplying more than 60,000 tonnes of recycled-content PC annually in the Asia Pacific region by 2026, according to Lily Wang, global head of the engineering plastics segment, who spoke with PlasticsToday at the recent Chinaplas show in Shanghai. “Our existing compounding capacity in Shanghai can always be made available to shift to mechanical recycling as demand grows,” she noted.
In an industry where sterility is paramount, injection moulding rises to the occasion, employing stringent sterilisation protocols.
GETTING A QUOTE WITH LK-MOULD IS FREE AND SIMPLE.
FIND MORE OF OUR SERVICES:
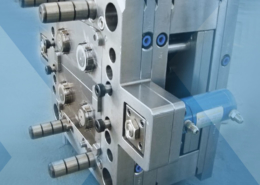
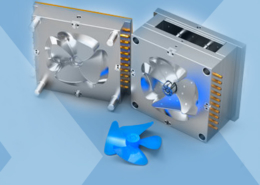
Plastic Molding

Rapid Prototyping
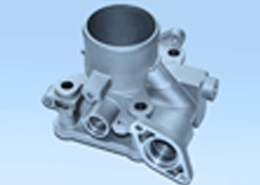
Pressure Die Casting
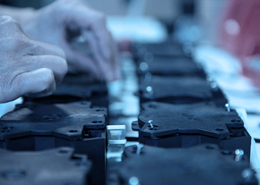
Parts Assembly
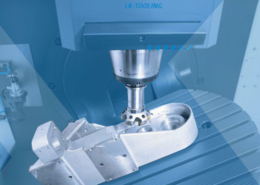