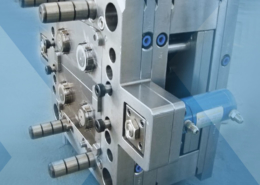
i-mold marks two decades in injection mould making - mould plastic injection
Author:gly Date: 2024-09-30
Fountas, N. A. et al. Modeling and optimization of flexural properties of FDM-processed PET-G specimens using RSM and GWO algorithm. Eng. Fail. Anal. 138, 106340. https://doi.org/10.1016/j.engfailanal.2022.106340 (2022).
Hsueh, M.-H. et al. Effect of printing parameters on the thermal and mechanical properties of 3D-printed PLA and PETG using fused deposition modeling. Polymers 13, 1758. https://doi.org/10.3390/polym13111758 (2021).
Material Extrusion (MEX) is defined by the ISO/ASTM 52,900:2015 standard as the “additive manufacturing process in which material is selectively dispensed through a nozzle or orifice”. SolidWorks 2019 was used to create all of the test specimen models. Ultimaker Cura 15.04.3 software was used for the slicing of the modelled specimens. The designed parts were converted to .STL files with reference to ISO/ASTM 52,900 standard. The Ultimaker Cura 15.04.3 software requires STL files to be imported. In this research, layer thickness of 0.1, 0.15, and 0.2 mm, printing temperature of 195, 200, and 205 °C, and printing speed of 50, 60, and 70 mm/s were chosen based on the manufacturer’s suggestion and the research gap. Most of the parameter settings were taken in a wide range which makes it more difficult to identify the precise process parameters. So, in this research, the process parameters were chosen in a close range in order to find out the exact optimal setting which results in improved mechanical properties. In the literature survey, it was reported that the reduced layer thickness exhibits better performance. So, in the research, all three layer thickness was chosen in a close range from 0.1 to 0.2 mm. These parameters were adopted to print the specimens (as shown in Table 2) and also a printing angle of 90°13 and 100% infill percentage were followed to print the PLA specimens in a set of experiments. These fixed parameters were taken from the literature where they have already proved that adopting those parameters shown improved performance when compared with the others parameters. Some of the already well know proven parameters settings are 100% infill density. Similarly, the Zig-Zag pattern was considered for this research based on the reference Yeoh et al.15. They have proved that PLA with zig-zag infill pattern has higher tensile strength of 23.409 MPa compared to PLA with grid and concentric infill pattern. These selected parameters are given as an input to the software. The diameter of the PLA filament was 2.85 mm, and it was extruded in the nozzle having 0.4 mm in diameter. The vertical (90°) building orientation with respect to ISO/ASTM 52,900 standard was assigned for printing tensile, impact and flexural specimen. Moreover, this orientation does not require support structure in reference to ISO/ASTM 52,900 standard. The G-code will be generated, and the generated G-code will be sent to the 3D printer as an input. The layer-by-layer printing operations was carried out in the 3D printer based on the supplied process parameters and G-code.
The impact (Izod) specimen was also built using the optimum criteria for evaluating impact strength. The defect such as porosity, poor adhesion, and molecular bonding had the most significant influence on enhancing impact strength. Cohesiveness and the structural morphology of the molecules are two intrinsic material attributes that substantially affect impact strength. Compared to the previous findings49, the maximum impact strength of 6.21 kJ/m2 was achieved with the optimal process parameters, indicating a 17.16% increase. This reveals that reduced layer thickness, proper printing speed, and appropriate printing temperature improve the impact strength of printed parts. Multiple fused layers with reference to ISO/ASTM 52,900 standard restricted the propagation of cracks with minimum thickness due to enhanced diffusion between the layers. The printing speed of 58 mm/s minimizes defects such as voids and porosity by building strong interfacial adhesion between the layers and enabling sufficient fusion time. Because these imperfections impaired the capability of the printed parts to absorb impact energy. The printed PLA was devoid of defects, as evidenced by SEM images of the impact fracture surface, as shown in Fig. 13.
Multi-criteria decision making (MCDM) approach assist to solve the decision-making problems where two are more responses are involved. In manufacturing process various MCDM techniques such as Techniques for Order Preferences by Similarity to Ideal Solution (TOPSIS), Grey Relational Analysis (GRA), Principal Component Analysis (PCA) etc. are adopted by expert and materials scientist to attain unique optimal solution for multi response problems. The main drawback in MCDM approach is the difficulties in proper allocation of weightage for each response viz. weightage are allocated with equal value for individual response. To resolve these issues, hybrid MCDM approach such as PCA weighted GRA, Entropy weighted GRA etc., are adopted for assigning weightage for each response based on their criteria. In this research Criteria Importance Through Intercriteria Correlation (CRITIC) embedded Weighted Aggregated Sum Product Assessment (WASPAS)40,41 approach is adopted to optimize the process parameters such as Layer thickness (mm), Printing speed (mm/s), Printing temperature (°C). Herein CRITIC approach is adopted to calculate the weightage of individual responses namely tensile and flexural strength of the printed components. This method bases the weights on how the choice problem's contrast intensity and conflict are evaluated. Additionally, this approach does not require human participation throughout the evaluation phase, which helps to automate the decision-making process. Further the calculated weights of each response will be assigned for WASPAS approach. The steps involved in CRITIC embedded WASPAS techniques is follows.
The compounds from Mitsubishi Chemical Advanced Materials are being used to replace aluminum and steel in structural applications.
Dawoud, M., Taha, I. & Ebeid, S. J. Effect of processing parameters and graphite content on the tribological behaviour of 3D printed acrylonitrile butadiene styrene. Mater. Werkst. 46, 1185–1195. https://doi.org/10.1002/mawe.201500450 (2015).
On the comparison of optimum and un-optimized parameters (Fig. 10), Specimen printed with optimized parameters shows more delamination on the fractured surface, indicating strong interfacial bonding (Fig. 10a1–a3). In the case of specimen printed with un-optimized parameters, the smooth fracture surface from the Fig. 10b2, b3 reveals the poor interlayer bonding and also deformed layer thickness due to under extrusion was noted in the Fig. 10b1 which was due to the higher printing speed of 70 mm/s. From the flexural strength analysis results, it was observed that increasing the layer thickness reduces the flexural strength of the specimens. Because increased layer thickness minimizes the contact area between neighboring layers, resulting in low bonding strength and, as a result, poor resistance to bending effect and flexural strength. The evaluation found that increasing the printing speed and temperature decreases the flexural strength of the specimens. Because higher printing speed causes porosity and fracture formation, resulting in poor bending strength48. Similarly, high printing temperature affects the structural stability of the filaments by overheating the filaments, whereas lower printing temperature does not create sufficient wettability between each layer. As a result, the optimized input parameters overcame the limitations.
By submitting a comment you agree to abide by our Terms and Community Guidelines. If you find something abusive or that does not comply with our terms or guidelines please flag it as inappropriate.
“KyronMAX compounds can significantly change the way engineers approach part design, manufacturing, and assembly,” said Wilkinson. “The combination of KyronMAX’s performance with MCAM’s proprietary high-pressure molding technology is now able to produce the highest strength structural components made from injection molded thermoplastics.”
Fernandes, J., Deus, A. M. & Reis, L. et al. Study of the influence of 3D printing parameters on the mechanical properties of PLA. Proc. Int. Conf. Prog. Addit. Manuf. 547–552. https://doi.org/10.25341/D4988C (2018).
When it was introduced in 2014, the KryonMAX family of high-strength injection moldable thermoplastic compounds was designed to bridge the gap between traditional thermoplastics and carbon-fiber composites. “KyronMAX combines the best of both worlds by allowing engineers to injection mold high strength, carbon-fiber-reinforced thermoplastics in minutes with strengths that are comparable to metal,” said Dave Wilkinson, Technology Director for Mesa, AZ–based MCAM. “Combining specialized short carbon fiber and proprietary sizing technology produces molded parts that have significantly higher mechanical performance than was previously possible using long-fiber technology (LFT).”
Comparison of fracture mechanism of tensile specimens (a1–a3) optimum parameters (Layer thickness = 0.1 mm, Printing speed = 58 mm/s, Printing temperature = 199 °C), (b1–b3) un-optimum parameters (Layer thickness = 0.2 mm, Printing speed = 70 mm/s, Printing temperature = 195 °C).
Dou, H. et al. Effect of process parameters on tensile mechanical properties of 3D printing continuous carbon fiber-reinforced PLA composites. Materials 13, 3850 (2020).
A Drona C300 3D printer was employed to print the required specimens, as shown in Fig. 1. Even though, it was a well-known machine, this schematic representation helps the budding researcher to understand more about the extrusion mechanism. In the extruder setup, the PLA wire filaments are inserted. The melted PLA filament was extruded from the nozzle and started printing on the preheated bed. 60 °C bed temperature must be maintained in order to stick the specimen in the bed and also helps to start to print in the exact place of the starting point.
The mechanical testing was done on the printed specimens based on the ASTM standard. The dimensions of the ASTM standard specimens were shown in the Fig. 2. The Universal Tensile Machine (ATEDigiServoUtm2000) was used to test the ultimate tensile strength of the 3D printed materials. The ASTM D638 Standards were used to create the tensile test specimen (Fig. 2). The flexural strength of the printed specimen was determined using a flexural testing instrument (Eqvimech) based on a 5% deflection of the printed specimen. The ASTM D790 standards were used to create the flexural strength specimen (Fig. 3). Pendulum-type Izod impact apparatus (TFIT-300 N & EN) was used for the evaluation of the impact strength of the printed specimen. ASTM D256 standards were used to create the flexural specimens. The fractured specimens from the mechanical testing were further examined for the fracture studies with the help of Scanning Electron Microscope (Genesis/Veritas Series) analysis and the mode of failure was compared and investigated between the parameters.
Sprint technology uses additive manufacturing to produce a mold that is injected with the KryonMAX compound in the same manner as a metal tool. These rapid, cost-effective prototypes allow for rapid design iterations while testing under operating conditions.
The analysis of variance helps in determining the significance of input variables on the response and characterizes the influences of inter- and intra-parametric settings. Analysis of variance (ANOVA) was used to establish the relationship between the input factors and output responses using quadratic terms (linear, square, and two-way interaction), as shown in Table 3. Further, it provides an adjusted sum of squares, probability 'p' values, R-square and adjusted R-Square values37. These values indicate the input factor's significance and contribution to the output responses. The adjusted sum of squares values estimated the percentage contribution of inputs factors and R-squares values. It is noted that the 'p' values less than 0.05 with R square value of 98.1% and 99.7% confidence level of significantly influence the flexural strength and ultimate tensile strength.
Samykano, M. Mechanical property and prediction model for FDM-3D printed polylactic acid (PLA). Arab. J. Sci. Eng. 46, 7875–7892. https://doi.org/10.1007/s13369-021-05617-4 (2021).
Metal replacement has become a strategic element in most major OEM strategies for lightweighting and sustainability. KyronMAX technology has raised the bar for performance of injection moldable plastics and provides customers the opportunity to replace metal parts with plastic, said MCAM. KyronMAX parts that replace metal components on vehicles contribute to lower overall weight, which translates into a reduction of fuel consumption and CO2 emissions. Part cost can also be significantly reduced through the consolidation of several metal components into a single thermoplastic part by eliminating secondary operations during assembly.
Hanon, M. M., Marczis, R. & Zsidai, L. Influence of the 3D printing process settings on tensile strength of PLA and HT-PLA. Period Polytech. Mech. Eng. 65, 38–46. https://doi.org/10.3311/PPme.13683 (2021).
PLA is a thermoplastic polyester made from natural and renewable resources such as corn, cassava, and sugarcane35. A premium grade PLA (polylactic acid) filament was purchased from Tesseract, Mumbai, Maharashtra, India and it was used to print the specimens with different layer thicknesses, printing speeds, and temperatures.
Liao, Y. et al. Effect of porosity and crystallinity on 3D printed PLA properties. Polymers 11, 1–14. https://doi.org/10.3390/polym11091487 (2019).
Zhu, Y. et al. Study on effects of FDM 3D printing parameters on mechanical properties of polylactic acid. IOP Conf. Ser. Mater. Sci. Eng. 688(3), 033026. https://doi.org/10.1088/1757-899X/688/3/033026 (2019).
The literature survey showed that the input printing parameters influenced the mechanical behavior of the 3D-printed parts. Multi-criteria decision-making approach help to improve the manufacturing process to obtained unique solution in manufacturing industries. Conversely these approaches are rarely reported for 3D printing process. Effective utilization of these approaches is believed to be better solution in solving decision making problem in materials printing. Therefore, this research is going to focus on determination of effective control over the process that ultimately improving the mechanical attributes. In addition, predictive models are presented to characterize the influence of process parameters on the response indicators. A comprehensive study on the mechanical attributes of the material extrusion processed parts is required where the instant predictive model validated through experiments provides aid in manufacturing planning. In this regard, this research aims to optimize the important 3D printing process parameters to improve mechanical performance. In most of the literature, they have chosen a wide range of printing process parameters which was difficult to find an exact optimal parameter setting for the improved mechanical performance of PLA parts. So, the input parameters were chosen in a close range which attributed to the attainment of precise optimal parameter setting with enhanced interlayer bonding of PLA parts. Especially the layer thickness settings have a huge impact on attaining effective interlayer bonding. Hence, the close range of input parameter settings such as layer thickness (0.1, 0.15, and 0.2 mm), printing temperature (195, 200, and 205 °C), printing speed (50, 60, and 70 mm/s) with 100 percent infill density and bed temperature of 70 °C were used in this study to create the PLA parts. Mechanical testing such as tensile, and flexural was performed for all the combinations. SEM analysis was also used to analyze the fractured surface of the printed PLA specimens. These fractures displays the effective and poor interlayer bonding of parts. Further, the Taguchi with Criteria Importance through Intercriteria Correlation (CRITIC) embedded Weighted Aggregated Sum Product Assessment (WASPAS) based multi-criteria decision-making approach is carried out to assess the percentage contribution of MEX input factors on the printed PLA's flexural strength and ultimate tensile strength. Additionally, the mathematical model predicts the values of output responses such as flexural strength and ultimate tensile strength under the optimum layer thickness, printing speed, and printing temperature with minimum base runs.
Luzanin, O. et al. Impact of processing parameters on tensile strength, in-process crystallinity and mesostructure in FDM-fabricated PLA specimens. Rapid Prototyp. J. 25, 1398–1410. https://doi.org/10.1108/RPJ-12-2018-0316 (2019).
Layer thickness represents the deposition of melted PLA material as a layer with a certain height on the build platform and it was one of the important parameters which enhances the bonding strength of the printed PLA specimens. The printing time and strength of the printed part were influenced by layer thickness. Similarly, improper printing temperature leads to inconsistent and over extrusion with reference to ISO/ASTM 52,900 standard. The printing speed denotes the nozzle velocity in the X/Y directions. So, the un-optimized printing speed may also lead to the gaps in top layers, layer separation and splitting. So, it was highly essential to optimize these parameters to have enhanced mechanical properties with good structural integrity. The experiments consist of three factor and three level, L27 orthogonal array was designed using the Minitab V16 statistical software. The printing was performed one time for each trial such as flexural strength and ultimate tensile strength were used for analysis, as shown in the Table 3.
Contour plot for flexural strength (a) printing speed and layer thickness, (b) printing temperature and layer thickness, and (c) printing temperature and printing speed.
Farooq, M. U. et al. Surface generation on titanium alloy through powder-mixed electric discharge machining with the focus on bioimplant applications. Int. J. Adv. Manuf. Technol. 122, 1395–1411. https://doi.org/10.1007/s00170-022-09927-1 (2022).
The 2D contour plot, as shown in Fig. 5a–c respectively represent the effect of input factors such as layer thickness, printing speed and printing temperature on the flexural strength and ultimate tensile strength, respectively. Flexural strength is the ability of the 3D printed PLA polymer to withstand bending stress which ensures the adhesion of the printed layers42. It is an intensive property that can be influenced by process input factors, not by the dimension of the specimen.
Until she retired in September 2021, Clare Goldsberry reported on the plastics industry for more than 30 years. In addition to the 10,000+ articles she has written, by her own estimation, she is the author of several books, including The Business of Injection Molding: How to succeed as a custom molder and Purchasing Injection Molds: A buyers guide. Goldsberry is a member of the Plastics Pioneers Association. She reflected on her long career in "Time to Say Good-Bye."
Sun, Q., Rizvi, G. M., Bellehumeur, C. T. & Gu, P. Effect of processing conditions on the bonding quality of FDM polymer filaments. Rapid Prototyp. J. 14, 72–80. https://doi.org/10.1108/13552540810862028 (2008).
Kumar, M.S., Farooq, M.U., Ross, N.S. et al. Achieving effective interlayer bonding of PLA parts during the material extrusion process with enhanced mechanical properties. Sci Rep 13, 6800 (2023). https://doi.org/10.1038/s41598-023-33510-7
Schematic representation of Layer thickness, zig-zag infill pattern, 100% infill density and slicing software images of the tensile, impact and flexural specimens with printed PLA parts.
Figure 11 depicts the mechanism of interfacial bonding between the layers. This densely packed structure avoids pores and confined spaces between the layers. Moreover, the closely packed interlayers resulting from the smaller layer thickness substantially impeded crack growth. This mechanism was shown in the schematic representation in Fig. 12. Each printed layer inhibits the propagation of cracks. As a result, parts built with the maximum number of layers and the minimum thickness significantly resist crack propagation. Whenever a specimen was printed with a relatively high layer thickness, voids with poor interlayer bonding appear (Fig. 8b1, b2), and that region acts as the stress concentrated zone when the load is applied.
Naveed, N. Investigating the material properties and microstructural changes of fused filament fabricated PLA and tough-PLA parts. Polymers 13, 1487. https://doi.org/10.3390/polym13091487 (2021).
From the Table 4, it can be observed P value is less than 0.05 that implies each and individual parameter has significant influence over tensile and flexural strength. Contribution of control factors are calculated based on sequential sum of square, as illustrated in Table3. Layer thickness has major contribution in governing the mechanical properties of printed materials with 90.8 and 92.8%. Printing speed has second major contribution of 5.3 and 4.4% for tensile and flexural strength. Printing temperature has least contribution of 2.2 and 2.5% respectively.
Comparison of fracture mechanism of tensile specimens (a1–a3) optimum parameters (Layer thickness = 0.1 mm, Printing speed = 58 mm/s, Printing temperature = 199 °C), (b1–b3) non-optimum parameters (Layer thickness = 0.2 mm, Printing speed = 70 mm/s, Printing temperature = 195 °C).
Similarly, Zig-Zag pattern with 100% infill density was adapted to the print the specimens which was chosen based on the literature15. Layer-by-layer printing with reference to ISO/ASTM 52,900 standard was done according to the slicing instructions which was shown in the Fig. 2. All test specimens were printed with various layer thicknesses, printing speeds, and temperatures.
Increased printing speed and temperature decreased the flexural strength of the specimens which was due to the lack of sufficient time for the bonding of interlayers and also evident that the higher printing speed causes porosity and fracture formation, resulting in poor bending strength.
Zhang, X., Chen, L., Mulholland, T. & Osswald, T. A. Characterization of mechanical properties and fracture mode of PLA and copper/PLA composite part manufactured by fused deposition modeling. SN Appl. Sci. 1, 616. https://doi.org/10.1007/s42452-019-0639-5 (2019).
In recent years, additive manufacturing technology has been used to manufacture a variety of aeronautical and healthcare applications1. Various additive manufacturing procedures exist as referred by the ISO/ASTM 52,900:2015 standard, with material extrusion process (MEX) being one of the most extensively utilized owing to its flexibility, minimal wastage of materials, and ability to print different geometry with structural support2,3. Poly-Lactic Acid (PLA), Nylon, Acrylonitrile Butadiene Styrene (ABS), and Polyethylene Terephthalate Glycol (PETG) were the filament materials used in MEX-process. Since it is a biodegradable polymer ideal for tissue/bone engineering disciplines, thermoplastic PLA is a regularly used 3D printing material4. The performance of the printed parts was affected by some common defects such as overheating, layer shifting, under and over extrusion, gaps in top layer, curing and rough corners5. Hence, the effort to overcome the defects accelerated over the past few years. However, to maintain the consistency of the properties of the MEX parts, the printing parameters needed to be optimized to enhance the mechanical properties of the printed parts. Some research was conducted to analyze the physical behavior of 3D printed objects to expand the engineering use of 3D printing technology. Liu H et al. found that the composite filament printed in the parallel direction has significantly better tensile performance than the composite filament printed in the vertical direction6. The support structure was one of the most significant constraints in constructing 3D printed parts and also best print support structure dependent on the orientation.
KyronMAX can be compounded into any polymer. If an application requires the cost and property balance of nylon 6/6, for example, MCAM can formulate a nylon 6/6 KyronMAX compound that is stronger than anything currently available on the market. This technology ultimately offers customers the flexibility of selecting any polymer they want and combining it with KyronMAX fiber to create the strongest moldable compound in that category.
MCAM continues to innovate in materials science, and it now offers materials with tensile strengths that exceed 60,000 psi (414 MPa), as shown in the video. In addition to improved processability, KyronMAX compounds exhibit mechanical properties that surpass conventional glass- and carbon-fiber-filled thermoplastic systems at similar fiber loadings. This allows for a reduction in filler loading, thereby increasing material strain and allowing the molded part to yield rather than fracture. These compounds are now being used to replace aluminum and steel in structural applications.
Kechagias, J. & Chaidas, D. Fused filament fabrication parameter adjustments for sustainable 3D printing. Mater. Manuf. Process https://doi.org/10.1080/10426914.2023.2176872 (2023).
Herein the values of λ varies from 0 to 1, in this research value of λ is consider as 0.5. The accuracy of λ values can be determined by sensitivity analysis.
Cicala, G. et al. Polylactide (PLA) filaments a biobased solution for additive manufacturing: correlating rheology and thermomechanical properties with printing quality. Materials 11, 1191. https://doi.org/10.3390/ma11071191 (2018).
Khan, S. A. et al. CFD simulation and optimization of natural convection in a vertical annulus with nanofluids. Int. J. Therm. Sci. 185, 108079. https://doi.org/10.1016/j.ijthermalsci.2022.108079 (2023).
Sood, A. K., Ohdar, R. K. & Mahapatra, S. S. Parametric appraisal of mechanical property of fused deposition modelling processed parts. Mater. Des. 31, 287–295. https://doi.org/10.1016/j.matdes.2009.06.016 (2010).
Yeoh, C. K. et al. Effect of infill pattern on mechanical properties of 3D printed PLA and cPLA. IOP Conf. Ser. Mater. Sci. Eng. 957, 012064. https://doi.org/10.1088/1757-899X/957/1/012064 (2020).
Shaik, Y. P., Schuster, J., Katherapalli, H. R. & Shaik, A. 3D printing under high ambient pressures and improvement of mechanical properties of printed parts. J. Compos. Sci. 6, 16. https://doi.org/10.3390/jcs6010016 (2022).
Coppola, B. et al. 3D printing of PLA/clay nanocomposites: influence of printing temperature on printed samples properties. Materials 11, 1–17. https://doi.org/10.3390/ma11101947 (2018).
Liu, Z. et al. A critical review of fused deposition modeling 3D printing technology in manufacturing polylactic acid parts. Int. J. Adv. Manuf. Technol. 102, 2877–2889. https://doi.org/10.1007/s00170-019-03332-x (2019).
Step 1: The output responses are arranged in a form of decision matrix followed by the segregation of beneficial and non-beneficial. In general, the larger, better standards are termed as beneficial criteria. In this research, tensile and flexural strength of the printed components are considered as output response. Higher tensile and flexural strength are needed for the developed components hence it is segregated under beneficial criteria and the normalized decision matrix can be obtain by using Eq. (7) as illustrated in Table 7.
Kechagias, J. et al. Direct 3D printing of a hand splint using reverse engineering. IOP Conf. Ser. Mater. Sci. Eng. 1037, 012019. https://doi.org/10.1088/1757-899X/1037/1/012019 (2021).
Wickramasinghe, S., Do, T. & Tran, P. FDM-Based 3D printing of polymer and associated composite: a review on mechanical properties, defects and treatments. Polymers 12, 1–42. https://doi.org/10.3390/polym12071529 (2020).
The fractured surface of the printed flexural specimen was examined under optimal process parameters, as illustrated in Fig. 9a and b. The SEM analysis of the fractured surface of the flexural specimen revealed a smooth and ridged surface with no pore formation. Similarly, there was a delamination and absence of micro-cracks, which contributed to the delayed flexural failure. These cracked surfaces demonstrate that the printing speed of 58 mm/s, a layer thickness of 0.1 mm, and printing temperature of 199 °C substantially enhanced flexural strength.
Menekse, A., Ertemel, A. V., Akdag, H. C. & Gorener, A. Additive manufacturing process selection for automotive industry using Pythagorean fuzzy CRITIC EDAS. PLoS One 18, e0282676. https://doi.org/10.1371/journal.pone.0282676 (2023).
The contour plot of flexural strength was obtained based on input factors' hold values, such as layer thickness of 0.10 mm, printing speed of 60 mm/s, and printing temperature of 200 °C. Figure 5a represents maximum flexural strength greater than 75 MPa at minimum layer thickness (0.1 mm) for printing speeds ranging from 50 to 65 mm/s. Similarly, Fig. 5b shows maximum flexural strength (> 75 MPa) at minimum layer thickness (0.10 mm) for all printing temperatures (195–205 °C). However, the moderate flexural strength around 60–65 MPa was obtained at a maximum printing speed of 70 mm/s with a minimum printing temperature of 195 °C and vice-versa (50 mm/s of printing speed and 205 °C of printing temperature), as shown in Fig. 5c.
Based on ranking it can be depicted lower layer thickness with medium printing speed and medium printing speed delivers optimal mechanical properties.
Figure 7a and b show a scanning electron microscopy (SEM) image of the fractured surface of the PLA tensile specimen under MEX-optimized conditions. The MEX process parameters had a significant effect on the tensile properties of the fabricated parts. The layer thickness exhibits a linear correlation with the specimen's tensile strength. It was revealed that increasing the layer thickness reduces the tensile strength of the specimen. The bonding strength was increased by fusing multiple layers with reduced thickness, and fused layers of small thickness achieved the closely packed interlayers. Fibrous filaments with more delamination were seen on the broken surface which signifies the higher bonding strength and also these was an absence of voids and porosity, these mechanisms were observed in Fig. 8a2. Zhang et al. suggested that the ridged fractured surface represents the effective layer deposition had occurred46. The clear circular shaped extrusion without any defects was observed in the Fig. 8a3 which was due to the optimum printing speed of 58 mm/s. However, some microcracks were observed in the fractured surface and that depicts the stress concentrated regions (Fig. 9a1). On comparison of optimum (Layer thickness = 0.1 mm, Printing speed = 58 mm/s, Printing temperature = 199 °C) and un-optimized parameters (Layer thickness = 0.2 mm, Printing speed = 70 mm/s, Printing temperature = 195 °C) which was shown in Fig. 8, The voids and poor interlayer bonding was evident on the fractured surface of the Specimen printed with un-optimized parameters which was shown in the Fig. 8b1, b2. Similarly, under extrusion was also observed in the un-optimized print setting. The under extrusion was shown in the Fig. 8b3. These defects had a considerable effect on the strength of the printed material, resulting in inferior specimens47. The excision of these defects enhances the mechanical properties of the specimens. This reveals that 0.1 mm layer thickness with 58 mm/s printing speed at 199 °C printing temperature yields smooth layers with good bonding. The fibrous filaments from the fractured surface depict the ductility of the PLA. Inter-layer cracks were visible on the broken surface, revealing the strong bonding layers. Furthermore, this fracture analysis also substantiates the Taguchi—CRITIC embedded WASPAS approach based optimum conditions.
The additive manufacturing technique of material extrusion has challenge of excessive process defects and not achieving the desired mechanical properties. The industry is trying to develop certification to better control variations in mechanical attributes. The current study is a progress towards understanding the evolution of processing defects and the correlation of mechanical behavior with the process parameters. Modeling of the 3D printing process parameters such as layer thickness, printing speed, and printing temperature is carried out through L27 orthogonal array using Taguchi approach. In addition, CRITIC embedded WASPAS is adopted to optimize the parts' mechanical attributes and overcome the defects. Flexural and tensile poly-lactic acid specimens are printed according to ASTM standards D790 and D638, respectively, and thoroughly analyzed based on the surface morphological analysis to characterize defects. The parametric significance analysis is carried out to explore process science where the layer thickness, print speed, and temperature significantly control the quality and strength of the parts. Mathematical optimization results based on composite desirability show that layer thickness of 0.1 mm, printing speed of 60 mm/s, and printing temperature of 200 °C produce significantly desirable results. The validation experiments yielded the maximum flexural strength of 78.52 MPa, the maximum ultimate tensile strength of 45.52 MPa, and maximum impact strength of 6.21 kJ/m2. It is established that multiple fused layers restricted the propagation of cracks with minimum thickness due to enhanced diffusion between the layers.
Liu, H. et al. Three-dimensional printing of poly(lactic acid) bio-based composites with sugarcane bagasse fiber: effect of printing orientation on tensile performance. Polym. Adv. Technol. 30, 910–922. https://doi.org/10.1002/pat.4524 (2019).
Rismalia, M. et al. Infill pattern and density effects on the tensile properties of 3D printed PLA material. J. Phys. Conf. Ser. 1402, 2–8. https://doi.org/10.1088/1742-6596/1402/4/044041 (2019).
The calculated OWJ value from Eq. (6) is used in weightage calculation in WASPAS approach. Herein the correlation coefficient and weightages are depicted in Table 6.
The model which corresponds to the experimental data in the case of flexural strength show R2 = 92.2% and for ultimate tensile strength around R2 = 94.2%. The high R2 value shows the closeness of the predicted results with the model which attributes the supremacy of the empirical model of the process in selected range.
Contour plot for ultimate tensile strength (a) printing speed and layer thickness, (b) printing temperature and layer thickness, and (c) printing temperature and printing speed.
Multi-objective optimization was used to reduce the quantity of materials needed for the structural support, lowering material costs, and increasing work efficiency7. The reuse of 3D printed items also contributes significantly to decreasing environmental issues. Even though regular PLA has good characteristics, recycled PLA has a lower viscosity, higher crystallinity, and less transparency8. The researchers found that the tensile qualities of 3D printed PLA material increase with increasing infill density and that concrete patterns had better tensile properties than grid and tri hexagon patterns9. The rise in tensile strength and young's modulus was attributed to an increase in infill density in numerous studies, and the anisotropy to the tension of 3D printed materials was demonstrated by shear tests, shear modulus, and shear rate10. Thermal stability analysis was used to assess the impact of printing temperature on 3D printed PLA material, and several experiments were carried out by adding clay nanoparticles to the PLA material to boost thermal stability11. A few researchers looked into the impact of infill density on the heat-resistant carbon fiber reinforced PETG material and found that a 60 percent infill density combined with annealing effects resulted in good wear resistance12. The influence of layer thickness was also documented in certain studies, in which the printing layer thickness was found to impact surface roughness and print orientation significantly. According to the findings, edge-oriented 3D printed PLA components with lower layer thickness and flat-oriented 3D printed PLA parts with higher layer thickness have better bonding strength13. Abdalla A et al. revealed that the vertically oriented materials have excellent resistivity and electron transport kinetics14. The infill pattern influenced the tensile characteristics of the manufactured 3D printed PLA materials. For 3D printing, various infill patterns such as grid, zig-zag, and concrete patterns were used, with zig-zag machining demonstrating improved tensile performance15. The effects of modifying the orientation and infill density on the tensile characteristics of 3D printed PLA and HT-PLA materials were studied. The HT-PLA with X orientation and 100 percent infill density substantially impact the tensile performance16. A comprehensive list of studies which incorporate a range of process parameters and their effects are tabulated in Table 1.
From the analysis of variance, it has been observed that P values are less than 0.05 for all the process parameter. Hence each and individual parameter has significance over output response and layer thickness play vital role in governing the material strength.
Beltrán, F. R. et al. Evaluation of the technical viability of distributed mechanical recycling of PLA 3D printing wastes. Polymers 13, 1247. https://doi.org/10.3390/polym13081247 (2021).
Step 2: It includes calculation of two total relative important variable namely weighted summed model (Qs) and weighted product model Qp. Herrin the weightage calculated in CRITIC approach viz. OWj is used for determining the Qs and Qp values are depicted in Eqs. (8) and (9).
Mishra, P. K., Senthil, P., Adarsh, S. & Anoop, M. S. An investigation to study the combined effect of different infill pattern and infill density on the impact strength of 3D printed polylactic acid parts. Compos. Commun. 24, 100605 (2021).
Wang, K. et al. Effects of infill characteristics and strain rate on the deformation and failure properties of additively manufactured polyamide-based composite structures. Results Phys. 18, 103346. https://doi.org/10.1016/j.rinp.2020.103346 (2020).
Rodríguez-Panes, A., Claver, J. & Camacho, A. M. The influence of manufacturing parameters on the mechanical behaviour of PLA and ABS pieces manufactured by FDM: a comparative analysis. Materials 11, 1333. https://doi.org/10.3390/ma11081333 (2018).
The balanced control over the air-gap reduction and improvement in the stiffness which is directly linked with print temperature and speed, and layer thickness enhances the tensile strength. Rajpurohit and Dave44 resulted in improved tensile strength through combined control over layer thickness and speed. This control provides maximum area for bonding and the number of printed layers (such as 60 mm/s) enhances the overall stiffness23. Similarly, Zandi et al.45 resulted in significant influence of print speed on the tensile strength because the process parameter significantly controls the increment in printed layers and their number. Moreover, the printing temperature and speed combinedly reduces airgap at optimized process parameters using 0.150 mm layer thickness. The ultimate tensile strength was reduced from 45 to 35 MPa as printing speed (70 mm/s), and printing temperature (205 °C) increased to their corresponding maximum limits (Fig. 6c).
The computed values of output response are used as weightage values in WASPAS method. The steps involved in WASPAS are illustrated as follows.
Kovan, V., Altan, G. & Topal, E. S. Effect of layer thickness and print orientation on strength of 3D printed and adhesively bonded single lap joints. J. Mech. Sci. Technol. 31, 2197–2201. https://doi.org/10.1007/s12206-017-0415-7 (2017).
Zandi, M. D. et al. Study of the manufacturing process effects of fused filament fabrication and injection molding on tensile properties of composite PLA-wood parts. Int. J. Adv. Manuf. Technol. 108, 1725–1735. https://doi.org/10.1007/s00170-020-05522-4 (2020).
Farooq, M. U. & Anwar, S. Investigations on the surface integrity of Ti6Al4V under modified dielectric(s)-based electric discharge machining using cryogenically treated electrodes. Processes 11, 877. https://doi.org/10.3390/pr11030877 (2023).
In January of this year, Mitsubishi Chemical Advanced Materials (MCAM) expanded its KyronMAX product line beyond performance-grade polymers, such as PEEK and PEI, by adding engineering polymers, including polycarbonate, nylon, polyphthalamide (PPA), and even polypropylene. These new compounds unlock a wider range of applications in the automotive and mobility, recreational, electronics, and medical industries.
The regression equations were derived for two output responses (Flexural strength and Ultimate tensile strength) and the three input factors (Layer thickness (LT); Printing speed (SP); and Printing temperature (TP)). The prediction of flexural strength and ultimate tensile strength using the regression Eqs. (1) and (2) expressed as a quadratic form to depict the non-linear relationship of input factors. The empirical model helps in predicting the output responses through input factors38. Moreover, the model competence was ensured by the R-square and adjusted R-square values39. Here, both values are greater than 92% in both output responses.
M.S.K., M.U.F., N.S.R., C.-H.Y., V.K. and A.A. A. wrote the main manuscript text and M S.K., M.U.F., N.S.R., C.-H.Y., V.K. and A.A. A. prepared figures. All authors reviewed the manuscript. All authors agreed upon the current version of submission for publication.
Rashia Begum, S. et al. Revealing the compressive and flow properties of novel bone scaffold structure manufactured by selective laser sintering technique. Proc. Inst. Mech. Eng. [H] 236, 526–538 (2022).
Chaidas, D. & Kechagias, J. D. An investigation of PLA/W parts quality fabricated by FFF. Mater. Manuf. Process. 37, 582–590. https://doi.org/10.1080/10426914.2021.1944193 (2022).
Asif, N., Saleem, M. Q. & Farooq, M. U. Performance evaluation of surfactant mixed dielectric and process optimization for electrical discharge machining of titanium alloy Ti6Al4V. CIRP J. Manuf. Sci. Technol. 43, 42–56. https://doi.org/10.1016/j.cirpj.2023.02.007 (2023).
Rajpurohit, S. R. & Dave, H. K. Analysis of tensile strength of a fused filament fabricated PLA part using an open-source 3D printer. Int. J. Adv. Manuf. Technol. 101, 1525–1536. https://doi.org/10.1007/s00170-018-3047-x (2019).
Through impact analysis, it was recognized that multiple fused layers by 0.1 mm layer thickness restrict the propagation of cracks. In which each layer with minimum layer thickness act as an obstacle to the propagation of cracks. Similarly, the printing speed of 58 mm/s minimizes defects such as voids and porosity by building strong interfacial adhesion between the layers and enabling sufficient fusion time.
The flexural strength and ultimate tensile strength of MEX processed PLA was investigated using Taguchi—CRITIC embedded WASPAS approach. The Taguchi method was adopted for experimental planning and to understand the effect of process parameter over mechanical properties of printed PLA parts. CRITIC embedded WASPAS method was used to attain optimal unique solution of parameter to achieve optimal mechanical strength viz. flexural and tensile strength. The results are summarized as follows.
Butt, J., Bhaskar, R. & Mohaghegh, V. Analysing the effects of layer heights and line widths on FFF-printed thermoplastics. Int. J. Adv. Manuf. Technol. 121, 7383–7411. https://doi.org/10.1007/s00170-022-09810-z (2022).
Kechagias, J. D. & Vidakis, N. Parametric optimization of material extrusion 3D printing process: an assessment of Box-Behnken versus full-factorial experimental approach. Int. J. Adv. Manuf. Technol. 121, 3163–3172. https://doi.org/10.1007/s00170-022-09532-2 (2022).
Gonabadi, H., Yadav, A. & Bull, S. J. The effect of processing parameters on the mechanical characteristics of PLA produced by a 3D FFF printer. Int. J. Adv. Manuf. Technol. 111, 695–709. https://doi.org/10.1007/s00170-020-06138-4 (2020).
Abdalla, A. et al. Augmentation of conductive pathways in carbon black/PLA 3D-printed electrodes achieved through varying printing parameters. Electrochim. Acta 354, 136618. https://doi.org/10.1016/j.electacta.2020.136618 (2020).
Open Access This article is licensed under a Creative Commons Attribution 4.0 International License, which permits use, sharing, adaptation, distribution and reproduction in any medium or format, as long as you give appropriate credit to the original author(s) and the source, provide a link to the Creative Commons licence, and indicate if changes were made. The images or other third party material in this article are included in the article's Creative Commons licence, unless indicated otherwise in a credit line to the material. If material is not included in the article's Creative Commons licence and your intended use is not permitted by statutory regulation or exceeds the permitted use, you will need to obtain permission directly from the copyright holder. To view a copy of this licence, visit http://creativecommons.org/licenses/by/4.0/.
Abbas, T., Othman, F. M. & Ali, H. B. Effect of infill parameter on compression property in FDM Process. Int. J. Eng. Res. Appl. 12, 25–34 (2017).
Kechagias, J. D., Zaoutsos, S. P., Chaidas, D. & Vidakis, N. Multi-parameter optimization of PLA/coconut wood compound for fused filament fabrication using robust design. Int. J. Adv. Manuf. Technol. 119, 4317–4328. https://doi.org/10.1007/s00170-022-08679-2 (2022).
A quarter-turn latch found in the galley of a commercial aircraft illustrates how even a small weight reduction can have a large impact. Typically made from machined aluminum, this latch is molded using KyronMAX S-6230, a carbon-fiber-reinforced PEI compound. Switching to the thermoplastic provided a 45% weight reduction while still meeting mechanical and flammability requirements. MCAM’s exclusive Sprint technology — a platform for rapid injection molding of functional parts — was used to rapidly prototype components prior to full production.
Step 3: Determination of generalized criteria Qc. The Qc values are calculated from Eq. (10) followed by ranking of obtained Qc value. The trail with highest Qc values is considered as the optimal parameter to attain components with higher mechanical strength. Table 8 shows the generalized criteria and optimal solution.
Hussin, M. S., Hamat, S. & Ali, S. A. S. et al. Experimental and finite element modeling of partial infill patterns for thermoplastic polymer extrusion 3D printed material using elasto-plastic method. In: AIP Conference Proceedings 020011 (AIP Publishing LLC, 2020).
Wang, L., Gramlich, W. M. & Gardner, D. J. Improving the impact strength of Poly(lactic acid) (PLA) in fused layer modeling (FLM). Polymer 114, 242–248. https://doi.org/10.1016/j.polymer.2017.03.011 (2017).
From the Taguchi—CRITIC embedded WASPAS approach, optimal printing parameters were identified as layer thickness of 0.1 mm with printing speed of 60 mm/s and 200 °C printing temperature which results in ultimate tensile strength of 45.22 MPa, flexural strength of 78.64 MPa and impact strength of 6.21 kJ/m2. These results were substantiated by displaying good interlayer bonding on the fractured surface under different loading conditions.
Thank you for visiting nature.com. You are using a browser version with limited support for CSS. To obtain the best experience, we recommend you use a more up to date browser (or turn off compatibility mode in Internet Explorer). In the meantime, to ensure continued support, we are displaying the site without styles and JavaScript.
Zaldivar, R. J. et al. Influence of processing and orientation print effects on the mechanical and thermal behavior of 3D-printed ULTEM® 9085 material. Addit. Manuf. 13, 71–80. https://doi.org/10.1016/j.addma.2016.11.007 (2017).
Silva, C. et al. Study on 3D printing of gyroid-based structures for superior structural behaviour. Prog. Addit. Manuf. 6, 689–703. https://doi.org/10.1007/s40964-021-00191-5 (2021).
Furthermore, the printing temperature and speed influence the tensile strength of the specimens. The high-speed printing (70 mm/s) was attributed to the extruded material's volume shrinking. High-speed printing inhibits the continuous flow of materials and causes discounters in layer thickness. It also contributes to the formation of porosity and poor interlayer bonding. These defects were shown in the Fig. 8b1–b3. This challenge was overcome by maintaining a constant printing speed of 58 mm/s and an appropriate printing temperature of 199 °C, allowing good fusion and solidification time for the extruded materials, thereby improving printing accuracy and contributing to the enhancement of the tensile strength.
Sachini Wickramasinghe et al. investigated the functional properties of the fiber reinforced composite fabricated through MEX and also examined their defects based on the infill density, print orientation and layer thickness. They have found that some common defects, such as void formation and surface roughness, were resolved by optimizing those process parameters12. Similarly, Yuhan Liao et al. analyzed the interrelationship between crystallinity and porosity, which influences the mechanical properties of the printed parts. Further, they found that the bed temperature and print orientation considerably affect the printed parts' microstructure28. Dawoud et al. examined the scaffolding angle and raster gap to enhance the mechanical properties of the printed parts. Further, the ABS filament was infused with graphite flakes to improve the tribological properties. They reported that a 90° scaffold angle with a negative gap has enhanced mechanical and tribological properties29. Gianluca Cicala et al. investigated printing the complex shape with high accuracy. Thermogravimetric analyses were performed on the printed parts to examine their rheology and carried out the tensile test to validate their experiments4. Patil et al.30 optimized material extrusion process parameters for roughness, printing time, and length of filament consumed. The layer thickness of 0.2 mm and printing speed of 100 mm/h were found to be the most optimal selection for achieving desired results. Luzanin et al.31 evaluated tensile strength (found optimized at 0.2 mm) and mesostructure in MEX-fabricated polylactic acid. It was found that layer thickness and its quadratic effect affected the tensile strength significantly. Hsueh et al.32 studied mechanical properties of 3D-Printed PLA against ASTM D638, ASTM D3410 and ASTM D790 standards. It was found that with the increase in print temperature or speed, the mechanical properties of the printed PLA material increased. Likewise, Rodríguez-Panes et al.33 evaluated tensile mechanical behavior of printed PLA and resulted that the increased layer height (0.1–0.2 mm) caused the tensile strength to reduce by 11%. On the other hand, Wang et al.34 compared injection molded PLA with 3D-printed PLA and resulted 114% higher performance of MEX-based PLA in Izod impact strength which certainly outperformed in quality matrix.
The datasets used and analyzed during the current study are available from the corresponding author on reasonable request.
In the full factorial design, a wide range of parametric settings are tested which significantly increase cost and time of the project. Therefore, different robust design of experiment approaches are used such as Taguchi or response surface methodology and Taguchi which offer higher confidence levels of experimental campaign, assist in modelling and directly reduce time and cost. Box-Behnken design (BBD) and Taguchi are one of the widely used fractional factorial experimental approaches which comes under response surface methodology. Kechagias and Vidakis established supremacy of BBD and compared its benefits with full factorial design during fused filament fabrication36. For this investigation, the experiments were designed using taguchi method with three different levels for three input factors: layer thickness, printing speed, and printing temperature (it indicates the extruder temperature), which was shown in Table 2. Also, two output parameters: Tensile strength and Flexural strength were considered to examine the influence of printing process parameters on the mechanical performance of the printed PLA specimens.
Patil, P., Singh, D., Raykar, S. J. & Bhamu, J. Multi-objective optimization of process parameters of fused deposition modeling (FDM) for printing polylactic acid (PLA) polymer components. Mater. Today Proc. 45, 4880–4885. https://doi.org/10.1016/j.matpr.2021.01.353 (2021).
The fitted line plot for both output responses (flexural strength and ultimate tensile strength) indicate the correlation between the predicted data from the regression equations and the actual data from the experimental runs, as shown in Fig. 4. It suggests that the actual values agree with the predicted values, which implies the adequacy and reliability of the regression model.
The ultimate tensile strength is the maximum load the PLA cross-section carries at the tensile condition43. There is a maximum ultimate tensile strength (> 45 MPa) with minimum layer thickness with moderate printing speed (55–60 mm/s) and printing temperature (197.5–200 °C), as shown in Fig. 6a and b, respectively. Mainly, the tensile strength is significantly affected by print speed and layer thickness. The fundamental reason behind the print speed is that the layer increment of PLA material unbalances the process which result in compromised mechanical attributes. The air-gap in the layers and the stiffness mainly drives the tensile strength in poly-lectic acid28.
GETTING A QUOTE WITH LK-MOULD IS FREE AND SIMPLE.
FIND MORE OF OUR SERVICES:
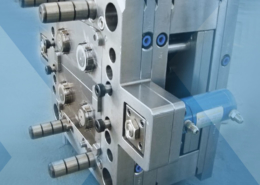
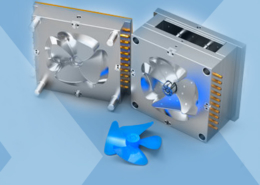
Plastic Molding

Rapid Prototyping
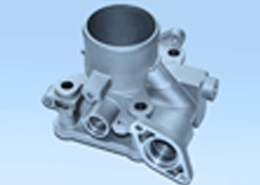
Pressure Die Casting
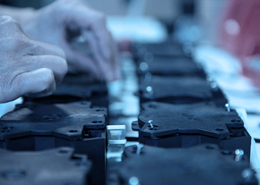
Parts Assembly
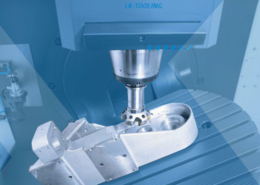