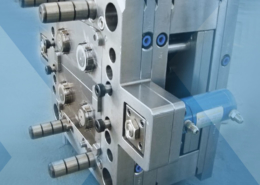
In MIM’s post-smartphone era, where is China’s Metal Injection Molding
Author:gly Date: 2024-09-30
Based in Worcester, MA, Absolute Haitian is the exclusive sales and service partner in the US and Canada for Ningbo Haitian Machinery Co., Ltd. based in Ningbo, China. Ningbo Haitian Machinery Co., Ltd. is the world’s largest supplier of plastics injection molding machinery, shipping an average of 43,000 machines each year. Haitian products are sold in more than 130 countries with machine sizes ranging from 44 to 7,425 tons of clamp force.
Working together in Italy, Unilever and Serioplast used 3D printing to rapidly create molds and produce pre-production sample bottles made of PET. The molds were built using Formlabs’ Rigid 10K Resin and Form 3L large-format, stereolithography (SLA) 3D printer.
The SLA 3D printing process enabled Serioplast to build resin molds in two days, a significant time savings vs. traditional machined metal molds (typically outsourced to a vendor), which take four to eight weeks to produce.
“We are talking about up to 30-bar pressure. It’s absolutely good and reliable on that. We are also talking about 100 °C heating for the [bottle] preform without any wearing on the cavity of the 3D printer mold,” says Flavio Migliarelli, R&D design manager at Serioplast, in a Formlabs video interview.
Absolute Haitian held an open house and luncheon September 28 for customers and industry members at its 116,000-square-foot applications center in Moncks Corner, SC, which opened in 2019. The event gave industry professionals the opportunity to view new technology, product introductions and more than 100 electric and servo-hydraulic stock machines and large-tonnage subassemblies ready for quick delivery.
To create the plastic molds, the team needed a resin that could endure the temperature and internal pressure of stretch blow molding and deliver dimensional accuracy and stability in the finished tooling. Formlabs’ Rigid 10K Resin provided the required strength, stiffness, and thermal resistance.
Haitian Precision was established in 2002 and offers a wide range of CNC machinery including vertical and horizontal machining centers, lathes, and dual-column machining centers. A preview of the new Haitian Precision product line at the open house included a TC25 II CNC lathe and a VMC850 II vertical machining center. Four vertical machining centers are currently in stock in South Carolina.
Through the art and science of 3D printing, “Something is on your screen, [and] in a short time is in your hands,” Cademartiri explains. “A real product with a real bottle, with a real cap, and the real label.”
So far, Unilever and Serioplast have tested about 15 bottle designs produced with the molds. Serioplast first created a standard mold design and print preparation and then modified the mold cavity for each unique bottle design.
Open house at 116,000-square-foot applications center in Moncks Corner, SC, featured more than 100 electric and servo-hydraulic plastic injection molding systems.
Zeres III electric molding machine – ZE 1500 / 210 III (169 U.S. tons) running a 4-cavity, thin-wall cup mold; cycle time of 10 seconds
The pilot included not only consumer testing but also primary validation of the bottle designs on Unilever’s filling line. This included bottle movement and how the containers functioned during filling, capping, and robotic case packing.
To produce bottles with the printed molds, Serioplast used the same blow-molding process window as for a metal pilot mold.
Printing the molds reduced tooling cost by up to 90% vs. metal molds. Specifically, the printed molds cost $500 to $1,000 to make vs. $2,500 to $10,000 for machined metal molds.
Additionally, Serioplast uses the printed molds to validate the stretch blow-molding process for the bottle designs. The company also performed dimensional analysis on the bottles and conducted performance evaluations, including bulge, cupping, and drop testing.
Attendees heard from industry experts in a series of quick-hitting “Tech Talks” geared towards providing high-value takeaways. Presenters included:
The ability to rapidly iterate bottle designs and molds speed pilot evaluations by enabling testing of multiple designs at the same time.
Mars III servo-hydraulic molding machine – MA 6500 / 6300h (730 U.S. tons) running a two-cavity flowerpot mold; cycle time of 18 seconds
Unilever and plastic-packaging manufacturer Serioplast Global Services are transforming stretch blowmolded bottle prototyping using 3D printing technology from Formlabs. The result is much faster, less expensive mold making and prototype production and testing.
Jupiter III servo-hydraulic, two-platen molding machine – JU 5500 / 4630 (618 U.S. tons) running a thick-wall electrical junction box mold
Kate Bertrand Connolly has been covering innovations, trends, and technologies in packaging, branding, and business since 1981.
On display were three operating injection molding machine cells and a static display of the electric Zeres III molding machine equipped with Haitian’s Medical Package introduced at K 2022. Injection molding machine cells in operation included:
Formlabs describes the resin as an industrial-grade, highly glass-filled material with a tensile modulus of 10,000 MPa. Molds printed from the resin exhibit good dimensional stability and tolerate hundreds of blow-molding cycles, with repeatability.
The printed molds also reduced lead time for pilot testing of blow-molded PET bottles. Lead time to produce 200 bottle samples using the printed molds was only two weeks, vs. the six to eight weeks required with conventional molds.
“The Formlabs machine plus the [Rigid] 10K Resin together offer the real possibility to have very good details on the bottles, [including logos or something] like a lemon detail, which requires a lot of precision,” says Stefano Cademartiri, CAD and prototyping owner at Unilever.
The Haitian Group introduced their Haitian Precision and Haitian Die Casting product lines to US and Canadian markets at the open house. Both business units’ products are now sold in Asia, Europe, Mexico, and South America. Distribution in the US and Canada will be handled by the Absolute Group with full-scale distribution in 2024.
Haitian Die Casting was established in 2016 and has quickly become of the largest suppliers of die-casting machines in the world. Haitian Die Casting offers standard machines sizes from 180 to 4,500 tons and is one of the few suppliers in the world with the manufacturing capability for die casting machines up to 9,000 tons. On display was an HDC550 with tonnage of 618 tons/560 tonnes.
Produced using the same resin and on the same blow-molding equipment as production bottles, the samples were ideal for pilot testing.
GETTING A QUOTE WITH LK-MOULD IS FREE AND SIMPLE.
FIND MORE OF OUR SERVICES:
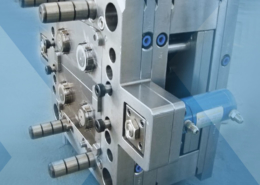
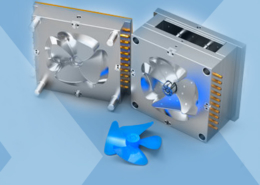
Plastic Molding

Rapid Prototyping
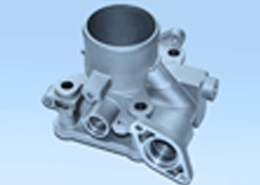
Pressure Die Casting
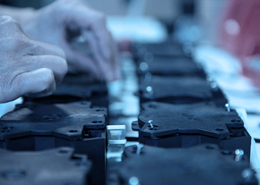
Parts Assembly
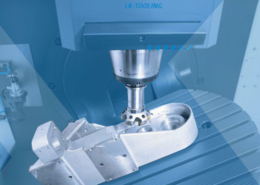