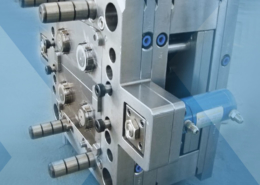
Induction Heated Molds Produce Class A Thermoplastic Composites - heat plastic t
Author:gly Date: 2024-09-30
In collaboration with multiple partners, Arburg will showcase IML for centrifuge tubes at Fakuma 2023, eliminating printing or other downstream steps.
Wittmann Battenfeld used its own Cellmould gas-injection process and variotherm molding with the aid of the BFMold (ball-filled mold) technology. The latter sends water through a mold chamber filled with ball bearings to ensure uniform flow across the mold and quick temperature transitions. After demolding, the flat ABS parts were exposed to ionized gas to burn off silicone-oil mold release and then pad printed.
More productivity with less energy consumption and capital investment; more operations in the machine or manufacturing cell with less time, labor, energy, and capital—these were the common themes of injection molding exhibits at October’s K 2013 show.
As noted above, micromolding and LSR sometimes overlap. The Babyplast desktop micromolding machine (see above) now can mold standard two-component LSR, rather than just premixed cartridges as before. It also boasts upgraded controls with pressure switchover capability, increased mold area (75 x 75 mm), energy-saving electric inverter drive for the hydraulic pump, and a new parts picker controlled by the machine.
Of Engel’s two thermoset composite demonstrations, one involved high-pressure resin-transfer molding (HP-RTM) of a latch cover for a KTM’s X-Bow sports car. Dry carbon and glass fabrics were impregnated with liquid two-component PUR in a new large vertical two-platen press, v-duo 700 (700 m.t.), which was developed specifically for composites. It is about 60% lighter in weight and 50% shorter in height than conventional presses. Platen parallelism control during molding is standard, as is energy-saving servo-hydraulic ecodrive. The clamp is accessible from all four sides for easier maintenance and simpler automation.
Discover how artifical intelligence is revolutionizing plastics processing. Hear from industry experts on the future impact of AI on your operations and envision a fully interconnected plant.
Japan Steel Works (JSW, with U.S. office in Lake Zurich, Ill.) exhibited a new enhancement to its Die Slide molding process for making hollow parts by molding two halves in separate cavities of the same mold, and then bringing them together via a sliding plate and overmolding the seam between them to provide a seal. The new wrinkle is integrating a hot-plate heater to soften the mating surfaces to be joined, for a better seal.
This Knowledge Center provides an overview of the considerations needed to understand the purchase, operation, and maintenance of a process cooling system.
Although the disposal of PLA sheets also produces the greenhouse gas CO2, the emissions correspond to what the maize plants originally absorbed from the atmosphere. According to the company, the life cycle of its 96-well plates therefore produces half the CO2 emissions of conventional plates.Additionally, Green Elephant Biotech’s microtitre plates can now compete with their petroleum-based counterparts: “Manufacturing the first product that meets the high technical standards of laboratory consumables involved many challenges, such as ensuring high transparency for optical applications. However, the tests have shown that our sheets are competitive with conventional plastics in this respect, which proves that quality does not have to come at the expense of sustainability,” says Eichmann.
Tecnomagnete of Italy (U.S. office in Sterling Heights, Mich.) has increased the durability of its magnetic quick mold-clamping systems and has added the ability for the magnetic mounting plates to self-clamp magnetically to the machine platens with no mounting screws.
In this collection of content, we provide expert advice on welding from some of the leading authorities in the field, with tips on such matters as controls, as well as insights on how to solve common problems in welding.
In this three-part collection, veteran molder and moldmaker Jim Fattori brings to bear his 40+ years of on-the-job experience and provides molders his “from the trenches” perspective on on the why, where and how of venting injection molds. Take the trial-and-error out of the molding venting process.
August 29-30 in Minneapolis all things injection molding and moldmaking will be happening at the Hyatt Regency — check out who’s speaking on what topics today.
One area of injection molding that is seeing a burst of new creativity is the field of structural composites. Still in its infancy, it is capturing imaginations—and commercial applications—in the automotive field, primarily, but also potentially in computers and electronics. Up to now, there have been two main players in machinery, but the ranks are growing.
Processors with sustainability goals or mandates have a number of ways to reach their goals. Biopolymers are among them.
Use of Borealis PP and Bockatech’s EconCore next-generation foaming technology yields thin-wall, robust and fully recyclable cups.
Yudo of Korea (U.S. office in Plains City, Ohio), known here primarily for its hot-runner systems, has come out with an LSR mixing/metering system. It’s enclosed in a box that measures 1070 x 1270 mm x 1730 mm high and has a side door and a 10-in. touchscreen on the front. It dispenses up to 3.3 lb/min at up to 250 bar pressure and a 1:1 ratio. Yudo also offers cold-runner systems for LSR molds.
This month’s resin pricing report includes PT’s quarterly check-in on select engineering resins, including nylon 6 and 66.
Boy also introduced a free smartphone and tablet app for iOS or Android devices. It includes calculators for cooling times and clamp-force requirements, as well as data sheets for processing, drying, and density of common plastics. It also provides quick access to Boy sales, service, and process engineering personnel.
Elmet showed off recent upgrades to its TOP 3000 LSR metering systems. It has a new controller with a USB port, touchscreen, and WiFi connection (via a free app). The latter is said to be useful for clean rooms—it allows the dosing equipment to be located outside the clean room but it can be monitored and controlled from inside. For example, operators inside the clean room can see how much material is left and how long it will last at the current production rate.
Two interesting overmolding applications from Arburg: (Top) The tire of this toy wheel was first molded of PP expandable bead foam and then inserted in an injection mold, where the inner wheel of PP and outer tread/skin of styrenic TPE were overmolded onto the EPP. (Bottom) A vacuum suction pad was produced by overmolding a threaded metal insert first with glass-filled PBT and then with LSR in the same machine.
While prices moved up for three of the five commodity resins, there was potential for a flat trajectory for the rest of the third quarter.
At the show, it took about 30 shots to change from white to blue and 33 shots from blue to silver. The system uses colorant containers pressurized to 10 bar and dispensing modules with servo screw pumps on the barrel, capable of injecting liquids at up to 150 bar. Both components come from ViscoTec in Germany (U.S. office in Kennesaw, Ga.). This approach can use any commercial liquid colorant or additive. Because the color is dispensed after the melting zone, the colorant experiences less heat history and less of the screw and barrel require cleanout for color changes.
At this show, Arburg made its debut in the composites field. A servohydraulic Allrounder 820 S (400 m.t.) combined organic sheet composite molding with DLFT (direct long-fiber thermoplastic) technology in molding a part similar to an automotive brake pedal. Two pieces of “organosheet” of glass fabric and PP copolymer were preheated at a two-sided infrared bank and placed robotically in the mold, where they were held in place by pins that pushed the fibers aside, rather than breaking them, when the mold closed. The sheet was formed into a 3D shape in the mold and overmolded with long-glass PP. Continuous glass rovings were fed directly into the injection barrel after the melting zone. The glass was chopped by the screw—in lengths continuously variable up to 50 mm—but fiber attrition was said to be minimized by feeding into already melted polymer. An extra-long 33:1 L/D screw was used.
This approach reportedly is simpler and more economical than mounting a twin-screw compounding extruder over the injection barrel, as has been offered by KraussMaffei and others. The 202 g part was molded in a single cavity with a 40-sec cycle time. The two pieces of organosheet—of different thicknesses—were bonded by the overmolded compound, which also sealed the edges of the sheet, producing a net-shape part that needed no trimming. The Krelus Infrared heaters from Switzerland turned on and off for each cycle to save energy.
Last December, Finnish Neste Oyj has partnered with Hamburg-based lab supplier Eppendorf AG to create a new line of renewable plastic lab consumables, Eppendorf Consumables BioBased, from cooking oil waste.
Sustainability continues to dominate new additives technology, but upping performance is also evident. Most of the new additives have been targeted to commodity resins and particularly polyolefins.
Plastic consumables used in pharmaceutical and biotechnological research must meet high quality standards. A German start-up has now launched the first sustainable product that is not based on petroleum chemistry: a 96-well microtitre plate The plastic for microtitre plates is made from corn starch.
Another IML supplier, which specializes specifically in digitally printed labels, is ZoMazz of Monterey, Calif. The advantage of what the firm calls “D-IML” is that it requires no setup time and costs, unlike offset lithography or screen printing. Continuous-tone digital printing makes short runs of a particular label more economical and shortens lead times.
In a time where sustainability is no longer just a buzzword, the food and beverage packaging industry is required to be at the forefront of this innovation. By adopting circular packaging processes and solutions, producers can meet regulatory requirements while also satisfying consumer demand and enhancing brand reputation. Join Husky to learn more about the broader implications of the circular economy — as well as how leading brands are leveraging this opportunity to reduce costs, increase design flexibility and boost product differentiation. Agenda: The cost and operational benefits of embracing circularity Key materials in circular packaging — including rPET and emerging bioplastics How to design a circular food and beverage package Strategies for selecting sustainable closures to future-proof packaging solutions Optimization and streamlining of production processes for enhanced efficiency How Husky Technologies can enable your sustainable success
In addition, the full benchtop Babyplast injection machine now is available with an electric turntable for two-shot molding.
Exhibitors and presenters at the plastics show emphasized 3D printing as a complement and aid to more traditional production processes.
Mixed in among thought leaders from leading suppliers to injection molders and mold makers at the 2023 Molding and MoldMaking conferences will be molders and toolmakers themselves.
WEB EXCLUSIVE: At K 2013, injection machine builder introduces the Freeformer, a novel machine for additive manufacturing.. But there was plenty to see in hot runners, LSR processing, and lightweighting as well.
The first half of 2024 is history, and experts are divided on whether the financing nadir has been reached or even passed. There are very different figures for different types of treatments under … more ➔
Since not everyone wants to buy a dedicated multi-component machine, add-on injection units offer a flexible and cost-effective way to convert standard machines when needed for a multi-shot job. Mold-Masters Ltd., Georgetown, Ont., which claims to be the largest supplier of auxiliary injection units, showed its expanded E-Multi line of electric units. New models are the EM4 (largest) and EM2 (second-smallest), for a total of 12 models with shot capacities from 7.7 to 500 cc. They have a new controller with a large touchscreen and high-end capabilities. In addition to floor and mold mounting, there’s a new platen-mount option with transverse and radial movements to allow the injector to swing out of the way for mold changes.
As reported in December, Elmet has explored new ways to utilize low-temperature UV-curing LSR formulations from Momentive Performance Materials, Waterford, N.Y. Elmet has built molds with polycarbonate inserts as a clear “window” through with to shine UV light to cure the part, but the plastic insert wears out after 5000 to 10,000 shots. Elmet’s newest solution, in the case of thermoplastic/thermoset overmolding, is to use the clear thermoplastic first shot as the window for UV light to reach the LSR in the second shot.
The Janus hybrid range (servo pump plus electric drive on screw and clamp traverse) has been upgraded with faster clamp motion since NPE 2012.
Since the first stage of the process clamped onto the glass fabric, leaving dry fibers along the edges, these were encapsulated by TPE in the final step. Total cycle was 6 min, though IKV sources said it could be cut to 3.5 min, depending on ambient humidity, which affects the nylon polymerization.
While prices moved up for three of the five commodity resins, there was potential for a flat trajectory for the rest of the third quarter.
Arburg will undoubtedly not be the last machine builder to tap into the composites action. Officials at Wittmann Battenfeld (U.S. office in Torrington, Conn.) said at the show that the company is looking hard at composites molding. In their view, the process requires less in the way of new injection molding technology than of adapting specialized automation—an area in which Wittmann feels it is well qualified.
Engel (U.S. office in York, Pa.) put on, or participated in, four demonstrations of different approaches to injection molding structural composites from oriented continuous fibers. As noted in our September preview, two of them involved thermoplastic composites and two of them thermosets. Both an automotive brake pedal and a case for a tablet PC were produced by overmolding or backmolding continuous-fiber thermoplastic prepreg sheets with additional thermoplastic. These are the first projects of Engel’s new technology center for lightweight composites in St. Valentin, Austria, which employs 15 people.
Next month’s mammoth triennial plastics show in Düsseldorf, Germany, challenges injection molding machine builders to demonstrate technological leadership in addressing the needs of the marketplace.
In addition, there’s a new smaller size of Bi-Power hybrid two-platen press; this 1000-m.t. model is now the lower end of the range, which previously spanned 1300 to 7000 m.t. Servo pump and electric screw drive are standard.
Engel’s new 770-ton vertical two-platen press (above) molded a composite latch cover for KTM’s X-Bow sports car using dry glass and carbon fabrics impregnated with liquid PUR by HP-RTM.
Despite price increase nominations going into second quarter, it appeared there was potential for generally flat pricing with the exception of a major downward correction for PP.
Given the increasing popularity of servo-driven hydraulic pumps for saving energy, Siemens Motion Control Business, Atlanta, introduced a new Sinamics servo pump for use on hydraulic presses. It combines a Sinamics S120 servo drive and a fixed-capacity pump. It’s said to be quieter than a variable-volume pump and easy to integrate into a molding machine. Sizes are from 7.5 to 90 kW. No additional PLC is required.
The fourth molding demonstration was exhibited by the Institute of Plastics Processing (IKV) at RWTH Aachen University in Aachen, Germany. It used dry glass fabrics impregnated with molten caprolactam monomer for in-situ polymerization to nylon 6. Six layers of fabric with binder were preformed with heat and vacuum in a tool with hot/cold cycling, then cut to shape. “Due to the extremely low viscosity of the monomer, even the finest fiber filaments can be infiltrated without damage, and therefore tailored fiber structures can be integrated to improve mechanical properties,” said Peter Egger, head of Engel’s composite technology center. The fabrics were injected and cured in one Engel tiebarless press (e-victory 120) and then the parts—soccer shin pads in two cavities—were transferred by robot to a second tiebarless press (victory 80) for overmolding with TPE. The same linear robot loaded the glass preforms in the first mold, transferred cured parts to the second press, and demolded the finished parts.
While the major correction in PP prices was finally underway, generally stable pricing was anticipated for the other four commodity resins.
This microcellular foam ASA/PC white-goods appliance part was molded with a very smooth, glossy surface using a raussMaffei AX electric press with the MuCell foaming process and Variotherm hot/cold mold-temperature control.
Multiple speakers at Molding 2023 will address the ways simulation can impact material substitution decisions, process profitability and simplification of mold design.
Though it requires specialized equipment and experience, liquid silicone rubber (LSR) or liquid injection molding (LIM) continues to attract molders’ interest. Among the numerous LSR exhibits at the show, Elmet Elastomere of Austria (U.S. office in Lansing, Mich.) showed off a micro-sealing part for wires in a medical device. It was only 1.6-mm long, and 0.1-mm thick, with0.3-mm ID. It had been molded in two cavities on a Wittmann Battenfeld MicroPower machine.
New eVesta all-electric models have linear bearings like the Canbio Evolution models, so there’s no grease on the tiebars. Beefed-up servo motors are said to boost clamp speeds by 30%.
The aim of this presentation is to guide you through the factors and the numbers that will help you determine if a robot is a smart investment for your application. Agenda: Why are you considering automation? What problems are you trying to solve? How and why automation can help Crunch the numbers and determine the ROI
Especially interesting about this cell was the use of a vision sensor to evaluate the parts’ surface gloss and smoothness with new software being developed by the Polymer Competence Center Leoben (PCCL) in Austria. As explained by PCCL senior researcher Dieter Gruber, PCCL is attempting to overcome previous limitations in gloss and surface-finish measurement, with closer correspondence to human vision. With conventional measuring instruments, he said, human observers may see little or no difference between measured gloss differences or may perceive a proportionally greater difference between two relatively close gloss values. “We attempt to measure the visibility of defects,” Gruber said, “not physical topography of the part, but what you can actually see.” The technology works for smooth and curved surfaces and is intended to become ready for market in the next few years.
Ultradent's entry of its Umbrella cheek retractor took home the awards for Technical Sophistication and Achievement in Economics and Efficiency at PTXPO.
Join Wittmann for an engaging webinar on the transformative impact of manufacturing execution systems (MES) in the plastic injection molding industry. Discover how MES enhances production efficiency, quality control and real-time monitoring while also reducing downtime. It will explore the integration of MES with existing systems, emphasizing compliance and traceability for automotive and medical sectors. Learn about the latest advancements in IoT and AI technologies and how they drive innovation and continuous improvement in MES. Agenda: Overview of MES benefits What is MES? Definition, role and brief history Historical perspective and evolution Longevity and analytics Connectivity: importance, standards and integration Advantages of MES: efficiency, real-time data, traceability and cost savings Emerging technologies: IoT and AI in MES
Formnext Chicago is an industrial additive manufacturing expo taking place April 8-10, 2025 at McCormick Place in Chicago, Illinois. Formnext Chicago is the second in a series of Formnext events in the U.S. being produced by Mesago Messe Frankfurt, AMT – The Association For Manufacturing Technology, and Gardner Business Media (our publisher).
Composites are hot: This demonstration part, similar to an automotive brake pedal, was molded by Arburg using PP/glass organic sheet overmolded with long-fiber PP produced from continuous rovings fed into the barrel downstream of the melting zone (below).
Gifted with extraordinary technical know how and an authoritative yet plain English writing style, in this collection of articles Fattori offers his insights on a variety of molding-related topics that are bound to make your days on the production floor go a little bit better.
And MGS Mfg. Group, Germantown, Wis., displayed its latest Universal Multishot (UMS) portable, servo-electric auxiliary injection unit. It boasts significantly improved repeatability and accuracy, and well as high nozzle touch force of up to 36,000 psi to prevent leaks. It uses no springs or belts to engage the nozzle. It's available in a mold-mounted version or on a portable cart together with hydraulics to power core pulls and vacuum controls for venting.
As reported last month, Trexel also announced at the show a new way to achieve lower density parts without sacrificing properties by combining MuCell with hollow glass microspheres from 3M.
Another add-on micro-injector is now available from Rambaldi & Co. of Italy, represented here by ALBA Enterprises, Rancho Cucamonga, Calif. (albaent.com). The Babyplast 1/10P hydraulic injector is adapted from the micro-machine of the same name. It has a color touchscreen display, wheeled cart containing the hydraulics and electronics, shot sizes from 3 to 36 cc, and injection pressures up to 2030 bar on the smallest unit. The control stores over 100 tool settings and a record of the last 20 cycles.
Bioplastics specialist Avantium N.V. has inked a 5-year agreement to supply Henkel with plant sugar based furandicarboxylic acid , a building block of PEF bioplastics. more ➔
Join this webinar to explore the transformative benefits of retrofitting your existing injection molding machines (IMMs). Engel will guide you through upgrading your equipment to enhance monitoring, control and adaptability — all while integrating digital technologies. You'll learn about the latest trends in IMM retrofitting (including Euromap interfaces and plasticizing retrofits) and discover how to future-proof your machines for a competitive edge. With insights from industry experts, it'll walk you through the decision-making process, ensuring you make informed choices that drive your business forward. Agenda: Maximize the value of your current IMMs through strategic retrofitting Learn how to integrate digital technologies to enhance monitoring and control Explore the benefits of Euromap interfaces and plasticizing retrofits Understand how retrofitting can help meet new product demands and improve adaptability Discover how Engel can support your retrofitting needs, from free consultations to execution
More productivity with less energy consumption and capital investment; more operations in the machine or manufacturing cell with less time, labor, energy, and capital—these were the common themes of injection molding exhibits at October’s K 2013 show in Dusseldorf, Germany. One article cannot cover the vast range of news at the show. This post-show report focuses mainly on news of interest to North American molders and on primary molding equipment. Robots, hot runners, and tooling will be covered in separate reports. And for a full picture of the news, refer also to our September show preview and December initial news report for developments that aren’t repeated here.
•A new name for many North American molders is Borche Machinery Co. (also spelled Borch) from China, with offices and spare-parts inventory in Ontario, Calif., and Hamilton, Ont. Borche also exhibited at NPE 2012. The company’s newest products are the BS-III Servo Series of toggle presses (60 to 1800 m.t.) and BU Ultra-Max Series of two-platen machines (500 to 6000 m.t.). Both have energy-saving servo pumps. Borche also offers BT Series hydraulic toggles (60 to 1800 m.t.).
The brake pedal was produced in cooperation with ZF-Friedrichshafen, which won an award a couple of years ago for the first thermoplastic composite brake pedal. That earlier design was produced in two steps—preforming and then overmolding the nylon prepreg sheet. The new version of the brake pedal at K 2013 was significant both for its more complex 3D shape and for its one-step process. The composite prepregs were heated and simultaneously preformed and overmolded in an Engel insert 200 vertical press with the aid of a six-axis robot and infrared oven with a shuttle system. The molded part required no trimming.
The Three R (Replacement, Reduction and Refinement) principles developed over 60 years ago provide a framework for more humane lab animal testing and, more importantly, less of it. A range of in-vitro … more ➔
The new touchscreen with process animation helps make control much simpler and easier. The user need enter only the shot weight and gas percentage desired. It displays gas level and pressure in storage tanks, as well as historical data curves and logs. Energy consumption reportedly has been cut in half, reducing operating costs. The equipment itself is also a little less expensive.
NPE2024: A slimmed-down version of Engel’s all-electric, e-mac injection molding machine is among eight displays, which also include LSR micromolding, quick mold changes and a cube mold.
When, how, what and why to automate — leading robotics suppliers and forward-thinking moldmakers will share their insights on automating manufacturing at collocated event.
Also new is the eVector series (650 to 1500 m.t.) with redesigned toggle clamp, wider tiebar spacing, longer stroke, and optional SmartEnergy pump. A wide-platen 1000-ton version has around 64 in. between tiebars.
“We are proud to be the first company in the world to produce disposable laboratory materials from PLA using the injection moulding process,” stressed co-founder and co-CEO Joel Eichmann. The sustainable solution not only reduces CO2 emissions compared to polystyrene, the production process for PLA is also less energy-intensive.
•Victor-Taichung of Taiwan, represented here by Fortune International, Somerset, N.J., has upgraded its all-electric Va II series (50 to 200 tons) in the past year with wide platens, redesigned toggle system, more robust clamp and injection units, low-friction linear guides on the injection unit, and the VPC2100 controller with a larger and higher-resolution touchscreen, graphical user interface, and optional remote monitoring.
On several new presses, Engel showed off its new CC 300 control. It can operate in conventional “component view,” showing functions and parameters related to injection, clamping, ejection, etc.; or else in new “task view,” showing information related to mold change, maintenance, startup, etc. Another new feature is the “e-move button,” the central operating element, which provides millimeter-precise accuracy and speed-sensitive control of all machine and robot movements. Pressing that one button starts the machine and initiates various motion sequences. The 21-in. HD touchscreen recognizes gestures—screens can be changed with a swipe, for example. Also, the operator interface panel can be set to swivel to different positions according to the preferences of different operators. The control recognizes an operator’s login and moves to the desired position automatically, and then retracts flat against the machine on logout. The CC 300 runs all CC 200 programs.
Meanwhile, Kistler of Switzerland (U.S. office in Amherst, N.Y.) has new sensors for liquid reactive molding processes such as HP-RTM or in-situ polymerization. These membrane sensors measure both vacuum and filling pressure in the tool. Kistler is also at the prototype stage with sensor systems for measuring both the pressure in the mold for forming heated composite sheet and the injection overmolding cavity pressure.
New figures published by the industry association European Bioplastics suggest a sharp increase in the production of sustainable plastics in the next two years and calls for policy support. more ➔
Core Technology Molding turned to Mold-Masters E-Multi auxiliary injection unit to help it win a job and dramatically change its process.
French bioplastics recycling specialist Carbios SAS and British recycling and waste management company FCC Environment want to establish a PET biorecycling facility in the UK. more ➔
KraussMaffei has a new animated, interactive simulation tool for visualizing complex production processes and individual process stages, such as demolding. The simulation tool is available for download to KM’s MC6 machine controller.
Also new from Priamus is the Priafit mounting sleeve for mold sensors. It combines the mounting nut and distance sleeve to make sensor mounting easier and less expensive.
Otto Männer GmbH of Germany (U.S. office in Lawrenceville, Ga.;) showed off new compact, highly precise electric injection units adapted from its unusual micromolding system (see below). Called duo-män, these add-on injectors come in shot capacities from 0.42 to 31.92 g of PS. One of these was shown in use at the booth of Fanuc (represented here by Milacron), where it was integrated with Fanuc’s Roboshot all-electric press.
While the melting process does not provide perfect mixing, this study shows that mixing is indeed initiated during melting.
Priamus also has a new BlueLine voltage module for measuring injection analog machine signals in the control cabinet and converting them to digital signals for the company’s BlueLine digital control devices.
In addition, MGS showed a new version of its servo-driven UMS rotary platen, which has been made significantly thinner. It's now 5.9 in., down from 7.1 in., while being simultaneously more robust in its indexing mechanism, which uses cam followers.
Join Engel in exploring the future of battery molding technology. Discover advancements in thermoplastic composites for battery housings, innovative automation solutions and the latest in large-tonnage equipment designed for e-mobility — all with a focus on cost-efficient solutions. Agenda: Learn about cutting-edge thermoplastic composites for durable, sustainable and cost-efficient battery housings Explore advanced automation concepts for efficient and scalable production See the latest large-tonnage equipment and technology innovations for e-mobility solutions
One of the most frequently demonstrated technologies at the show was multi-material or multi-color molding, either using overmolding or in-mold assembly, or both. Almost all major suppliers showed something in this vein (see September preview).
A novel method of multicolor molding with one injection barrel was introduced by Sumitomo (SHI) Demag (U.S. office in Strongsville, Ohio). Its novel activeColorChange system was set up to feed three liquid colors to the machine barrel downstream of the melting zone. After a preset number of shots, the system switched colors.
KraussMaffei (U.S. office in Florence, Ky.) demonstrated an expanding range of capabilities in continuous-fiber composite overmolding with a complex application using fabric-based organic sheet, unidirectional tape, and a hollow section. The automated molding cell was based on a CX 300 (300 m.t.) two-platen press with a six-axis robot mounted on the fixed platen. The overall shape of the part was a square, hollow channel with a flat cover. The process involved preheating two sheets of nylon 6/glass-fabric sheet in a hot-air convection oven, which KM said provides more uniform heating than radiant infrared. In one mold cavity, one sheet was formed into a long U-channel shape and overmolded with ribs in glass-filled nylon. Overmolding also filled out the outer contours of the part to produce a net shape that needed no trimming. In addition, fiber-spreading devices created functional holes in the part.
Thousands of people visit our Supplier Guide every day to source equipment and materials. Get in front of them with a free company profile.
Take a deep dive into all of the various aspects of part quoting to ensure you’ve got all the bases—as in costs—covered before preparing your customer’s quote for services.
In this collection of articles, two of the industry’s foremost authorities on screw design — Jim Frankand and Mark Spalding — offer their sage advice on screw design...what works, what doesn’t, and what to look for when things start going wrong.
The biologics contract development and manufacturing (CDMO) market is experiencing rapid growth and is dominated by global players with investments in large scale stainless steel capacity. But is larger always better? Not necessarily says Celonic, a mid-sized, privately owned CDMO, who has … more ➔
•Fu Chun Shin Machinery (FCS) of Taiwan, represented here by Maruka U.S.A. Inc., Pine Brook, N.J. (marukausa.com) introduced the SD series of servohydraulic toggle presses. These are the former HT Series with a redesigned exterior shape for a sleeker look. The first model is the SD-150 (150 tons), and future models will range from 30 to 1420 tons.
•Negri Bossi (U.S. office in New Castle, Del.) showed off its new “Evolution” program of redesigns and upgrades for several of its press lines, signified by a small “e” added to the name. New eCanbio hydraulic toggle presses have prismatic linear bearings on the moving platen, eliminating tiebar bushings. This is said to result in faster movements and more accurate mold alignment. Platens have also been engineered to reduce mass, and tiebar spacing has been enlarged on all Canbio presses. It’s available in a “FAST” version with accumulator and SmartEnergy variable-volume pump with variable-speed inverter drive. The latter is said to use only 10% more energy than an all-electric machine.
•Arburg’s new machine is the Allrounder 820A (400 metric tons), which was shown with the new 2100 size injection unit. The latter increases the shot capacity to 1286 g of PS. (U.S. office in Newington, Conn.).
Learn about sustainable scrap reprocessing—this resource offers a deep dive into everything from granulator types and options, to service tips, videos and technical articles.
Priamus (U.S. office in Brunswick, Ohio) has adapted its FillControl system for automatic hot-runner balancing with the ability to balance multicavity filling of LSR in cold-runner systems. The solution is again the automatic detection of the flow front via cavity pressure or temperature sensors and the automatic delay of the valve-gate opening to achieve equal filling. Essential to control of very low-viscosity LSR are use of pressure sensors with twin seals and new control software that can measure less than 1 bar pressure change in the mold.
All-electric, hybrid, hydraulic, and servo-hydraulic: Machines of every size and stripe made their debuts from suppliers across the globe. In September, we previewed many of these new entries from firms such as Arburg, Athena Automation, Boy Machines, Engel, Haitian, KraussMaffei, MHS, Negri Bossi, Netstal, Sumitomo Demag, and Wittmann Battenfeld.
Mold maintenance is critical, and with this collection of content we’ve bundled some of the very best advice we’ve published on repairing, maintaining, evaluating and even hanging molds on injection molding machines.
Across all process types, sustainability was a big theme at NPE2024. But there was plenty to see in automation and artificial intelligence as well.
Mike Sepe has authored more than 25 ANTEC papers and more than 250 articles illustrating the importance of this interdisciplanary approach. In this collection, we present some of his best work during the years he has been contributing for Plastics Technology Magazine.
Plastics Technology covers technical and business Information for Plastics Processors in Injection Molding, Extrusion, Blow Molding, Plastic Additives, Compounding, Plastic Materials, and Resin Pricing. About Us
Both KraussMaffei and Wittmann Battenfeld demonstrated ability to produce foamed parts with very smooth, glossy surfaces using Variotherm hot/cold mold-temperature cycling. KM molded a 127 g washing-machine cover of ASA/PC in an all-electric AX 130 press equipped for the MuCell microcellular process of Trexel Inc., Wilmington, Mass. Dynamic mold-temperature control was provided by the machine’s MC6 controller, which regulated a TCU from gwk of Germany. The latter uses a hot-water reservoir that allows quick change from hot to cold water circulating in the mold. The polished mold surface and placement of water lines as close as possible to the mold cavity contributed to the highly aesthetic result. Cycle time was 37 sec.
The other is a new two-shot version of Otto Männer’s micro-män micromolder. This unique, all-electric system is a complete production cell with molds that travel on a track around the periphery from injection to cooling, ejection, sorting, and quality-check stations. In the twin-injector version, the mold is filled at one injection station and shuttles to the second injector for overmolding before continuing on its way to other stations. One- and two-component systems are available with 5- and 15-m.t. clamps and two-stage screw/plunger injectors with shot capacities of 0.42 to 9.03 g of PS and pressure capability up to 3000 bar.
According to estimates, around 5.5 million tonnes of plastic are produced in life science laboratories worldwide every year. Material that cannot be recycled and is therefore incinerated. The start-up Elephant Green Biotech now offers 96-well microtitre plates made from bioplastics to replace the petroleum-based products and thus reduce emissions. Microtitre plates are among the most frequently used disposable products in laboratories and are mainly used for high-throughput analysis. They are usually made of polystyrene. Green Elephant Biotech uses cplant-based polylactic acid instead for the production of its microtitre plates.
Sumitomo Demag demonstrated its activeFlow Balance or Flow Front Control technology on its all-electric InteElect machine (it’s also available on the electric SE-EV series). This technology is designed to provide uniform filling of multiple cavities or single parts with hard-to-fill areas. It was demonstrated on a family mold at K. The system allows the material to decompress as it fills the cavities by halting the screw momentarily (around 0.3 sec) at the transfer point. Controlled deceleration and stop time prevent any screw bounce in the electric injection unit. After the pause, injection is completed, perhaps at a lower pressure and with reduced clamp tonnage to facilitate venting and minimize molded-in stresses.
In-mold labeling and decorating were demonstrated by numerous machine builders (see September preview). In addition, two IML/IMD film suppliers had interesting news. Verstraete IML of the Netherlands had its film labels running in 16 demonstrations at the show (photo). It showed off metallic IML that preserves a metallic look when a packager moves from metal to plastics. It also showed double-sided IML with printing visible inside and outside of clear containers; peelable IML that can be removed easily from packaging that is suitable for reuse by the consumer; barrier IML that adds oxygen or light barrier, SuperClear IML that produces packaging with a no-label look; and new MockUp IML that is digitally printed with short lead times at low cost.
As reported in December, Kortec, Rowley, Mass., introduced three-layer coinjection technology for making UV-barrier PET preforms for milk bottles. Kortec’s special nozzles produce preforms with white layers inside and out and a black light-barrier layer in the middle.
Meanwhile, Trexel announced that use of its MuCell physical foaming process has become much simpler and less expensive, thanks to the new T-Series of SCF (Super Critical Fluid) dosing and delivery systems. The system converts gaseous carbon dioxide or nitrogen into a supercritical fluid and injects precise doses through a port in the injection barrel. The new design is simpler and more compact, with no more bulky block on top of the molding machine.
One of the more elaborate examples was a cap molding demonstration—one of three—by Ferromatik Milacron (U.S. office in Batavia, Ohio). The cell used an F 270 all-electric machine with a second injector mounted at an angle on the moving platen. A turning-stack cube mold with two parting lines produced two-piece twist-top caps from two colors of PP with in-mold assembly. The mold from Foboha (U.S. office in Beverly, Mass.) had two parting lines, each with 8+8 cavities. After each 90° mold rotation, automation on both sides of the machine unscrewed one closure component and then screwed it onto the other part; then the assembly was ejected at the same station. Cycle time was 9.5 sec.
A print magazine focussing on start-ups in the life sciences! Like a catalyst, it aims to promote young companies in the life sciences with the right impulses. more ➔
Across the show, sustainability ruled in new materials technology, from polyolefins and engineering resins to biobased materials.
Wittmann Battenfeld teamed up two 5-ton, all-electric MicroPower micromolding systems for clean-room assembly and overmolding of a “lab-on-a-chip” (below). An enclosed conveyor transported parts between the machines.
Say “manufacturing automation” and thoughts immediately go to the shop floor and specialized production equipment, robotics and material handling systems. But there is another realm of possible automation — the front office.
As reported in September, Wittmann Battenfeld demonstrated a novel setup using two of its 5-ton, all-electric MicroPower micromolding systems, linked by an enclosed conveyor in a cell for clean-room two-shot molding and assembly of diagnostic “lab-on-a-chip” devices. Two unique new micromolding systems were in operation at K. Both are developments from companies known mainly for hot-runner systems. One is the 4-ton, all-electric M3 machine from MHS-Mold Hotrunner Solutions, Georgetown, Ont.
Second quarter started with price hikes in PE and the four volume engineering resins, but relatively stable pricing was largely expected by the quarter’s end.
Join KraussMaffei for an insightful webinar designed for industry professionals, engineers and anyone interested in the manufacturing processes of PVC pipes. This session will provide a comprehensive understanding of the technology behind the production of high-quality PVC pipes: from raw material preparation to final product testing. Agenda: Introduction to PVC extrusion: overview of the basic principles of PVC pipe extrusion — including the process of melting and shaping PVC resin into pipe forms Equipment and machinery: detailed explanation of the key equipment involved — such as extruders, dies and cooling systems — and their roles in the extrusion process Process parameters: insight into the critical process parameters like temperature, pressure and cooling rates that influence the quality and consistency of the final PVC pipes Energy efficiency: examination of ways to save material and energy use when extruding PVC pipe products
In this collection, which is part one of a series representing some of John’s finest work, we present you with five articles that we think you will refer to time and again as you look to solve problems, cut cycle times and improve the quality of the parts you mold.
While all this was occurring, the second organic sheet was preheated and bonded to piece of unidirectional nylon/glass tape applied for local reinforcement. Then this flat sheet (the “cover” for the channel) was placed in the second mold cavity, to which the first overmolded part had been transferred by the robot, and the two were joined under pressure while additional melt was injected along the seams. Two more holes were needle-punched into the part, and inert gas was injected into the hollow channel shape to prevent wrinkling and provide a smooth, flat surface. The robot had two different grippers to accomplish all these tasks. The overall cycle was 57 sec.
Zeiger Industries, Canton, Ohio, offers new modifications of plasticating units for sensitive materials—halogen-free flame-retardant compounds, clear polycarbonate, and high-flow rigid PVC for technical parts. Modified components include the continuous-taper end cap, nozzle, nozzle tip, screw design, and screw tip. Screws can utilize stainless-steel powder-metallurgy materials and longer tips for less shear.
Successfully starting or restarting an injection molding machine is less about ticking boxes on a rote checklist and more about individually assessing each processing scenario and its unique variables.
Resin drying is a crucial, but often-misunderstood area. This collection includes details on why and what you need to dry, how to specify a dryer, and best practices.
•As we reported in September, Netstal (U.S. office in Florence, Ky.) presented three new machines at the show, the all-electric Elion 2200 (220 m.t.), Elion 4200 hybrid with servo pump (420 m.t.), and Evos 4500 hybrid with servo pump (450 m.t.). At the show, Netstal previewed its plans for 2014:
Additive technology creates air pockets in film during orientation, cutting down on the amount of resin needed while boosting opacity, mechanical properties and recyclability.
The Plastics Industry Association (PLASTICS) has released final figures for NPE2024: The Plastics Show (May 6-10; Orlando) that officially make it the largest ever NPE in several key metrics.
After successfully introducing a combined conference for moldmakers and injection molders in 2022, Plastics Technology and MoldMaking Technology are once again joining forces for a tooling/molding two-for-one.
Four sizes of the T-Series are available, including one for small screws (<40 mm diam.) and small shots (10 to 120 g), a size range in which MuCell systems have not been cost-competitive before, according to Trexel. The smallest units are even less expensive and simple in design than other models.
A new cavity-pressure sensor from Kistler was previewed in September. Priamus also showed new sensors. These “heavy-duty” temperature sensors can be used at mold temperatures up to 320 C (608 F) for LSR and other thermosets, as well as high-temperature engineering thermoplastics. These sensors can be ordered with a hardened front for abrasive materials like powdered metal or ceramic compounds.
technotrans says climate protection, energy efficiency and customization will be key discussion topics at PTXPO as it displays its protemp flow 6 ultrasonic eco and the teco cs 90t 9.1 TCUs.
Here’s just a taste of the innovations on display, a selection of the top headlines not covered in our September show preview.
•Boy Machines (U.S. office in Exton, Pa.) brought out five new machines that come standard with energy-saving servo pump and EconPlast plasticating unit . One model was reported in September—the Boy 25 E (also available in a vertical-clamp version, 25 E VH) with 25 m.t. clamp. It offers three new injection units with “differential injection” capability. This refers to the flexibility to select either fast injection for thin-wall parts or very high injection pressure for hard-to-fill shapes. Other new models are the Boy 50 E, 60 E, 80 E, and 100 E (50, 60, 80, and 100 m.t.). The 100 E is a new, larger size for the company (the 90 E was previously the biggest). Boy has discontinued the 22, 55, and 90 models. All the new models also will have as standard the new Alpha 2 control with large touchscreen that accepts gestures for functions such as scrolling between screens.
Sumitomo Demag’s new activeColourChange system injects liquid colors under pressure into the melt stream. The system changes colors automatically after a preset number of shots.
This three-piece composite demonstration part was molded by KraussMaffei in a complex series of operations. One nylon/glass-fabric sheet was preheated and then formed into a channel shape and overmolded with ribs while functional holes were created by spreading the fibers without breaking them. The second organic sheet, for the flat “cover” was preheated, bonded to a piece of unidirectional nylon/glass tape for local reinforcement, and placed over the channel part in a second mold cavity. There the two components were bonded by pressure and overmolded around the edges, while inert gas was injected into the channel to ensure flatness and a smooth surface.
Plastics Technology’s Tech Days is back! Every Tuesday in October, a series of five online presentations will be given by industry supplier around the following topics: Injection Molding — New Technologies, Efficiencies Film Extrusion — New Technologies, Efficiencies Upstream/Downstream Operations Injection Molding — Sustainability Extrusion — Compounding Coming out of NPE2024, PT identified a variety of topics, technologies and trends that are driving and shaping the evolution of plastic products manufacturing — from recycling/recyclability and energy optimization to AI-based process control and automation implementation. PT Tech Days is designed to provide a robust, curated, accessible platform through which plastics professionals can explore these trends, have direct access to subject-matter experts and develop strategies for applying solutions in their operations.
Boy’s new EconPlast system (econplast.de) is a patented technology that addresses the fact that the injection barrel is the biggest energy consumer on the machine. Boy claims can it can cut energy consumption by 40% for barrel heating and 60% for plasticating. The system achieves more efficient heating by embedding the heater bands in grooves in the barrel and covering the entire barrel with insulation. Boy also claims faster heat-up times and more precise temperature control, as well as improved cooling of feed zones with much less energy loss. EconPlast is available for all barrels of 24 mm diam. or larger.
Boy introduced its largest press ever, the servohydraulic Boy 100 E, and a new plasticating unit, called EconPlast, which is said to cut energy consumption by about half.
Introduced by Zeiger and Spark Industries at the PTXPO, the nozzle is designed for maximum heat transfer and uniformity with a continuous taper for self cleaning.
Auxiliary injection units proliferate for multi-component molding: Männer (top) now offers duo-män compact all-electric, two-stage (screw/plunger) injection units from its micromolding system as auxiliary injection units for standard presses. Mold-Masters’ E-Multi family of electric auxiliary injection units (below) now comes in a wider range of sizes with a new touchscreen control and additional mounting options.
Radiopharmaceuticals have turned into a hot commodity when it comes to M&A financing and deals. Targeted therapies that employ high-energy attachments linked to antibodies, small molecules or … more ➔
GETTING A QUOTE WITH LK-MOULD IS FREE AND SIMPLE.
FIND MORE OF OUR SERVICES:
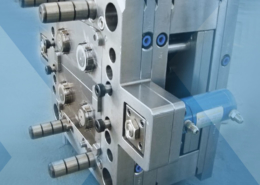
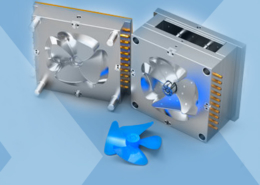
Plastic Molding

Rapid Prototyping
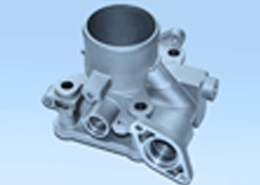
Pressure Die Casting
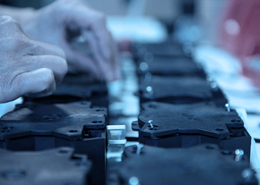
Parts Assembly
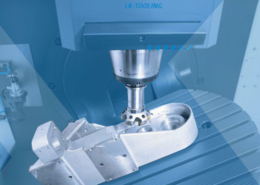