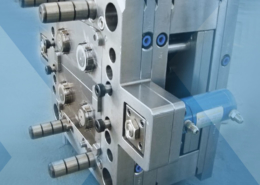
Unveiling the Potential of PP Moulding
Author:gly Date: 2024-06-08
Introduction
PP moulding, an innovative manufacturing process, holds immense promise in various industries. As a method for producing plastic components, PP moulding offers versatility, cost-efficiency, and design flexibility. This article explores the intricacies of PP moulding, delving into its applications, advantages, and evolving technologies, captivating readers with its potential and providing essential background information.
Understanding PP Moulding
What is PP Moulding?
PP moulding, or polypropylene moulding, is a manufacturing technique used to produce plastic components from polypropylene resin. It involves injecting molten polypropylene into a mould cavity under high pressure, allowing it to cool and solidify into the desired shape.
Injection Moulding Process
The injection moulding process begins with the heating of polypropylene resin pellets to a molten state. The molten material is then injected into a mould cavity, where it cools and solidifies, taking the shape of the mould. Once the part has sufficiently cooled, it is ejected from the mould, ready for further processing or assembly.
Advantages of PP Moulding
PP moulding offers several advantages over traditional manufacturing methods. It allows for high production volumes, precise dimensional control, and the ability to create complex geometries with ease. Additionally, polypropylene is a lightweight, durable, and cost-effective material, making it ideal for a wide range of applications.
Applications of PP Moulding
Industrial Applications
Automotive Components
PP moulding is widely used in the automotive industry for manufacturing interior and exterior components such as bumpers, dashboards, door panels, and trim pieces. The lightweight and impact-resistant nature of polypropylene make it an ideal material for these applications.
Consumer Goods
In the consumer goods sector, PP moulding is utilized for producing a variety of products, including household appliances, packaging containers, toys, and electronic devices. Its versatility and ability to incorporate intricate designs make it a preferred choice for manufacturers seeking cost-effective solutions.
Medical Devices
Disposable Medical Supplies
PP moulding is integral to the production of disposable medical supplies such as syringes, IV catheters, surgical instruments, and pill dispensers. The sterile, biocompatible nature of polypropylene ensures the safety and reliability of these critical healthcare products.
Diagnostic Equipment
In addition to disposable supplies, PP moulding is employed in the manufacturing of diagnostic equipment such as test kits, specimen containers, and lab consumables. Its precision and consistency contribute to the accuracy of diagnostic procedures in medical laboratories.
Innovations in PP Moulding Technology
Advanced Materials
Reinforced Polypropylene
Recent advancements in PP moulding technology have led to the development of reinforced polypropylene composites, incorporating materials such as glass fibers, carbon fibers, or minerals. These reinforced materials offer enhanced strength, stiffness, and heat resistance, expanding the range of applications for PP moulding.
Bio-based Polypropylene
The emergence of bio-based polypropylene derived from renewable sources presents a sustainable alternative to traditional petroleum-based plastics. Bio-based polypropylene retains the properties of conventional polypropylene while reducing reliance on fossil fuels and mitigating environmental impact.
Conclusion
In conclusion, PP moulding represents a cutting-edge manufacturing process with vast potential across various industries. Its versatility, cost-efficiency, and design flexibility make it an indispensable tool for producing a wide range of plastic components. By understanding the intricacies of PP moulding and embracing innovative technologies, manufacturers can unlock new opportunities for efficiency, sustainability, and product innovation.
Future Directions
Looking ahead, ongoing research and development efforts in PP moulding technology are poised to further enhance its capabilities and applications. Advancements in materials science, process optimization, and sustainability initiatives will continue to drive innovation in the field, paving the way for a more sustainable and efficient manufacturing ecosystem.
GETTING A QUOTE WITH LK-MOULD IS FREE AND SIMPLE.
FIND MORE OF OUR SERVICES:
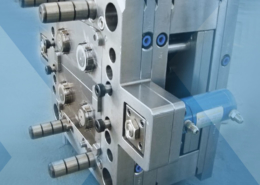
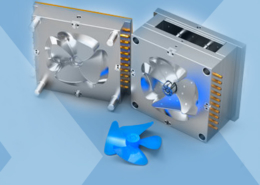
Plastic Molding

Rapid Prototyping
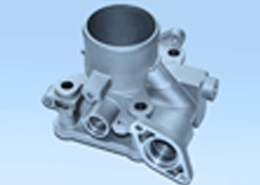
Pressure Die Casting
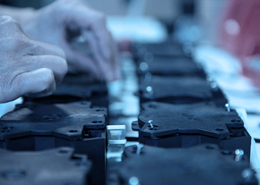
Parts Assembly
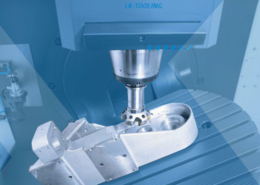