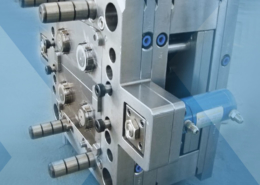
Industrial Molding Corp. Sold to Private Equity Firm - molded plastic products
Author:gly Date: 2024-09-30
About Prophecy Market Insights:Prophecy Market Insights is specialized market research, analytics, marketing/business strategy, and solutions that offers strategic and tactical support to clients for making well-informed business decisions and to identify and achieve high-value opportunities in the target business area. We also help our clients to address business challenges and provide the best possible solutions to overcome them and transform their business.
The research project is also investigating possible ways to automate data matching and the adaptation of neural networks. Manufacturers not only gain the benefit of improved data quality from optical inspections, they can also design their entire process to be as rigorous and error-free as possible, even in complex production environments where a variety of different parts need to be tested.
The Global Plastic Injection Molding for Medical Device Market accounted for US$ 82.7 million in 2020 and is estimated to be US$ 148.88 million by 2030 and is anticipated to register a CAGR of 6.1%. The global plastic injection molding for medical device market report segments the market on the basis of type, end-user, and region.
A research project is exploring new avenues for AI-assisted automated optical quality assurance during the injection molding process.
Some potential challenges for the plastic injection molding for medical device market in the future include increasing competition, regulatory changes, and the need for more sustainable and eco-friendly materials. Opportunities include advancements in technology and materials science, increased demand for medical devices due to aging populations and the prevalence of chronic diseases, and growing healthcare infrastructure in emerging markets.
Some key challenges faced by manufacturers of plastic injection molding for medical devices include meeting regulatory requirements, ensuring product consistency and quality, managing costs, and keeping up with advancements in technology and materials.
The molded parts are serialized using individual QR codes and sorted onto trays. While production is still in progress, Kistler’s ComoNeo system monitors cavity pressures via pressure sensors. With support from appropriately trained AI, ComoNeoPREDICT software generates quality predictions for the individual parts. Driverless transport vehicles convey parts selected for spot checks to the optical test cell. This is the first time autonomous transportation has been used in this context. The parts then pass through the predefined inspection program and are checked for dimensional stability and surface defects as well as injection molding anomalies, such as black specks or moisture splay. Issues specific to plastics processing such as shrinkage due to cooling and crystallization are also taken into account.
The objective is to achieve consistently smooth and efficient part handling throughout the entire test process. Integrated safety concepts monitor the systematic progression of the individual steps in the process — as well as the “handshakes” — to guarantee process reliability while preventing data loss. The automatic system then sends the collected data via an OPC UA interface to the operator's higher-level quality assurance system and to relevant databases for analysis.
When starting to design an inspection concept of this sort, the focus initially is on the requirements for the part being tested. The project team collaborates with manufacturers to develop the required quality-relevant test parameters, mostly related to surface defects and dimensional accuracy. They also identity the appropriate test methods. Kistler-developed sensors make it possible to integrate mechanical pressure and force and torque tests. Experts from the company’s competence center then design the test cell accordingly. In addition to determining the number and positioning of camera stations with lighting elements, the key factor at this stage is outlining the inspection path for the part.
Following inspection, the autonomous vehicle transports the tested parts to the warehouse and the test cell sends the analyzed data to higher-level QA or MES systems. Experts can then compare the quality data with the quality forecasts previously generated by ComoNeo PREDICT. If variances occur, the AI models are retrained using new test data.
Additional injection molding machines producing different parts can be integrated into this setup and incorporated into the material flow with the use of autonomous vehicles. In other words, the concept allows for automation of quality control in complex production environments as long as the test cell is equipped with the appropriate inspection programs: The inspection system recognizes the different parts and triggers the relevant test program.
There are various applications of plastic injection molding in the medical device industry, such as manufacturing of diagnostic equipment, drug delivery systems, surgical instruments, disposable devices like syringes, IV tubing, and catheters, orthopedic implants, and dental instruments. Plastic injection molding is also used for producing housings, covers, and enclosures for medical devices.
Autonomous vehicles transport parts to the test cell and storage area. Image courtesy of OST – Ostschweizer Fachhochschule.
Covina, March 16, 2023 (GLOBE NEWSWIRE) -- The Plastic Injection Molding for Medical Device Market accounted for US$ 82.7 million in 2020 and is estimated to be US$ 148.88 million by 2030 and is anticipated to register a CAGR of 6.1%. The medical plastic injection molding process is cost-efficient, and ideal for top volume production runs and applications requiring consistency and tight tolerances. This molding process is additionally used for medical device prototype development for the FDA approval process and to be used in laboratory testing. Since inception, the utilization of plastics within modern medicine has steadily increased. Medical devices that are manufactured from injection molded plastic have contributed to a discount in medical costs, communicable disease and pain management. High tech polymers are used within medical device prototype development and are commonly wont to create improved artificial limbs and devices that reduce the danger of infection. Medical plastic injection molding directly results in increased patient safety and therefore the ability to save lots of more lives. Since medical device plastics provide increased versatility and may be combined with metal to make enhanced medical product attributes, medical grade plastics became the well-liked material for varied sorts of electronic medical devices.
The research project with the IWK Institute for Materials Technology and Plastics Processing is focused on injection molding of a medical part. The objective is to develop a system that provides medtech manufacturers with comprehensive automated random sample inspection, generating accurate AI-based quality predictions while injection molding is still in progress.
Switzerland-based Kistler, a developer of measurement systems and sensors, is collaborating with the Eastern Switzerland University of Applied Sciences (OST) in researching advanced quality-control technologies. In particular, Kistler is involved in a project with the university’s IWK Institute for Materials Technology and Plastics that fully automates the inspection of injection molded parts while harnessing the power of AI to hone quality predictions while injection molding.
Analyst View:Increasing technological advancements in plastic injection molding techniques to make sure medical products are free from contamination and safer is additionally expected to drive the expansion of the respective market. Rising healthcare expenditure and spending in both developing and developed economies are among the crucial factors anticipated to bolster the worldwide plastic injection molding for the medical device market. Moreover, the growing global geriatric population, including the prevalence of chronic diseases, is another factor expected to fuel market growth.
Quality control is an essential aspect of the production process, especially when it involves parts used in automotive and medical technology applications. The entire quality control process must be designed to ensure maximum precision and reproducibility, and typically requires reams of documentation. All of this is labor-intensive and time-consuming, and is reliant on expert personnel. Automation coupled with artificial intelligence (AI) may offer an alternative.
The market provides detailed information regarding the industrial base, productivity, strengths, manufacturers, and recent trends which will help companies enlarge the businesses and promote financial growth. Furthermore, the report exhibits dynamic factors including segments, sub-segments, regional marketplaces, competition, dominant key players, and market forecasts. In addition, the market includes recent collaborations, mergers, acquisitions, and partnerships along with regulatory frameworks across different regions impacting the market trajectory. Recent technological advances and innovations influencing the global market are included in the report.
The process can be burdensome, as the samples are removed, transported, and tested manually, tying up resources. Moreover, the quality of the data depends on the skills and expertise of the personnel performing the inspections. Critical parts may have narrower tolerances and require more frequent spot checks, increasing the potential for human error. Automated, reproducible random sample testing can optimize the process.
Dr.-Ing. Oliver Schnerr is head of sales, Integrated Solutions Automation Solutions / Vision Systems / Fastening Technology at Kistler.
Manufacturers typically rely on statistical process control (SPC) to verify quality. The frequency and scope of sample testing is defined, enabling users to monitor the production process according to predefined quality parameters.
There are several factors that are driving the growth of the plastic injection molding for medical device market, including:
GETTING A QUOTE WITH LK-MOULD IS FREE AND SIMPLE.
FIND MORE OF OUR SERVICES:
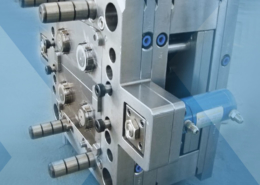
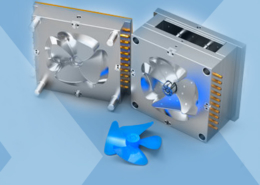
Plastic Molding

Rapid Prototyping
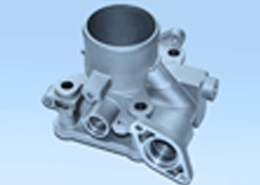
Pressure Die Casting
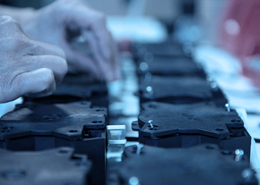
Parts Assembly
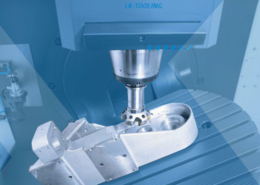