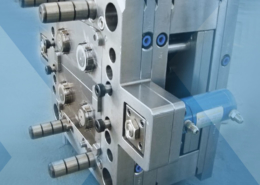
Unveiling the Power of PT Plastic Injection
Author:gly Date: 2024-06-08
PT plastic injection molding stands as a cornerstone in the realm of manufacturing, offering a multitude of possibilities and innovations. This article embarks on an exploration of PT plastic injection molding, delving into its applications, technological advancements, environmental considerations, and future prospects. By unraveling the intricacies of PT plastic injection, readers will gain a profound understanding of its significance in modern industry and beyond.
Introducing PT Plastic Injection Molding
PT plastic injection molding represents a sophisticated manufacturing process wherein molten plastic material is injected into a mold cavity, solidifying into the desired shape upon cooling. This method enables the production of intricate and precise components with high efficiency and repeatability, revolutionizing various industries worldwide.
Applications Across Industries
Automotive Sector
In the automotive industry, PT plastic injection molding plays a pivotal role in manufacturing interior and exterior components, such as dashboards, bumpers, and door panels. Its ability to produce lightweight yet durable parts with intricate designs contributes to enhancing vehicle performance and aesthetics.
Electronics and Consumer Goods
PT plastic injection molding is ubiquitous in the production of electronic enclosures, appliance components, and consumer goods. From smartphone casings to kitchen utensils, this method offers manufacturers the flexibility to create products that are not only visually appealing but also functional and cost-effective.
Medical Devices
In the medical sector, PT plastic injection molding facilitates the fabrication of sterile and biocompatible equipment, including syringes, surgical instruments, and implantable devices. The stringent requirements for precision, consistency, and material purity make it an indispensable manufacturing technique in ensuring patient safety and healthcare efficacy.
Technological Advancements
Advanced Materials
Technological advancements have expanded the repertoire of materials compatible with PT plastic injection molding, ranging from traditional thermoplastics to biodegradable polymers and composite materials. These innovations offer enhanced properties such as strength, flexibility, and sustainability, opening new avenues for product design and performance.
Process Optimization
Advances in process optimization techniques, including computer-aided design (CAD), simulation software, and real-time monitoring systems, have revolutionized PT plastic injection molding. These tools enable manufacturers to fine-tune process parameters, minimize defects, and maximize productivity, ultimately improving product quality and cost efficiency.
Additive Manufacturing Integration
The integration of additive manufacturing technologies, such as 3D printing, with PT plastic injection molding has ushered in a new era of hybrid manufacturing. By leveraging the strengths of both processes, manufacturers can achieve unparalleled design freedom, rapid prototyping, and on-demand production capabilities, driving innovation and customization in product development.
Environmental Considerations and Sustainability
Material Recycling
Addressing environmental concerns, PT plastic injection molding has embraced material recycling initiatives to minimize waste and promote sustainability. Closed-loop recycling systems and eco-friendly materials offer viable solutions for reducing the environmental footprint associated with plastic production and consumption.
Energy Efficiency
Efforts to enhance energy efficiency in PT plastic injection molding processes have led to the development of energy-saving technologies and lean manufacturing practices. By optimizing heating, cooling, and cycle times, manufacturers can reduce energy consumption and greenhouse gas emissions, aligning with global sustainability goals.
Circular Economy Initiatives
Embracing the principles of the circular economy, PT plastic injection molding stakeholders are exploring innovative approaches to resource management, product lifecycle assessment, and waste reduction. Collaborative efforts across the supply chain, from material suppliers to end-users, are essential for achieving a circular economy model that maximizes resource efficiency and minimizes environmental impact.
Future Prospects and Recommendations
Looking ahead, the future of PT plastic injection molding holds immense promise for continued innovation and sustainability. Research endeavors focused on advanced materials, digital manufacturing technologies, and circular economy strategies will drive the evolution of PT plastic injection molding towards a more efficient, resilient, and environmentally conscious future.
In conclusion, PT plastic injection molding stands as a cornerstone of modern manufacturing, offering unparalleled versatility, efficiency, and innovation across diverse industries. By understanding its applications, technological advancements, environmental considerations, and future prospects, stakeholders can navigate the evolving landscape of PT plastic injection molding with foresight and sustainability at the forefront of their endeavors.
GETTING A QUOTE WITH LK-MOULD IS FREE AND SIMPLE.
FIND MORE OF OUR SERVICES:
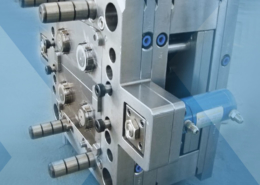
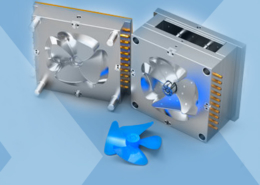
Plastic Molding

Rapid Prototyping
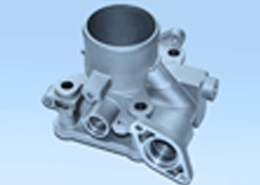
Pressure Die Casting
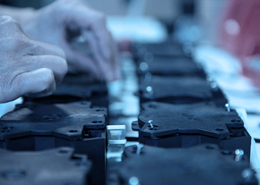
Parts Assembly
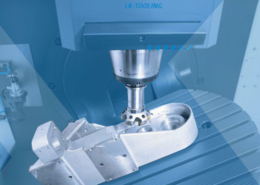