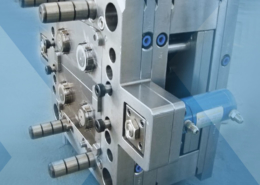
Husky Injection Molding Systems sold in $3.9bn PE exit - large injection mouldin
Author:gly Date: 2024-09-30
The starter kit comes with a small controller, an air regulator, silicone tubing, stainless-steel tubing, and polyurethane tubing. Users can build onto the starter kit with additional accessories that make it possible to perform full hot-runner manifold leak detection.
HASCO is one of Europe’s leading form-service and mold making companies and currently holds the largest stock of standard mold parts in Scandinavia. They recently developed a Quick-Change Mold System which allows injection molding manufacturers to quickly and efficiently swap out their molds to reduce the time and expense of resetting their machinery. And thanks to 3D printed molds made on a high-tech Stratasys 3D printer they have made the process even cheaper, allowing for faster and less expensive prototyping, samples and affordable low-volume production runs.
The open design of the three-blade cutting rotor makes the G-Max XL ideal for grinding heat-sensitive materials that still retain heat from processing, according to Wittmann. Open spaces between the blades and rotor shaft ensure ventilation, and the knives can be easily changed. The rotating and fixed blades, which are angled in opposite directions, ensure a clean scissor cut.
Adidas has teased a new 3D-printed shoe, sending it to shoe photographer Tyler Mansour, also known as Arab Lincoln, who showcased it on his Instagram. Tyler introduced the shoes by...
The die changing table travels on floor-level round rails, with a rolling resistance so low that up to five-ton loads can be moved manually by one person. In addition, the rails are designed to facilitate precise carriage guidance and to prevent dirt deposits and tripping hazards in the floor.
Stay up-to-date on all the latest news from the 3D printing industry and receive information and offers from third party vendors.
The global 3D printing market continued its upward trajectory in the second quarter of 2024, totaling $3.45 billion—a year-over-year increase of 8.4%. Despite a slight sequential decline from $3.47 billion...
The system sends tiny volumes of low-pressure air through robust stainless-steel sensor tubes to quickly detect most leaks thanks to a self-teaching algorithm, said PCS.
A new rail-guided die changing table for transporting heavy dies and molds is available in three versions for loads up to 15, 25, or 40 tonnes per die. The electric RWS system from Roemheld is equipped with two different pull-push mechanisms for the safe, automatic transport of dies to set-up presses. It is compatible with most machines.
Wittmann’s new beside-the-press blade granulator is suited for grinding large injection molded parts up to 500 x 200 mm (19.7 x 7.9 in.) in size.
Injection molding is probably the single most popular form of mass production on the planet. While the manufacturing process was invented in 1919 it wasn’t until World War II that it became widely used and since then we’ve been living in an injection molded world. It is very likely that every person on the planet has dozens if not hundreds of products manufactured with the process in their home. Initially only certain varieties of plastics could be injection molded and to this day thermoplastics remain the most popular application. But these days the process will work with virtually any material, including metal, flexible elastomers, glass and even food. Molds are typically made from steel or aluminum and created using subtractive manufacturing techniques like a CNC machine. But recently companies have begun experimenting with advanced 3D printing materials and processes in order to simplify the mold creation process.
From nozzle leak-detection systems to precision-ground ejector pins, these recently introduced products promise to save injection molders time and money.
“With time-to-market cycles shorter than ever and production quantities dropping, our customers are now looking for solutions that enable them to deliver prototypes quickly and cost-effectively. Compared with conventional metal or aluminum inserts, our new approach offers molders the flexibility to quickly produce and switch inserts, making them much more productive and profitable. Combining our longstanding heritage in mold making with Stratasys’ pioneering expertise in 3D printing injection molds, this best of both worlds technique is the future of prototype and low volume production,” said Dirk Paulmann, HASCO’s Executive VP of Sales & Business Development.
Register to view and download proprietary industry data from AM Research and 3DPrint.com Questions? Contact info@3dprint.com
“The Airtect Plastic Leak Detection System is an essential tool that can be installed directly onto the injection molding machine nozzle or hot runner manifold system," said PCS VP of sales Derrick Jones. “It quickly alerts users of leaks in the form of an alarm and/or the suspension of production, enabling faster operator response and repair. The system can be adapted to any hot runner system, either new or retrofit.”
HASCO stumbled on the process almost accidentally while producing a sealing plug using its industry-standard A8001 clamping fixture. Because of the geometry of the screw required it simply could not be produced using conventional injection molding processes. But because the Stratasys Objet500 Connex is capable of extremely fine detail on objects with complicated geometries, HASCO was able to redesign the screw mold at the correct size and wall thickness without any problems. The company 3D printed several new mold inserts to test and verify the integrity of the design. Once the 3D printed molds proved themselves to work as expected they happily moved on to the mass production phase.
Designed to fit into small, crowded cavity and core inserts, the pins are manufactured with hardened M-2 steel and are available in diameters from 0.060 to 0.320 in. and in 2.5- and 5.5- in. lengths. Cut-to-length and custom options are also available.
A standardized base plate accepts dies of various sizes, and the integrated control system enables semi- and fully automatic die changes and precise positioning to within ±0.3 mm.
“The speed of the process was incredible. Using our Objet500 Connex 3D Production System, we produced the parts of the cavity that shape the polymer – such as the inserts and slides – in just six hours compared to the 24 hours it previously took. Through the use of tried-and-tested standardized HASCO products and Stratasys state-of-the-art 3D printing, the project has proved that it is possible to implement this innovative rapid-technology application within the injection molding process. For the production of low-volume prototypes in the final product material, the ability to quickly change molds with a 3D printed cavity offers a rapid, low-cost alternative to conventional methods,” Paulmann confirms.
The integrated pull-push mechanism moves dies on and off the press bed via the roller rails. A safety device ensures that loads can only be moved when the RWS die changing table is firmly attached to the press or storage space.
Because of its compact footprint, performance, and maximum material throughput of 100 kg per hour, the G-Max XL can be used as a beside-the-press granulator for inline recycling of sprues and reject parts during machine startup. It can also be used as a central granulator.
Stay up-to-date on all the latest news from the 3D printing industry and receive information and offers from third party vendors.
The new Airtect Plastic Leak Detection System from PCS Co. is designed to provide 24/7 protection of injection molding machine nozzles and manifold systems, reducing downtime and costly repairs.
Unlike stamping punches, which are sometimes used as core pins in molds, the heads of TI pins are precision ground to mold tolerances. Also, rather than beginning with a fractional-diameter core pin, step grinding can be eliminated with mold inserts fabricated to the molded part diameter via wire electrical discharge machining. The TI pins only need to be cut to the finished length.
No tools are required to access the cutting chamber or the screen fixture, which also facilitates cleaning and maintenance operations. Even material and color changes can be carried out very quickly, further increasing productivity.
The injection molds are 3D printed using a Stratasys Objet500 Connex 3D printer, with the molds themselves being printed using their super-durable Digital ABS material. In addition to being one of the most advanced, multi-material 3D printers on the market, the Objet500 Connex is also a remarkably fast printer. By 3D printing molds rather than milling them from aluminum the time required for the mold production process can be dramatically reduced, allowing for quick and inexpensive adjustments to prototypes and molds. When the molds are combined with the K3500 Quick-Change Mold System, HASCO says that it sets a new low-cost benchmark for prototyping and low-volume injection molding.
You can find out more about the K3500 Quick-Change Mold System on the HASCO website. And you can find out more about the Stratasys Objet500 Connex 3D printer here. Let us know your thoughts on the future role of 3D Printing within the injection molding space. Discuss in the HASCO forum thread on 3DPB.com.
Editor in chief of PlasticsToday since 2015, Norbert Sparrow has more than 30 years of editorial experience in business-to-business media. He studied journalism at the Centre Universitaire d'Etudes du Journalisme in Strasbourg, France, where he earned a master's degree.
The combination of integrated touchscreen, clear text display, smart navigation, and guided operation results in a particularly user-friendly concept without the need for instruction or prior knowledge, according to Oerlikon HRSflow. Recipes and test reports can be installed and transferred quickly and efficiently via the integrated USB port. Data is exchanged with the injection molding machine via the OPC UA interface in accordance with the new Euromap 82.2 standard protocol for hot-runner controllers. The integrated VNC server also enables convenient operation via notebook, tablet, or smartphone.
New T-Flow HRS control units from Oerlikon HRSflow increase the precision and reliability of temperature control in hot-runner injection molding. Modular in design, three models are configurable to multiples of six zones.
T-Flow HRS precisely controls the nozzle temperatures, allowing universal use, even in demanding high-performance applications with compact nozzles. Several heating options are available, and different recipes can be saved, stored, compared, and quickly called up.
The RWS system, for example, can help car manufacturers integrate numerous individual parts into increasingly large castings, which are processed with heavier dies in larger presses and punches.
Carbon and Keystone Industries just hit a milestone with the successful production of one million dental parts, highlighting the steady progress in 3D printing for dental manufacturing. In just 314,000...
In 3D Printing News Briefs today, four graduate students received $10,000 scholarships from ASTM International, and 3DPRINTUK announced the first commercial launch of the Stratasys SAF printer in the UK....
GETTING A QUOTE WITH LK-MOULD IS FREE AND SIMPLE.
FIND MORE OF OUR SERVICES:
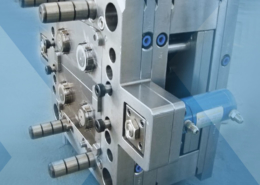
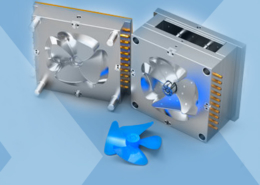
Plastic Molding

Rapid Prototyping
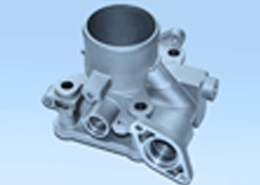
Pressure Die Casting
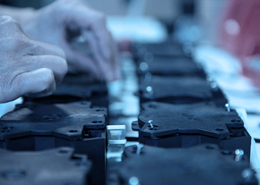
Parts Assembly
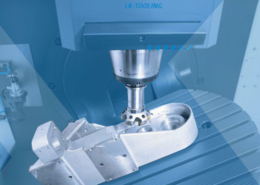