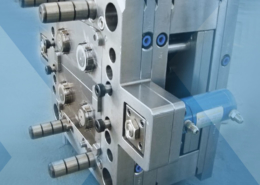
How to Optimize Your Molds and Hot Runners for Processing Bioresins - pla inject
Author:gly Date: 2024-09-30
The companies actively participating in the MedAccred Plastics Task Group, which developed the audit criteria for injection molding, reads like a who's who of medical manufacturing: Abbott, Baxter Healthcare, Becton, Dickinson & Co., Boston Scientific, Johnson & Johnson, Medtronic, Philips and Stryker on the OEM side; in addition to BMP Medical and MTD Micro Molding, GW Plastics, Mack Molding and Plastikos were among the suppliers taking part. The plastics injection molding audit criteria draw from established industry standards as well as manufacturing best practices.
By providing OEMs with oversight and verification of compliance to critical manufacturing process requirements, MedAccred enhances patient safety, says the organization. Suppliers benefit by improving their operations based on audit criteria while reducing the number of on-site customer audits. They can also benefit from exposure to existing and new customers, which, in the long term, strengthens relationships and creates new opportunities.
MedAccred accreditation is not the same as ISO certification, John Hastings of Johnson & Johnson told PlasticsToday at MD&M West in Anaheim, CA, last week. "ISO is an inch deep and a mile wide, whereas a MedAccred audit is an inch wide and a mile deep for the critical process," he explained. "Our audit criteria are developed for specific processes collaboratively with OEMs and relevant CMs."
The first product packed with bi-oriented bottles injection stretch-blow molded (ISBM) from high-density polyethylene (HDPE) is now available on the supermarket floor at Italian chain UNES. The grade was supplied by France’s Total and used to package a refill bottle containing dishwashing liquid.
Dishwashing liquid from I.C.E. For SpA employs bi-oriented bottles molded from HDPE to save 50% plastic usage versus traditional extrusion blow molded containers.
Editor in chief of PlasticsToday since 2015, Norbert Sparrow has more than 30 years of editorial experience in business-to-business media. He studied journalism at the Centre Universitaire d'Etudes du Journalisme in Strasbourg, France, where he earned a master's degree.
Thus far, MedAccred has established audit systems in the following areas: Cable and wire harness; heat treating; plastics; printed circuit board assemblies; sterilization; and welding. Injection molding is the initial subcategory within the plastics sector. MTD Micro Molding (Charlton, MA) is the first micro injection mold company to pilot the audit criteria, and the aforementioned BMP Medical is the first injection molding firm to complete a pilot audit against the criteria.
If all goes according to plan, BMP Medical (Gardner, MA) can claim a world first. It will soon be the first injection molding company to achieve accreditation from MedAccred (Warrendale, PA), a new medtech-industry-managed program that provides supply chain oversight via standardized audit criteria.
Processor Incoplas (Brussels, Belgium) has continuously invested in technical development aiming at weight reductions, while maintaining bottle performance and quality, for the past few years focusing on developing ISBM bottle production using bi-oriented HDPE. The compay employed Total’s HDPE SB 1359 grade to produce an extra-light bottle with excellent mechanical properties, soft touch, as well as transparency.
MedAccred has established rigorous audit criteria that incorporate industry standards along with specific OEM and contract manufacturer (CM) requirements. The program replaces some of the routine critical process supplier audits conducted by many OEMs and CMs with a single, robust audit. It is administered by Performance Review Institute (PRI), a not-for-profit organization that also supports the Nadcap accreditation program for the aerospace industry. MedAccred is modeled after this successful 25-year-old program.
Incoplas is able to process bottles in a standard range of sizes up to one liter in capacity that are applicable in various market segments. Compared to equivalent extrusion blow molded (EBM) HDPE bottles, weight reduction potential of up to 50 percent is reportedly achievable. The SB 1359 resin features a unique molecular design capable of being processed on ISBM machines.
Ed Kangas, BMP Vice President, Sales and Marketing, came away impressed with the process. "It was an open, very collaborative discussion," he told PlasticsToday, adding that it involved a "deep, three-day dive into our processes that provided us with an opportunity to implement internal improvements." As the first injection molder to achieve MedAccred accreditation, pending approval, "it's a differentiating factor and gives smaller suppliers like us greater visibility."
The idea for MedAccred originated with Johnson & Johnson's DePuy Synthes group in Ireland, where a director of supplier quality, familiar with Nadcap, wondered why a similar accreditation program was not available for the medtech industry. That was in 2010, and an industry roundtable in 2012 officially kicked off the program. The MedAccred Plastics Task Group was formed about one year ago, added Hastings.
GETTING A QUOTE WITH LK-MOULD IS FREE AND SIMPLE.
FIND MORE OF OUR SERVICES:
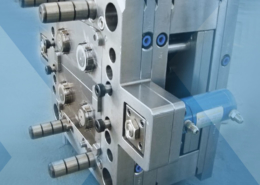
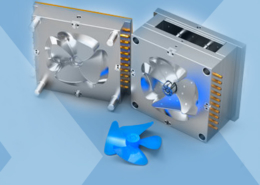
Plastic Molding

Rapid Prototyping
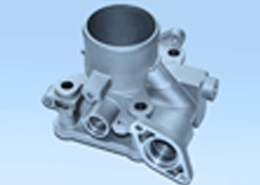
Pressure Die Casting
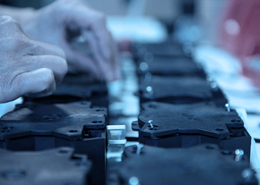
Parts Assembly
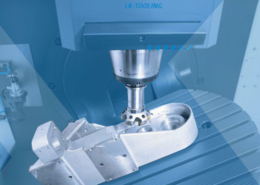