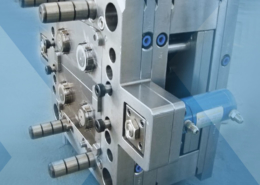
If oil is so cheap, why do my plastic parts stay the same price? - injection mol
Author:gly Date: 2024-09-30
Product take-out and insertion processes can be performed simultaneously during injection, reducing cycle time and improving productivity. Servo motors and drivers ensure precision molding and minimize product defects during production. A range of injection specifications, such as speed and pressure, are available to meet customer requirements.
hydraulic oil tanks and lines designed for reduced operating flow — approximately 45% — and cooling water consumption — approximately 30% — resulting in lower operating and maintenance costs, and improved sustainability.
The duo 5500 combi M represents the latest technology in injection molding, said Engel in the announcement. It features two movable (combined and individually operable) horizontal injection units and a combi M injection unit. It is also equipped with two six-axis Engel easix articulated robots for flexible and efficient automation.
The company aims to use this machine to explore technologies and mold components in completely new dimensions in collaboration with its customers and partners. The extra-large mold space accommodates molds weighing up to 150 tonnes, with possible shot weights up to a massive 42 kg. The state-of-the-art machine was developed to meet the demands of the automotive industry and technical injection molding and is now available for customer trials.
An energy-saving servo pump and closed-loop system that uses a high-powered AC servo motor to achieve 0.1% reproducibility through feedback control;
Until now, large plastic parts have often been manufactured using various processes other than injection molding, which have significant limitations. With the availability of an injection molding machine as large as the duo 5500 combi M in a technical center, extensive possibilities for part and technology development and sampling are now available. This offering reinforces Engel's role as an enabler of new technologies, allowing customers and partners to actively pursue developments in new dimensions and expand injection molding capabilities.
Manufacturers of large, complex plastic parts and toolmakers can now test feasibility and implementation at an early project stage. This significantly shortens time to market and avoids costly subsequent errors by identifying and eliminating sources of error early on. Initial customer trials are scheduled to begin shortly.
All digital assistance systems from Engel are integrated into the machine control, enabling energy-efficient, sustainable production while optimizing processes.
At NPE2024 in May, LS Mtron will exhibit a 170-ton LSG-V machine molding an electric vehicle component for sister company LS Automotive.
The LSG-V — known outside North America as the WIZ-VR II — previously was available in three models from 100 to 350 tons and only as a vertical rotary machine. The newly expanded line includes 13 models in varying tonnages with options for vertical or horizontal injection, and rotary table, shuttle, or single-station designs.
The automotive industry increasingly uses larger plastic parts to reduce vehicle weight, improve fuel efficiency, and lower production costs. Plastics offer design flexibility, enhance corrosion resistance, and contribute to the longevity and safety of vehicles. They also allow for the integration of functional elements and reduce the number of individual parts needed. Engel’s new facility supports this trend by enabling the production of larger plastic components.
The LSG-V hybrid system is intuitive and easy to operate and is equipped with features for enhanced operator safety, said LS Mtron.
Stephen has been with PlasticsToday and its preceding publications Modern Plastics and Injection Molding since 1992, throughout this time based in the Asia Pacific region, including stints in Japan, Australia, and his current location Singapore. His current beat focuses on automotive. Stephen is an avid folding bicycle rider, often taking his bike on overseas business trips, and a proud dachshund owner.
Engel reports that it has expanded its technical center in St. Valentin, Austria, with one of the largest injection molding machines from its standard portfolio — the duo 5500 combi M. With a clamping force of 55,000 kN and measuring 32 meters long, 13 meters wide, 6.8 meters high, and weighing 545 tonnes, it is by far the largest technical center machine in the world, according to Engel.
LS Mtron Injection Molding Machines USA has added several new models to its line of LSG-V vertical injection molding machines ranging in size from 35 to 660 tons.
The new Engel technical center facility covers all application areas for the automotive sector and technical injection molding.
For PU applications, two Cannon systems are available — one for small-volume applications and another for high-volume output. A corresponding dosing unit allows for coloring the polyurethane.
The LSG-V has a four-post tie-bar structure to ensure durability and stability. Additionally, users gain capacity with support for up to four injection fixtures, and the slide-type guide bar design minimizes transfer resistance.
Initially developed to mold large parts for the automotive sector, the press is now available for customer trials at the St. Valentin, Austria, technical center.
With the introduction of the duo 5500 combi M, Engel said it has reinforced its role as a leading hub for testing new technologies and collaborating closely with the industry to promote new injection molding possibilities. The machine allows for the testing and development of existing and new customer projects under real conditions and on neutral ground. This includes tool and material tests as well as the development of new manufacturing technologies.
GETTING A QUOTE WITH LK-MOULD IS FREE AND SIMPLE.
FIND MORE OF OUR SERVICES:
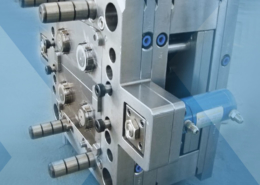
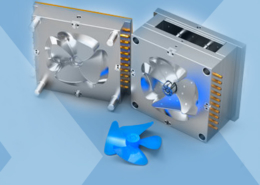
Plastic Molding

Rapid Prototyping
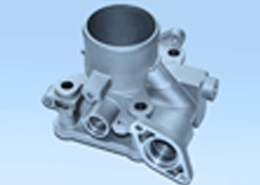
Pressure Die Casting
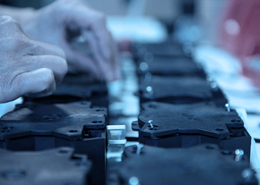
Parts Assembly
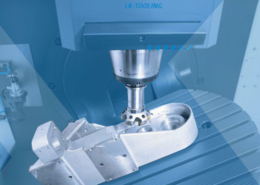