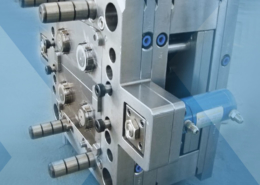
Husky Injection Molding builds medical business unit, one considered step
Author:gly Date: 2024-09-30
The range of dryers on display at the FIP will include a Drymax primus und a Drymax plus dry air dryer, as well as a Card primus compressed air dryer. The dry air dryers from the Drymax series are each equipped with two desiccant cartridges and therefore deliver a continuous flow of process air with consistent dry air quality for perfect drying of plastic granulate. The Drymax plus offers high operating comfort with a generously dimensioned touch display panel. Card compressed air dryers are small and effective and ideally suited for simple drying applications directly next to the machine’s feed zone.
By harnessing the reams of data produced in modern plastics processing facilities, artificial intelligence can improve machine performance.
Moreover, WITTMANN BATTENFELD France will also demonstrate its expertise in micro injection moulding by showing a MicroPower 15/10 specially designed for this type of application live in action. With this machine a micro retaining ring for medical miniature tubes will be produced from PC with an 8-cavity mould supplied by Wittner, Austria. This product has a part weight of only 2 mg. The machine comes with a rotary unit, an integrated WITTMANN W8VS2 robot and a camera for complete parts inspection. Following removal and camera inspection, the parts are transferred to transport containers, separated according to individual cavities.
As AI and machine learning are further leveraged to improve injection molding operations, simply gathering data is not enough to optimize processes, Faulhaber cautioned. “You also need the process expertise and domain knowledge. In the future, the evaluation of many data directly in the control unit will offer further added value.”
Multi-component technology expertise will be shown as well, by the production of a bottle opener made of PC and TPE on a SmartPower B8X Combimould, using a mould supplied by FKT Formenbau und Kunststofftechnik, Germany. The SmartPower B8X 120/350H/130S is presented as an insider solution with a W918 robot from WITTMANN and a conveyor belt integrated in the production cell. The robot takes the prepared metal parts from a magazine and places them into the mould, where they are insert-moulded with polycarbonate. A rotary unit subsequently turns the resulting base bodies into position and passes them on to the second station, where they are over-moulded with TPE to provide them with a better grip. The finished parts are then deposited on the insider cell’s conveyor belt.
The Industry 4.0 era of manufacturing depends so heavily on data-driven precision that artificial intelligence (AI) is playing an increasing role in harnessing that data to enhance the performance of machines — including injection molders.
With its presentation of an EcoPower 180/750+ B8X DC machine, WITTMANN BATTENFELD France will demonstrate to its visitors the WITTMANN Group’s expertise in the field of utilising renewable energies. This machine, operating with a solar power storage unit, is also equipped with a WX142 robot in DC version.
Wittmann Battenfeld, which has fully embraced Industry 4.0 connectivity across its portfolio of injection molding and auxiliary machines over the past several years, employs AI with its robots to monitor cycle times and control robots’ speeds outside the molding machine.
Based on factors like changes in material, ambient temperature, machine wear, tool wear, and other influences, “AI can determine which machine parameters need to be changed so that the product can be produced within its quality tolerances. This can take months, as errors first must occur in order to learn from them.”
One application Arburg is working on is the automatic programming of its Multilift linear robotic systems. “The idea is that the operator simply enters the destination, as with a car navigation device, and the system automatically calculates the optimal route. For robotic systems, this means that the operator simply enters the desired start and end positions, and the control system takes care of the rest.”
In addition to the robots and auxiliaries connected to the machines on display, a number of stand-alone solutions will also be shown at the FIP.
Geoff Giordano is a tech journalist with more than 30 years’ experience in all facets of publishing. He has reported extensively on the gamut of plastics manufacturing technologies and issues, including 3D printing materials and methods; injection, blow, micro and rotomolding; additives, colorants and nanomodifiers; blown and cast films; packaging; thermoforming; tooling; ancillary equipment; and the circular economy. Contact him at [email protected].
Finally, WITTMANN BATTENFELD France will provide tangible evidence of the WITTMAN Group’s expertise in dosing technology by showing a volumetric Dosimax MC Balance blender and a Gravimax primus 14 blender with real-time weighing.
“AI is becoming increasingly important in mechanical engineering, not least because of the need to automate injection molding processes efficiently and flexibly despite ever smaller batch sizes and shorter product life cycles,” said Werner Faulhaber, Director of Research and Development at Arburg. “Application examples of AI include automatic programming of robotic systems, targeted malfunction remedying, and a spare parts system with ‘intelligent’ image processing. Arburg is working on making injection molding more intelligent, step by step — ensuring that the machine continuously learns, keeps itself stable, and can even optimize itself in the future.”
Furthermore, WITTMANN BATTENFELD France will exhibit a selection from the WITTMANN Group’s range of materials handling technology. In addition to central conveyors and stand-alone conveyors, such as the Feedmax S3 net, the exhibits will also include the new Feedmax Clean with dedusting function, which has been specially developed in response to the more and more stringent demands of the circular economy and the resulting increase in plastic granulates containing dust. The program will be rounded off with an XMB filter station and a Codemax RFID-controlled coupling station, which in combination with the M8 network control system ensures correct material feeding.
Comparing AI and machine learning, Glueck said, “AI actually requires a much higher time investment and, correspondingly, a higher financial investment. A large number of parameters must be recorded from a running process and the relevant parameters are determined on the basis of the deviations. These are compared with measurement data of the product.”
Another Wittmann feature, Eco-Vac conserves energy by setting a few parameters on the robot and allowing the robot to turn its vacuum circuits off and on. “The robot monitors the vacuum level of the circuit used for picking the part out of the mold. If the robot senses the vacuum has reduced to a level that it could drop the part before it is told to, the robot will turn the vacuum on until it reaches the safe level again, then shuts back off.” This feature cuts the amount of compressed air each robot uses “and could save customers hundreds of dollars a year per robot.”
Wittmann Battenfeld’s HiQ software can generally be retrofitted even to older injection molding machines equipped with a B8 machine control.
Wittmann co-funded such an assessment program with Austria’s Montanuniversität Leoben university, “but we found that the time needed to make it workable for production had to be questioned because in addition to the long-term investigation of the process, you also need the manpower necessary to handle it.”
AI in manufacturing encompasses an array of technologies that allow machines to perform with intelligence that emulates that of humans. Machine learning and natural language processing help machines approximate the human capacity to learn, make judgments, and solve problems. Data-enhanced efficiency keeps processes moving faster and more cost-effectively.
“The technology draws new conclusions from current parameters and, thus, becomes increasingly intelligent as it monitors performance,” said Product Manager Christian Glueck. “We limit it to a methodical determination of parameters. Therefore, the time required to use the technology is minimal, as is the price.”
Arburg forms flexible — and controllable — production systems by combining machines, automation, and proprietary IT solutions. The company’s Gestica control system, with its intelligent assistant functions, is integral to those systems. “All Kuka six-axis robots, for example, have been equipped with the new Gestica user interface as standard,” Faulhaber noted. “This simplifies programming, as well as the monitoring, storage, and evaluation of process data.”
The robot receives its energy supply directly from the DC intermediate circuit of the EcoPower and also returns any surplus energy derived from axis deceleration to that circuit. On this machine, a crinkle box made of PP will be manufactured using a single-cavity mould supplied by the Austrian company Haidlmair. The power supply for the machine will come from ultra-modern ecological salt battery technology on sodium-nickel basis supplied by innovenergy. The battery has a total capacity of over 45 kWh, more than sufficient for continuous operation of the machine during an entire 8-hour trade fair day. To compensate the injection moulding machine’s short-term load peaks, additional electrochemical capacitors known as super-caps are used to complement the sodium-nickel storage units.
“One of Arburg's medium-term goals is to develop a system for digital twins of customized injection molding machines. This will open up completely new possibilities for simulating the cycle and making energy predictions. In addition, 3D views and installation plans of the machine — stored in the arburgXworld customer portal and in the control system — support the operator,” said Faulhaber.
Thanks to the integrated arburgXworld Control FillAssist, Arburg’s Allrounder "knows" the molded part it is supposed to produce. One issue for the future is to ensure that the machine not only keeps itself stable, but also self-optimizes.
A further highlight of the presentation will be a selection from the range of granulators manufactured locally at WITTMANN BATTENFELD France. The exhibits will include G-Max 9 and G-Max 23 grinders as well as the screenless granulator models S-Max 2 and the new S-Max Dual 6. The S-Max Dual 6 is the ideal granulator for central grinding of reject parts, but it can also be used for in-line recycling of sprue from injection moulding machines. For use beside the press, the footprint of the S-Max Dual 6 has been reduced by about 25% compared to its predecessor model.
At the FIP Solution Plastique 2024 in Lyon to be held from June 4 to 7, WITTMANN BATTENFELD will present ultra-modern injection moulding technology, automation and auxiliaries to trade visitors.
Arburg uses AI “to develop master models using experience and data collected over the years on process, material, and machinery,” Faulhaber continued. “The customer could then sharpen the provided master model ‘on edge’ and optimize their processes. The in-house development Gestica control system, the Arburg host computer system, and the arburgXworld customer portal give an advantage here.
From the segment of temperature control technology, one temperature controller from the Tempro basic series will be presented at the FIP, plus a single-circuit and a dual-circuit appliance from the Tempro plus D series. The features of auxiliaries from the Tempro plus D series are their comfortable touch control units and optional extras such as utilisation-controlled pump regulation with EcoDrive. In addition, WITTMANN BATTENFELD France will show a selection from the WITTMANN portfolio of flow controllers. A WFC 120 flow regulator will also be on display. The WFC is an appliance to control both flow quantity and temperature. It comes with a maintenance-free flow measurement unit.
From its range of robots, WITTMANN BATTENFELD France will exhibit at the FIP a WX138T with AC servo axis and a Primus 128 model with the new R9 robot control unit. With its control cabinet flange-mounted to the horizontal axis and its internal power chain, the WX138T is particularly suited for compact production cells. It is driven by toothed belts to reduce its operating noise to a minimum. The Primus 128 for pick-&-place applications offers a robust axle design thanks to its vertical Y axis supported by a steel profile. A lubrication system for the vertical axis included as standard ensures a continuous supply of lubricant and consequently quiet operation of the drive system with minimal wear.
Energy measurements using the IMAGOxt software will be carried out on all injection moulding machines shown at the WITTMANN BATTENFELD booth. IMAGOxt, a program developed by WITTMANN Digital, will be used to display the energy consumptions of all injection moulding machines exhibited at the fair, and the auxiliaries connected to them. The program also calculates the CO2 consumption. All values calculated can be recorded in quality reports and thus remain available for long-term analyses. IMAGOxt is available as a web application, as an optional extension of the WITTMANN TEMI+ MES system, or as a stand-alone program.
The SmartPower B8X to be presented comes equipped with all-electric injection units, thus combining the advantages of the servo-hydraulic SmartPower’s flexible, generous mould space with the all-electric EcoPower’s excellent performance and high precision.
The company’s machine-learning capabilities — HiQ Flow and CMS technology — will be on display at this year’s K show on Oct. 19 to 26 in Düsseldorf, Germany. The speed of ROI can be as short as a few cycles with HiQ Flow, and the software can often be retrofitted to older injection molding machines equipped with a B8 machine control. A CMS Pro version will be available at a later date.
The company’s Eco-Mode saves wear and tear on the robot by ensuring it does not run faster than necessary — ultimately saving maintenance and energy costs. Offered standard on many Wittmann robots, Eco-Mode “requires no special programming or interface with the IMM or operator/programmer,” said Jason Long, National Sales Manager for robots and automation for Wittmann USA. “All the end user has to do is tell the robot how many seconds it should get back over the IMM before the mold opens.”
GETTING A QUOTE WITH LK-MOULD IS FREE AND SIMPLE.
FIND MORE OF OUR SERVICES:
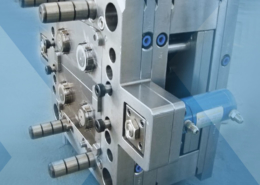
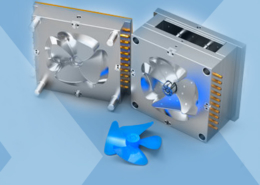
Plastic Molding

Rapid Prototyping
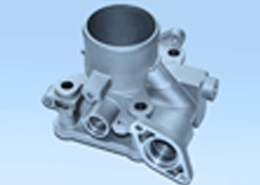
Pressure Die Casting
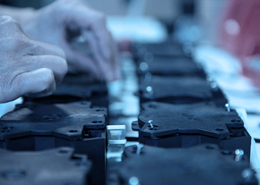
Parts Assembly
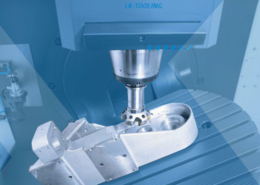