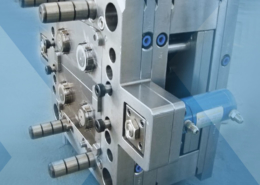
How to Remove Mold from Every Type of Outdoor Furniture (Including Plastic!) - p
Author:gly Date: 2024-09-30
Discover how artifical intelligence is revolutionizing plastics processing. Hear from industry experts on the future impact of AI on your operations and envision a fully interconnected plant.
Join Wittmann for an engaging webinar on the transformative impact of manufacturing execution systems (MES) in the plastic injection molding industry. Discover how MES enhances production efficiency, quality control and real-time monitoring while also reducing downtime. It will explore the integration of MES with existing systems, emphasizing compliance and traceability for automotive and medical sectors. Learn about the latest advancements in IoT and AI technologies and how they drive innovation and continuous improvement in MES. Agenda: Overview of MES benefits What is MES? Definition, role and brief history Historical perspective and evolution Longevity and analytics Connectivity: importance, standards and integration Advantages of MES: efficiency, real-time data, traceability and cost savings Emerging technologies: IoT and AI in MES
Resin drying is a crucial, but often-misunderstood area. This collection includes details on why and what you need to dry, how to specify a dryer, and best practices.
In a time where sustainability is no longer just a buzzword, the food and beverage packaging industry is required to be at the forefront of this innovation. By adopting circular packaging processes and solutions, producers can meet regulatory requirements while also satisfying consumer demand and enhancing brand reputation. Join Husky to learn more about the broader implications of the circular economy — as well as how leading brands are leveraging this opportunity to reduce costs, increase design flexibility and boost product differentiation. Agenda: The cost and operational benefits of embracing circularity Key materials in circular packaging — including rPET and emerging bioplastics How to design a circular food and beverage package Strategies for selecting sustainable closures to future-proof packaging solutions Optimization and streamlining of production processes for enhanced efficiency How Husky Technologies can enable your sustainable success
After a year of testing to gain experience, EVCO is ready to begin production with its first LSR press for programs in medical and lighting. (Photos: EVCO Plastics)
When EVCO got its first plastic 3D printer in 2014, the goal was to produce parts for internal use—jigs, fixtures and other assembly components, as well as R&D prototypes. “Additive manufacturing pushes the boundaries of part design,” says Degenhardt, “and there’s a lot less risk involved in testing concepts this way.”
In Oshkosh, Wis., where EVCO focuses on larger machines, and expanded by 31,000 ft2 in 2019, the company has leased and additional 120,000 ft2 for contract manufacturing and warehousing—specifically new large-scale assembly projects. The company recently added a 1000-ton Engel press to the Oshkosh plant and is expecting arrival of a 4400-ton Engel machine this summer. That will be the largest ever at EVCO, which has two 3500-ton Engels there. Notes Bernie Degenhardt, corporate automation manager, “It will come in 20 containers and take three months to assemble.” It’s intended for agricultural and power-sports applications.
The breakthrough in precision combined with economic efficiency has been achieved in recent years with the 2-photon printer of UpNano, a start-up also based in Vienna and a partner of NanoVoxel. This printer is based on the principle of non-linear absorption of photons, called two-photon polymerisation (2PP). A femtosecond laser emits a narrowly focused beam to excite a photosensitive resin. The scanner unit moves the laser beam via Galvano mirrors and lens systems to cure the resin. Like SLA/DLP 3D printing, when the light is absorbed, it triggers a chemical reaction in the resin, causing it to polymerise and solidify at the focal point of the laser beam. However, in a deviation from established 3D printing technologies, 2PP achieves full control of z-dimension polymerisation, so holes and cavities are precise and round. The 2PP printing process offers unparalleled precision and resolution to most other manufacturing techniques, enabling the creation of complex 3D micro-structures with sub-micron accuracy, even down to the nanometre range. This makes it ideal for applications requiring particularly intricate detail with high surface quality. A variety of photosensitive resins are available for 2PP printing, including photopolymers and hybrid materials. These materials can be tailored to specific applications and offer a wide range of mechanical, optical, and chemical properties.
Custom injection molder is adding floorspace, machine capacity, and contract manufacturing capabilities at multiple plants in the U.S. and Mexico.
In Calhoun, Ga., EVCO purchased a second plant, dubbed CAL2 (40,000 ft2), last year, and just started production there in March. It houses EVCO’s first white room, outfitted with high-speed automation, and five bays designated for the firm’s foray into LSR molding.
This Knowledge Center provides an overview of the considerations needed to understand the purchase, operation, and maintenance of a process cooling system.
In this collection of articles, two of the industry’s foremost authorities on screw design — Jim Frankand and Mark Spalding — offer their sage advice on screw design...what works, what doesn’t, and what to look for when things start going wrong.
The combination of 2PP printing and µ-injection moulding is not limited to only the high precision rapid tooling process. NanoVoxel GmbH brings a significant addition to the micromanufacturing industry with its capacity to 2PP print directly on parts of different materials manufactured with other processes. This print can be made onto many materials including glass, ceramics, carbon substrates, metals, and plastics. Moreover, the ability to combine varied materials for different functions offers customisability ideal for rapid prototyping, product development, and mass manufacturing. This enables customers to imprint detailed functional features directly onto bulky and larger parts obtained from more efficient processes. Initial applications have been successfully applied in the microfluidics world, where NanoVoxel printed unmouldable features into commercial chips, using their advanced printing process only where needed.
NanoVoxel's efficiency with the micromanufacturing process unlocks new creative avenues for designers and engineers across diverse industries and changes the way in which to approach design and fabrication of intricate, customised, and functional micro-scale parts.
The aim of this presentation is to guide you through the factors and the numbers that will help you determine if a robot is a smart investment for your application. Agenda: Why are you considering automation? What problems are you trying to solve? How and why automation can help Crunch the numbers and determine the ROI
technotrans says climate protection, energy efficiency and customization will be key discussion topics at PTXPO as it displays its protemp flow 6 ultrasonic eco and the teco cs 90t 9.1 TCUs.
Gifted with extraordinary technical know how and an authoritative yet plain English writing style, in this collection of articles Fattori offers his insights on a variety of molding-related topics that are bound to make your days on the production floor go a little bit better.
Jason Glanzer, EVCO automation engineer and integration lead, has been focused on high-volume, high-speed automation. “We’re doing a lot of medical kitting with 3D inspection, heat sealing and assembly.”
A new low-pressure molding process, 3D printing of production parts and prototype tooling, collaborative robots, and process monitoring with automatic QC are all on the menu.
Such assembly systems are typically built in-house by EVCO’s automation team; but given the accelerating pace of new projects, they have sought outside help. For example, Germany’s Ilsemann Automation helped EVCO’s team build the first of an intended four cells for packaging components. As described by Glanzer, each cell will have two Husky presses, each with a 16-cavity stack mold and custom-built side-entry robots, operating on an 8- to 12-sec cycle with 1.5-sec takeout time. Parts from both presses travel on a common conveyor to an assembly station where the mating parts are snapped together. All parts are weighed and inspected by metal detectors and layer-packed in gaylords. These systems are one of the first candidates for implementing EVCO's SCADA (supervisory control and data-acquisition) system.
Now that the company has 15 printers, such internal uses are still the dominant purpose for those machines. But in 2020, the COVID-19 pandemic demonstrated their value in making production parts on short notice. “We printed headbands for a proprietary face shield while we waited for steel to be cut for injection molds,” recalls Bartz.
August 29-30 in Minneapolis all things injection molding and moldmaking will be happening at the Hyatt Regency — check out who’s speaking on what topics today.
Mixed in among thought leaders from leading suppliers to injection molders and mold makers at the 2023 Molding and MoldMaking conferences will be molders and toolmakers themselves.
In this collection, which is part one of a series representing some of John’s finest work, we present you with five articles that we think you will refer to time and again as you look to solve problems, cut cycle times and improve the quality of the parts you mold.
An example of NanoVoxel’s service is the development and manufacturing of an endoscope for the aiEndoscope company (Picture 4): the segments of the endoscope have been initially printed in different design variations at the prototyping stage for geometrical tests and optimisation. Upon design validation from the customer, the quickly moulded parts were produced and enabled functional and mechanical testing. All the manufacturing process and iterations on this project were completed within 5 weeks.
NanoVoxel has since achieved a breakthrough in the moulding of micro-parts that was previously impossible to fulfil, enabling the moulding of small, detailed structures with high accuracy and repeatability within tolerances of a few microns. In addition, high-precision 2PP 3D-printing to create mould cavities enables larger parts with single-digit micron features, which would otherwise be time-consuming, expensive, or impossible to produce.
Most of EVCO’s printers are MarkForged models that use filament extrusion. But the newest model is an SLA (stereolithography) type that uses liquid resin and photocuring. “It provides very high resolution and no lines between layers,” says Degenhardt. He also notes that EVCO uses outside vendors to produce metal parts by AM, such as robot end-of-arm tooling, conformal cooling channels for injection molds, and prototype cavity/core sets. What about getting their own metal 3D printer? “It’s on the wish list,” he replies.
Across the show, sustainability ruled in new materials technology, from polyolefins and engineering resins to biobased materials.
All told, Bartz says, EVCO now has 10 plants with 1.2 million ft2 total manufacturing space (20% more than this time last year), 265 injection machines, and 1700 employees worldwide. “We added 200 in the last year,” says Bartz, acknowledging that as quite an achievement in times of acute labor shortages. “It’s even more of a problem with COVID illnesses,” she notes. “But fortunately we have great relationships with a lot of technical schools and their professors. We conduct tours for students, and we have internship programs.”
Exhibitors and presenters at the plastics show emphasized 3D printing as a complement and aid to more traditional production processes.
Plastics Technology covers technical and business Information for Plastics Processors in Injection Molding, Extrusion, Blow Molding, Plastic Additives, Compounding, Plastic Materials, and Resin Pricing. About Us
Outside the U.S., EVCO’s M2 plant in Mexico recently added 17,200 ft2, and its China plant is now leasing a second building (40,000 ft2) for its tooling department.
Mike Sepe has authored more than 25 ANTEC papers and more than 250 articles illustrating the importance of this interdisciplanary approach. In this collection, we present some of his best work during the years he has been contributing for Plastics Technology Magazine.
3D printing a core and cavity on machine from Gefertec, followed by machining, allowed for a complete mold tool to be produced in three days.
Second quarter started with price hikes in PE and the four volume engineering resins, but relatively stable pricing was largely expected by the quarter’s end.
As the coronavirus pandemic eased its grip on the global economy, EVCO was ready with freshly added capacity at several locations. It purchased around 20 injection machines in 2021. At the start of 2022, the company moved its corporate headquarters in DeForest, Wis., to its MED (medical and electronics) facility, another of the three EVCO facilities there, which has remodeled its office space with an addition of 8000 ft2.
Supply-chain snafus are another widespread obstacle that has hamstrung production at many molders. However, EVCO is able to sidestep that challenge in ways that may not be accessible to smaller molders. Degenhardt explains, “Getting components is a big deal. So we have been stockpiling control components, for example. We have had some problems with resin lead times, but it’s getting a little better now. Machine deliveries have been okay—we’ve been lucky to get some from orders canceled by other molders. Robots, in fact, have longer lead times than injection presses. So we recently bought five robots to put on the shelf for later use.”
Through the combination of the high precision 2PP µ-3D printing and the performance of the Micropower 15t micro injection moulding machine from WITTMANN BATTENFELD, NanoVoxel has successfully reduced the fabrication timeline of high precision micro-parts to two weeks. Integration of these micro-manufacturing methods allows for swift prototyping and opens new possibilities in engineering and design across industries. With initial applications in biomedical and consumer electronics, the breakthrough includes the production of intricate microparts with unprecedented accuracy and design freedom.
Through its commitment to advancing micromanufacturing technologies and re-imagining solutions, NanoVoxel welcomes unconventional part geometry and strives to provide a creative, efficient, and yet simple approach to manufacturing
The capabilities of combining different processes including mastering, casting, and sintering, allow NanoVoxel to create moulds with the highest precision, not only from 3D printing materials but also with more robust materials like glass, ceramics, and metals.
NanoVoxel aims to become a one-stop service platform offering flexible and multiple manufacturing solutions and strives to become one of the most innovative companies in the micro manufacturing world. NanoVoxel's multi-disciplinary team of experts combine these different technologies to offer prototypes through to high-volume production as a service provider. This remarkable accomplishment compresses the timeline for structure fabrication into an incredible two-week span.
To leverage the highest precision of the moulds, NanoVoxel uses the MicroPower 15 t (Picture 5) from WITTMANN BATTENFELD, a manufacturer of injection moulding machines and automation solutions. With a clamping force of 150 kN, the machines of the MicroPower series are designed for the economical production of exceedingly small and micro parts with maximum precision and repeat accuracy. A two-stage screw-piston injection unit with a shot volume of 1.2 to 6.0 cm3 injects a thermally homogeneous compound. This makes it possible to produce parts with outstanding precision, extremely stable production, and exceptionally short cycle times. The distinctive design of the machine allows the injection plunger to nearly reach the parting line of the mould. This reduces the mass cushion to a minimum. In addition, the standard version of the machine is already ideally suited for production under clean room conditions: it is designed with an enclosed housing cell. The housing cell offers enough space for the integration of equipment options like a rotary table, robot, material drier, and temperature control units. Robots and peripheral equipment from WITTMANN are specially adapted for this machine.
High precision microparts are finding increasing relevance in different sectors including biomedical, consumer electronics, and many others. Most of the applications being developed require designs that require high precision, fast iterations, and challenge conventional design freedom.
While prices moved up for three of the five commodity resins, there was potential for a flat trajectory for the rest of the third quarter.
EVCO also has completed a 13,000-ft2 expansion of its Advanced Molding Plant (AMP) in DeForest to accommodate new 560- and 720-ton Engel presses, additional warehousing, a new grinding room, and workspace for the automation team. Anna Bartz, director of marketing, expects that the building will need another expansion in the next two to four years.
Since 2018, EVCO has supplemented its conventional molding takeout robots with the newer category of collaborative robots, or cobots. “Cobots are a popular topic of conversation around here,” says Glanzer. “We have more and more contract-manufacturing business, which creates more opportunities to use cobots for inspection and assembly.” In particular, he notes, “We are working on using them to pick inserts out of a bin and hand them to a faster robot for insertion into the mold. Cobot bin picking offers a higher degree of flexibility in terms of part variations than using traditional bowl feeders for manipulating and feeding components—especially with the help of 3D vision systems."
EVCO is expecting its largest press yet, a 4400-tonner that will arrive in 20 containers and take three months to assemble.
Thousands of people visit our Supplier Guide every day to source equipment and materials. Get in front of them with a free company profile.
Additive technology creates air pockets in film during orientation, cutting down on the amount of resin needed while boosting opacity, mechanical properties and recyclability.
However, this is made possible when two advanced technologies in micromanufacturing are combined: 2PP µ-3D printing and micro-injection moulding. This expertise is NanoVoxel's forte, a start-up founded in Vienna in 2022 to disrupt the industry standard of such micro-components.
Currently the main AM production business that helps pay for the printers’ internal uses is iPhone cases of a carbon-fiber filled nylon with a metal insert. Explains Bartz, “The insert allows consumers to attach scopes and photography equipment to their iPhone. Given the frequency of iPhone design changes, it’s not cost-effective for us to cut new steel with every new release, which is why 3D printing is a sound production solution.”
As reported last year, EVCO outfitted its new CAL2 plant in Georgia with five bays for LSR molding, a new venture for the company. “We had been thinking about LSR for five years,” says Degenhardt. The first machine, a 130-ton Engel tiebarless press with Nexus LSR dosing system and Engel viper robot, is located in the DeForest Innovation Center, where it has been used for development purposes over the past year. Degenhardt is impressed with the integration of the robot and machine: “They share a common controller, so the machine always knows what the robot is doing and vice versa, so there are no crashes and we can optimize the cycle time. Since February, the EVCO team has gained confidence to transition into LSR commercial production. “We’ve been awarded a few programs in medical and lighting,” notes Degenhardt.
While the major correction in PP prices was finally underway, generally stable pricing was anticipated for the other four commodity resins.
Learn about sustainable scrap reprocessing—this resource offers a deep dive into everything from granulator types and options, to service tips, videos and technical articles.
Provisionally, the disadvantage of this technique is its capacity for high volume production, making it uneconomical for parts larger than a few mm.
She says EVCO is not really looking for short-run business in additive manufacturing (AM). However, she acknowledges that a small amount of such business “offsets the cost of new printers, materials, labor, etc. so we’re able to produce things like CMM fixtures, automation components and prototype parts. Keeping the amount of production frees up the printers for our Innovation Center team to test new tooling, fixturing and other protyping.”
Using 2PP printers, micro parts can be printed within hours from a 3D-CAD file with a precision that cannot be achieved by conventional toolmakers, even with the most advanced machinery. Tolerances below 1 µm, structures down to 200 nm, and surface finishes with an average surface roughness better than 10 nm can be produced quickly and economically with this advanced additive manufacturing. Geometries that cannot be produced through injection moulding, due to undercuts for example, can be produced quickly with 3D printing. Picture 2 shows an example of 2PP printed microneedle prototypes, emphasising sharp edges and micro-hollow structures.
Introduced by Zeiger and Spark Industries at the PTXPO, the nozzle is designed for maximum heat transfer and uniformity with a continuous taper for self cleaning.
Plastics Technology’s Tech Days is back! Every Tuesday in October, a series of five online presentations will be given by industry supplier around the following topics: Injection Molding — New Technologies, Efficiencies Film Extrusion — New Technologies, Efficiencies Upstream/Downstream Operations Injection Molding — Sustainability Extrusion — Compounding Coming out of NPE2024, PT identified a variety of topics, technologies and trends that are driving and shaping the evolution of plastic products manufacturing — from recycling/recyclability and energy optimization to AI-based process control and automation implementation. PT Tech Days is designed to provide a robust, curated, accessible platform through which plastics professionals can explore these trends, have direct access to subject-matter experts and develop strategies for applying solutions in their operations.
For example, current manufacturing methods such as CNC, EDM, mask-lithography, and SLA 3D printing struggle to quickly or precisely produce parts like micro-diffusors for acoustic applications featuring 70 µm 3D details (Picture 1); micro-lenses with a roughness below 10 nm; micro-needles with 5 µm tips; micro-nozzles with apertures under 20 µm; and micro-fluidic chips with specialised filters.
EVCO has the financial heft to combat supply-chain uncertainty by stocking up on control components and even buying five robots to put on the shelf for future use.
EVCO’s automation team is busy with projects like this consumer-packaging cell that ties together two injection presses with 16-cavity stack molds to produce mating parts that are conveyed, snapped together, packaged, labeled and inspected, after which data on each assembly is read via barcode and uploaded to a production and quality database in the cloud.
The limitations of both micro-moulding and micro 3D printing pose the question: What changes can expedite lead times, keep high precision, and still maintain high productivity?
While prices moved up for three of the five commodity resins, there was potential for a flat trajectory for the rest of the third quarter.
This month’s resin pricing report includes PT’s quarterly check-in on select engineering resins, including nylon 6 and 66.
Take a deep dive into all of the various aspects of part quoting to ensure you’ve got all the bases—as in costs—covered before preparing your customer’s quote for services.
In this collection of content, we provide expert advice on welding from some of the leading authorities in the field, with tips on such matters as controls, as well as insights on how to solve common problems in welding.
Mold maintenance is critical, and with this collection of content we’ve bundled some of the very best advice we’ve published on repairing, maintaining, evaluating and even hanging molds on injection molding machines.
Core Technology Molding turned to Mold-Masters E-Multi auxiliary injection unit to help it win a job and dramatically change its process.
Adds Brandon Westra, automation engineer, “We had 20 molds built to run parts for two assembly systems with UV cured adhesives.”
The Plastics Industry Association (PLASTICS) has released final figures for NPE2024: The Plastics Show (May 6-10; Orlando) that officially make it the largest ever NPE in several key metrics.
There are a lot of 3D printing technologies out there, and it’s not uncommon for processors new to additive manufacturing to get tripped up. Here are some typical snafus, along with advice on how to avoid them before you start making parts.
Adding people, plants and machines, expanding capabilities in LSR, high-tonnage presses, automation and 3D printing—EVCO Plastics maintains momentum through challenging times.
Multiple speakers at Molding 2023 will address the ways simulation can impact material substitution decisions, process profitability and simplification of mold design.
EVCO operates 15 3D printers mainly for internal prototypes and automation components, but limited production business helps pay for these machines and materials.
Formnext Chicago is an industrial additive manufacturing expo taking place April 8-10, 2025 at McCormick Place in Chicago, Illinois. Formnext Chicago is the second in a series of Formnext events in the U.S. being produced by Mesago Messe Frankfurt, AMT – The Association For Manufacturing Technology, and Gardner Business Media (our publisher).
NanoVoxel, based in Austria, has innovated this approach that marks a significant advancement in the landscape of efficient and customised micromanufacturing.
Degenhardt describes another large cell for COVID DNA test kits in the MED facility. It collects six different parts from six injection presses. One of those parts is a fluid-filled vial—itself an assembly of three parts from a different cell. The test-kit cell uses several feeder bowls, an assembly conveyor, label wrapper, Tyvek sealing, vision inspection and a barcode reader to send production data to the cloud for access by the plant computer system. “This is new for us—using a SCADA system to collect data from the production line and send it to the cloud, so we can verify production quantities and quality data in real time. The cell is designed to make 70 million test kits a year.”
Processors with sustainability goals or mandates have a number of ways to reach their goals. Biopolymers are among them.
New plant in Georgia has room for 20 injection machines, including the company’s first LSR molding presses to enhance its medical capabilities.
Sustainability continues to dominate new additives technology, but upping performance is also evident. Most of the new additives have been targeted to commodity resins and particularly polyolefins.
Join Engel in exploring the future of battery molding technology. Discover advancements in thermoplastic composites for battery housings, innovative automation solutions and the latest in large-tonnage equipment designed for e-mobility — all with a focus on cost-efficient solutions. Agenda: Learn about cutting-edge thermoplastic composites for durable, sustainable and cost-efficient battery housings Explore advanced automation concepts for efficient and scalable production See the latest large-tonnage equipment and technology innovations for e-mobility solutions
While the melting process does not provide perfect mixing, this study shows that mixing is indeed initiated during melting.
All drive modules of the all-electric drive system, including all mechanical components, are encapsulated in easy-to-clean housings. The extremely well controlled injection of thermally homogeneous thermoplastics in exceptionally small quantities is necessary for successful injection moulding of precise and quality consistent mass production of micro-parts.
In this three-part collection, veteran molder and moldmaker Jim Fattori brings to bear his 40+ years of on-the-job experience and provides molders his “from the trenches” perspective on on the why, where and how of venting injection molds. Take the trial-and-error out of the molding venting process.
To answer this question NanoVoxel GmbH combines the best of both worlds, establishing the union of 2PP printing with micro-injection moulding its core business. By using 2PP 3D-printing to quickly produce a high-precision mould for the micro-injection, it replicates the precision and the resolution of 2PP in moulded micro-parts with highest efficiency. Picture 3 shows an example of a micro-gear moulded from one of these printed cavities.
When, how, what and why to automate — leading robotics suppliers and forward-thinking moldmakers will share their insights on automating manufacturing at collocated event.
Join this webinar to explore the transformative benefits of retrofitting your existing injection molding machines (IMMs). Engel will guide you through upgrading your equipment to enhance monitoring, control and adaptability — all while integrating digital technologies. You'll learn about the latest trends in IMM retrofitting (including Euromap interfaces and plasticizing retrofits) and discover how to future-proof your machines for a competitive edge. With insights from industry experts, it'll walk you through the decision-making process, ensuring you make informed choices that drive your business forward. Agenda: Maximize the value of your current IMMs through strategic retrofitting Learn how to integrate digital technologies to enhance monitoring and control Explore the benefits of Euromap interfaces and plasticizing retrofits Understand how retrofitting can help meet new product demands and improve adaptability Discover how Engel can support your retrofitting needs, from free consultations to execution
About two decades ago, machine manufacturers, including WITTMANN BATTENFELD with its MicroPower 15 t, specialised injection moulding systems. These systems were tailored for precision micro-scale parts, offering industrial modularity and significant economic benefits. Despite this versatility and precision, the bottleneck in micro-part production persisted by their injection cavities, resulting in prolonged lead times of up to 20 weeks. Clients reluctantly accept larger tolerances (± 30 µm), but there's a growing need for shorter lead times, and smaller features, especially in prototype development. The time-consuming precision mould production lingers as the chief bottleneck.
EVCO Plastics doesn’t seem to have a first gear. Since 1964, the family-owned custom injection molder has launched a major expansion on average every three years, right through recession and pandemic, and has accelerated that pace of late. In recent years, EVCO also has expanded its technological base with the addition of 3D printing, collaborative robots, iMFLUX low-pressure molding, an automated UV-curing paint line, expanded process monitoring, white-room molding and liquid silicone rubber (LSR). In a recent interview with Plastics Technology, EVCO executives and engineers provided an update on the latest capacity expansions and technological initiatives in three main areas: automation, LSR and 3D printing.
Say “manufacturing automation” and thoughts immediately go to the shop floor and specialized production equipment, robotics and material handling systems. But there is another realm of possible automation — the front office.
Glanzer says his team currently favors Fanuc cobots, which in his experience have proven to be cost-effective with reasonable lead times. EVCO uses safety scanners rather than hard guarding around cobots. He notes that the Fanuc cobots can downshift from high-speed production mode to slower “cobot mode”—or even stop entirely—when a person enters its safety envelope.
Join KraussMaffei for an insightful webinar designed for industry professionals, engineers and anyone interested in the manufacturing processes of PVC pipes. This session will provide a comprehensive understanding of the technology behind the production of high-quality PVC pipes: from raw material preparation to final product testing. Agenda: Introduction to PVC extrusion: overview of the basic principles of PVC pipe extrusion — including the process of melting and shaping PVC resin into pipe forms Equipment and machinery: detailed explanation of the key equipment involved — such as extruders, dies and cooling systems — and their roles in the extrusion process Process parameters: insight into the critical process parameters like temperature, pressure and cooling rates that influence the quality and consistency of the final PVC pipes Energy efficiency: examination of ways to save material and energy use when extruding PVC pipe products
After successfully introducing a combined conference for moldmakers and injection molders in 2022, Plastics Technology and MoldMaking Technology are once again joining forces for a tooling/molding two-for-one.
Despite price increase nominations going into second quarter, it appeared there was potential for generally flat pricing with the exception of a major downward correction for PP.
Across all process types, sustainability was a big theme at NPE2024. But there was plenty to see in automation and artificial intelligence as well.
Ultradent's entry of its Umbrella cheek retractor took home the awards for Technical Sophistication and Achievement in Economics and Efficiency at PTXPO.
Successfully starting or restarting an injection molding machine is less about ticking boxes on a rote checklist and more about individually assessing each processing scenario and its unique variables.
GETTING A QUOTE WITH LK-MOULD IS FREE AND SIMPLE.
FIND MORE OF OUR SERVICES:
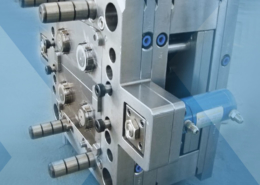
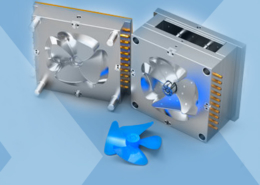
Plastic Molding

Rapid Prototyping
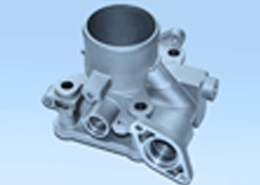
Pressure Die Casting
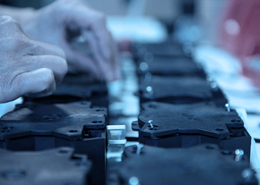
Parts Assembly
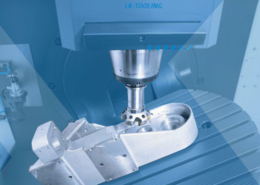