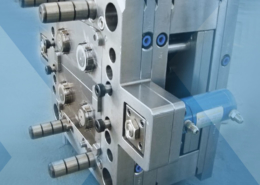
How to Optimize Your Molds and Hot Runners for Processing Bioresins - pp mold
Author:gly Date: 2024-09-30
Xact Metal, State College, Pennsylvania, USA, has announced the launch of its new initiative, “Breaking the Mold: The Xact Solution to Better Tooling.” The move aims to change the approach to metal Additive Manufacturing in the tooling industry by reframing the technology as a valuable option for rapid and cost-effective parts.
Xact Metal states that its Additive Manufacturing machines complement traditional manufacturing processes, offering cost-effective solutions for producing small inserts and complex geometries that are otherwise challenging or costly to manufacture. The company’s technology enables on-site production, reducing downtime and increasing operational efficiency.
Reach a truly international audience that includes component manufacturers, end-users, industry suppliers, analysts, researchers and more.
“Our mission is to make Additive Manufacturing more accessible and affordable for all,” added Juan Mario Gomez. “With our focus on cost-effective design and high-performing components, Xact Metal 3D printers offer a compelling solution for businesses looking to enhance their tooling and molding capabilities.”
Xact Metal’s strategic partnership with Uddeholm enables them to offer Corrax powder for its machines. Corrax is a cobalt-free and corrosion-resistant material that can be polished to an A1 surface finish. This partnership empowers molders and mold makers with the ability to produce optimised mold inserts and tooling components, save time, and ensure high-quality results.
The circular economy is a catalyst for new packaging design and more efficient production, as well as value chain collaboration to ensure products meet specific regional requirements regarding recycling and recycled content.
Husky’s RMTP technology is offered as a module of the company’s proven HyPET HPP5e high-performance system designed to support the closed-loop conversion of washed flake to preform by accepting food-approved grade melt from an upstream provider. By eliminating the drying and melting steps, this solution facilitates the effective production of packaging made from 100 per cent rPET material.
“We are excited about the new possibilities direct metal 3D printing brings to our rapid prototyping capabilities and engineering labs,” stated Tyler Stark, Innovation Hub leader at Spectrum. “Adding stainless steel printing to our current lineup of 3D thermoplastic printers not only bridges the gap for fixtures and tooling but also speeds up significantly the prototyping process, enabling us to meet our customers’ most complex device development needs and in rapid fashion.”
Our audience includes component manufacturers, end-users, materials and equipment suppliers, analysts, researchers and more.
Metal AM magazine, published quarterly in digital and print formats, is read by a rapidly expanding international audience.
Discover suppliers of these and more in our comprehensive advertisers’ index and buyer’s guide, available in the back of Metal AM magazine.
In addition, a recent collaboration with Oqton offers advanced software solutions, including conformal cooling channel automation, enabling seamless integration of Additive Manufacturing into the tooling and molding workflow. Xact Metal has also recently partnered with Dlyte Polishing Solutions from GPAINNOVA to complete the entire workflow and offer a comprehensive solution for achieving superior tooling surface finish with AM.
Robert Domodossola, Husky’s President of Rigid Packaging, said: “We are truly excited about the possibilities that our new RMTP system presents. Its introduction further strengthens our commitment to sustainable PET packaging that is produced with an increasingly lower carbon footprint.”
Don't miss any new issue of Metal AM magazine, and get the latest industry news. Sign up to our twice weekly newsletter.
As a result, recent customers Actco Tool and Mfg and Spectrum Plastics Group, a DuPont Business have invested in Xact Metal technology to strategically grow their capabilities for tooling and molding applications. They join existing Xact Metal customers such as JST, a global connectors manufacturer, and The Plastek Group, a global plastics packaging company specialising in mold building. Both of these customers utilise Xact Metal technology to create complex tool inserts for injection molds.
The free to access Metal Additive Manufacturing magazine archive offers unparalleled insight into the world of metal Additive Manufacturing from a commercial and technological perspective through:
Investing in the production of sustainable packaging that supports the circular economy has long been a top priority for Husky, and the RMTP system is the company’s most recent development enabling this initiative.
Husky Technologies has introduced its HyPET HPP5e Recycled Melt to Preform (RMTP) system, which marks the integration of a preform injection moulding system with melt decontamination unit – enabling the direct conversion of washed flake to preform.
From May 6-10 in Orlando, Florida, Xact Metal’s technical team will take over the Cimquest booth – S25196 – at NPE 2024 Plastic Show to showcase its equipment and capabilities.
By streamlining the process, the new system also enables producers to achieve 30 per cent energy savings, according to a Husky press release. In addition, the system is equipped with Husky’s Advantage+Elite real-time proactive, predictive, transparent monitoring solution as a standard feature, which can reduce the variability risk associated with running higher levels of post-consumer-resin (PCR).
In addition to providing extensive industry news coverage, Metal AM magazine is known for exclusive, in-depth articles and technical reports.
“Actco has nearly six decades in close tolerance tool and die work, and we’re actively looking to the future by adding more close tolerance equipment to our toolbox” shared Dana Gruber, President of Actco. “The Xact Metal XM200G fits that bill. The 20-micron build layer and compact machine design allows us to meet our customer’s needs.”
GETTING A QUOTE WITH LK-MOULD IS FREE AND SIMPLE.
FIND MORE OF OUR SERVICES:
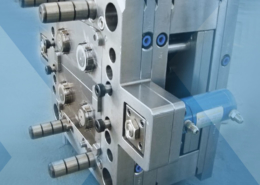
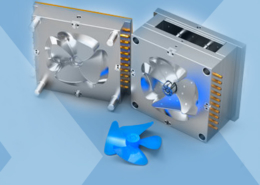
Plastic Molding

Rapid Prototyping
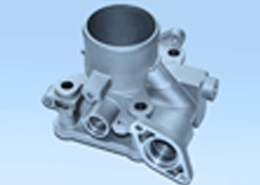
Pressure Die Casting
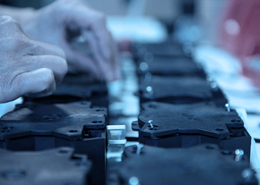
Parts Assembly
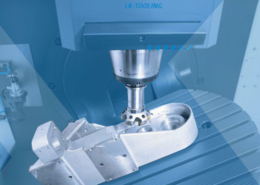