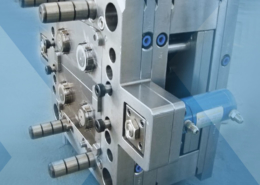
Hungarian plastic injection mould maker Euroform automates machining - plastic i
Author:gly Date: 2024-09-30
“From our early days producing Ooho in our student kitchen, to seeing runners consume them in their thousands at the London Marathon, all the way through to today where we’re making millions of real, credible packaging solutions for industries – it’s just huge. This investment brings us one step closer to a world where truly plastic-free packaging is the standard, not the exception.”
The recently qualified medical device development tool (MDDT) provides an accelerated test methodology to address the performance of new materials at long human implant times. Not only does careful use of accelerated testing reduce dependency on preclinical models, the MDDT increases certainty in predictions of a new material’s bio-durability. Kimberly Chaffin, vice president corporate technologist at Medtronic, will review predictive accelerated testing conducted for a series of commonly implanted medical device polymers, where the accelerated predictions are validated with up to 20 years of real-time human implant data.
Durable medical devices typically are expected to function for up to 10 years or more under a combination of mechanical and/or thermal loads. Designing and analyzing medical devices that incorporate polymeric components, therefore, requires a thorough understanding of the material properties that influence creep and fatigue performance, as well as test and analysis methods for evaluating device performance. In this session, Paul Briant, practice director and principal engineer at Exponent, will review polymer properties that affect creep and fatigue, test methods for evaluating long-term creep and fatigue, and simulation methods of polymer performance under thermal and mechanical loads.
Plastics have been instrumental in advancing medical technology for many decades, but, to my mind, a seminal moment happened during WW II, when plastic replaced glass in IV bags on the battlefield and proved its superiority, particularly when it comes to breakage. Since then, polymers have been on a roll in medical technology. From single-use devices that prevent patient infections to resorbable implants that eliminate having to undergo a second surgical procedure to remove the devices, plastics have revolutionized healthcare practices, improving patient outcomes and quality of life.
Wei Shen, associate professor in the Department of Biomedical Engineering at the University of Minnesota, will present a class of thermoplastic elastomers that exhibit elastomeric properties in both wet and dry environments. The elastomers can be processed via 3D printing, extrusion, and hot-press processing at 60°C. The collective elastomeric, biodegradable, biocompatible, and thermoplastic properties make these materials highly valuable for biomedical applications.
“Our goal has always been to create products and materials that can make a real difference," added Rodrigo Garcia Gonzalez, Notpla’s other co-founder and co-CEO.
To reduce friction in products made from thermoplastic elastomers (TPEs), lubricious coatings can be applied to the devices or the TPEs can be compounded with specialty additives. Shruba Manna , senior development engineer at compounder Foster Corp., will explain the low-friction technolgies available on the market along with the effect of additives on a polymer’s properties and processability.
Sustainable packaging specialist Notpla has completed a £20m series A+ fundraising round, doubling its initial target despite challenging economic conditions.
Material science experts will discuss current and emerging applications for medical plastics during a daylong conference track.
Here are capsule summaries of some of the key sessions and speakers at the medical plastics conference track, which takes place on Oct. 16 in room 102F.
A daylong conference track at Plastec Minneapolis is devoted to current and emerging medical plastics technology, bringing together experts from industry and academe to share insights on everything from micromolding to biostability in implants.
Co-founder and co-CEO Pierre Paslier said: “Our investors recognise the commercial potential of our technology and our unique solutions. This funding allows us to accelerate our growth and continue leading the market in sustainable innovation.
In micromolding, plastics can reach a point where shear thinning behavior is stretched to its limits. In this talk, Patrick Haney, R&D engineer at MTD Micro Molding, will explore the typical flow behavior of plastics and discuss the intriguing phenomena that arise under extreme shear conditions. He will touch on the ramifications of these changes on the final micromolded product, including the effects on final part microstructure as it applies to device application.
Industry experts from the Society of Plastics Engineers (SPE) Medical Plastics Division will discuss growth drivers and trends in medical polymers, including new resins, advanced molding methods, sustainability, personalized medicine, and regulatory shifts. Rob Klein, senior principal materials engineer at Atricure, and Chris Lyons, managing scientist at Exponent, are scheduled to speak. They will be immediately followed by Arthur Erdman, founding director of the Bakken Medical Devices Center, at 9:30 a.m. Named for Earl Bakken, the founder of Medtronic, the center follows his lead in exploring new avenues for medtech innovation through material development and 3D printing. Erdman will discuss several case studies illustrating the role polymers play in advancing medical technology.
Plastec Minneapolis is part of the Advanced Manufacturing Minneapolis event, along with co-locates MD&M, ATX, MinnPack, and D&M, at the Minneapolis Convention Center on Oct. 16 and 17, 2024. The event is organized by Informa Markets – Engineering, which also produces PlasticsToday.
Customers include Compass Group, Just Eat Takeaway.com, Aston Villa FC, The O2 Arena, Allianz Stadium, and Tottenham Hotspur FC.
Since launching in 2014, Notpla has launched products including ‘Ooho’, an edible liquid bubble made from seaweed. The company has applied its innovation to takeaway food packaging, and this year the firm added rigid cutlery to its portfolio, producing a compostable ice-cream spoon which is now available at scale.
Jacobs Media is a company registered in England and Wales, company number 08713328. 3rd Floor, 52 Grosvenor Gardens, London SW1W 0AU. © 2024 Jacobs Media
Editor in chief of PlasticsToday since 2015, Norbert Sparrow has more than 30 years of editorial experience in business-to-business media. He studied journalism at the Centre Universitaire d'Etudes du Journalisme in Strasbourg, France, where he earned a master's degree.
“This investment is more than just financial support; it’s a validation of the growing demand from consumers around the world for real solutions to the plastic problem.”
The capital injection should prepare Notpla to further scale its seaweed-based materials solution and build on its US presence.
GETTING A QUOTE WITH LK-MOULD IS FREE AND SIMPLE.
FIND MORE OF OUR SERVICES:
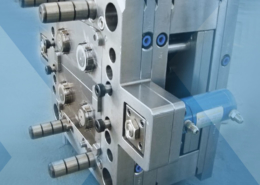
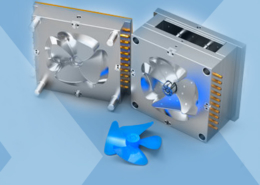
Plastic Molding

Rapid Prototyping
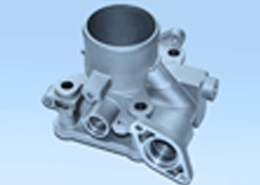
Pressure Die Casting
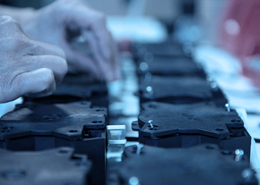
Parts Assembly
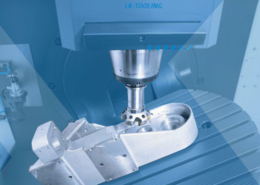