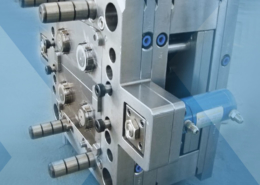
Injectables maker Maiva Pharma raises ₹1,000 crore to set up new
Author:gly Date: 2024-09-30
For years automotive and aeronautics engineers have discussed (and begun to implement) MBD, a sea change in which all engineering data is delivered to manufacturing people (or to customers) not as stacks of 2D drawings and accompanying model files but as 3D model files with product manufacturing information (PMI) attached. A few small vendors (including Anark and Lattice 3D) have made a living making software to support MBD for companies such as Boeing and Ford.
For years CAD users looked at what Google and others were doing in search and wished something similar could find geometry. Advances in both software and hardware now make it possible to search by both shape and engineering attributes. Siemens PLM acquired technology for this a few years ago; more recently, Dassault Systèmes acquired Exalead for its search technology.
Solidworks is now rolling out its 2015 portfolio, and while there is truly interesting news to report about Solidworks and several of its add-ons, the real news is a weather report: the dark cloud is gone. “Solidworks is not going away,” said division CEO Bertrand Sicot, specifically in reference to the core CAD product. He said it could easily be around in its current form another 10 to 15 years. This year’s updates prove the company is serious about keeping its flagship software fresh and vital.
When 3D CAD started to take off in mechanical engineering, it was a tool for design. When a design was complete, the data was passed along to others for QA/inspection, costing, simulation and analysis, tooling, and documentation; there was considerable rework in 2D. With each annual release of the Solidworks portfolio, the company has provided more tools to keep the larger engineering/manufacturing process inside Solidworks longer.
Another way Solidworks is delaying the handoff is with a new way to extract and display assemblies. Treehouse is a slick tool in core Solidworks for visual assembly structure planning, creation, editing, and viewing. It is an old idea with its roots in the Computervision era, but it’s now possible to implement it in a modern interface.
Much of what Solidworks does with each release is make hundreds of little improvements that keep users coming back for more. Notable among the 2015 tweaks are these advances:
Since 2010, a dark cloud of questions has been hanging over the Solidworks division of Dassault Systemés regarding the future of the company’s eponymous, market-leading 3D CAD software. Several “look but don’t touch” demos of “possible future software” and statements about the next generation of Solidworks switching to the same geometry technology as Catia, which is not perfectly compatible with the Solidworks core geometry, kept customers and resellers muttering about the future.
Arrays of sun-tracking mirrors called heliostats concentrate thousands of watts of heat onto the mould, heating it quickly without the emissions and cost of natural gas. Depending on local market conditions product cost 15-30% less to make with SRM than traditional equipment.
Solidworks claims the use of MBD for drawingless product detailing and 3D PMI delivery can save up to 50% on product development costs, by reducing rework, scrap, tooling, and fabrication. Solidworks MBD supports both 3D PDF, fast becoming an industry standard, and its own eDrawings 2D/3D display technology, which is popular among Solidworks users.
LightManufacturing is a company innovating in sustainable plastic moulding with its Solar Rotational Moulding (SRM) process. Unlike traditional methods that heat moulds with fossil fuels, SRM uses a system of mirrors (heliostats) to concentrate sunlight. This process significantly reduces the environmental impact of plastic production.
Previews of new software for the Solidworks portfolio based on what Dassault now calls the “3D Experience” platform only made the cloud seem more ominous. Dassault’s 3D Experience platform includes a common interface program with technology that allows companies to create shared information systems around a project. The 3D Experience tool will help tie together Dassault’s CAD and PLM products including Catia, Simulia, Enovia, Delmia, and Solidworks. The 3D Experience Platform app provides access to content created in Dassault’s products and also information related to a project via a common interface.
Due to low CapEx (@ 10% of a traditional factory/machine) it is cost effective to run multiple systems in parallel during sunlight hours, then if needed do secondary operations on a second shift.
In some markets like Hawaii LM sell product B2C (direct to customer); there we sell water tanks at prices 30-40% less than our traditional rotomoulding competitors.
In contrast, we radiatively heat the mould using the solar beam and largely avoid heating anything else in the chamber. Thus, we can use servo and stepper motors in the chamber, put active temperature monitoring systems permanently in the chamber, and generally use a wide range of sensors and electronics not available in traditional machines. We can monitor mould surface and internal mould air temperatures, mould position, beam intensity, and much more.
Our machines adapt cycle times to varying solar conditions and always produce a well-cured part - likewise the machines automatically begin cooling with fans, cool the parts to an ideal de-moulding temperature then ‘beep’ and stop, waiting for the operator to remove the finished product.
Our CONEX containerised systems are transported like any other shipping container (crane/truck/forklift etc) and don’t require infrastructure - e.g. a building with a poured concrete floor, utilities, etc. They are placed directly on the ground, and our heliostats deploy on weighted ‘pods’ which require no digging. This factory in a box approach is highly scalable, and even re-deployable if market conditions change. No sunk costs!
Editor Rebekah Jordan spoke to LightManufacturing's CEO Karl von Kries to learn more about the company's SRM systems that can achieve even heat distribution through a combination of mould rotation and controlled heating during sunlight hours. The interview also delves into the technology's high level of automation, which allows for precise temperature control and consistent part quality.
Coming later this year to the Solidworks portfolio will be Exalead Onepart, software for searching corporate databases by part attribute or shape. The initial installation will be time consuming and pricey but worth it not only for finding parts but for weeding out duplicate parts in inventory. No word yet on price or maintenance cost.
Our Solar Rotational Moulding (SRM) systems reflect heat from the sun onto a rotational mould to eliminate the need for fossil fuels.
As mentioned above, we estimate CapEx for SRM is @ 10% of traditional moulding systems including building / infrastructure costs. This is important, but quickly dwarfed by the reduction in product cost. Also important is our ability to supply customers and markets from nearby locations; because deploying SRM does not require infrastructure but just ‘raw land’ we deploy near-to-the-need and greatly reduce transportation costs and associated emissions. LightManufacturing currently does not offer SRM systems for sale, but rather provides moulding-as-a-service for partner brands.
The Solidworks portfolio now consists of 19 separate products, including a variety of tools for simulation, plastic injection molding, electrical engineering, and technical documentation. While many of these products are tuck-ins that appear inside Solidworks, several are complementary applications that have their roots not in Solidworks but in the 3D Experience technology that shapes the rest of Dassault’s products.
A few years ago Solidworks introduced a costing module, which was an instant hit among users. This year Solidworks introduces Inspection, another plug-in and standalone application to automate the tedious process of creating inspection sheets. The entry-level version costs $1,995 plus $599 for the annual subscription. For an extra $1,500 (and $1,049 maintenance), there is a premium version that enables users to enter measurements and collect inspection values from CMM software.
But the MBD conversation always seemed to be at the high end of the market. Three recent changes are bringing MBD to mainstream engineering:
In 2005 Solidworks surveyed its user base and found 1.5% of them wanted to use MBD. A similar survey last year found 16% wanting to use MBD in Solidworks. The product will be sold separately from the regular Solidworks packages. The initial license fee is $1,995 plus an annual $495 subscription for support and future upgrades. Those 16% of users will provide more than enough early adopters to justify the development.
This is a key point: our system are ~highly~ automated in a way not possible with traditional systems. Recall that traditional moulding systems have the mould in a 300C+ oven, deadly to servo motors, complex electronics, many sensors etc. It’s a harsh environment. As a result most traditional moulding systems temporarily monitor plastic temperatures using a sensor package in a chilled box, then use a ‘best guess’ for how long to cook the part.
Solidworks is the first mainstream CAD company to respond, introducing Solidworks MBD as a new product in the 2015 portfolio. The product enables Solidworks users to fully implement ANSI standard Y14.41, which specifies how 3D annotations should be attached as named views to 3D models. To our knowledge, no other mid-priced CAD vendor has accomplished this.
Any thermoplastic used in traditional rotomoulding can be used in SRM - most common resins are polyethylene and polypropylene, but PVC, Nylon, and Polycarbonate are also rotomolded.
Rotation in two axes (typically at one to five revolutions per minute) does an excellent job of averaging out small variations in heat intensity, and of course steel or aluminium moulds convey heat laterally across the mould surface to even out temperatures. But most importantly, our patented control systems actively speed up and slow down the mould as each face passes through the solar heat beam to achieve target temperatures - to the extent that we can heat certain mould faces more (producing thicker plastic in that area) or heat other faces less (forming a thinner part in that area). This per-face thickness control is difficult to achieve in traditional moulding, yet we can do it ‘programatically’. An example of how this is useful: we can mould water tanks with extra thick bottoms for durability, but thin upper walls to save plastic.
Production volume varies greatly with product size, wall thickness, can multiple tools be mounted at once, etc. Cycle times are similar to traditional gas fired moulding (that is to say, heating times are similar - cooling times tend to be faster because we radiatively target the tool, not the surrounding machinery and thus there is less mass to cool).
GETTING A QUOTE WITH LK-MOULD IS FREE AND SIMPLE.
FIND MORE OF OUR SERVICES:
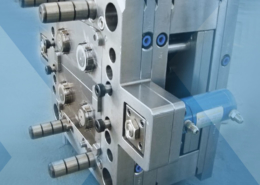
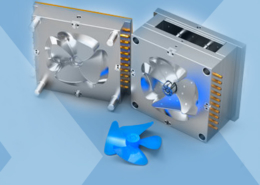
Plastic Molding

Rapid Prototyping
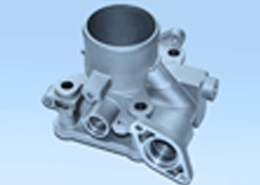
Pressure Die Casting
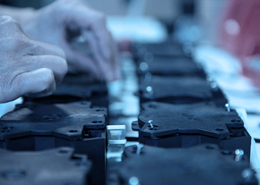
Parts Assembly
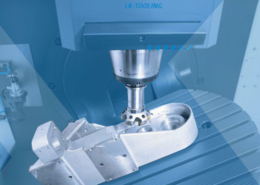